Kraft paper production line are categorized into kraft paper machines, corrugated paper machines, paperboard machines, etc. according to the type of paper produced. According to the type of paper former used, paper machines are divided into long mesh, round mesh, clip mesh and long round mesh models.
A paper machine can be viewed as a coupling machine consisting of several pieces of equipment. It is usually divided into two main parts: the wet part and the dry part. Wet section includes pulp flow equipment, net section and press section. Cadre includes the drying section, calender and winder.
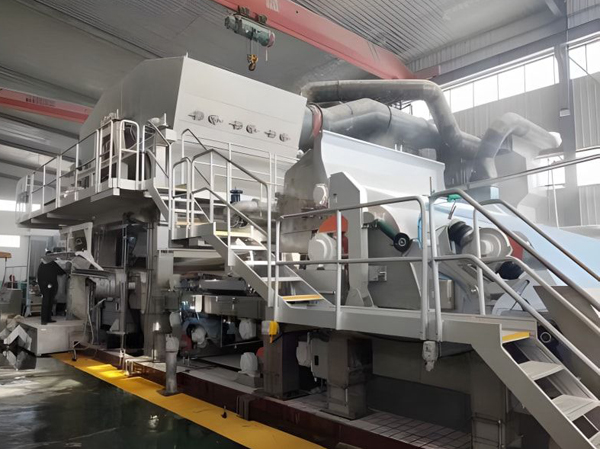
Automatic kraft paper production line
The kraft paper machine can use various waste paper, recycled old cardboard boxes, wheat or straw, sugarcane bagasse, virgin pulp, cotton, wood, etc. as raw materials to make kraft paper, and the finished product can be a large paper roll. This product is a 3900mm, 200m/min pressure forming multi cylinder paper machine, mainly used for producing 100-300g/m2 products. The main product is high-strength liner paper, and all products are rolls. The main components of this paper machine include the turning section, forming section, pressing section, drying section, cover section, size pressing section, winding machine, base section, mechanical transmission and electrical control section. We have a complete kraft paper machine production line, as well as various spare parts for kraft paper machines, and professional engineers to provide installation and after-sales service for you.
Kraft paper machines are categorized into kraft paper machines, corrugated paper machines, paperboard machines, etc. according to the type of paper produced. According to the type of paper former used, paper machines are divided into long mesh, round mesh, clip mesh and long round mesh models.
A paper machine can be viewed as a coupling machine consisting of several pieces of equipment. It is usually divided into two main parts: the wet part and the dry part. Wet section includes pulp flow equipment, net section and press section. Cadre includes the drying section, calender and winder.
1. Net section
Net is mainly used to remove the water in the pulp, it bears the vast majority of the dehydration task, in addition to a certain degree of disturbance to the pulp, while making the paper has a good molding, which consists of the top net and low net composition, the two nets are designed to make the paper in the water to the paper on both sides of the paper to take off, so as to reduce the two-sided nature of the paper.
In the design of the full consideration of the convenience of changing the net and the use of cantilever beam structure, its main components are molding board, dewatering board, vacuum case box, the upper suction box, loading table and preloading table, vacuum suction box, ambush roll, chest roll guide roll and doctor blade, drive net roll, water needle and high-pressure water spraying water and other components.
2. Press section
The press section of the paper machine is composed of several groups of roller presses. The wet paper web is drawn by the press felt and dewatered by mechanical extrusion between the press rolls. In order to maintain the good dewatering performance of the press felts, the upper rolls of the press are equipped with a felt washing device. After the press section, the dryness of the wet paper web is generally up to about 40%.
Technical Parameter
Product | Kraft Paper Machine |
Weight range | 100-300g/m2 |
Trim paper width | 3900mm |
Rolled paper width | 3950mm |
Production capacity | 120t/d |
Working speed | 130-200m/min |
Design speed | 200m/min |
Crawling speed | 25m/min |
Wire width | 4400mm |
Rail distance | 4900mm |
Transmission method | AC Motor Division drive |
Arrangement model | one layer arrangement |
The main products | high strength corrugated paper,Kraft liner paper |
Production Name | YD3600 kraft Paper Production Line | |||||||
Output paper | kraft paper | |||||||
Daily Capacity | 10-30T/D | |||||||
Raw material | Waste paper | |||||||
Net Paper Width | 4200mm | |||||||
Product weight | 90-180g/m² | |||||||
Floor area | 2000–2400m² | |||||||
Factory Width | 10m | |||||||
Factory Height | 8m | |||||||
Design Speed | 100-180m/min | |||||||
Work speed | 60-140m/min | |||||||
Suitable voltage | 220-380-440V | |||||||
Worker Number | 7-9workers/class |

Production process of kraft paper production line
Raw material(waste paper)—— Pulper——Vibrating screen——Grinder——Stuff pump——Blender——Fiber Separator——Pressure screen——Main paper making machine——Paper Rewinding machine

Application&Feature of kraft paper production line
1.Headbox : Two sets of open headbox, corresponding to top layer, bottom layer, and by controlling the gas pressure in the headbox to control and stabilize the sizing of the pulp.
2.Forming section : Double layer include top layer and bottom layer, The main components are consist of breast roll , forming board, dewatering board, vacuum box, composite roll, suction couch roll, wire drive roll, wire guiding roll and paper machine framework.Top layer and bottom layer are all equipped with one forming wire respectively .
3.Press section: including First press, second press.The first press is K-type composite press with vacuum suction roll, which also equipped with one rubber coated metal roller, one vacuum press roll and one stone roll.The second press is MG press with upper & lower rubber coated metal rolls and upper & lower felts. The two press are all equipped with wire guiding roll and felt suction box. These two press are pressurized by the hydraulic cylinder pressure.
4.Front drying section: Φ1500/Φ1800 dryer, drove in group and equipped with wire guiding roll , dry wire and closed gas hood.
5.Oblique surface sizing machine: one surface chrome-plated metal roller and one rubber coated metal roll. it is pressurized by corrugated gas tire pressure.
6.Back drying section: Φ1500/Φ1800 dryer drove by group and equipped with wire guiding roll ,dry wire and closed gas hood.
7.Calender section: Double roller calender, the upper and lower rollers are metal rollers, pressurized way is the corrugated gas tire pressure.
8.Reel section: Pneumatic horizontal reel and pressurized way is cylinder pressure.