The company is mainly engaged in the research and development, production, and sales of automatic paper production line equipment, specialty paper, and processing machinery. The company is a technology driven enterprise, and technological innovation is its core advantage. The main equipment of the company is independently innovated and developed, with a leading level of similar equipment in China. The company independently develops a paper machine with a width of 6600mm and a design speed of 3000m/min. It produces 1 million tons of high-end cultural paper annually and is a wide width high-speed paper machine with independent intellectual property rights.
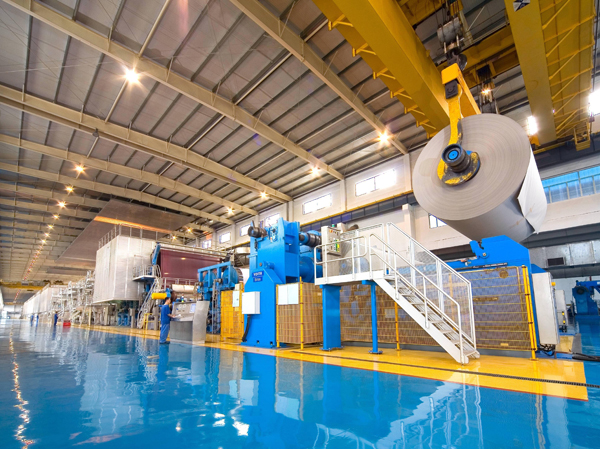
Fully automatic paper production line
Main products:
1、 Paper machines: toilet paper production line (napkins), household paper production line, kraft paper production line, corrugated paper production line, coated whiteboard paper machine, cardboard box board paper, packaging paper production line, cultural paper production line (writing paper), specialty paper production line, waste paper paper production line.
2、 Pulping equipment: horizontal/vertical pulper, grinder, vertical high concentration mill, vibrating screen, centrifugal screen, desander, rinse machine, thruster, agitator, Dutch style beater, circular mesh thickener, side pressure thickener, pressure screen, slicer, coarse mill.
3、 Completed equipment: single blade paper cutter, double blade paper cutter, drum paper cutter, horizontal paper cutter, three roll calender, five roll calender, upward paper rewinding machine, embossing rewinding punching machine (toilet paper), disc paper slitting machine, band saw paper cutter, napkin folding machine.
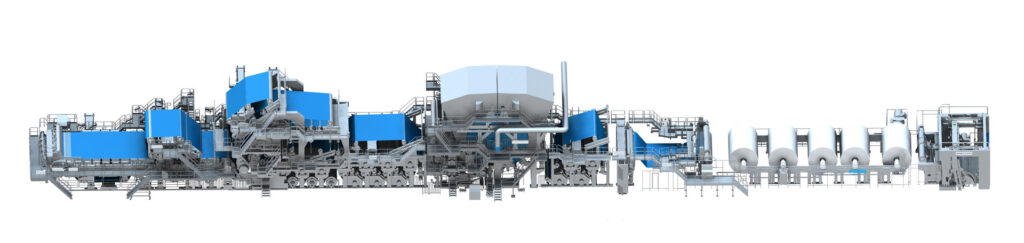
Large paper equipment overview map
What is papermaking machinery
Paper making machinery is an important equipment for manufacturing paper and paper products, mainly including material preparation equipment, pulp making equipment, paper machines, and finishing processing machinery.
Material preparation equipment is mainly used for pre-treatment and processing before steaming or grinding, including grass cutters, reed cutters, peelers, slicers, etc. Pulp making equipment is a key device for separating plant raw materials into fibers, including steamers, wood mills, thermal grinders, pulp washing machines, bleaching machines, pulping machines, etc.
The paper machine is the core equipment that transforms pulp water suspension into paper through processes such as filter dewatering, mechanical extrusion dewatering, and drying. It mainly includes three main parts: forming, pressing, and drying, and is equipped with necessary finishing, winding, and transmission devices, as well as auxiliary systems such as slurry supply, slurry and white water circulation, vacuum, ventilation and exhaust, paper damage treatment and lubrication, and self-control. The width of modern large-scale paper machines can reach 11m, the working speed can reach over 1000m/min, the daily paper output can reach hundreds of tons, and the weight of the entire machine can reach over a thousand tons, with a length of over a hundred meters.
In addition, papermaking machinery also includes some auxiliary equipment, such as crushing conveyors, balers, and specialized equipment for the production of special paper products. These devices play an important role in the papermaking process, greatly improving production efficiency, reducing production costs, and also helping to improve paper quality and environmental performance.
Overall, papermaking machinery is an indispensable and important equipment in the papermaking industry, and its technological level and development status directly affect the development level and competitiveness of the papermaking industry. With the continuous advancement of technology and increasingly strict environmental requirements, papermaking machinery is also constantly being updated and upgraded, developing towards a more efficient, energy-saving, and environmentally friendly direction.
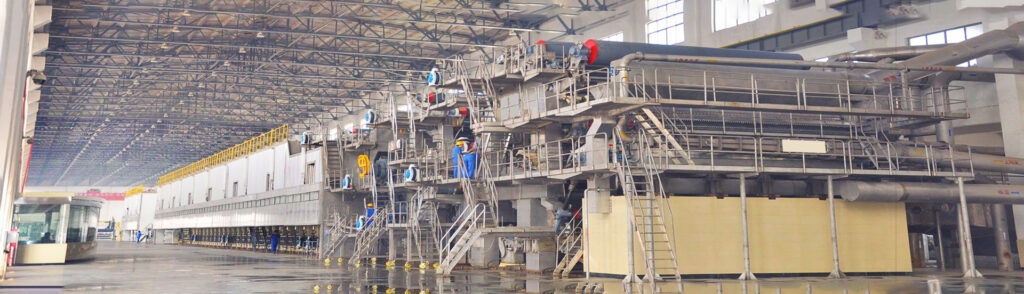
The main production processes of the paper production line
The production of paper includes pulp making, papermaking, and paper processing.
(1) Pulp making
Pulping is the process of separating plant fiber raw materials into natural pulp or bleached pulp. Pulping can be done using chemical, mechanical, or chemical mechanical methods. Except for mechanical methods, both chemical methods and chemical mechanical methods require the addition of chemical raw materials and chemicals.
China mainly uses chemical pulping, and its basic process is: raw material storage → steaming → washing → screening → bleaching. The most critical process is steaming and boiling.
① Steaming and cooking is the process of dissolving lignin and cooking chemicals in raw materials through chemical reactions, making it easier to separate from cellulose. There are mainly two methods: alkaline method and sulfite method.
Alkaline method is to treat plant fiber raw materials with alkaline solution, dissolve the lignin in it, and separate the raw fibers into pulp. According to different alkali materials, it can be divided into lime method, caustic soda method, and sulfate method. Sodium carbonate, sodium polysulfide, hydrogen sulfide, sulfate, etc. can also be used. At present, alkaline cooking is still the main method for pulping in various countries, and most of them use the sulfate method.
