In the field of grain edible oil processing, our company has become a trusted partner for many oil and fat enterprises with its profound industry accumulation and strong technical strength. As a professional manufacturer of complete equipment for grain and oil production lines, the company is committed to providing high-quality and efficient oil processing solutions to global customers.
The complete set of equipment we provide for grain and oil production lines covers all aspects from raw material pretreatment, pressing, refining to filling. The company not only has advanced oil presses, extraction equipment, and refining equipment, but also has a complete pre-treatment and filling production line to ensure that customers can easily achieve full automation of peanut oil production.
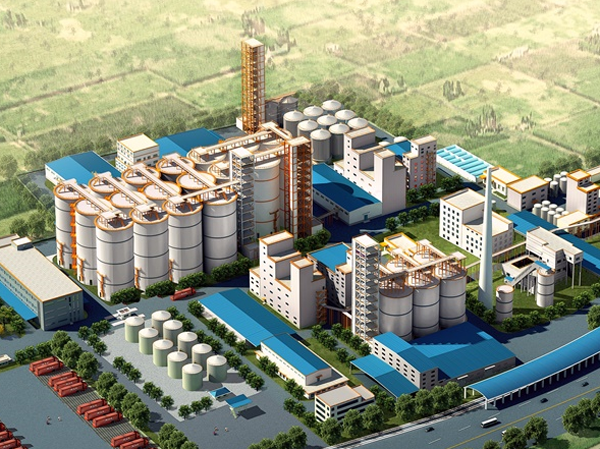
We provide complete sets of fully automatic grain and oil production lines, including peanut oil, soybean oil, corn germ oil, rice bran oil, cottonseed oil, palm oil, tea seed oil, flaxseed oil, coconut oil, walnut oil, sunflower oil, rapeseed oil, sesame oil, olive oil, sesame oil, castor oil, peony seed oil, grape seed oil, almond oil, wheat germ oil, pumpkin seed oil, perilla seed oil, tea seed oil and other raw material pretreatment equipment, grain and oil pressing and extraction equipment, and complete sets of crude oil refining equipment
The raw material pretreatment, oil pressing equipment, and refining equipment all adopt high-efficiency and energy-saving design concepts. By optimizing the process flow and selecting high-quality materials, the company has effectively reduced energy consumption and costs in the production process, while improving product quality. The pressing process can fully extract the oil and fat from the raw materials, preserving their natural flavor and nutritional components; The refining process can remove impurities and unpleasant flavor substances, improving the purity and stability of grain and oil.
Solutions for Grain oil processing
1, Grain pretreatment workshop process:
Grain → Weighing → Cleaning → Stoning → Conditioning → Cracking → Peeling → Aspiration → Flaking/Flattening → Extruder → Cooling → Solvent Extraction
2, Grain meal leaching workshop process:
Grain flakes→ Wet meal desolvation→ Mixed oil evaporation and desolvation→ Solvent cooling and water separation → Exhaust gas recovery→ Leaching oil to refining workshop
3, Grain oil refining workshop process:
Crude Grain oil→ Continuous degumming and deacidification→ Continuous decolorization→ Continuous deacidification and deodorization→ Cooling – deodorized oil to dewaxing workshop
4, Grain oil dewaxing workshop process:
Deodorized oil → Pre-cooling → Crystallization → Filtration and separation → Refined oil
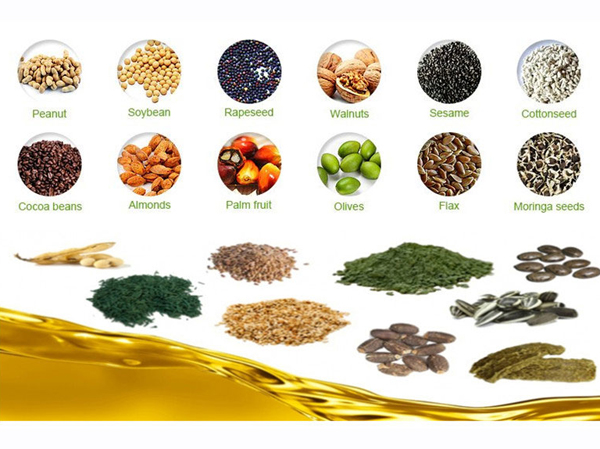
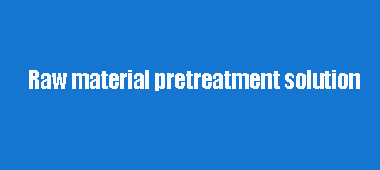
Adopting scraper conveyor reduces failure rate and has a long service life.
The dust removal system is designed reasonably and the exhaust gas meets environmental protection requirements.
The workshop adopts noise reduction design with low noise.
The equipment adopts frequency conversion regulation to reduce power consumption.
Reasonable power configuration and low power consumption.
High degree of automation and scientific and reasonable human-machine interface.
Laser cutting, precise and intelligent manufacturing, well-equipped.
The material impact part adopts wear-resistant design, with a long service life.
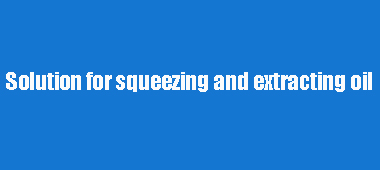
The utilization of steam depleted water and material heat exchange effectively reduce steam consumption.
The equipment in the leaching workshop has strong adaptability and can meet the processing needs of different materials.
The evaporation system adopts a vacuum combination method to reduce production costs.
Add VRS layer to the steaming machine, reduce residual dissolution in the meal, and decrease dissolution consumption.
Adopting a tail gas absorption system effectively reduces the solvent content in the tail gas.
The workshop adopts an automatic control system, which can reduce the labor intensity of workers.
Matching branded mechanical pumps and reducers to reduce equipment failure rates.
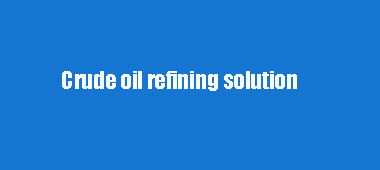
Provide advanced refining processes based on different oil products and requirements.
Enzymatic degumming, anhydrous soap removal, pre decolorization, fatty acid capture, etc
The workshop has a high degree of automation, with full computer display and automatic control.
Adopting preheating and reuse technology to reduce steam consumption;
Design odor capture devices to eliminate odor pollution and meet environmental protection requirements
Adopting a vacuum system greatly reduces steam consumption and wastewater discharge;
It has the advantages of high oil yield, excellent oil quality indicators, and low consumption
Main machine of Complete set oil pretreatment
The technical advantages of complete set of pretreatment project
- 1.There are few conveying equipment, and the elevator and auger are used as little as possible, and the scraper conveyor is used to reduce the failure rate and have a long service life.
- 2.The workshop adopts a noise reduction design with low noise, laser cutting, precise and intelligent manufacturing, and is well-equipped.
- 3.The material impact part adopts a wear-resistant design and has a long service life.
- 4.The design of the dust removal system is reasonable, the whole system is in a slightly negative pressure state, and the discharged gas meets the national environmental protection requirements.
- 5.Some equipment adopts frequency conversion regulation to reduce power consumption, reasonable power configuration, and low power consumption.
- 6.The degree of automatic control is high, and the man-machine interface is scientific and reasonable.
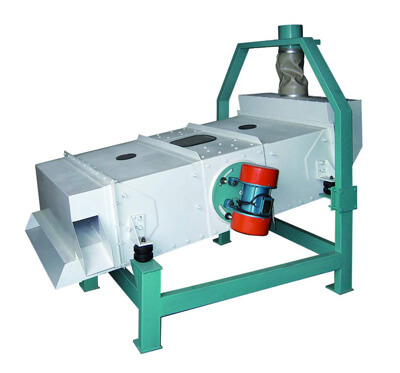
Oilseeds Puffing Machine
Generally speaking, the percentage of impurities in oil seed is 1%-6%, and the highest is 10%. so oilseed cleaner is an important machine for the oilseed pretreatment process.
Features
Reduce oil loss and increase oil yield rate
Improve the quality of oil, cake, and by-products
Improve oilseeds pressing effect. The lower the impurities of oilseed, the better the oilseed extraction result.
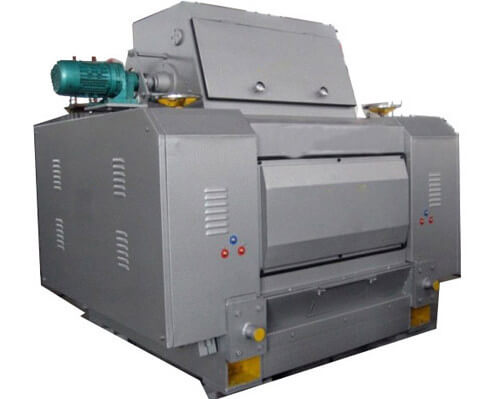
Oilseeds Crushing Machine
Generally speaking, the percentage of impurities in oil seed is 1%-6%, and the highest is 10%. so oilseed cleaner is an important machine for the oilseed pretreatment process.
