Waste paper production line to waste paper, waste carton, waste paper shell, waste book paper, waste newspaper and so on as raw materials, the production of wrapping paper, toilet paper. According to the production of paper varieties of raw materials for waste books, white paper or old box board paper, the production of low-grade toilet paper and wrapping paper.
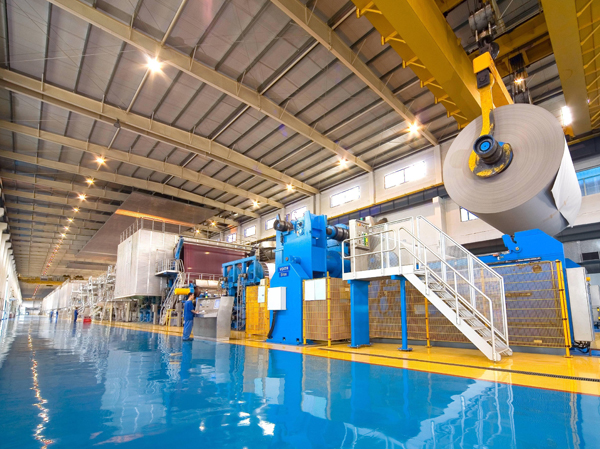
Automatic waste paper pulping production line
Waste paper production line
Paper type: Grade A base paper
Quantitative: 60-150 GSM
Clean paper width: 4600-6600mm
Annual output: 50,000 tons – 800,000 tons
Maximum working speed: 1600 m/min
Design speed: 1900 m/min
Category of waster paper processing paper production line
Production Name | 1092 paper Production line |
---|---|
Number | 1092 |
Output paper | Kraft paper /corrugated paper |
Daily Capacity | 4-6T/D |
Raw material | waster paper |
Net Paper Width | 1100-1200mm |
Product weight(GRM) | 100-150g/m² |
Design Speed | 80-140m/min |
Work speed | 60-120m/min |
speed regulation mode | VVVF |
pulp distributing way | Circular arc plate of garden net |
Press Dehydration way | dryer roller |
drying way | steam |
Installation way | left and right model |
class people | 5-6people/class |
Production Name | 1575 paper Production line |
---|---|
Number | 1575 |
Output paper | Kraft paper /corrugated paper |
Daily Capacity | 8-10T/D |
Raw material | waster paper |
Net Paper Width | 1600-1800mm |
Product weight(GRM) | 100-200g/m² |
Design Speed | 80-140m/min |
Work speed | 60-120m/min |
speed regulation mode | VVVF |
pulp distributing way | Circular arc plate of garden net |
Press Dehydration way | dryer roller |
drying way | steam |
Installation way | left and right model |
class people | 5-6people/class |
Production Name | 1760 paper Production line |
---|---|
Number | 1760 |
Output paper | Fluting paper, test liner paper |
Daily Capacity | 18-25T/D |
Raw material | waster paper |
Net Paper Width | 1600-1800mm |
Product weight(GRM) | 100-350g/m² |
Design Speed | 80-140m/min |
Work speed | 60-120m/min |
speed regulation mode | VVVF |
pulp distributing way | Circular arc plate of garden net |
Press Dehydration way | dryer roller |
drying way | steam |
Installation way | left and right model |
class people | 5-6people/class |
Production Name | 1880 paper Production line |
---|---|
Number | 1880 |
Output paper | Fluting paper, test liner paper |
Daily Capacity | 20-25T/D |
Raw material | waster paper |
Net Paper Width | 1800-2000mm |
Product weight(GRM) | 120-310g/m² |
Floor area | 1200–1500m² |
Cylinder mold width | 2300mm |
Rail gauge | 2900mm |
Factory Width | 8m |
Factory Height | 6.5m |
Design Speed | 70-200m/min |
Work speed | 70-150m/min |
speed regulation mode | VVVF |
pulp distributing way | Circular arc plate of garden net |
Press Dehydration way | dryer roller |
drying way | steam |
Installation way | left and right model |
class people | 8-12people/class |
Suitable voltage | 220-380-440V |
Production Name | 2100 paper Production line |