② The extraction of waste liquid and the washing of pulp in alkaline pulping cooking liquid are black liquor, while the acid pulping cooking liquid is red pulp, collectively referred to as cooking waste liquid. The lignin, sugars, and fats contained in it must be separated from the pulp as much as possible after cooking to ensure the purity of the pulp. Due to lignin being a water-insoluble network type macromolecule, its molecular chain contains rigid groups such as benzene rings, which are difficult to move and have low flexibility. When the lignin content in pulp is high, it appears stiff and fragile, making it difficult to hydrate during pulping and prone to breakage. The process of extracting waste liquid and washing pulp involves the separation of fiber and non fiber impurities. The treatment of papermaking wastewater involves environmental protection and other issues, which have attracted the attention of various countries. More and more polymer chemicals are being used in this process.
③ Adding bleaching agents to pulp bleaching increases its whiteness.
(2) Paper making
Papermaking mainly refers to beating, papermaking, and producing cardboard.
① The pulp after clean washing and screening cannot be directly used for papermaking. It must be processed using physical and mechanical methods to cause fiber cutting, crushing, water absorption swelling, and fine fibrosis, resulting in uniform fiber size, increased surface area, softness, and increased strength.
② Seasoning is the general term for multiple processes such as gluing, filling, coloring, etc.
Glue application is a chemical treatment of pulp, paper, or cardboard to achieve resistance to fluid (primarily water) infiltration. Most paper and cardboard require gluing, which can be divided into in pulp gluing and surface gluing depending on the method.
Adding fillers (such as talcum powder, kaolin, calcium carbonate, titanium dioxide, etc.) and organic polymer chemicals to the slurry to improve the opacity, brightness, smoothness, stiffness, dry strength, wet strength, and other properties of the paper. Adding fillers is crucial for reducing production costs and improving paper quality.
③ Coloring involves adding pigments to pulp to produce the desired color. Colorants are divided into pigments (organic and inorganic pigments) and dyes (alkaline dyes, acidic dyes, and direct dyes, etc.). In addition, paper dyeing can also be achieved through methods such as surface dyeing, immersion dyeing, and coating dyeing.
④ Papermaking is divided into two types: dry papermaking and wet papermaking. The former uses air as the medium, while the latter uses water as the medium. Depending on the papermaking method, equipment, and chemical composition, different varieties of paper can be obtained. Cardboard production is basically the same as paper production, and also requires steps such as pulping, pulping, copying, calendering, coiling, cutting or rewinding.
(3) The processing of paper refers to the production of various processed papers and non plant fiber papers.
① The secondary processing of processed paper after the papermaking process includes coating with pigments (copperplate paper, coated paper, cast coated paper, etc.) and surface treatment with various chemicals (producing pressure-sensitive paper, thermosensitive recording paper, flame retardant paper, release paper, etc. through extrusion, impregnation, bonding, and other methods). According to different preparation methods, it can be further divided into coated processing paper, modified processing paper, impregnated processing paper, mechanically processed paper, composite processing paper, etc.
② Non plant fiber paper includes synthetic fiber paper, mineral wool fiber paper, metal fiber paper, etc. Under the situation of shortage of papermaking raw materials, these non plant fibers have broadened the range of papermaking raw materials, and opened up a new world for the production and application of paper with their unique and new properties.
The main categories of paper production lines
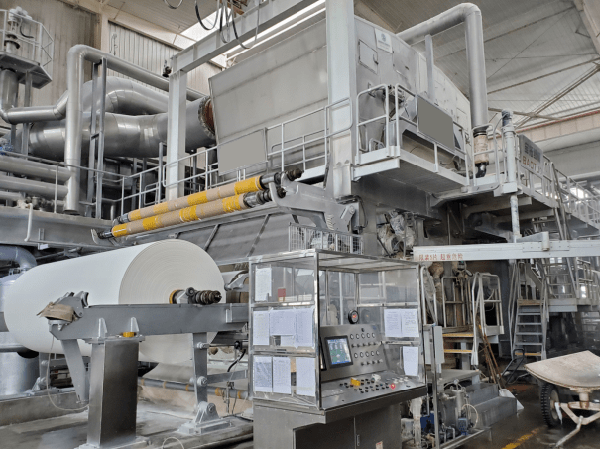
Automatic toilet paper production line
1. output paper: toilet paper, facial tissue paper, napkin paper, kitchen towel
2. raw material: wood pulp, waste paper, virgin pulp, recycled paper
3. capacity: 5-50 ton per day
4. net paper width: 1575-3600mm
5. output paper weight: 13-40g/m2
1- In two rewinding shaft center winding reel, fixing grooves lift.
2- Inverter motor drive, PLC control system.
3- With a constant tension control system; photoelectric automatic correction correcting system.
4- Fracture automated shutdown device, emergency stop function, and maintaining constant tension.
5- Put paper winding shaft adopts tension air shaft, collect winding shaft use tension inflatable shaft.
6- Pneumatic feeding, pneumatic discharge mechanism, Air shaft locate.
7- Hear round knife slitting, it can adapt to slitting different properties material.
8- With fan, Using wind scrap, Automatic counting of scrap moving length.
Automatic kraft paper production line
The kraft paper machine can use various waste paper, recycled old cardboard boxes, wheat or straw, sugarcane bagasse, virgin pulp, cotton, wood, etc. as raw materials to make kraft paper, and the finished product can be a large paper roll. This product is a 3900mm, 200m/min pressure forming multi cylinder paper machine, mainly used for producing 100-300g/m2 products. The main product is high-strength liner paper, and all products are rolls. The main components of this paper machine include the turning section, forming section, pressing section, drying section, cover section, size pressing section, winding machine, base section, mechanical transmission and electrical control section. We have a complete kraft paper machine production line, as well as various spare parts for kraft paper machines, and professional engineers to provide installation and after-sales service for you.