Features
Easy to operate and maintain conveniently.
Energy saving and high efficiency.
Stable performance and reasonable structure.
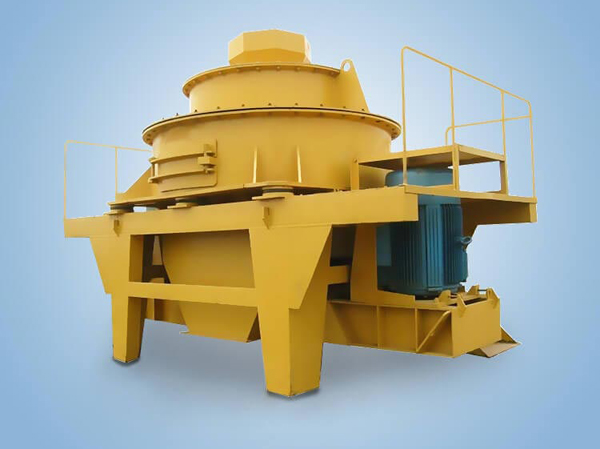
Oilseeds Flaking Machine
An oilseed flaking machine is vital pretreatment equipment in oil mill plants. It can turn granular oil materials into flakes by rolling the pressure of the rollers. The flaking process can help oil extraction more smoothly from oil materials.
Features
Flaking can destroy the cellular structure of oilseed, and create favorable conditions for the cooking process.
Greatly increase contact surface area of oil materials, and more oil can be extracted, so increase the oil yield.

Oilseeds Puffing Machine
An oilseed puffing machine is for preprocessing high oil-content materials like rapeseeds, corn germ, or various pre-pressed oil cakes before sending them into an oil solvent extraction workshop. The puffing machine is suitable for soybean, rape seeds, cotton seeds, rice bran, etc. The puffing process of oil materials can improve oil yield, reduce energy consumption, and save investment in oil production equipment.
Features
Increasing oil yield can increase production efficiency by 30-50%.
Shorten the extraction time and increase the leaching rate.
Reduce oil residue in oil meal.
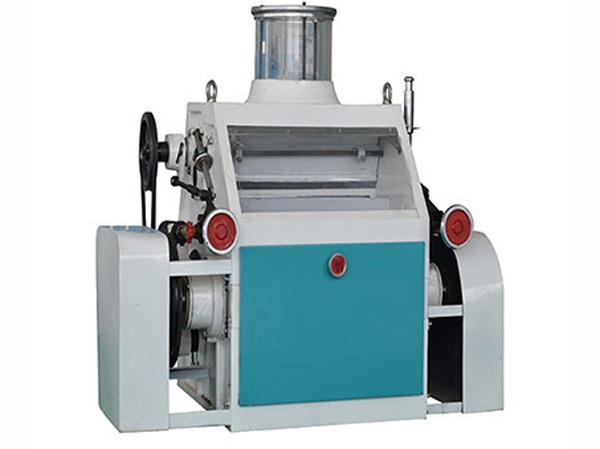
An Oilseeds sheller machine is often used with kernel shell separator and peeling machine in the pretreatment process of edible oil production line. Oilseed shelling is an important process before oil pressing. Many oilseeds contain shells and peels which have very low oil content and if not removed, the shells and peels will absorb oil and reduce oil yield.
Features
High efficiency, saving labor, small occupation area.
High shelling rate, low kernel broken rate, good separation effect, low loss rate.
Simple and compact structure, easy operation and maintenance, stable and reliable performance.
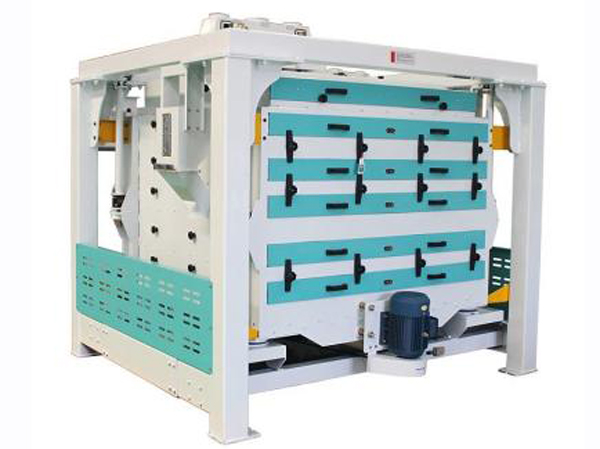
Three points by, seven points by roasting materials. It’s key to choose a reliable oilseeds roasting machine to improve the oil yield. Temperature control oilseeds roasting machine, also named drum type oilseeds roasting machine, can roast oilseeds evenly.
Features
Simple structure, easy operation.
Time and labor saving, high efficiency.
Even and uniform heating can ensure the seeds roasting quality.
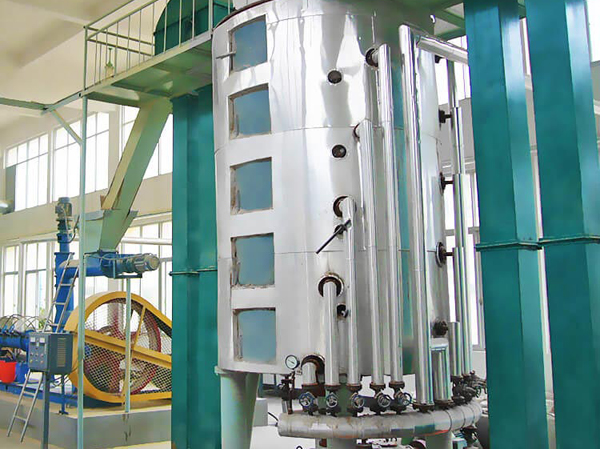
Oilseeds Softening Machine
Oilseeds Softening machine is for adjusting the moisture and temperature of crushed oil seeds or small size oil materials, to soften oil seed and increase the plasticity of oilseed, especially for oil materials with low oil content low moisture content. Oilseeds softening machine is an important oil pretreatment equipment before flaking. Oil material softening equipment includes horizontal softening machine and vertical softening machine.
Features
Increase the softening of oil.
Applied to a variety of oils, such as: soybean, cottonseed kernel, rapeseed, etc.
Main machine of oil Complete set solvent extraction
The technical advantages of complete set of solvent extraction project
- Comprehensive consideration of the utilization of steam exhaust water and the heat exchange of materials in the process, effectively reducing steam consumption.
- The VRS layer is added by steaming and de-bonding, which can reduce the residual solvent in the meal and the solvent consumption.
- Adopt a reasonable exhaust gas absorption system to effectively reduce the solvent content in the exhaust gas.
- The equipment in the extraction workshop has strong adaptability and can meet the processing of different materials. The Automatic control system reduces the labor intensity of workers.
- The evaporation system adopts a combination of steam and mechanical vacuum to reduce production costs and ensure the quality of crude oil.
- Equipped with pumps and reducers of well-known brands, which can reduce the failure rate of workshop equipment.
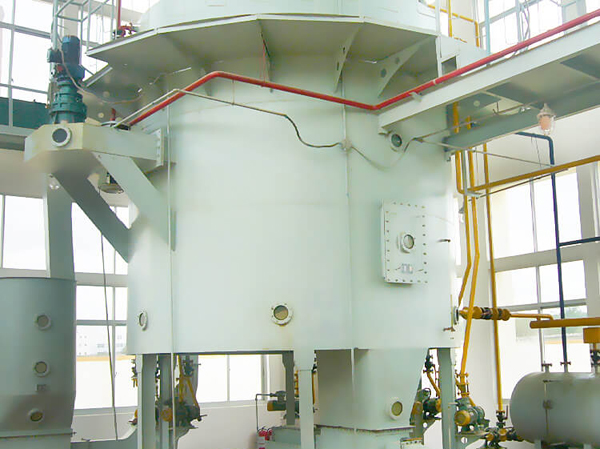
Edible Oil Extractor
Oil extractor is the main equipment in the edible oil solvent extraction process. The pretreated oilseeds or pre-pressed oil cake are sent to the edible oil extractor by the conveyor,after solvent extraction,miscella and the wet meal is obtained.Crude-extracted oil shall be refined to be edible.
Features
Residue oil rate of extracting meal can be controlled under 1%, high oil yield.
Improving the nutritive value and practical value of feed, and increasing the efficiency of fertilizer.