---|---|
Number | 2100 |
Output paper | Fluting paper, test liner paper |
Daily Capacity | 20T/D |
Raw material | waster paper |
Net Paper Width | 2100mm |
Product weight(GRM) | 80-420g/m² |
Design Speed | 80-140m/min |
Work speed | 60-120m/min |
speed regulation mode | VVVF |
pulp distributing way | Circular arc plate of garden net |
Press Dehydration way | dryer roller |
drying way | steam |
Installation way | left and right model |
class people | 7-9people/class |
Production Name | YD2400 Paper Production Line |
---|---|
Output paper | Kraft paper |
Daily Capacity | 20T/D |
Raw material | Waste paper |
Net Paper Width | 2400mm |
Product weight | 60-320g/m² |
Floor area | 1600m² |
Factory Width | 10m |
Factory Height | 5m |
Design Speed | 80-140m/min |
Work speed | 60-120m/min |
Suitable voltage | 220-380-440V |
pulp distributing way | Circular arc plate of garden net |
Press Dehydration way | dryer roller |
drying way | steam |
Installation way | left and right model |
Worker Number | 7-9workers |
Production Name | 3200 paper Production line |
---|---|
Number | 3200 |
Output paper | Fluting paper |
Daily Capacity | 40-50T/D |
Raw material | waster paper |
Net Paper Width | 3200mm |
Product weight(GRM) | 100-200g/m² |
Floor area | 3200–4000m² |
Cylinder mold width | 3300mm |
Factory Width | 10m |
Factory Height | 8m |
Design Speed | 80-140m/min |
Work speed | 60-120m/min |
speed regulation mode | VVVF |
pulp distributing way | Circular arc plate of garden net |
Press Dehydration way | dryer roller |
drying way | steam |
Installation way | left and right model |
Suitable voltage | 220-380-440V |
class people | 8-12people/class |
Production Name | YD3600 Paper Production Line | |||||||
Output paper | kraft paper | |||||||
Daily Capacity | 25-30T/D | |||||||
Raw material | Waste paper | |||||||
Net Paper Width | 4200mm | |||||||
Product weight | 90-180g/m² | |||||||
Floor area | 2000–2400m² | |||||||
Factory Width | 10m | |||||||
Factory Height | 8m | |||||||
Design Speed | 100-180m/min | |||||||
Work speed | 60-140m/min | |||||||
Suitable voltage | 220-380-440V | |||||||
Worker Number | 7-9workers/class |
Production Name | 4200 paper Production line |
---|---|
Number | 4200 |
Output paper | Fluting paper, test liner paper |
Daily Capacity | 50T/D |
Raw material | waster paper /Virgin pulp |
Net Paper Width | 4200mm |
Product weight(GRM) | 100-190g/m² |
Floor area | 4000m² |
Cylinder mold width | 4800mm |
Factory Width | 15m |
Factory Height | 8m |
Design Speed | 120-250m/min |
Work speed | 100-200m/min |
speed regulation mode | VVVF |
pulp distributing way | Circular arc plate of garden net |
drying way | steam |
Installation way | left and right model |
Suitable voltage | 220-380-440V |
class people | 8-12people/class |
Waste paper The process of producing paper
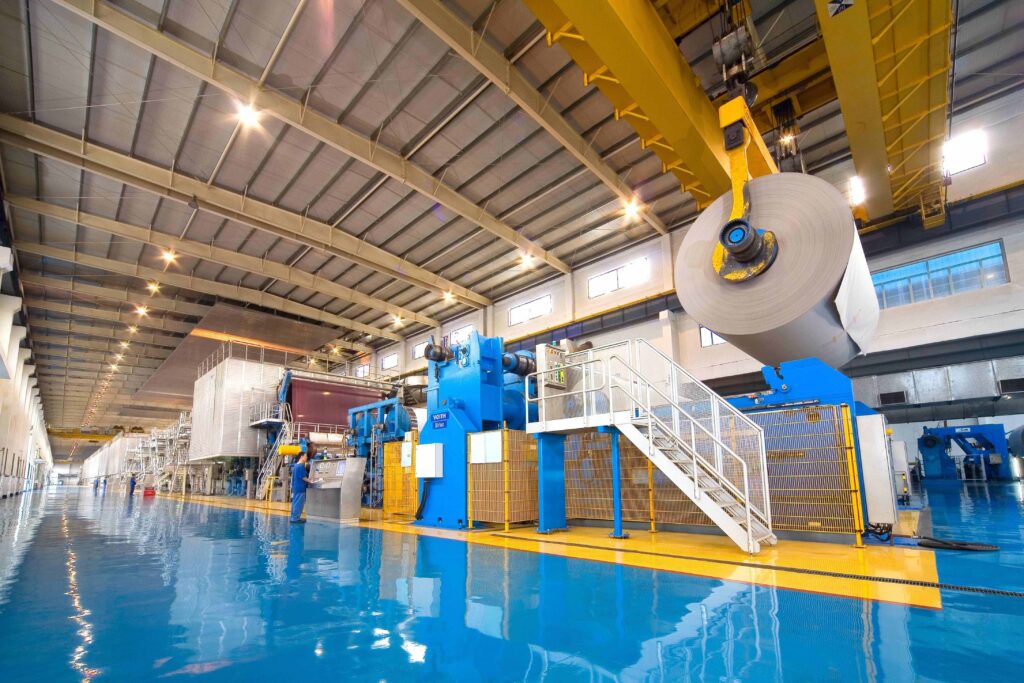
First, waste paper recycling and treatment
- Waste paper collection:
Collect waste paper from a variety of sources, including waste paper from homes, offices, printing plants, etc.
