Thermal&Sublimation Coating Paper Machine is mainly used for the surface coating process of paper. This Paper Coating Machine is to coat the rolled base paper with a layer of Clay or chemical or paint with specific functions, and then rewind it after drying.
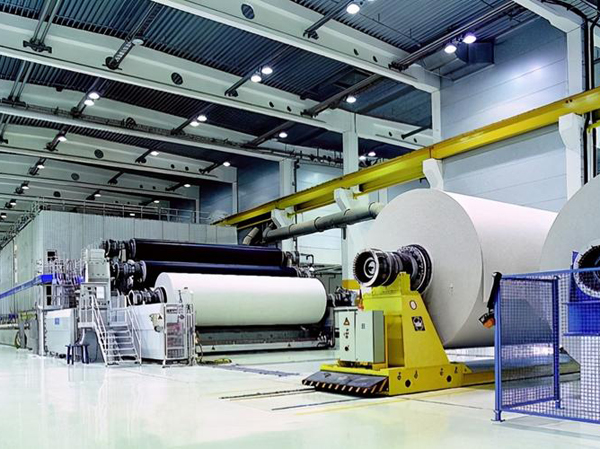
Sublimation coating paper making machine
According to the user’s requirements, the basic structure of Thermal&Sublimation Coating Paper Machine is: Double-axis unloading bracket (automatic paper splicing) → Air knife coater → Hot air drying oven → Back coating → Hot stereotype dryer→Soft calender →Double-axis paper reeler (automatic paper splicing)
Main Technical Parameter
1..Raw material: White base paper
2.Base paper weight: 50-120g/m2
3.Output paper: Sublimation Paper,Thermal Paper
4.Output paper width: 1092-3200mm
5. Capacity: 10-50T/D
6.Working speed: 90-250 m/min
7.Design speed: 120-300 m/min
8.Rail gauge: 1800-4200mm
9.Drive way: Alternating current frequency conversion adjustable speed, section drive
10.Coating method: Top coating: Air knife coating
Back coating: Mesh back coating
11.Coating amount: 5-10g/m² for top coating (each time) and 1-3g/m² for back coating (each time)
12.Coating solid content: 20-35%
13.Heat conduction oil heat dissipation:
14. Air temperature of drying box: ≥140C° (circulating air inlet temperature ≥60°) Wind pressure: ≥1200pa
15. Power parameters: AC380V/200±5% Frequency 50HZ±1
16. Compressed air for operation: Pressure: 0.7-0.8 mpa
Temperature: 20-30 C°
Quality: Filtered clean air
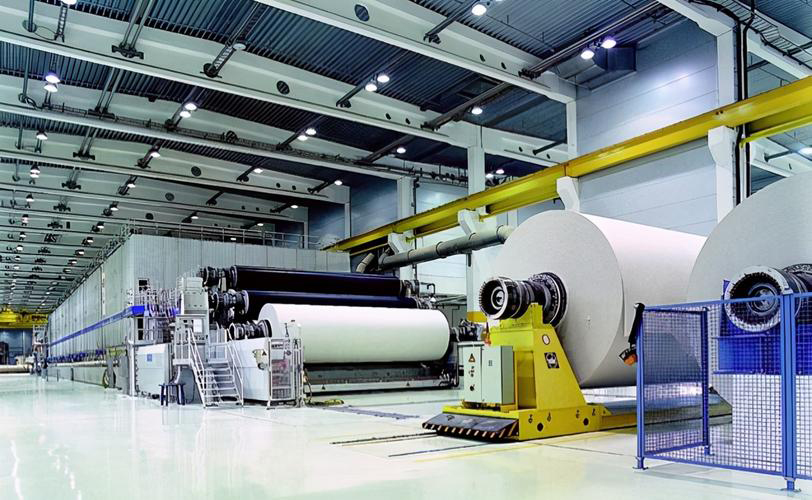
How the paper machine works
The working principle of the paper machine is mainly realized through the following parts: paper supply, stock distribution, dehydration, pressing, drying, pressing, rolling paper.
- Paper feed part: The paper raw material is cut to the appropriate size and sent through a series of conveyor belts to the next stage.
- Pulp distribution part: The pulp is screened on a rotating screen, and chemicals are added to improve its quality.
- Dehydration stage: Water is removed from the pulp by high pressure and high speed rotation.
- Pressing and drying: the pulp is compressed and further dehydrated.
- Calender: Use high pressure and high temperature to smooth the paper and improve its quality.
- Roll the paper: Roll the paper to the appropriate length and cut it.
The advantages of paper machines lie in their efficiency and flexibility. In addition, paper making machinery includes raw material preparation, pulping, paper making, until the production of rolled or flat finished products, as well as processing paper and board machinery, covering the entire production process from raw materials to finished products.