Low labor intensity, low power consumption, low processing cost.
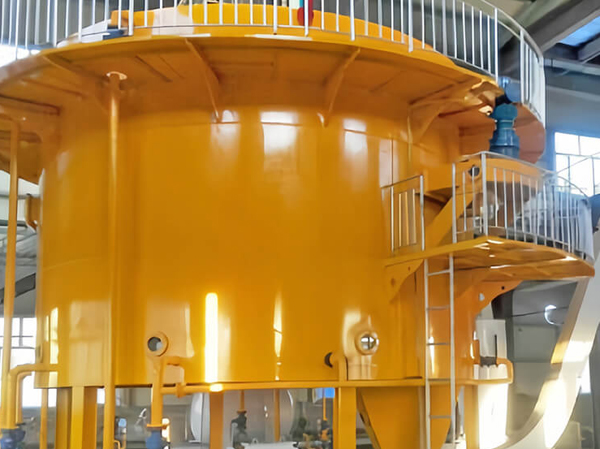
Edible Oil Extraction Equipment
Edible oil extraction equipment or tank extractor is a small-scale batch-type edible oil solvent extraction equipment. Tank extractor has both the function of extraction and meal desolventizing.It extracts oil by immersing the pre-pressed cake in solvent or miscella of various concentrations.
Features
The vapor has a good condensing effect.
Increase the temperature, saving energy.
High absorption rate, and good desorption effect.
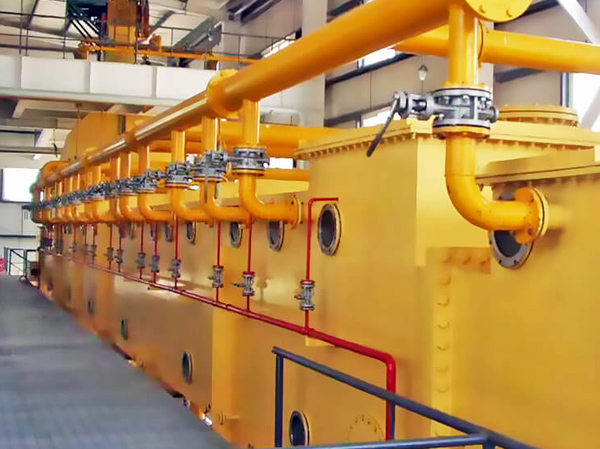
Solvent Vacuum Evaporation System
The solvent evaporation system adopts negative pressure evaporation technology, using the secondary steam from the desolventizer toaster as the heat source of the first evaporator and using the steam jet pump to vacuumize the system to make it works under negative pressure, having low evaporating temperature and good oil quality, saving steam and solvent consumption.
Features
The vapor has a good condensing effect.
Increase the temperature, saving energy.
High absorption rate, and good desorption effect.
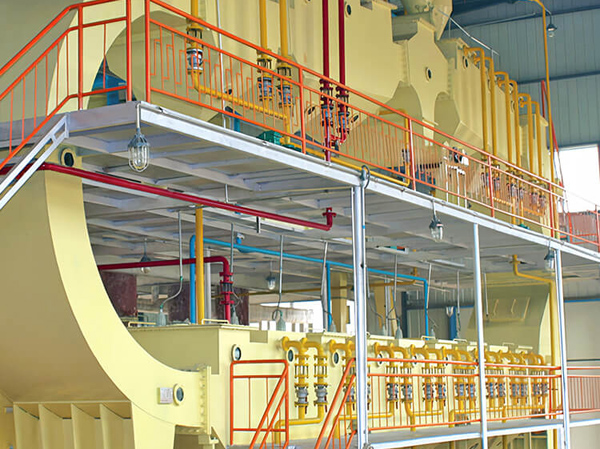
Solvent Recovery Systems
Solvent recovery systems consist of a condensing recovery system and a mineral oil system. The condensing solvent recovery equipment includes the condenser, solvent water separator, boiling tank, etc. We can equip the condenser according to your conditions.
Features
The vapor has a good condensing effect.
Increase the temperature, saving energy.
High absorption rate, and good desorption effect.
Main machine of Complete set oil refining
The technical advantages of complete set of refining project
- we can provide advanced refining processes according to different oil products and needs, the refining process mainly includes enzymatic degumming, Anhydrous soap removal, Pre bleaching, fatty acid two-stage capture, etc.
- When blowing cake with clay, a device for odor capture is designed to eliminate odor pollution in the decolorization process and meet the requirements of environmental protection.
- The workshop has a high degree of automation, full computer display, and automatic control; the preheating and reuse technology is adopted to maximize waste heat in the production line and reduce steam consumption.
- The vacuum system adopts a freezing or chilled water vacuum system, which greatly reduces the low steam consumption and wastewater discharge: It has the advantages of high product yield, excellent oil indicators, and low consumption.
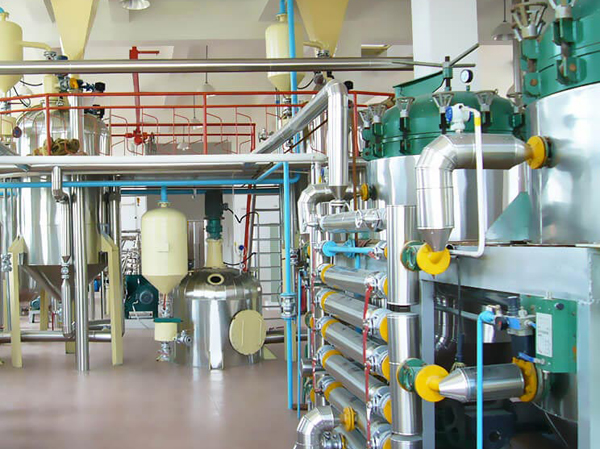
Edible Oil Dewaxing Machine
In short, oil dewaxing adopts forced cooling to make the high melting point wax solid oil precipitate out from liquid oil and then use the method of filtration or centrifugal separation to remove them. Different oils have different wax content. It is almost necessary to dewax the following products (such as corn oil, rice bran oil, sunflower oil, cottonseed oil, etc.)
Conventional dewaxing is the common oil dewaxing method with the working principle of freezing and then mechanically separating oil wax without any auxiliary means, the separating methods are usually pressure filtration, vacuum filtration, and centrifugal separation. Conventional dewaxing is the simplest oil crystallization and filtration method.
First of all, the oil crystallization is carried out in the cooling chamber at 0~4℃, after 72 hours of cooling, the final oil temperature in the oil tank is around 6~10℃. The average cooling rate is 2℃/hour at the first 24 hours of the cooling period, the cooling rate of the next 24 hours is 0.5℃/hour and the last 24-hour’ cooling rate is 1~2℃/hour. Then, the oil and precipitated wax crystals are separated by bag filtration in the filtration room at 15~18℃, and the filtration time is around 10~12 hours. The available filtration bags are polyester card, cotton, or cotton fabric, and their filtering speed is polyester card>cotton>cotton fabric.
At present, most of the oil refining plants are cooling, crystallizing, and plate filters separating oil from the wax paste. Oil such as sunflower seed oil contains less wax which could be dewaxed by cooling to 10~15℃ for 2 days and then pumping to the plate filter with compressed air. The dewaxing effect is good with a wax content in dewaxed oil is only ten milligrams per kilogram.
In general, conventional dewaxing is simple and cost-effective, but the wax separation is not complete and has a high cloud point which could be through crystallizing filtration twice.
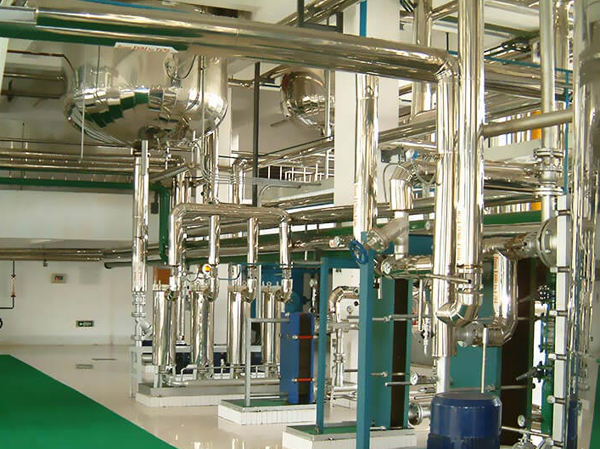
Oil Refining Plant Degumming
The degumming process in an oil refining plant is to remove gum impurities in crude oil by physical or chemical methods, and it is an oil purification process. After screw pressing and solvent extraction from oilseeds, crude oil mainly contains triglycerides and a few non-triglyceride. The non-triglyceride composition including phospholipids, proteins, phlegmatic, and sugar would react with triglycerides to form colloids, which are known as gum impurities.