- Waste paper classification:
The collected waste paper is sorted to remove impurities such as plastic, metal, glass, etc.
- Crushing and cleaning:
Use a crusher to break the waste paper into smaller pieces for subsequent processing.
Clean the broken waste paper to remove dust, oil and other pollutants on the surface.
Second, the pulping process
- Hydraulic crushing:
The cleaned waste paper fragments are sent to the hydraulic pulper for beating and deinking. The hydraulic pulper will hydraulically break up scrap paper and remove ink and other impurities from it.
- Screening and removing impurities:
The beaten pulp is screened through a high-frequency vibrating screen to remove large particles and unbroken impurities.
- Bleaching and bleaching:
The filtered pulp is fed into the rinsing machine for further cleaning to remove residual ink and impurities.
According to the need, the pulp is bleached to improve the whiteness and appearance quality of the toilet paper. Chemicals such as sodium hypochlorite are used in the bleaching process.
- Grinding and impurity removal:
The bleached pulp is sent to the pulp mill for fine grinding to make the pulp more fine and even.
Use the sand table and other equipment to separate the sediment of impurities such as sand and ash in the pulp to make pure pulp.
Three, the papermaking process
- Pulp preparation:
Add appropriate amount of water and chemicals to the pure pulp to form a stable and uniform pulp.
- Paper machine forming:
The prepared pulp is fed into the paper machine, and the paper machine evenly spreads the pulp on the mesh belt.
Through the action of a series of rollers and pressure rollers, the paper pulp is formed on the mesh cloth with a certain thickness and uniformity.
- Pressing and drying:
The formed web is pressed to improve its tightness and strength.
The pressed web is sent to the dryer for high temperature drying treatment to remove the moisture and form dry toilet paper.
- Processing and packaging
- Rewinding and punching embossing:
The large roll of dried toilet paper is rerolled and rerolled into small rolls.
Punching and embossing are carried out during the rewinding process to make it easier for consumers to use and tear the toilet paper.
- Cutting and packaging:
The rerolled small roll of toilet paper is sent into the slitting machine for slitting processing to form specifications and sizes that meet the market demand.
Packaging of the cut toilet paper, such as the use of plastic film, carton, etc., to protect the toilet paper from contamination and damage.
Four.Processing and packaging
- Rewinding and punching embossing:
The large roll of dried toilet paper is rerolled and rerolled into small rolls.
Punching and embossing are carried out during the rewinding process to make it easier for consumers to use and tear the toilet paper.
- Cutting and packaging:
The rerolled small roll of toilet paper is sent into the slitting machine for slitting processing to form specifications and sizes that meet the market demand.
Packaging of the cut toilet paper, such as the use of plastic film, carton, etc., to protect the toilet paper from contamination and damage.
Five.Quality control and environmental measures
In the entire production process, the quality and technical parameters of each link need to be strictly controlled to ensure that the produced toilet paper meets national standards and market demand.
At the same time, take the necessary environmental protection measures, such as the use of environmentally friendly chemicals, reduce wastewater discharge, recycling waste, etc., in order to reduce the impact on the environment.
Through the above steps, waste paper can be effectively converted into high-quality toilet paper products, to achieve the goal of recycling resources and reducing environmental pollution.