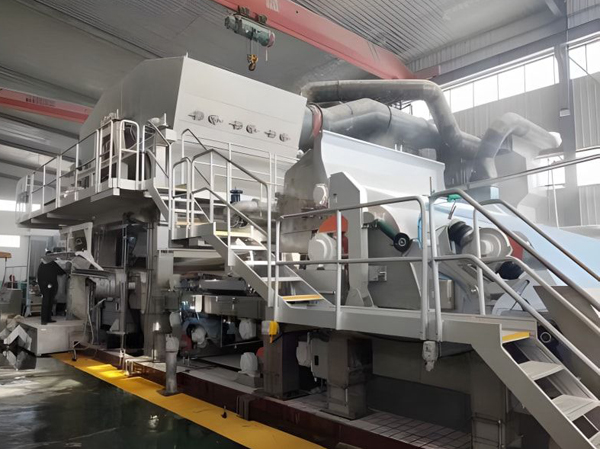
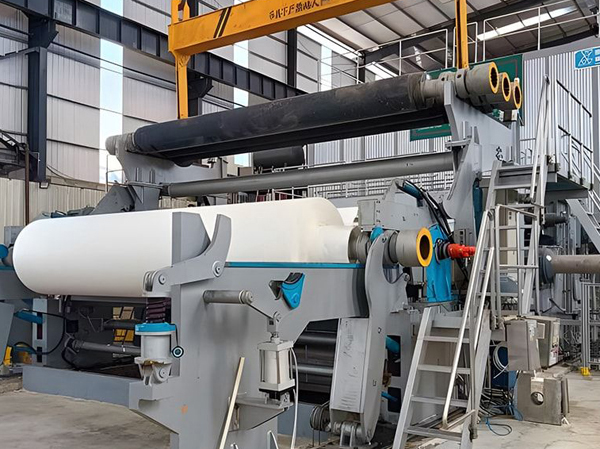
Automatic tissue paper production line
1.Output paper:toilet paper,tissue paper.
2.Output weight:13-40g/m2
3.Net paper width: 2400mm
4.Wire width:2850mm
5.Capacity: 7-200t/d
6.Working speed:100-180m/min
7.Rail gauge:3500mm
8.Drive way:AC frequency converter and adjustable speed, drive part by part.
Corrugated paper making machine
Product:Low GSM High Strength Fluting
Trimmed Width:3200-6600 mm
Design Speed:300-1000m/min
Gram Weight:70-140g/m²
Production Capacity:50,000-200,000 Tyr
Product:A Grade High Strength Corrugated Paper
Trimmed Width:3200-6600 mm
Design Speed:300-1000m/min
Gram Weight:100-160g/m²
Production Capacity:50,000-300,000 T/Yr
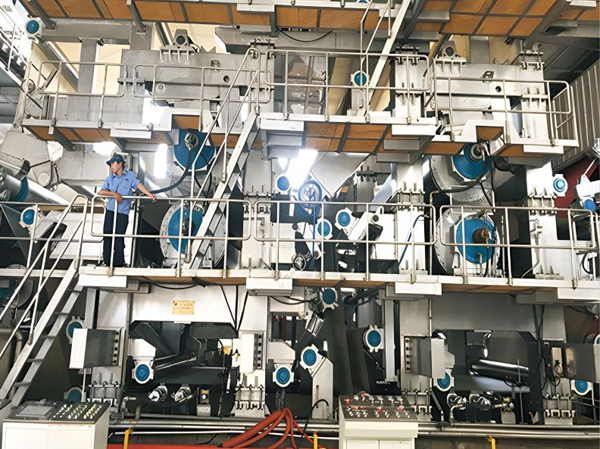
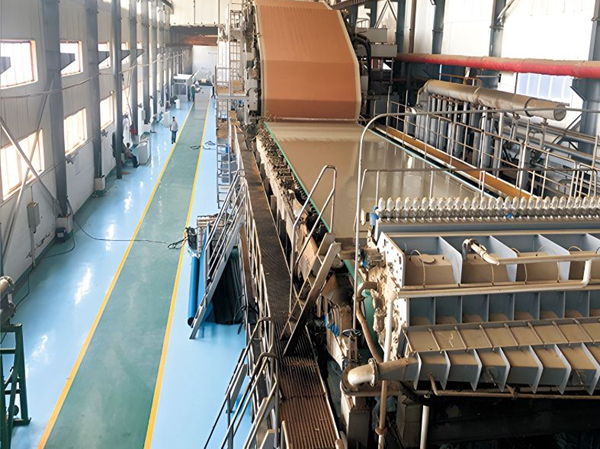
Automatic Newsprint paper production line
Newsprint Paper Machine is used for making Newsprint paper.The output paper basis weight is 42-55 g/m² and brightness standard 45-55%,for news printing. News paper is made of Mechanical wood pulp or waste newspaper. The quality of output News paper by our paper machine is loose,light and has good elasticity; the ink absorption performance is good, which ensures that the ink can be well fixed on the paper. After calendering, both sides of Newspaper are smooth and lint-free, so that the imprints on both sides are clear; Paper has a certain mechanical strength,good opaque performance; it is suitable for high-speed rotary printing machine.
keyword: paper machine|paper machinery|papermaking equipment|Newspaper machine
subcategory: Cultural paper machine
Automatic writing paper making machine
summary: Cultural paper machine is a paper making machine specially designed for the production of cultural paper, with a wide range of uses and efficient production capacity. Cultural paper is mostly used for writing, printing and other cultural activities, such as printing paper, copy paper, writing paper, etc.
keyword: paper machine|paper machinery|papermaking equipment|Writing paper machine
subcategory: Cultural paper machine
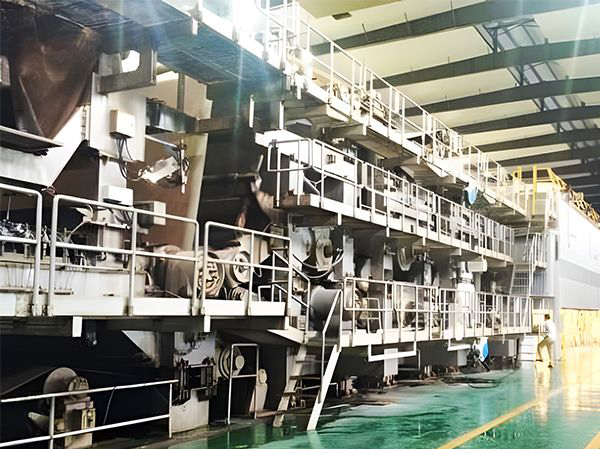
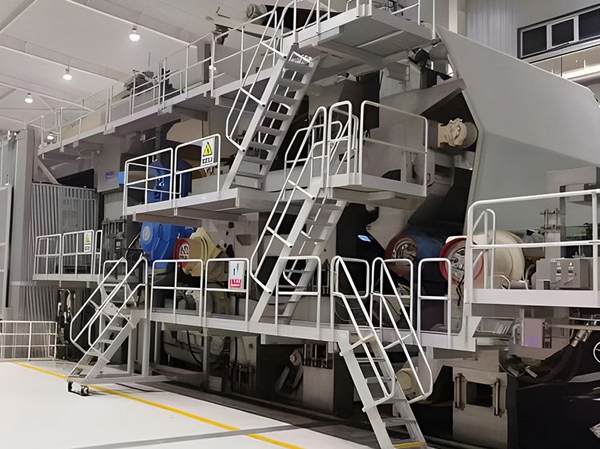
Automatic yarn tube paper production line
A type of industrial paper specifically designed for the textile industry to produce paper yarn tubes and conical paper tubes. It is a thin steel paper. The quantification is 65g/m2 and 145g/m2. Thickness of 0.1-0.2mm. The basis weight of the yarn tube cardboard is 85-510g/m2. Paper is tough and wear-resistant. The paper surface is smooth and even. Has good water resistance (with a sizing degree of not less than 1.25mm). Can resist edge indentation and withstand lathe machining during use. In order to distinguish between the rows of yarn tubes on the spinning machine, various colors such as red, orange, yellow, green, blue, etc. are often dyed during use, and the dyeing is firm. Using bleached or unbleached chemical wood pulp as raw material, the paper is made by free pulping and coloring with dyes on a long web paper machine, then compressed and rewound into a roll paper shape, and further processed into lightweight and easy-to-use yarn tubes.