The gum impurities not only affect the stability of the oil but also affect the process effect of oil refining and deep processing. For instance,non-degummed oil makes it easy to form an emulsified oil in the alkaline refining process, thus increasing the difficulty of operation, oil refining loss, and auxiliary material consumption.
In the decolorization process,non-degummed oil will increase the consumption of adsorbent and reduce discoloring effectiveness. Therefore, gum removal is necessary as the first step in the oil refinery process before oil deacidification, oil decolorization, and oil deodorization.
Degumming Method: Hydrated degumming
The specific methods of degumming include hydrated degumming, acid refining degumming, alkali refining method, adsorption method, electropolymerization, and thermal polymerization method.
In the edible oil refining process, the most commonly used method is hydrated degumming, which can extract the hydratable phospholipids and some non-hydrate phospholipids, while the remaining non-hydrate phospholipids need to be removed by acid refining degumming.
Working principle of hydrated degumming
The gum impurities such as phospholipids have the characteristic of hydrophilic. First of all, you can stir and add a certain amount of hot water or electrolyte aqueous solution like salt phosphoric acid to the hot crude oil. After a certain reaction period, the gum impurities would be condensed, subsided, and removed from the oil.
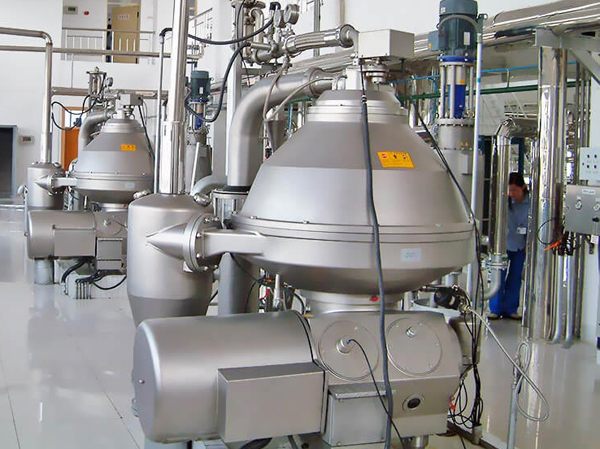
Oil Refining Deacidification System
Since FFA would produce an irritating odor and accelerate the hydrolysis rancidity rate of neutral oil, deacidification is necessary and it has long been used as the greatest economic benefit for the crude oil refining process.
Alkali refining for removing acid is the most critical step in the entire refining process, and it creates conditions for decolorizing, deodorizing, hydrogenating, and deep processing of oil. After alkali refining, oil quality is improved, oil stability is increased and its storage time is prolonged.
The Alkali refining method uses alkali to neutralize FFA in the oil to generate soap and the generated soap can adsorb impurities. Soap and impurities are then subsided and separated from the oil by gravitational sedimentation separation method or by centrifuge.
Alkali refining is divided into the intermittent type and continuous type, and the intermittent type is suitable for concentrated alkali refining at low temperatures with steps like pre-treatment-lye neutralization-separation of soap stock-washing separation-dehydration(dissolution)-filtration-soap stock processing-packing.
Main Equipment of Oil Alkali Deacidification
Disc centrifuge is mainly made up of the fuselage, drum, transmission, and water distribution devices. The mixture enters the drum from the bottom or top, then enters the discs from the dispensing holes in the lower and middle discs, and slides towards the inner wall of the drum, after that, the mixture is diluted by the flushing water coming from the lower dispenser. Along the inner wall of the drum up into a centripetal pump in the pump area, under the action of the centripetal pump, the heavy material is discharged to the heaviest phase outlet, while the light material is discharged from the light phase outlet.
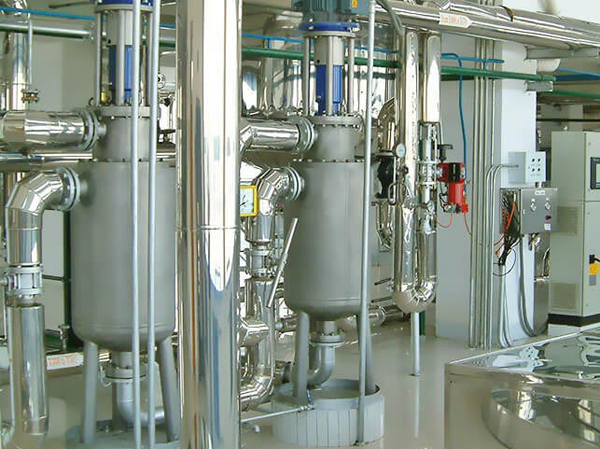
Edible Oil Decolorizing Equipment
The purpose of oil bleaching is not to theoretically remove all pigments but to improve the color of the oil and provide qualified materials for oil deodorization. What’s more, the decolorization section can avoid oil color reversion and improve the oil product’s shelf life.
The main composition of the edible oil is triglycerides. Pure triglyceride liquid is colorless and they become white when in solid form. But the common oil has different colors due to different amounts and varieties of pigments in oil, the pigments can be divided into three categories: Organic pigments such as chlorophyll, carotenoids, and gossypol; Organic degradants such as proteins, carbohydrates, and phospholipids; Some chromogens. Not all the pigments are bad, but the harmful pigments would damage oil quality and threaten human health, which should be removed.
Common Methods of Oil Decolorization
In industrial cooking oil production plants, there are many methods for oil decolorization: adsorption decolorization, heating decolorization, oxidation decolorization, chemical reagent decolorization, and so on. Among them, adsorption decolorization is the mostly method in oil refining processes
Adsorption Decolorization
Oil adsorption decolorization is making use of some substances that have a strong adsorption effect on pigments(such as bleaching earth, activated clay, and activated carbon)to adsorb pigments and other impurities in oil under certain conditions. Adsorption decolorization can not only achieve the purposes of improving oil color and removing gum but also effectively remove trace metal ions in oil and some substances that cause the poisoning of hydrogenated catalysts,so as to provide a good condition for further oil refining (hydrogenation, deodorization).
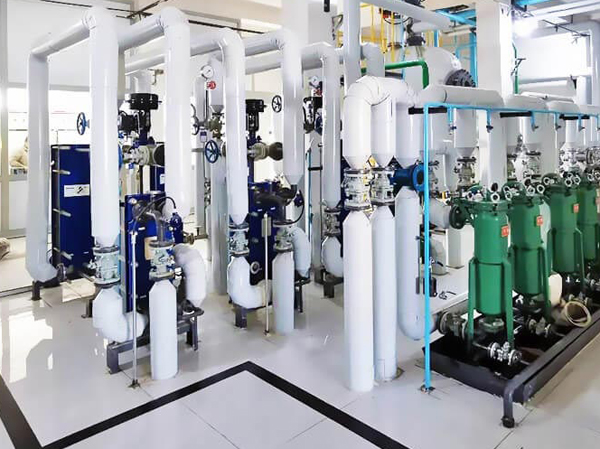
Cotton Seed Oil Refinery Plant
Oil Refining is the progress of removing impurities such as phospholipids, FFA, pigment, and off-flavor in cruel oil before edible application. An oil refining machine is used for producing the first or second-grade edible oil. We are able to supply the professional oil refining plant and related oil refining equipment. With a high degree of automation, the oil refining machinery can refine 20 kinds of oil, such as soybean, rape seeds, peanut, etc. in a small production line or in a large oil plant.
Degumming
This progress adopts hydration by adding hot water to remove the agglomerated and deposited hydrosol and phosphatide because of their water affinity. The separated gum (after being dried) can be made into lecithin or added to cakes or meals in the extraction workshop. The hydration degumming process can improve oil edibility, and storage and do well for the downstream neutralization section.
Neutralizing
Oil containing fatty acid is mixed mechanically with a slight excess of alkali to react with fatty acids present to form soaps. The mixture is centrifuged to separate oil from soapstock. After washing with water, the water is separated from the oil in a second centrifuge.
Bleaching
Degummed and neutralized oil is pumped into this system and mixed with the use of bleaching earth, a special soap, gum, and pigment-attracting adsorbent. The mixture enters the Pre-filtration Dryer where the moisture in the oil and adsorbent is evaporated. Then the oil is pumped through an automatically closed filter to remove clay.
Deodorization
The oil contains the disagreeable flavor and odors that are naturally present or created during processing. All odoriferous matter is distilled off by injecting high-pressure steam through the vacuum system. Then the product achieves the national standard.
