The wrapping packing paper production line can process kraft paper, chicken skin paper, paper bag paper, parchment paper, cellophane paper, asphalt paper, moisture-proof paper, gunpowder wrapping paper, neutral wrapping paper, translucent paper, rust proof paper, greaseproof paper, food wrapping paper, wax paper, tea bag paper, red electric light gun paper, vacuum aluminized paper, composite paper, etc.
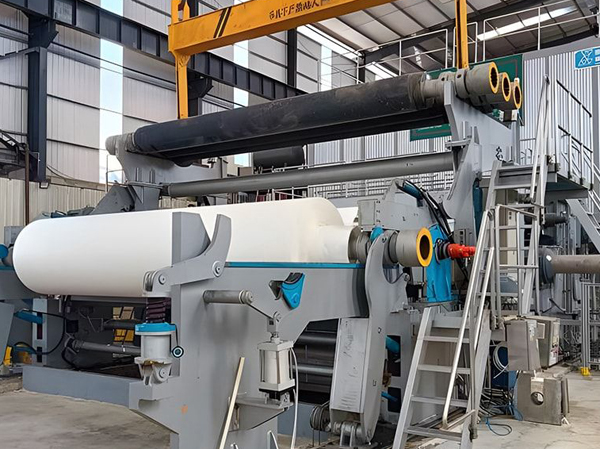
Automatic wrapping packing paper production line
A general term for a type of paper used for packaging purposes. It can be divided into ordinary packaging paper, specialized packaging paper, trademark paper, oil resistant packaging paper, and moisture-proof packaging paper. Usually has high strength and toughness. Various types of packaging paper have different properties and uses. For example, specialized fruit packaging paper is thin and soft. The photosensitive protective paper is opaque. Oil resistant packaging paper (such as vegetable parchment paper) has the ability to prevent oil penetration. Moisture resistant packaging paper (such as asphalt paper, oil paper, aluminum foil paper, etc.) has moisture resistance. Trademark paper is used for packaging after printing.
Detailed explanation of packaging paper paper making process flow
1、 Pulp preparation
- Raw material selection
- The pulp preparation of packaging paper mainly uses waste paper, wood, grass and other plants as raw materials. Waste paper is an important raw material for making packaging paper, which can be divided into recycled paper and waste cardboard. Choose high-quality and pollution-free waste paper as the raw material.
- Pulp making process
- The pulp making process mainly involves adding water to the raw materials and decomposing them into cellulose of a certain particle size through mechanical or chemical treatment, forming pulp. Pulping equipment can be divided into two types: mechanical pulping and chemical pulping. Mechanical pulping is relatively simple and suitable for raw materials with longer cellulose content, such as wood and grass. Chemical pulping is suitable for waste paper with shorter cellulose content.
2、 Paper making process
The papermaking process mainly includes operations such as pulp forming, wet paper drying, calendering and smoothing, coating and laminating.
- Slurry forming: Spread the prepared pulp evenly on the forming net, and use methods such as shaking, pressing, etc. to evenly arrange the pulp on the forming net to form a paper skeleton.
- Wet paper drying: After multiple presses, the paper frame is sent to the drying section for drying, compression, and other operations to gradually increase the compactness of the paper, achieving the desired dryness and strength.
- Smooth calendering: The dried packaging paper is calendered by a calender machine to make the surface smooth and improve the appearance quality.
- Glue coating and lamination: Some packaging papers need to be treated with glue coating and lamination to change their surface properties and increase their waterproof, moisture-proof and other characteristics.
3、 Processing and processing
- Cutting processing
- Cut the finished paper according to the specified specifications, usually by flattening it and using a cutting knife to cut it to the desired width and length.
- Printing processing
- Printing processing is the process of printing packaging paper into various patterns, beautifying the packaging, and enhancing the brand image.
- Reinforcement treatment
- In order to increase the strength and durability of packaging paper, reinforcement treatments such as glue coating and film covering are often required.
4、 Environmentally friendly production
In the production process of packaging paper, attention should be paid to environmentally friendly production to reduce pollution to the environment. This can be achieved by selecting renewable raw materials, optimizing process flow, and strengthening waste disposal. At the same time, attention should be paid to operational skills and equipment adjustments to reduce environmental pollution and resource waste.
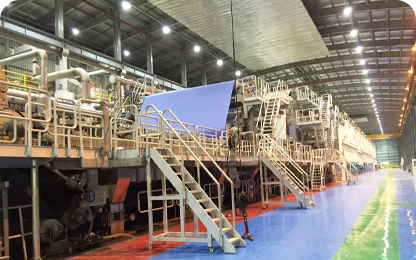
Fluting Paper line
Paper Grade: A Fluting Paper
Basic weight: 60–150 GSM
Net paper Width: 4600-6600 mm
Yearly capacity: 50,000 tons-400,000 tons
Operation speed: 1200 m/min
Design speed: 1400 m/min
Kraft & Testliner line
Paper Grade: Kraft & Testliner
Basic weight: 120–280 GSM
Net paper Width: 4600-6600 mm
Yearly capacity: 50,000 tons-500,000 tons
Operation speed: 1200 m/min
Design speed: 1400 m/min
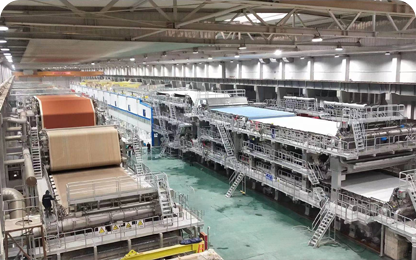
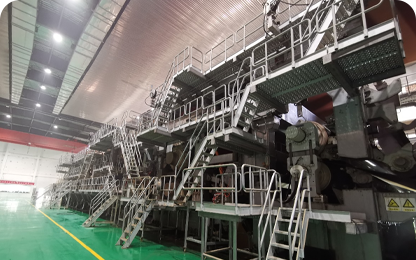
Duplex Board Machine
Grade: Duplex Board
Basic weight: 150–400 GSM
Net paper Width: 3400-6600 mm
Yearly capacity: 50,000 tons-600,000 tons
Operation speed: 1000 m/min
Design speed:1200 m/min