Automatic duplex board paper production line
Product:High Grade White Coated Duplex Board
Trimmed Width:3200-6600 mm
Design Speed:250-900m/min
Gram Weight:150-400g/m²
Production Capacity:60,000-500,000 T/Yr
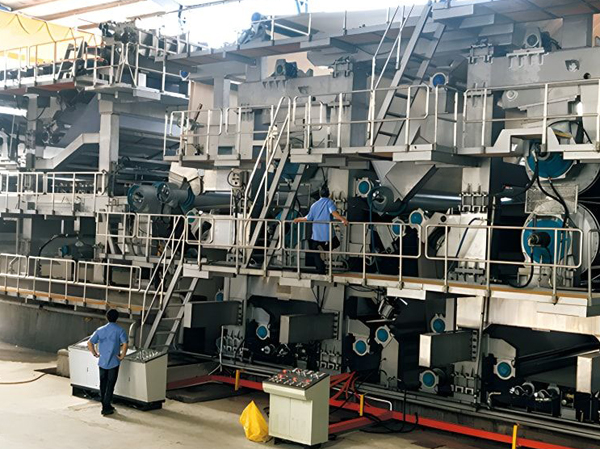
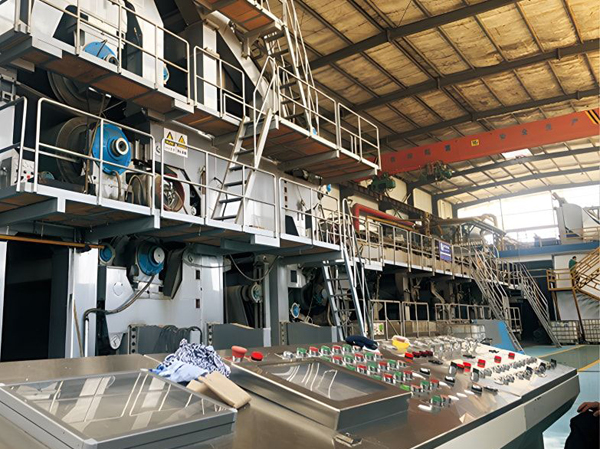
Automatic Test-liner paper production line
Description:
Product:A and B Grade Test-liner
Trimmed Width:3200-6600 mm
Design Speed:300-1000m/min
Gram Weight:110-220g/m²
Production Capacity:50,000-350,000 T/Yr
Automatic wrapping packing paper production line
A general term for a type of paper used for packaging purposes. It can be divided into ordinary packaging paper, specialized packaging paper, trademark paper, oil resistant packaging paper, and moisture-proof packaging paper. Usually has high strength and toughness. Various types of packaging paper have different properties and uses. For example, specialized fruit packaging paper is thin and soft. The photosensitive protective paper is opaque. Oil resistant packaging paper (such as vegetable parchment paper) has the ability to prevent oil penetration. Moisture resistant packaging paper (such as asphalt paper, oil paper, aluminum foil paper, etc.) has moisture resistance. Trademark paper is used for packaging after printing.
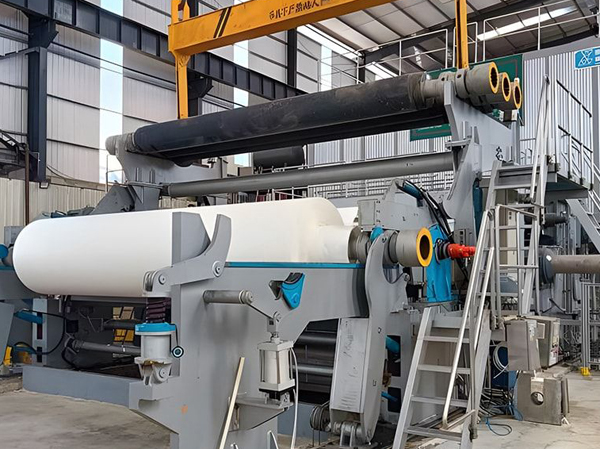
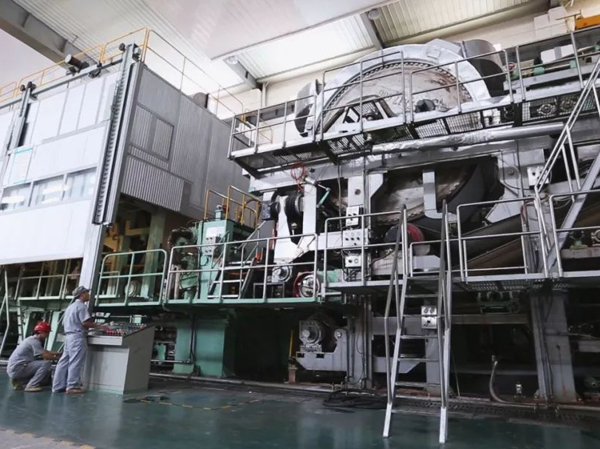
Automatic culture paper making machine
1.Easy operation,superior performance,can work continuously with high efficiency
2.Low noise,the use of harmless broken paper.
3.This paper simple operation on board.Paper automatic positioning,the paper transport mechanism are equipped with elastic adjusting device.
4.Automatic roll,synchronous cutting paper,work continuously
5.Wire section: It consists of flow part,forming section,round cylinder mould,couch and evening device and so on form the flow and forming section.
6.Presssection:This section has three main press.Pneumatic tyre pressure main press section.Pressfelt are equipped with corrector,tensioner.
7.Drying section:In order to guarantee the drying capacity of the drying part.This paper machine has 3 groups 1500 mm and they are divided into 4+6+4.
8.Driving section:The total installed capacity of this machine is 223kw.
9.Foundation part:The foundation part of this machine include foundation plate,anchor bolt,iron pad on paper machine drawing.Foundation plate indicates all kinds of bottom rail,guide rail,foundation base and so on of the paper machine.