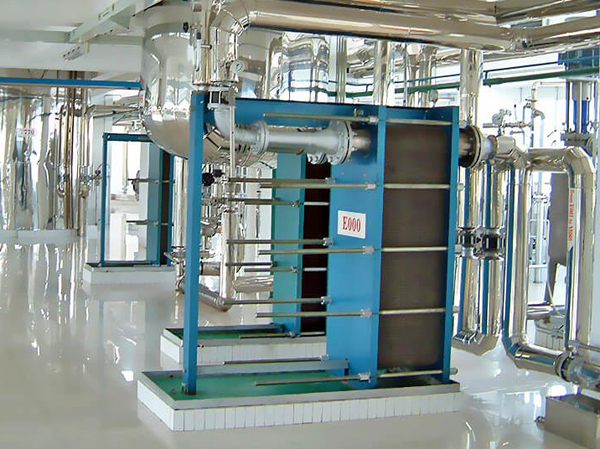
Edible Oil Refining Plant
A refining pot, decolorizing pot, deodorizing pot, vacuum pump, steam generator, and heat conduction furnace are necessary for the edible oil refining process. They are connected with vessels by pipeline.
Edible oil is indispensable in our daily lives, no matter what kind of food you make. Especially in China, we have accumulated thousands of years of diet culture, and edible oil quality will directly influence the food flavor. Thus high-quality edible oil is definitely important. It is said that edible oil without refinery is full of impurities such as gums, pigments, waxes, phosphatides, and free fatty acids (FFA), of which some are harmful to our health. Edible oil refining is essential to remove them and offer us the first or second-grade edible oil.
Edible Oil Refinery Process
Actually, the edible oil refinery is classified as physical refining and chemical refining, and we will introduce the chemical refining method. The complete edible oil refining process is composed of the following sections which are Degumming, Neutralising, Bleaching, Deodorization, and Dewaxing.
Degumming
This is also the pretreatment of the oil refinery. Degumming is to remove the phosphatides and mucilaginous material in crude oil. Phosphatides have strong hygroscopy and their existence is not good for edible oil storage, but it has high nutrition and wide application. The removal of phosphatides is an essential part of oil refining. This step adopts a hot water or alkali electrolyte solution. The phosphatides puff by absorbing water, then precipitate and separate out from the oil.
Neutralization
The second step is neutralization. It is to remove the Free Fatty Acids(FFA)by adding caustic soda. Thermic fluid oil is needed here to heat crude oil to about 60C. Then stir the crude oil, and the chemical reaction can create soap stock, which settles at the bottom of the tank and is taken out.
Main grain and oil production line
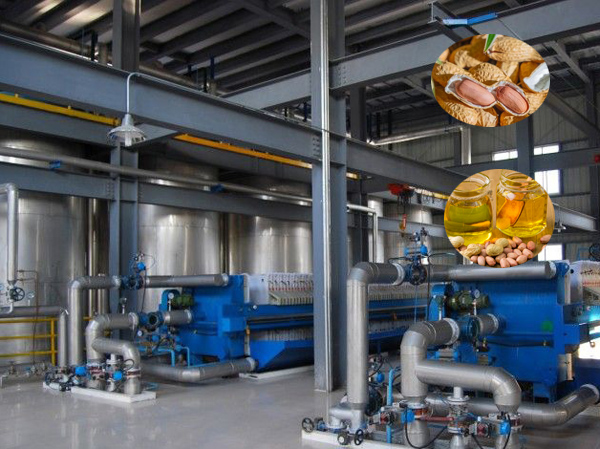
The peanut oil production line integrates advanced mechanical technology and intelligent control systems, which can complete the entire process from raw material processing to finished oil production. The fully automated operation mode means that all processes, from cleaning, crushing, steaming and frying of peanut raw materials, to pressing, filtering, refining, to filling and packaging of finished oil, are mechanically automated without excessive manual intervention.
The intelligent control system is another highlight of this production line. Through precise temperature control, pressure regulation, and time management, the system ensures that every drop of peanut oil meets the optimal quality standards. At the same time, real-time data monitoring and fault warning functions also provide strong guarantees for the stable operation of the production line. This production line also provides flexible configuration solutions for production needs of different scales
We provides intelligent soybean oil processing and soybean by-product deep processing solutions covering the entire supply chain – soybean pre-treatment workshop equipment, soybean embryo leaching workshop equipment, soybean crude oil refining workshop equipment, soybean oil dewaxing, soybean protein isolate, soybean protein concentrate, soybean lecithin production line.
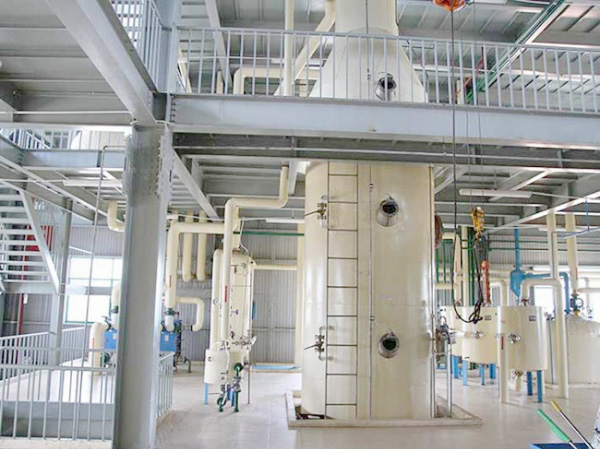
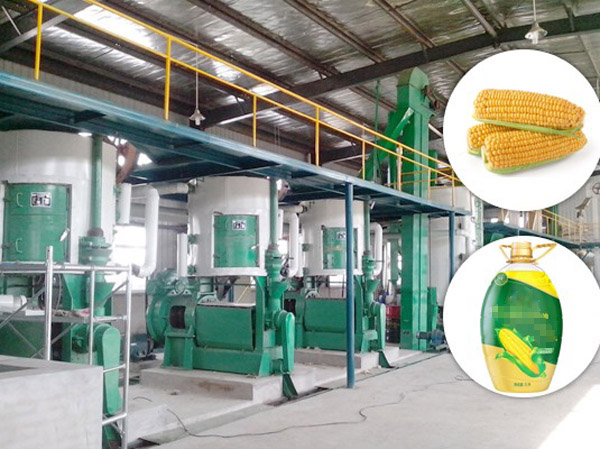
The extraction process of corn germ can be divided into dry extraction, wet extraction, and semi wet extraction. If oil factories find it troublesome, they can directly cooperate with corn starch factories. Directly collecting corn germ can reduce the operational difficulty of oil factories, but the collected corn germ needs to undergo processes such as cleaning, drying, and softening to achieve a convenient oil production state.
Corn oil can be extracted through pressing or leaching processes, but considering the difficulty of extracting corn germ and the relatively low oil content, leaching processes are often used in industrial production to extract corn germ oil in order to achieve good production results. The extraction process of corn oil involves transporting processed oilseeds to the extraction system to obtain corn germ wool oil.
Raw oil can be processed through processes such as water washing, alkali stripping, acid removal, vacuum dehydration, adsorption decolorization, and vacuum deodorization to obtain healthy and nutritious finished corn oil. It is an indispensable part of mechanical equipment in the extraction and processing of corn oil. With the widespread application of mechanization and automation, mechanical production can replace most manual operations in the oil processing process, reducing the production intensity of workers.
We are a manufacturer of rice bran oil pressing production lines and rice bran oil refining and processing equipment. Our company is engaged in the research and development of rice bran oil production equipment and has rich experience in the production design of rice bran oil equipment. The rice bran oil production equipment we manufacture is sold worldwide. The company’s main products include rice bran hydraulic pressing equipment, rice bran oil refining equipment, and rice bran oil production lines. We provide professional and high-quality full process services for domestic and foreign clients, including oil engineering consulting and design, equipment manufacturing, mechanical and electrical engineering system delivery, engineering general contracting, operation and maintenance.
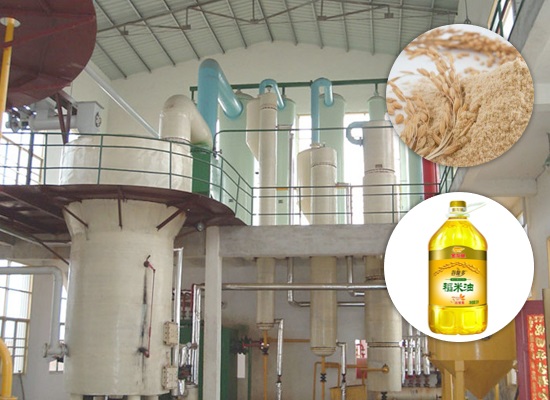
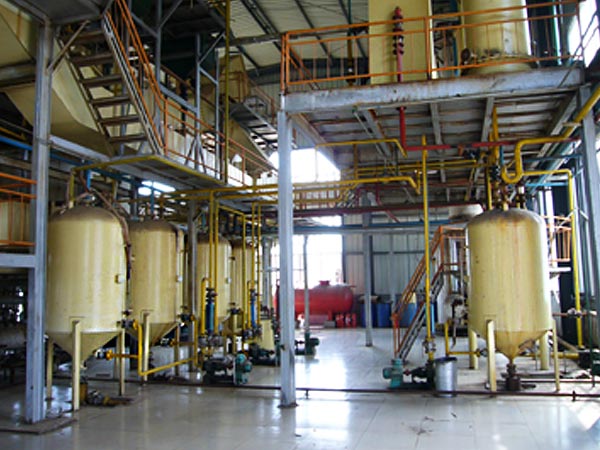
Cottonseed oil processing plant
Cottonseed oil content is about 16-20%. Through different processing methods, we can get three kinds of cottonsed oil.
