The machines required for a4 paper processing plants are sanitary paper machines, rewinding equipment, pulping equipment (pulper, pressure screen, slag remover, pulp pump), chain conveyor, boiler, sewage treatment system, etc. A4 paper is defined by the International Organization for Standardization ISO216, the specification is 21cm*29.7cm, the paper size used by most countries in the world is the use of this international standard. ISO216 defines three groups of paper sizes: A, B and C. Group C paper sizes are mainly used for envelopes. The aspect ratio of Group A paper sizes is the square root of 2:1 and then rounded to the nearest millimetre value. Group B paper size is the geometric average of group A paper with the same number and one less number.
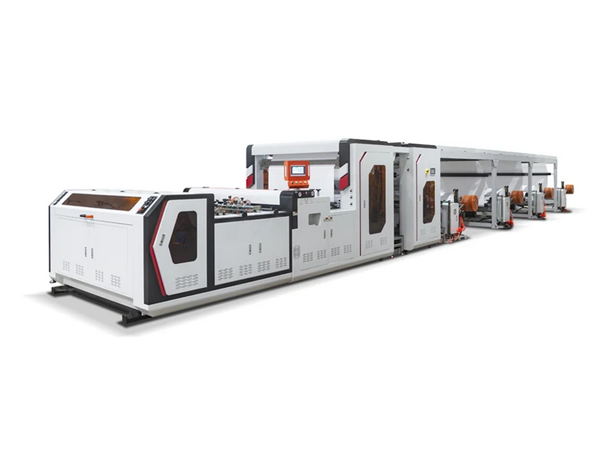
Automatic A4 Paper Production Line for Reams Paper
Paper machines can use many types of raw materials to make pulp and then pass through the paper machine to make good quality A4 paper. The raw material is mainly white wood pulp board, and White paper edge after unprinted trimming in the printing house.
Capacity: 6-18 reams/min
Paper size: A4 / A3 Paper Size
If you want to start the business with the pulp production line, then YG Machinery can provide the processing machines. This machine can make A4 paper from recycled paper, waste paper, virgin pulp, wheat straw, sugar cane, bagasse, cotton, wood, etc. And the finished product can be a paper roll. It includes the following parts:
Pulp manufacturing production line;
Paper production line;
Boiler part;
Paper conversion part;
Spare parts.
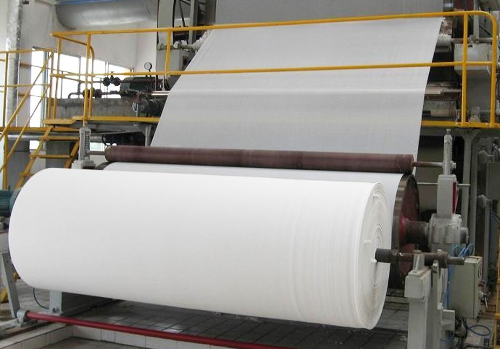
The equipment required by the pulp mill includes shredders, stirrers, cooking POTS, screening machines, bleaching equipment and dryers.
The mill is one of the key equipment in pulp production, which is used to break wood, waste paper or other raw materials into fine particles suitable for subsequent processing. According to the different raw materials, the crusher can be divided into hammer type, cutter type and sawtooth type and other types. These machines are able to break raw materials into the required size of pulp quickly and efficiently.
The mixer plays a mixing and homogenizing role in the pulp production process. The mixer mixes the fibers, moisture and other additives in the pulp through the high-speed rotating blades or stirring shafts to ensure the uniformity and stability of the pulp. The design and selection of agitator need to be selected according to the characteristics of pulp and the requirements of production process.
Digester is one of the important equipment in pulp production, which is used to cook the crushed raw materials to remove lignin and other impurities and improve the purity of the pulp. The digester usually uses pressurized steam or hot water as a heat source, and hydrolyzes the lignin in the raw material through a high temperature and high pressure environment, thereby separating the cellulose and obtaining pure pulp.
The screen is used to screen the boiled pulp to remove impurities and particles. The screen is usually composed of screen, screen frame and drive device, etc., through the filtering effect of the screen, the impurities in the pulp are separated to ensure the quality and stability of the pulp.
Bleaching equipment is used for bleaching the pulp to remove pigments and other colored substances and improve the whiteness and brightness of the pulp. Bleaching equipment usually uses the method of chemical bleaching or oxidative bleaching, by adding bleach or oxidizing agent, so that the pigment in the pulp decomposition or oxidation reaction, so as to achieve the purpose of bleaching.
The dryer is the last piece of equipment in pulp production and is used to remove water from the pulp to obtain a dry pulp product. Dryers usually use hot air drying or vacuum drying, by heating the air or reducing the pressure, so that the water in the pulp evaporates or sublimates, so as to get dry pulp. The design and selection of the dryer need to be selected according to the characteristics of the pulp and the requirements of the production process.
The above equipment is the core equipment in the production process of the pulp mill, and they work together to complete the conversion process from raw materials to pulp. Of course, according to the specific production process and raw material characteristics, pulp mills may also need other auxiliary equipment and supporting facilities, such as conveying equipment, dust removal equipment, control systems, etc., to ensure the smooth progress of the production process and the stability of product quality.
A4 Copy Paper Making General Description
Technical Parameters
Max working width | 1100-2000mm |
Raw material diameter | 800mm |
Rewinding diameter | 600mm |
Cutting precision | ±0.5mm |
Slitting speed | 0-350m/min |
Dimensions | 2400*2300*1600mm |
Weight | 1300kg |
Power | 6kw |
Fourdrinier writing and printing paper machine
Paper Grades | Writing & Printing Paper, A4 Copy Paper |
Trimmed Width | 2200mm~4200mm |
Basis Weight Range | 45~80GSM |
Design Basis Weight | 70GSM |
Design Speed | 220 m/min~650 m/min |
Drive Speed | 220 m/min~650m/min |
Working Speed | 200 m/min~600m/min |
Design Production | 40~250TPD |
Delivery Time | 5 months |
Warranty | The guarantee period is 1 year for the main machine’s mechanical use. But consumption parts like bearings, clothing, rubber cover of rolls, etc are calculated differently. |
Installation | Our company will arrange and send several engineers to the paper mill on-site. They are in charge of installing, test-running, and also training local workers on the operating machine. |
Cylinder mold A4 Copy Paper Machine
Paper Grades | Writing & Printing Paper, A4 Copy Paper |
Trimmed Width | 1600mm~3200mm |
Basis Weight Range | 45~80GSM |
Design Basis Weight | 70GSM |
Design Speed | 80 m/min~220 m/min |
Drive Speed | 80 m/min~220m/min |
Working Speed | 50 m/min~200m/min |
Design Production | 15~60TPD |
Delivery Time | 4 months |
Warranty | The guarantee period is 1 year for main machine mechanical use, but consumption parts like bearing, clothing, rubber cover of rolls, etc are calculated differently. |
Installation | Our company will arrange and send several engineers to paper mill on-site, they are in charge of installing, test-running, and also training local workers on the operating machine. |