Automatic Security paper making machine
summary: Anti-counterfeiting paper machine is a device that produces paper with anti-counterfeiting function. It usually has some special structure and functions to realize the application of various anti-counterfeiting technologies on paper. It is widely used in banknotes, tickets, important documents and printed matter.
keyword: paper machine|paper machinery|papermaking equipment|Security paper machine
subcategory: Special paper machine
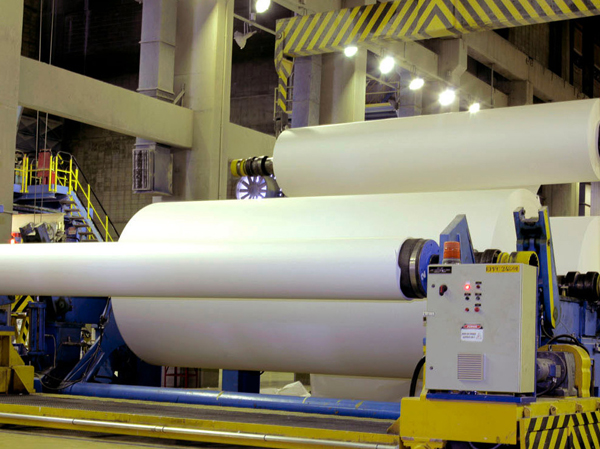
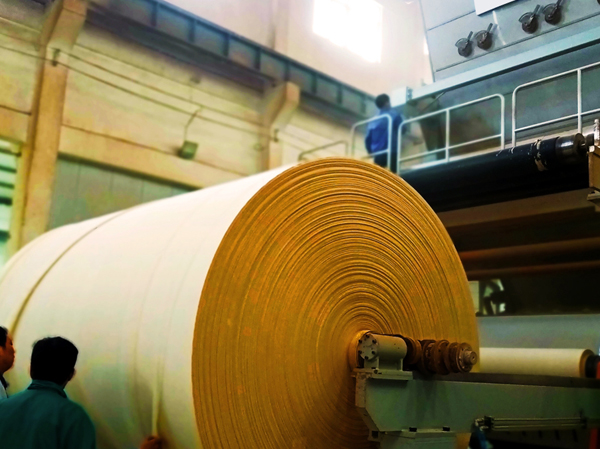
Automatic insulated paper making machine
summary: Insulating paper machine is to make insulating paper with specific properties and specifications by making paper raw materials through a series of processes.It has good electrical insulation properties, high temperature resistance, etc., used in transformers, motors, generators and other electrical equipment.
keyword: paper machine|paper machinery|papermaking equipment|Insulated paper machine
subcategory: Special paper machine
summary: The “friction plate” is usually used as a component in various mechanical equipment, which plays the role of transmitting power, braking, clutch, etc. The function of the friction sheet paper machine is to process a specific material into a friction sheet with the desired properties and specifications.
keyword: paper machine|paper machinery|papermaking equipment|Friction sheet paper machine
subcategory: Special paper machine
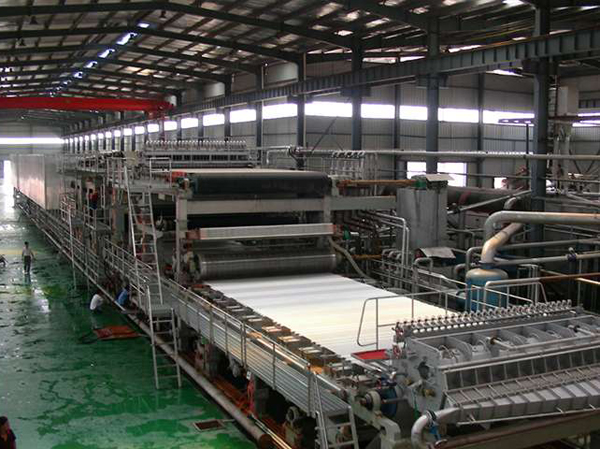
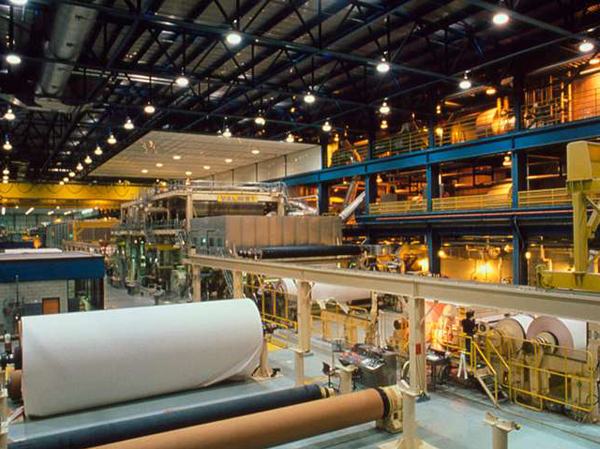
Automatic filter paper making machine
summary: The filter paper machine has high accuracy and stability, and can produce paper with specific pore structure and filtration performance to meet different filtration needs. For example, it plays an important role in air filtration, liquid filtration and other fields.
keyword: paper machine|paper machinery|papermaking equipment|Filter paper machine
subcategory: Special paper machine
Sublimation coating paper making machine
According to the user’s requirements, the basic structure of Thermal&Sublimation Coating Paper Machine is: Double-axis unloading bracket (automatic paper splicing) → Air knife coater → Hot air drying oven → Back coating → Hot stereotype dryer→Soft calender →Double-axis paper reeler (automatic paper splicing)
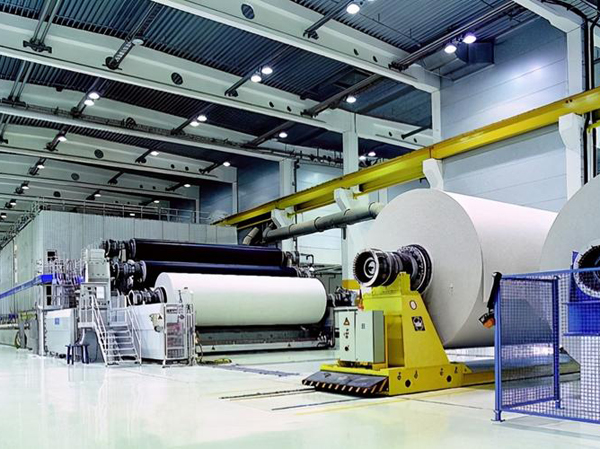
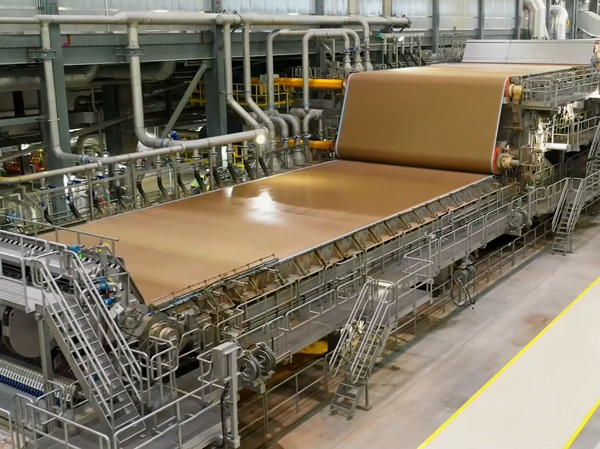
Insole paper board making machine
As different capacity and paper’s width and requirement, there are many different machines’ configuration. From the outside, shoes are composed of sole and upper. In fact, it also has a midsole. The midsole of some shoes is made of paper cardboard, we name the cardboard as insole paper board. Insole paper board is bending resistant, environmental friendly and renewable. It has the function of moisture-proof, air permeability and odor prevention. It supports the stability of shoes, plays a role in shaping, and can also reduce the overall weight of shoes. Insole paper board has great function, it is a necessity for shoes.