Crude cottonseed oil (produced by cottonseed oil pressing plant or solvent extraction plant)
Refined cottonseed oil (produced by cottonseed oil refining plant)
Final cottonseed oil (produced by cottonseed oil fractionation plant)
As long as you tell us your ideal amount of cottonseed feeding/processing per
Palm kernel oil production line
Palm oil is a commonly used edible oil in Nigeria, Malaysia, Indonesia, Liberia, and Congo, making palm oil production equipment extremely popular locally. Our company is a specialized manufacturer of palm oil equipment. We can not only produce palm oil production equipment, but also palm kernel oil production equipment. Our complete set of palm kernel oil production equipment mainly includes: palm kernel oil pressing production line, palm kernel oil refining production line, and palm kernel oil extraction production line.
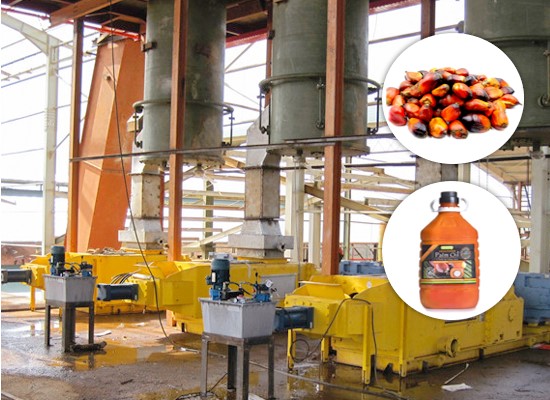
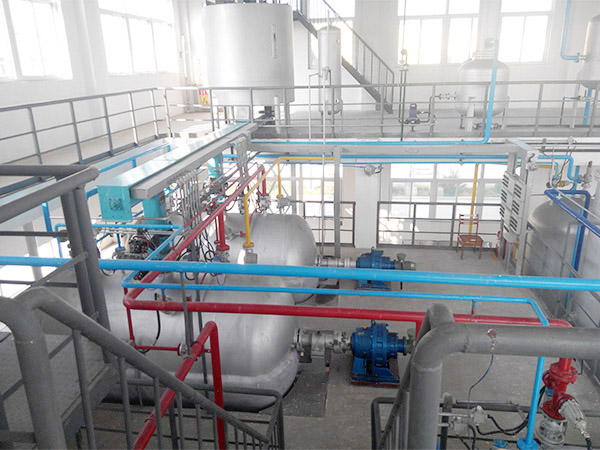
The raw material for the production of rapeseed oil is generally rapeseed, with an oil content of 30%-48%. There are two main ways to prepare rapeseed oil, one is the pre-extraction method, and the other is the pressing method. From the perspective of return on investment, production projects with an output of more than 30 tons/day are suitable for the pre-expression leaching method. If the output is 1-10 tons/day, the cost of oil production by the pretreatment pressing method will be lower. The equipment used in the two production methods is also different.
Process characteristics of linseed oil production line:
Avoiding high-temperature distillation deodorization effectively prevents the damage of polyunsaturated fatty acids – α – linolenic acid in linseed oil caused by high temperatures, effectively preserving the natural and complete nutritional components, making it easier for the human body to absorb and supplement nutrients.
Avoid harmful substances caused by the degradation of oils, sugars, and protein denaturation during high-temperature pressing.
Avoiding the darkening of linseed oil color and the appearance of burnt flavor caused by high temperature.
After multiple filtration processes, direct contact and secondary pollution of chemical substances and active ingredients caused by sulfuric acid degumming, caustic soda deacidification, and activated clay decolorization processes in the hot pressing process are avoided.
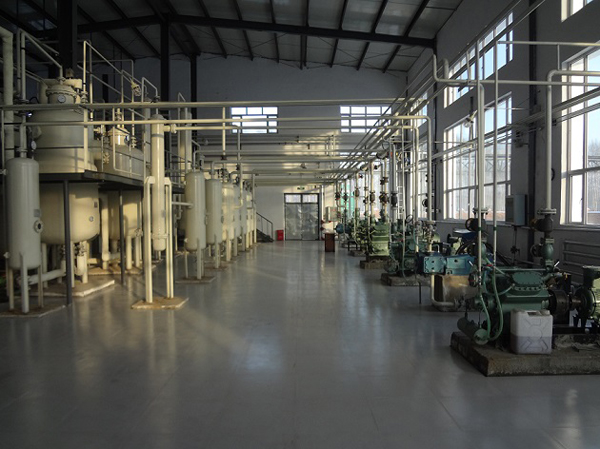
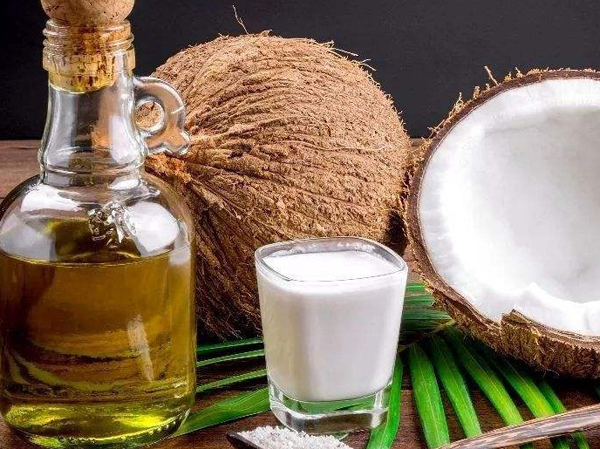
Coconut jerky with a moisture content of 10% -12% is transported to an automatic scale through a magnetic chamber to remove crushed iron, which is then crushed into particles with a diameter of approximately 0.3cm. The rolling mill presses the particles into thin sheets to enlarge the surface of the coconut jerky and produce oil.
Steam and stir fry the raw materials in a 115 ℃ horizontal steaming and frying pan for 20 minutes. Under these conditions, due to the rupture of adipocytes and the precipitation of phospholipids, the moisture content decreases to 3-5%. After steaming and frying the uniformly sized raw materials, they are sent to an oil press machine for continuous pressure extraction of oil. The residual oil in the processed coconut cake is 7%. This production line generally consists of equipment such as a dehazing machine, sheller, peeler, crusher, juicer, centrifuge, coconut oil refining machine, etc.
Walnut oil production process:
Fresh walnut kernel → peeling → cleaning → drying and roasting → screw pressing → oil → hydration degumming → deacidification → drying → decolorization → vacuum deodorization → compound antioxidant and nutrient enhancer → mixing → cooling → filling → finished product Refined walnut oil
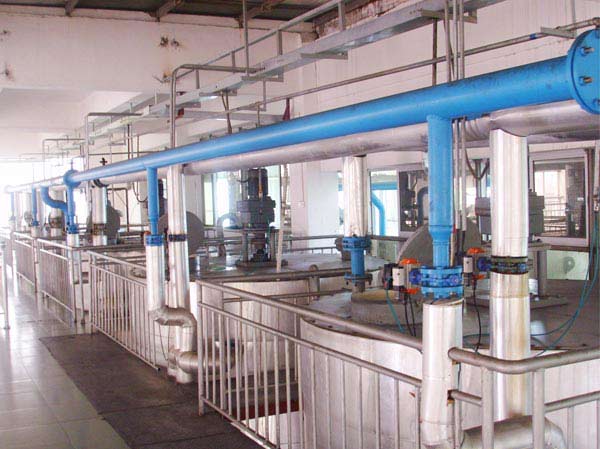
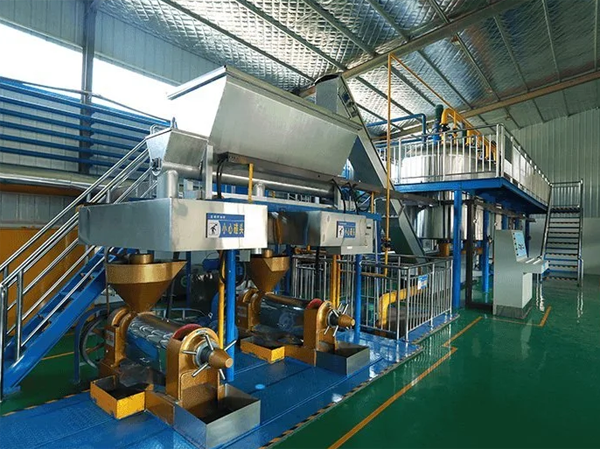
Our advanced sunflower seed pretreatment and pressing process includes seed cleaning → shelling→ conditioning → flaking → cooking → pressing → three-stage To enhance the flavor of sunflower seed oil, a unique roasting and pressing process is used to produce aromatic sunflower seed oil.
specializing in edible oil processing solutions and equipment . We provide complete plant solutions for converting rapeseed/canola to rapeseed/canola oil and protein. Our comprehensive range of products helps you to increase output while meeting increasingly stringent environmental and health requirements. When you have a project plan for the rapeseed/canola oil processing plant, please contact us soon.
