Corrugated paper production line machine is an important equipment specially used for the production of corrugated paper board, which has a wide range of applications in many industries.
First of all, corrugated cardboard is widely used in the construction industry, and can be used to process doors, partitions, ceilings, wall skirts, floors, siding, mobile rooms, open office partitions, etc. Its characteristics of light weight, high strength and good toughness make it very suitable for the manufacture of building materials.
Secondly, in the furniture industry, corrugated cardboard is also an important raw material, which can be used to make a variety of panel furniture and general civilian furniture, such as writing desk, desk, wall cabinet, combined cabinet, bed board, etc. Its strength and durability make the furniture more stable and durable.
In addition, corrugated cardboard also has a good application in the transportation industry. It is one of the ideal alternative materials for wood products and wood-based panels in buses and passenger ships, helping to reduce the weight of vehicles and ships and improve transportation efficiency.
In the field of packaging, the role of corrugated cardboard is indispensable. It can be used for the packaging of precision machine tools, instruments, tools, household appliances, electronic and computer products, auto parts and glass, food and other products. Corrugated cardboard has the characteristics of low cost, light weight, easy processing, high strength, excellent printing adaptability, convenient storage and handling, making it an ideal choice for the packaging industry. Moreover, more than 80% of corrugated paper can be recycled, which is relatively environmentally friendly, which also meets the requirements of the modern packaging industry for environmental protection and sustainable development.
In general, corrugated paper machines provide important raw materials for many industries such as construction, furniture, transportation and packaging by producing high-quality corrugated board, and promote the development and progress of these industries.
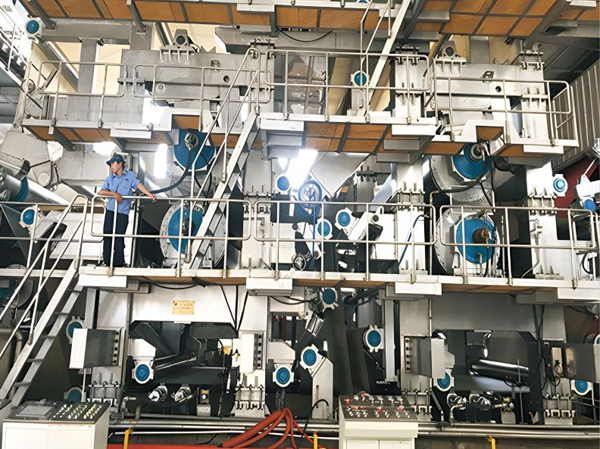
Corrugated paper making machine
Product:Low GSM High Strength Fluting
Trimmed Width:3200-6600 mm
Design Speed:300-1000m/min
Gram Weight:70-140g/m²
Production Capacity:50,000-200,000 Tyr
Product:A Grade High Strength Corrugated Paper
Trimmed Width:3200-6600 mm
Design Speed:300-1000m/min
Gram Weight:100-160g/m²
Production Capacity:50,000-300,000 T/Yr
Corrugated boxes are the most widely used shipping container in commerce. They are made by folding and gluing corrugated cardboard. Corrugated cardboard is made of surface paper and corrugated core paper formed by processing corrugated sticks. Generally, corrugated cardboard has a dedicated corrugated paper production line to produce and cut into the cardboard of the required specifications. Today, we will talk about the Corrugated paperboard production line.
Corrugated Paper Production Line
Corrugated paper board production line plays an important role in the production of a corrugated cardboard box. The corrugated cardboard production line is the most important production line equipment in carton packaging enterprises. It includes several important components such as wet section equipment, cadre equipment, and production management system.