Cone&Core Base Paper is widely used in industrial paper tube, chemical fiber tube, textile yarn tube, plastic film tube, fireworks tube, spiral tube, parallel tube, honeycomb cardboard, paper corner protection, etc. The Cylinder Mould Type Cone&Core Paper Board Making Machine designed and manufactured by our company uses waste cartons and other mixed waste paper as raw material,adopts traditional Cylinder Mould to starch and form paper, mature technology, stable operation, simple structure and convenient operation. The output paper weight mainly includes 200g/m2,300g/m2, 360g/m2, 420/m2, 500g/m2 . The paper quality indicators are stable, and the ring pressure strength and performance have reached the advanced level.
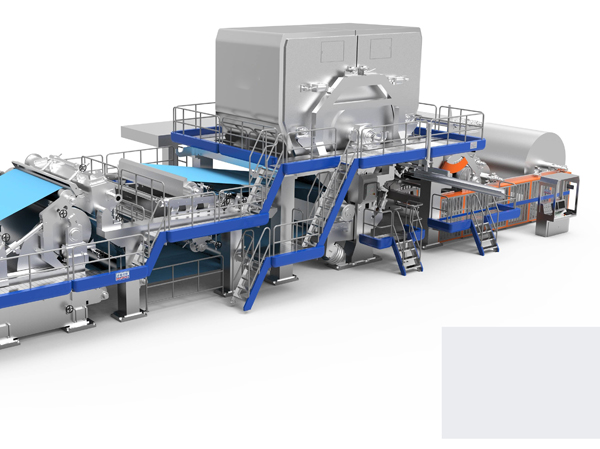
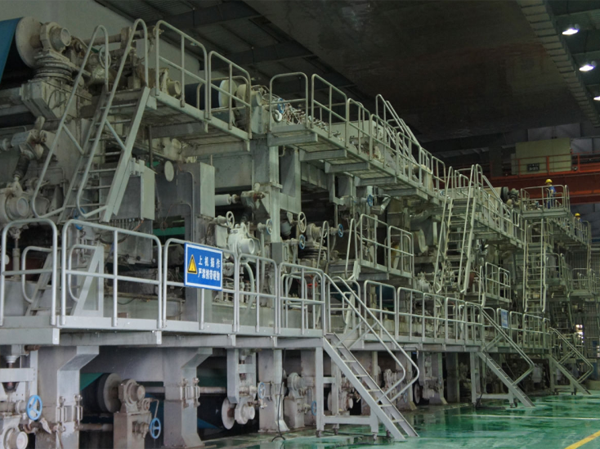
Ivory coated board paper processing machine
What is coated paper? Is that literally paper covered in cloth? No, no, no, that’s not true! In fact, coated paper often appears in our lives, such as the inside pages of magazines we like to read, book paper, packaging bags, advertising posters and so on
Automatic gypsum board paper processing machine
Paper type: Gypsum board covering base paper
Quantitative: 120-220GSM
Paper width: 3800-5200mm
Annual production: 50000 to 350000 tons
Maximum working speed: 1000 m/min
Design speed: 1200 m/min
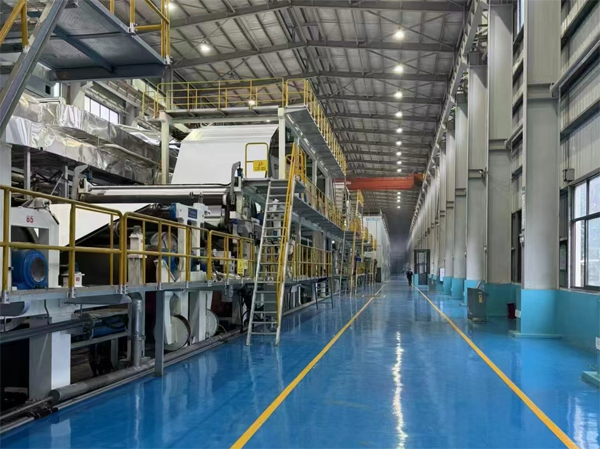
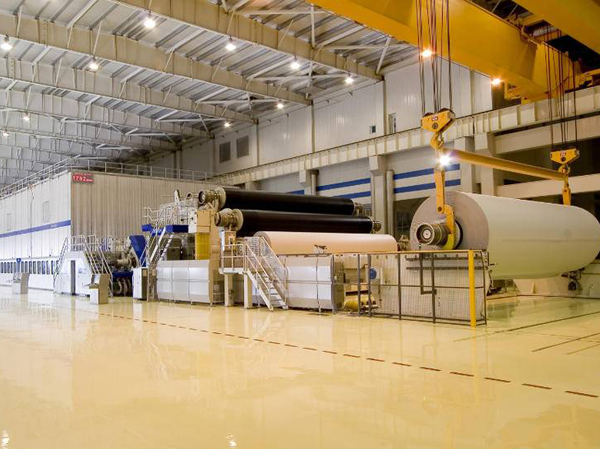
Automatic deko paper production plant
Decorative base paper has strict requirements for optical properties such as whiteness, and titanium dioxide is relatively expensive. Therefore, it is very important to find a filler with similar properties to titanium dioxide to replace it. This paper investigates the effects of pulp ratio, beating degree, PAE addition amount, titanium dioxide addition amount, and CPAM addition amount on the physical properties of decorative base paper; Titanium dioxide/kaolin composite fillers were prepared using the mechanochemical method, and the effects of drying methods and different types of fillers on the physical properties of decorative base paper were studied.
Automatic Tobacco Paper Production Plant
The manufacturing methods of tobacco flakes mainly include rolling method, thick pulp method, and papermaking method.
Roll pressing method is to crush tobacco raw materials, mix them with natural fibers, add a solution of adhesive and other additives, stir evenly, and then roll press and dry them to make thin sheet products. The production of tobacco flakes by roll pressing method has simple equipment, low energy consumption, and low cost, which is suitable for small and medium-sized production. However, the produced flakes have poor strength, high density, low filling performance, and high tar content. The thick paste method is to crush tobacco raw materials, evenly disperse them in water, add adhesives and other additives, and then spread the uniform paste on a rotating metal belt for drying and peeling to make tobacco flakes. The strength, specific gravity, filling properties, tar content, and production cost of tobacco flakes produced by the thick pulp method are between those of papermaking and roll pressing methods.