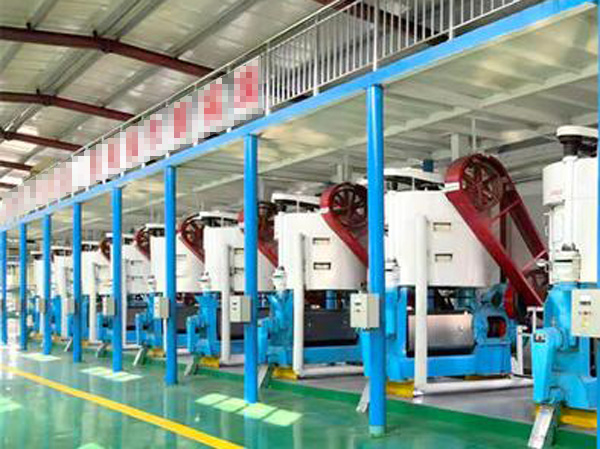
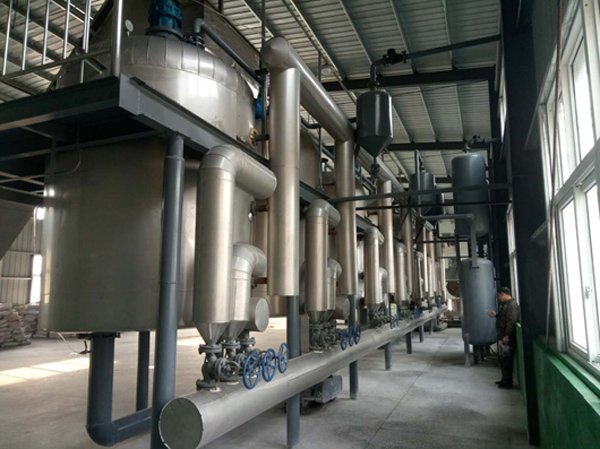
Castor bean oil extration machine
The castor oil production line includes castor seed pretreatment and pressing production line and castor seed oil refining production line. The castor seed oil is pretreated and processed in the early stage, and the castor seed oil is refined in the later stage
Process of sesame oil production line
Harvesting and selection of flaxseed → flaxseed → cleaning impurities → shelling → crushing → pressing → pressing flaxseed oil → coarse filtration → fine filtration → low-temperature crystallization and crystal growth → low-temperature filtration →
The sesame seeds contain 6% to 10% sesame gum. Hula gum is a pectin based substance mainly composed of polysaccharides, containing 12% protein, about 17% pectin acid, starch, minerals, etc. It can be used as a food additive, cosmetic powder, pharmaceutical raw material, etc.
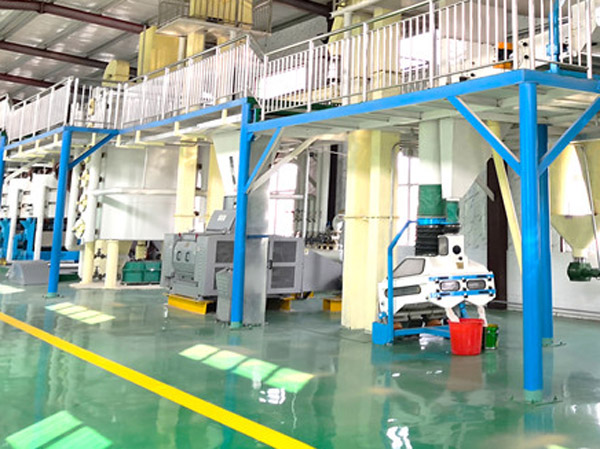
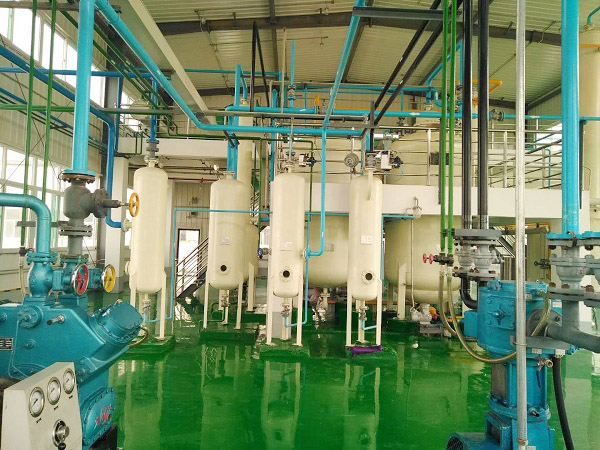
The oil extraction efficiency of olive oil, the oil content of the fruit, and the rupture of fresh fruit oil cells are related to the aggregation status of the oil after outflow and the juice yield of the pulp during pressing. Crushing is a key process for breaking the oil containing cells in the fruit flesh, but the particles produced by the crushing method cannot be too fine, and a certain particle size of fruit kernel residue must be preserved to facilitate the process of juice extraction. The main function of fusion stirring is to accelerate the aggregation and outflow of oil droplets.
Sesame oil does not require strict purification and refining, in fact, it is one of the few vegetable oils that can be used without refining. The sesame crude oil obtained by pressing method often contains suspended meal particles, which can be removed by precipitation, separation or filtration methods. The sesame filtered crude oil produced by the leaching plant also contains impurities such as phospholipids, resins, free fatty acids, and colored substances, which often require full refining measures such as degumming, neutralization, decolorization, winterization, and deodorization processes.
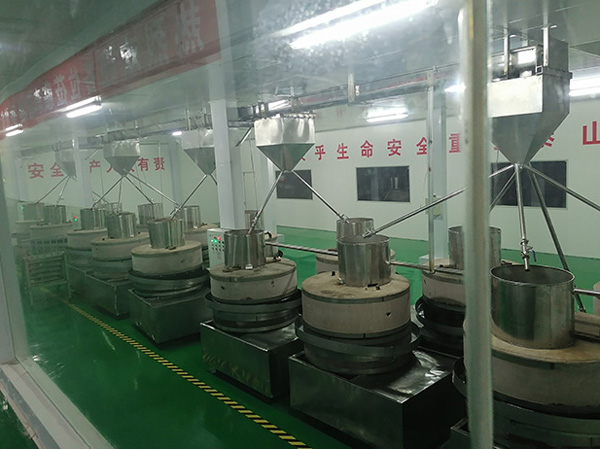
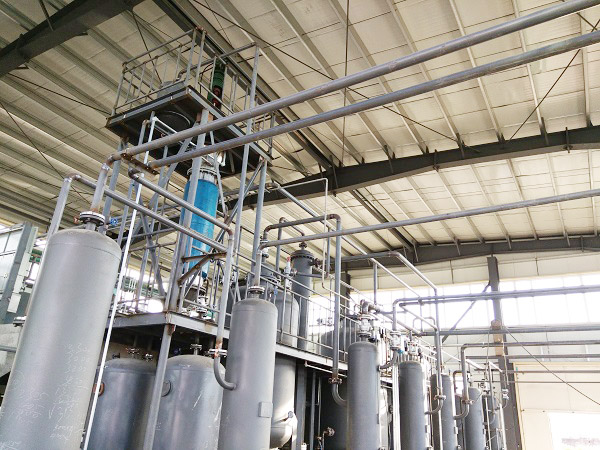
Peony seed oil production line
The core technical principle of this device lies in its highly integrated physical and chemical refining processes. Firstly, through advanced low-temperature pressing technology, the natural active ingredients and aroma in peony seed oil are maximally preserved. Subsequently, a precise filtration system is used to remove impurities and suspended solids, ensuring the clarity and transparency of the oil. The key processes of degumming, deacidification, decolorization, and deodorization are carried out under mild conditions, which not only remove unnecessary free fatty acids and pigments, but also avoid the damage of nutrients by high temperatures, achieving a dual guarantee of efficiency and quality.