Finished Product: Fluting paper, Testliner paper, Kraft paper, Colorful Paper Cup, Cardboard Paper Machine, Paper Board, Paper Drinking Straw
Technical Parameters of Corrugated paperboard production line
Model | YG-1100PC-A |
Suitable paper | 200-800 g / m2 cardboard, E-F-N corrugated board |
Box type | Straight line, crash-lock bottom, double sides, four/six corner box |
Feeding way | Continuous automatic feeding. |
Glue type | Solute style |
Max. speed | 400m/min |
Power | 31KW, AC220V/380V |
Weight | 11T |
Dimension | 19000mm*2050mm*1600mm(L*W*H) |
Inching speed | 40m/min |
Compressed air | 6 bar |
Air compressor capacity | 10m/3 |
Air tank capacity | 60L |
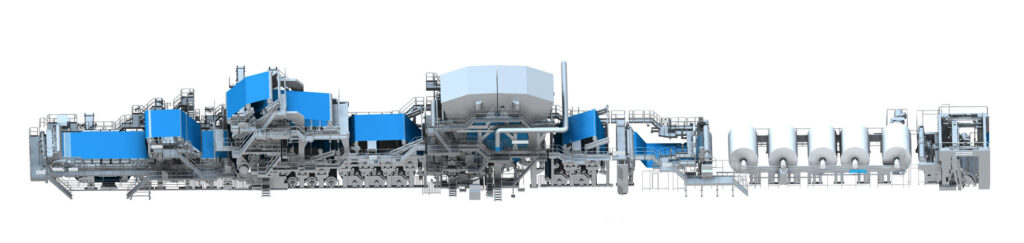
Process Flow Diagram of automatic corrugated paper board production line
Raw materials (waste paper)——chain conveyor——pulper——hign density cleaner——pressure screen——fiber separator——reject separator ——low density cleaner——inflow pressure screen——paper making machine——the big finished jumbo paper
The main components of corrugated paper production line
The long net multi cylinder corrugated paper machine consists of a slurry box system, a long net section, a pressing section, a drying section, an open hood, a transmission section, a foundation section, a pneumatic control system, a thin oil lubrication system, an electrical control system, and a horizontal pneumatic paper winding machine.
Slurry box
Air cushion headbox is adopted, which is mainly composed of square cone header, stepped diffuser, homogenizer roll, box, spray tube, air cushion adjustment device, upper and lower lip plates and adjustment device. The upper lip plate can be adjusted horizontally and vertically, and there is a vertical small lip plate at the nozzle.
Changwang Department
The net case adopts fully static dehydration components, mainly composed of chest rollers, forming plates, three piece and five piece dehydration plates, low vacuum wet suction boxes, high vacuum suction tanks, vacuum voltage rollers, drive rollers, cantilever beam net stand, pneumatic corrector, pneumatic constant tension tensioner, electric tensioner, electric high-pressure needle shaped mobile water spray device, low-pressure water spray pipe device, white water tray, and paper loss pool of voltage rollers.
Pressing department
The press frame is a gantry style structure with welded steel plates, and all connecting beams of the press are wrapped in stainless steel. When changing the woolen cloth, use a hydraulic jack to slightly lift the operating frame, and pull out the cushion block to make the frame in a cantilever state, making it extremely easy to replace the woolen cloth; Equipped with railings and walkways.
Drying cadres
The drying cylinder adopts rolling bearings, and each drying cylinder is equipped with a rotating steam inlet head, siphon tube, and cleaning scraper; The dryer transmission adopts a closed gearbox transmission and centralized lubrication with thin oil. The adjustment of the woolen fabric adopts an electric tensioner, a pneumatic corrector, and a polyester dry mesh with a dry mesh tension of 4KN/M.
Transmission Machinery Department
Adopting AC variable frequency motor sub transmission and variable frequency speed regulation, there are a total of 15 main transmission points, mainly composed of electric motor, ZLY hard tooth surface gearbox, universal joint, column pin coupling, transmission shaft, base plate, etc.
Thin oil lubrication system
The thin oil station is located in the middle of the drying section (specific to be considered in the process design). Oil is supplied to the operating side and transmission side frame of the dryer through the conveying pipeline, and the oil is manually adjusted and sent to each lubrication point through the oil distributor. The lowest point of each lubrication point (dryer bearings, dryer transmission gears, press roller bearings, and roller bearings) is equipped with a return oil pipeline to allow the lubricating oil to flow back to the lubrication station by itself.
Compressed air control system
Including: corrector control, pneumatic control of the pressing section, vacuum pressure roller, lifting and pressing of each pressure roller in the pressing section, three curved pneumatic tire and other devices, as well as the pipeline parts of each gas consumption point. The corrector control box is placed on a nearby column or rack, and the pneumatic control box for the pressing section is placed on the operating side corridor of the pressing section. The air used for supplying tires should not only have stable pressure requirements, but also be a clean and oil-free air source. It is recommended that users use oil-free lubricated air compressors.