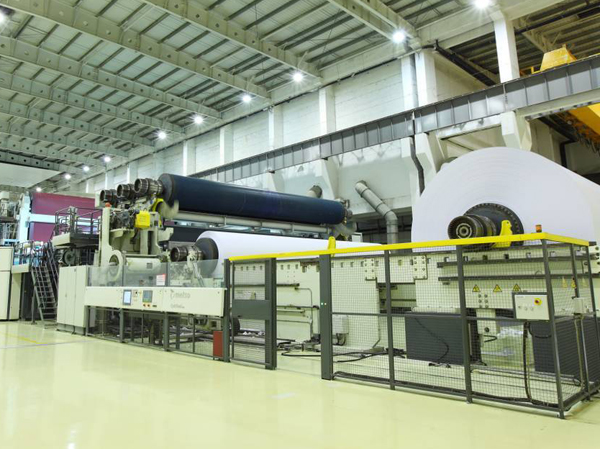
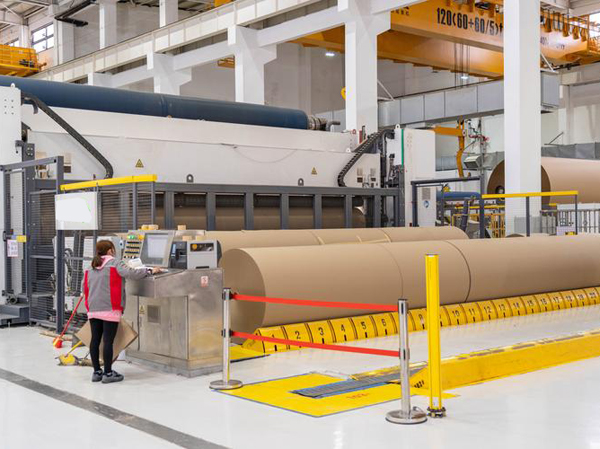
Automatic wood making paper production line
summary: wood paper because of its high strength and durability, usually used to make paper bags, envelopes, packaging materials, etc. Kraft paper machine is a complex and sophisticated equipment system, which mainly includes raw material processing, pulp manufacturing, paper making, post-processing and other steps.
keyword: paper machine|paper machinery|papermaking equipment| paper machine
subcategory:paper machine
Automatic waste paper pulping production line
Waste paper production line
Paper type: Grade A base paper
Quantitative: 60-150 GSM
Clean paper width: 4600-6600mm
Annual output: 50,000 tons – 800,000 tons
Maximum working speed: 1600 m/min
Design speed: 1900 m/min
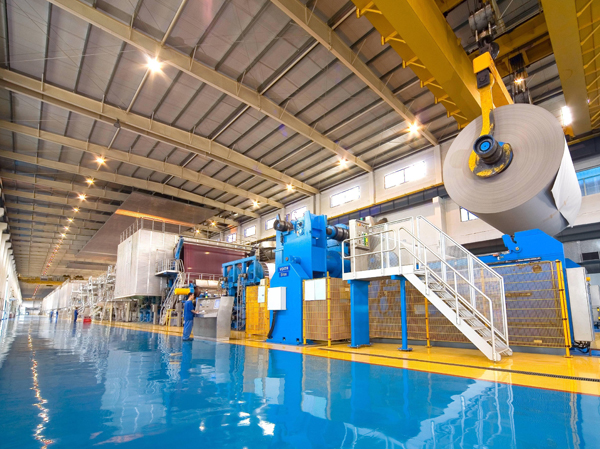
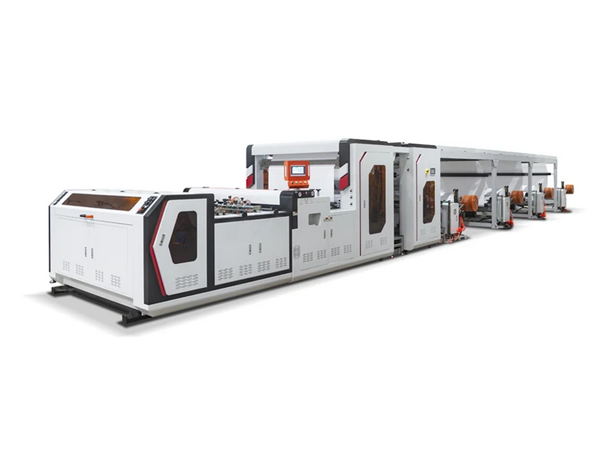
Automatic A4 Paper Production Line for Reams Paper
Paper machines can use many types of raw materials to make pulp and then pass through the paper machine to make good quality A4 paper. The raw material is mainly white wood pulp board, and White paper edge after unprinted trimming in the printing house.
Capacity: 6-18 reams/min
Paper size: A4 / A3 Paper Size
How to choose suitable paper making equipment
Choosing the appropriate papermaking equipment is a process that takes into account multiple factors. Here are some suggestions to help you make a wise choice:
- Clarify production requirements: Firstly, you need to clarify your production scale, product types, and quality requirements. This will help determine the model and configuration of the required equipment. For example, if you plan to produce a specific type of paper, you need to choose equipment that can meet this production demand.
- Understanding equipment performance: Equipment performance is one of the key factors in choosing papermaking equipment. You need to understand the production capacity, automation level, ease of operation, difficulty of maintenance, and service life of the equipment. These information can be obtained by communicating with the equipment manufacturer or consulting relevant materials.
- Assessing equipment quality and brand: Equipment quality and brand are crucial for ensuring production stability and reducing failure rates. You should choose equipment brands with reliable quality and good reputation, and conduct on-site inspections of the equipment before purchasing to understand its actual operation and production efficiency.
- Consider price and cost-effectiveness: Price is one of the important factors to consider when choosing papermaking equipment. You should evaluate the performance, quality, and brand of the equipment comprehensively based on your budget, and choose the equipment with high cost-effectiveness. Avoid pursuing low prices without considering the performance and quality of the equipment.
- Pay attention to after-sales service: After sales service is an important guarantee to ensure timely maintenance and upkeep of equipment during use. You should choose equipment suppliers with comprehensive after-sales service to ensure timely resolution of equipment problems.
- Consider environmental requirements: With the increasing awareness of environmental protection, the paper-making industry has higher and higher requirements for environmental protection. When choosing equipment, you should pay attention to its environmental performance and choose equipment that meets national environmental standards to ensure that the paper produced meets environmental requirements.
In short, selecting suitable papermaking equipment requires comprehensive consideration of multiple factors, including production needs, equipment performance, quality, brand, price, cost-effectiveness, after-sales service, and environmental requirements. By carefully comparing and evaluating the advantages and disadvantages of different equipment, you can find the papermaking equipment that suits your production needs.