Grape seed oil production line
Using grape seeds as raw materials, the fluid extraction method, supercritical CO2 extraction method, solvent extraction method, cold pressing method and hot pressing method were used to extract grape seed oil, and the effects of different oil production processes on grape seed oil phenols and their resistance were studied. The effect of oxidation activity. The results show that the content of oil polyphenols is relatively high, and the content of oil polyphenols is very low. The quantitative analysis of 7 monomer phenols in grape seed oil shows that.
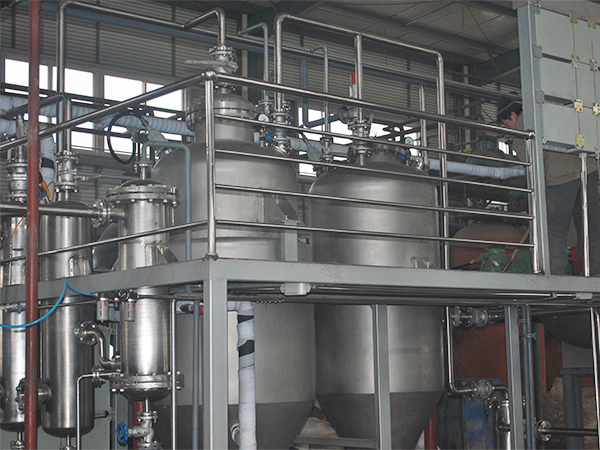
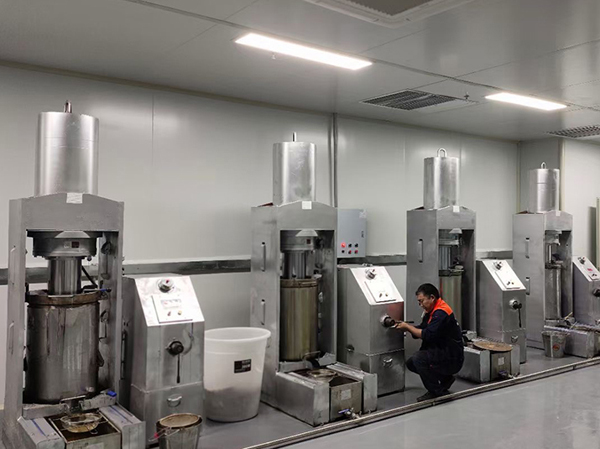
Almond oil, yellow transparent, fragrant taste, is not only an excellent edible oil, but also a good lubricating oil, can withstand the low temperature below -20℃, can be used as an important raw material for paint, cosmetics and high-quality soap, but also extract flavor and vitamins. Because almonds are different from south apricot (sweet almond) and North apricot (bitter almond), there is sweet almond oil. Almond oil is rich in protein, unsaturated fatty acids, vitamins, inorganic salts, dietary fiber and trace elements needed by the human body. It has the function of moistening the lungs, strengthening the stomach and supplementing physical strength. Its amygdalin is a natural anticancer active substance.
Wheat germ oil processing machine
Wheat germ oil processing machine are generally divided into physical pressing method and chemical leaching method, among which pressing method is further divided into hot pressing and cold pressing. The quality of edible oil produced by different processes varies in the following aspects:
1.Squeezing method: refers to the use of physical pressure to separate oil from oilseeds. This method originated from the traditional oil production mode of workshops, and now the pressing method has been industrialized.
2.Extraction method: a method of extracting oil from oilseeds using plant oil extraction solvents based on chemical principles. From the development history of the world’s edible oil production technology, the extraction oil production process is currently internationally recognized as a production process.
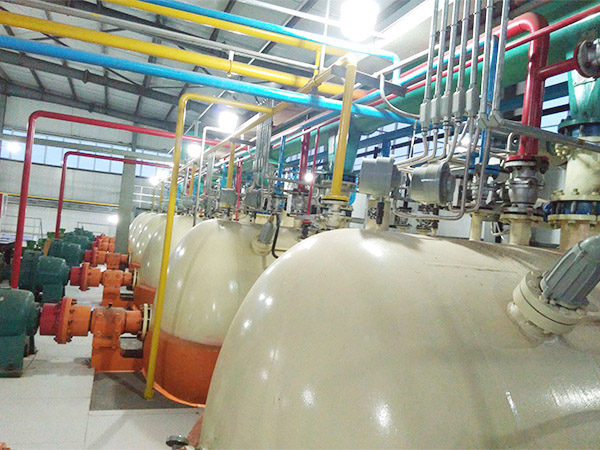
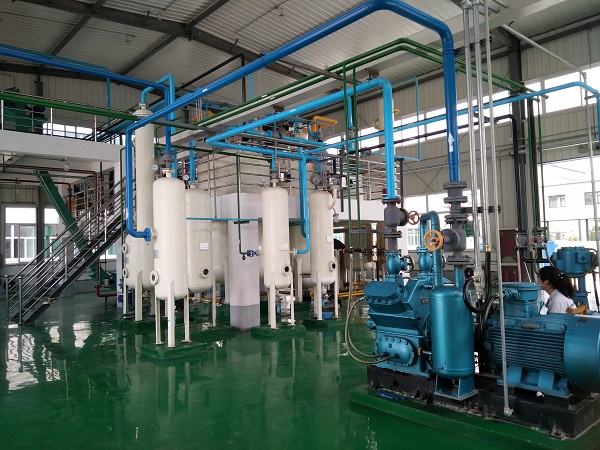
Pumpkin seed oil production line
processing capacity:10-500tons/D
Application scope:pumpkin seed oil processing machine
Product introduction:
Pumpkin seed oil production line,large pumpkin seed oil processing machine,pumpkin seed oil extraction equipment,pumpkin seed protein refined oil processing production line machine manufacturer
Perilla seed oil processing equipment
The pressing process can be divided into cold pressing and hot pressing processes. Cold pressing can better preserve the nutrients of perilla seed oil at low temperatures, while hot pressing can improve the oil yield of perilla seeds and create better profits for oil factories. The selection of two processes is based on the needs and planning of the oil factory, and the equipment required for the production line will change with the changes in the process. The commonly used oil press equipment on the market is mainly divided into two types: spiral oil press and hydraulic oil press
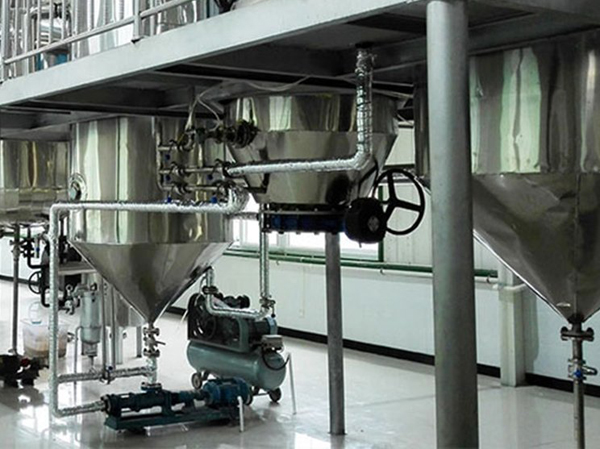
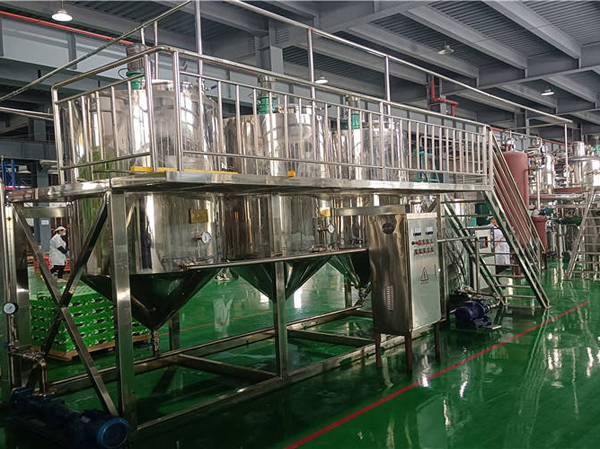
Camellia seed oil refining line features:
1, the use of food grade stainless steel material, and polished treatment; Meet food machinery standards.
2, simple design, exquisite appearance, improve customer satisfaction.
3, the operation data are all displayed by the instrument, simple operation, safe operation; Ordinary staff can work on the machine after telephone training.
4, can achieve oil dephosphorization, dealkali, dehydration function, according to user needs can also be constant temperature decolorization.