Open hood section
The hood is an open type hood, divided into two parts: the front and rear parts, with the upper part of the hood fixed. The hood is composed of wall panels, top panels, ventilation ducts, movable sliding doors, exhaust ducts, and supporting frames. The wall panel is made of corrugated aluminum plate, the top plate is made of insulated double-layer aluminum plate (with rock wool filling in the interlayer), and the rectangular ventilation duct is located under the top plate. There are movable plates on both sides of the ventilation duct to adjust the extraction volume of evaporated water vapor in each section of the drying cylinder. The ventilation duct is connected to the exhaust duct and leads to the outside of the transmission side wall panel. The user provides their own air duct and exhaust fan. The front and rear ends of the bottom of the hood are equipped with water tanks.
electric control system
Series variable frequency AC three-phase asynchronous motor with temperature protection device is selected. Adopting an AC frequency converter with speed and load distribution functions, it has strong reliability, comprehensive functions, and high accuracy.
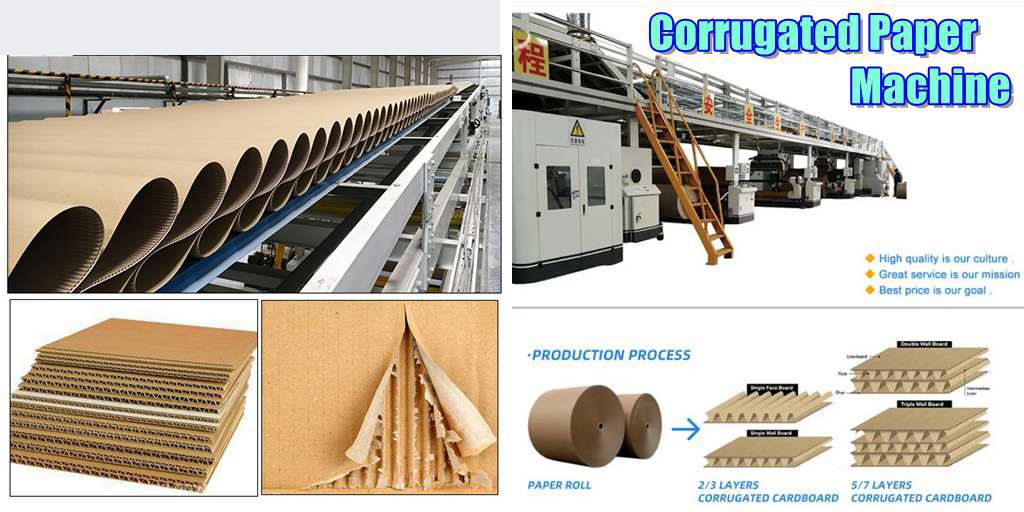
Project Overview: Examples of Practical Cases in Corrugated Paper Processing Plants
This project plans to use waste paper to produce packaging paper such as corrugated paper, kraft paper, and box board paper with a weight of 70-300g/m. The main equipment consists of a pulp production line, a papermaking press drying unit, and a paper processing completion department.
1、 Main technical parameters:
- Production varieties: corrugated paper, box board paper, kraft paper, packaging paper, yarn tube paper, hanging paper, cup paper, etc
- Quantitative range: 70-300g/m2
- Paper width: 1575-3800mm
- Daily production: 10-100t/d
- Working speed: 80-400m/min
- Design speed: 450m/min
- Pressure method: Pneumatic pressure
- Track gauge: 2400-4900mm
- Transmission mode: AC variable frequency speed regulation, segmented transmission
2、 Paper machine configuration form:
- Molding department configuration: composed of multi round mesh, pressure forming machine round mesh, super forming, single long mesh, double long mesh, and stacked mesh.
- Pressing section configuration: open pressing, vacuum pressing, large roller pressing, three roller two pressure zone composite pressing (commonly known as K-pressing), 606 structure composite pressing, etc.
- Drying cadre configuration: composed of multiple cylinders. The transmission form can be divided into open gear and closed gearbox transmission configurations.
It can be configured with various models of glue dispensers, hot pressing machines, and semi dry pressing machines.
- Complete department configuration: various models of cylindrical paper winding machines, horizontal paper winding machines, etc.
- Paper processing configuration: Various models of ordinary rewinding machines.
The above paper machine configuration form is chosen by the customer themselves.