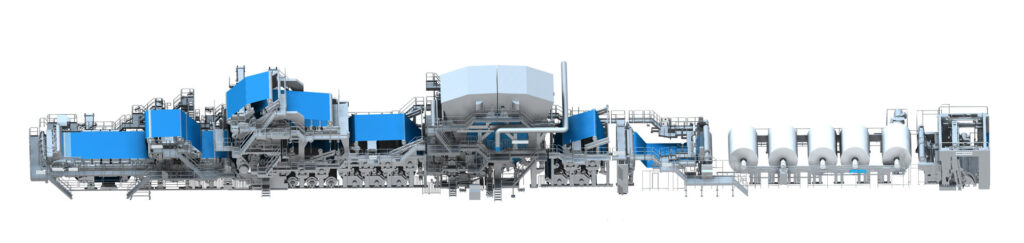
Introduction to the Basic Structure of Paper Machines
According to the needs of the copying process, paper machines come in various structural forms, generally consisting of components such as flow, forming, pressing, drying, finishing, coiling, and transmission, as well as supporting equipment such as auxiliary systems.
Forming Department
It consists of a headbox, chest roller, forming net, suction tank, and idler roller. The slurry box distributor evenly sprays the slurry sent by the flow system onto the forming mesh, and the slurry speed should match the mesh speed. Controlling the slurry speed and mesh speed is the main factor in selecting the slurry box type. The fully enclosed hydraulic slurry box is used to adjust the slurry speed by adjusting the slurry pressure of the flushing pump, and is suitable for high-speed paper machines; The air cushion type headbox adjusts the speed by adjusting the air cushion pressure, while the open high-level headbox adjusts the speed by adjusting the height of the slurry inside the box, which is suitable for medium speed paper machines; The open compartment slurry box is suitable for low-speed paper machines. The forming net is an endless circular net, which forms a horizontal or slightly inclined flat net surface between the chest roll and the bottom roll. As the working section of pulp dewatering, it is commonly referred to as a net, and therefore called a long net. If the endless formed mesh is placed on a circular mesh cage to form an arc-shaped dehydration forming working section, it is called a circular mesh. If a steel mesh drum with drilled holes is used to suction vacuum from the shaft end to accelerate the dewatering of pulp on the forming mesh surface, it is called a vacuum circular mesh or vacuum forming mesh. If the pulp is clamped between two long nets and both nets are simultaneously dehydrated and formed, it is called a clamp net former (Figure 2). These forming machines use different forms of dewatering elements to accelerate the dewatering of pulp on the web. There are three types of components: stationary, rotating, and dual-use. Static components such as dehydration plates, curved vacuum boxes, etc., and rotating components such as case rollers, vacuum forming rollers, etc. In addition to using a single form of forming machine to assemble long web paper machines, circular web paper machines, and clamp web paper machines, there are also forming parts that combine multi long web, multi circular web, multi clamp web, and various forms of long web hybrid forming machines.
Pressing department
Further dehydrate the formed wet paper sheet by applying pressure. It consists of two rollers with hard and soft surfaces, such as a stone roller and a rubber roller, matched to form a set of presses. The pressing section is composed of pressing groups of the same or different forms, which traditionally also includes a vacuum suction device. When squeezing, a suitable specification of woolen cloth is used to support the paper sheet. It can evenly distribute the pressure and take away some of the water squeezed out, and enhance the pressure to improve the dewatering ability of the squeezing process. Low speed paper machines often use a line pressure of 20-60kN/m, while high-speed paper machines use a line pressure of up to 210kN/m. When using high impact pressing, such as wet paper machines, the line pressure can reach up to 350kN/m; Making rubber rollers into vacuum pressure rollers, groove pressure rollers, lining pressure rollers, blind hole pressure rollers, etc., to more effectively remove the pressing water from the pressing zone, these are new technologies adopted since the 1950s to improve the efficiency of pressing and dewatering. Afterwards, a compound pressing structure was adopted to form a closed paper feeding system. It is composed of two or three groups of presses combined, with wet paper peeled off from the forming net by vacuum suction rollers, supported by a blanket and sent to the composite press. Afterwards, the paper is transferred between the pressure rollers, eliminating the phenomenon of paper breakage caused by self weight and other factors during the press in the past. Since the 1980s, wide compression zone pressing technology has emerged, with strong and tough rubber belts or rollers that deform under strong pressure, resulting in a line pressure of up to 750kN/m and a wider contact surface, significantly extending the dehydration time and greatly improving the pressing and dehydration capacity. The effect is more prominent on high-speed paper machines. The dryness of the pressed paper can be increased from 30-37% in the past to 43-45%, and some even reach 50%. The number of times the paper comes into contact with smooth hard roller surfaces or rough adhesive surfaces, as well as the amount of dehydration on each surface, will affect the surface quality of the paper. Reasonable handling can significantly reduce the difference in smoothness between the two sides of the paper, and vice versa can also cause a difference in smoothness between the two sides.
Drying department
Several drying cylinders are driven by gears or wool cloth to form a group, and the drying section is composed of several groups of drying cylinders. The linear speed of each group of drying cylinders can be adjusted separately to maintain a slight speed difference between each group of drying cylinders to compensate for the shrinkage of paper sheets during the drying process. The dryness of the paper leaves in the drying section is generally around 92-94%. At the end of the drying section, a cold cylinder is usually equipped to allow water vapor to condense on the surface of the cold cylinder. Condensed water can wet the surface of paper sheets to achieve better surface smoothness during decoration. A drying cylinder diameter of 1.5m is effective. Single sided glossy paper can achieve high single-sided glossiness by using a large-diameter drying cylinder with high hardness and smoothness. The diameter of the large-diameter drying cylinder is generally 3-7.5m.
Surface Decoration Department
Use multiple processes to achieve good surface quality. Most papers undergo mechanical calendering after being processed by a paper machine to achieve a flat and consistent surface. The mechanical calender is made of several cold cast iron rollers, which flatten the paper surface with their own weight or additional pressure. If higher surface smoothness is required, a calender machine should be used for calendering. It is generally composed of paper pulp rollers and cold cast iron rollers arranged alternately. According to different usage requirements, some varieties require surface gluing to improve surface quality; Some require surface coating to improve appearance or printing quality. Surface gluing and coating can be processed on paper outside the paper machine using glue and coating machines, or by combining glue and coating equipment inside the paper machine for in machine processing.
drive system
Connect and synchronize the various parts of the paper machine to form an integrated mechanical and electrical system. It is composed of mechanical deceleration device, speed regulation and stabilization device, and sub transmission device, all of which use electricity as the power source.
White water system
It is a recycling, processing, and reuse system for the dewatering of the paper machine forming section. The entire system includes equipment for collecting, transporting, filtering or precipitating white water, air flotation, etc., to separate and recycle fibers and fillers for reuse, as well as to recycle clean white water in the papermaking process.
Auxiliary system
It consists of electrical system, vacuum system, lubrication system, workshop steam supply and exhaust system, paper damage treatment, compressed air system, steam supply and drainage system, etc. that are matched with the paper machine.