The products of yarn tube paper production line are mainly used in the production of core and pipe, industrial pipe, film pipe, fireworks tube, textile tube, spiral tube, pagoda tube, parallel tube, all kinds of paper corner guard, carton, honeycomb cardboard and so on.
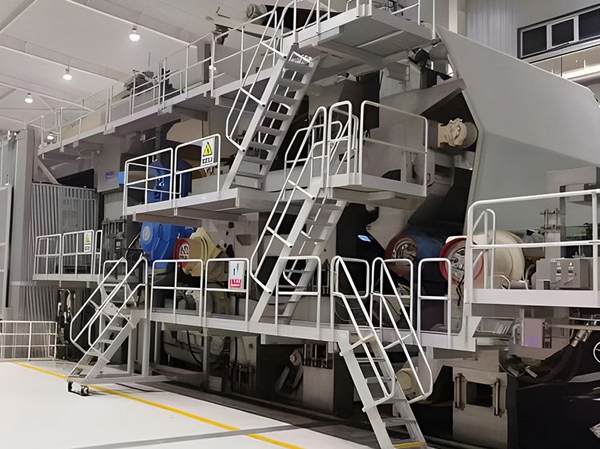
Automatic yarn tube paper production line
A type of industrial paper specifically designed for the textile industry to produce paper yarn tubes and conical paper tubes. It is a thin steel paper. The quantification is 65g/m2 and 145g/m2. Thickness of 0.1-0.2mm. The basis weight of the yarn tube cardboard is 85-510g/m2. Paper is tough and wear-resistant. The paper surface is smooth and even. Has good water resistance (with a sizing degree of not less than 1.25mm). Can resist edge indentation and withstand lathe machining during use. In order to distinguish between the rows of yarn tubes on the spinning machine, various colors such as red, orange, yellow, green, blue, etc. are often dyed during use, and the dyeing is firm. Using bleached or unbleached chemical wood pulp as raw material, the paper is made by free pulping and coloring with dyes on a long web paper machine, then compressed and rewound into a roll paper shape, and further processed into lightweight and easy-to-use yarn tubes.
Detailed explanation of the papermaking process and professional knowledge of yarn tube paper
Yarn tube paper, as an indispensable packaging material in the textile industry, has a certain degree of professionalism and technicality in its papermaking process. Next, we will delve into the papermaking process of yarn tube paper and related professional knowledge.
1、 The production process of yarn tube paper
The production process of yarn tube paper includes steps such as pulp preparation, paper sheet forming, pressing, drying, and finishing. In the pulp preparation stage, it is necessary to select suitable fiber raw materials and perform pulping treatment to obtain pulp suitable for papermaking. The paper forming stage is to evenly distribute the slurry on the forming net through a flow box, forming wet paper sheets. Subsequently, the moisture in the paper is removed through pressing and drying steps, followed by finishing treatment to achieve the desired quality and performance of the yarn tube paper.
2、 Raw material selection and processing
The main raw materials for yarn tube paper are high-quality waste paper or other cellulose fibers. When selecting raw materials, factors such as fiber length, strength, and water absorption need to be considered. At the same time, in order to improve the strength and durability of the yarn tube paper, it may be necessary to add some chemical additives, such as reinforcing agents, sizing agents, etc. After being processed through crushing, screening, purification, etc., the raw materials can be used for papermaking.
3、 Paper machine operation and adjustment
The operation and adjustment of the paper machine are crucial in the papermaking process of yarn tube paper. Operators need to adjust the parameters of the paper machine in real time according to the production situation, such as pulp concentration, mesh speed, pressing pressure, etc., to ensure stable quality of the produced yarn tube paper. In addition, it is necessary to regularly inspect and maintain the paper machine equipment to ensure its normal operation and extend its service life.
4、 Quality Control and Testing
In order to ensure that the quality of the yarn tube paper meets the standards, strict quality control and testing are required during the production process. This includes physical performance testing of raw materials, semi-finished products, and finished products (such as tensile strength, tear resistance, flexural strength, etc.), visual inspection, and chemical performance analysis. Through these detection methods, problems in the production process can be detected and dealt with in a timely manner, ensuring the stable and reliable quality of the yarn tube paper.
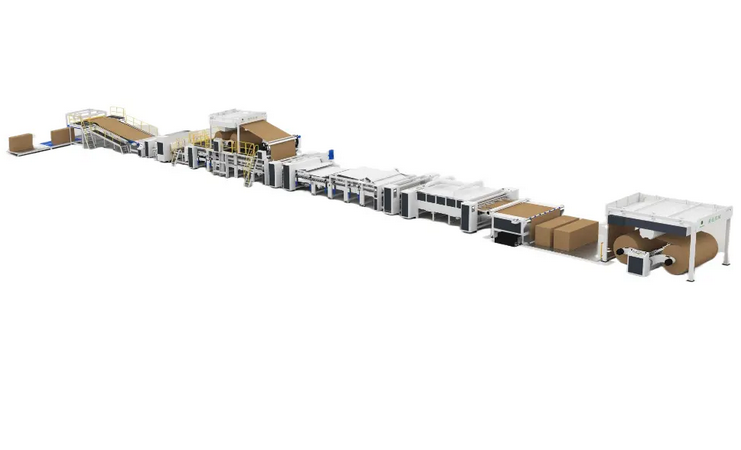
Precautions for use
When producing yarn tube paper, manufacturers need to pay close attention to safety issues. Operators should wear personal protective equipment correctly. It is necessary to wear what should be worn, and if not, they must not wear it.
Before operation, it is necessary to conduct a safety check on the paper tube machinery equipment and perform an empty operation. Only after confirming that it is normal can it be put into operation. Paper tube machinery equipment should be inspected for safety according to rules during operation, especially for fastened objects to see if they have become loose due to oscillation, in order to tighten them from the beginning. During the operation of paper tube machinery, manual adjustment is prohibited; It is also not allowed to measure parts by hand, lubricate or clean debris. If necessary, the mechanical equipment should be shut down first. Equipment must not be operated with defects, and must not be used casually to prevent accidents.
After completing the homework, the switch should be closed, the cutting tools and workpieces should be removed from the work position, and the work site should be organized. The parts, fixtures, etc. should be placed neatly, and the hygiene of the paper tube machinery equipment should be cleaned.
Application&Feature
Main Paper Machine Is Divided Into The Following Parts
Cylinder mould part,Return back press size part, Press part, Drying part, Reeling part
1.Cylinder mould part: the cylinder mould part is equipped with seven cylinders, main components: each cylinder is with a wire tank, a piece couch roll, a vacuum dehydration box,and guide roll, frame, etc., and share a bottom felt with 1st press.
2.Return back press part: in the wire part return back position, set the vacuum return back 1st press, the upper roll is metal roll coated with rubber, the lower press roll is the double vacuum chamber vacuum return back roll equipped with a return back press top felt. Return back press is double felt press.
3.Press part: divided into 1st press, 2st press, 3st press. 1st press is vacuum press, the top roll is metal roll coated with rubber, the bottom roll is vacuum press roll, and with top and bottom felt; 2st press, 3st press are large diameter press roll, each equipped with two coated metal roll, and with top and bottom felt. 1st press, 2st press are all equipped with felt roll and felt suction box, and top, bottom felt. 1st press, 2st press, 3st press pressurized type is corrugated tire pressure.
4.Drying part: Φ1500 / Φ1800 dryer cylinder, sub-drive, with guide roll, wire leading roll. It is equipped with semi-closed hood.
5.Reeling part: Pneumatic Horizontal Reeling Machine.