The cottonseed oil processing production line usually consists of multiple key components, including raw material pretreatment equipment, oil press, refining equipment, decolorization and deodorization equipment, as well as finished oil storage and packaging equipment. These devices work together, from the initial processing of cottonseeds to the final production of refined oil, every step is crucial
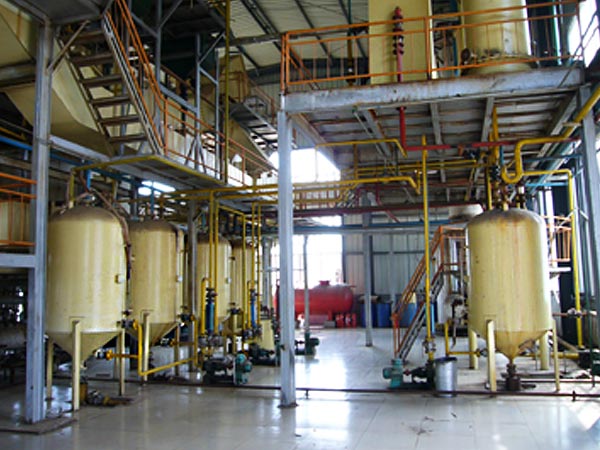
Cottonseed oil content is about 16-20%. Through different processing methods, we can get three kinds of cottonsed oil.
Crude cottonseed oil (produced by cottonseed oil pressing plant or solvent extraction plant)
Refined cottonseed oil (produced by cottonseed oil refining plant)
Final cottonseed oil (produced by cottonseed oil fractionation plant)
As long as you tell us your ideal amount of cottonseed feeding/processing per
Complete sets of cottonseed dephenol-protein equipment, including low-temperature pretreatment section, leaching and extraction cottonseed oil section, cottonseed meal dephenolization section, etc.
A complete set of cottonseed dephenol protein equipment, which mainly includes a low-temperature pretreatment section. Leaching and extracting cottonseed oil section, cottonseed meal dephenolization section, etc.
The secondary extraction dephenolization technology is the stepwise extraction of cottonseed oil and gossypol with two solvents to ensure the quality of the oil and the complete removal of gossypol. It can ensure that free gossypol ≤0.04%, which has reached the standard (WHO/FAO/ The free gossypol content of food-grade cottonseed protein specified by UNICEF International organization ≤0.06%). At the same time, it can remove the aflatoxin produced by the cottonseed during storage. After the leaching section, the damp-containing meal is directly extracted and dephenolized, which not only reduces consumption, avoids thermal denaturation of cottonseed protein, and ensures the stability of product quality.
Technology Process of Cottonseed oil production line
1.COTTONSEED SEED PRETREATMENT PROCESS
Cottonseed Seeds → Screening → Cleaning Impurities → Shelling → Crushing → Steaming And Frying → Pressing Crude Oil → Cottonseed Oil And Cake
2.COTTONSEED CAKE SOLVENT EXTRACTION PROCESS
Cottonseed Oil And Cake → Extractor → Solvent Recovery → Steam And Remove Wet Meal → Mixed Oil Treatment → Crude Oil And Meal
3.CRUDE OIL REFINING PROCESS
Cottonseed Crude Oil → Alkali Refining → Degumming → Centrifugal Drying → Continuous Decolorization → Dewaxing → Continuous Deodorization → Filtration → Finished Cottonseed Oil
Cottonseed oil extraction plant adopts solvent extraction method to extract cottonseed oil. The cottonseed oil plant includes cottonseeds pretreatment and prepressing workshop, cottonseed cake solvent extraction workshop and crude cottonseed oil refinery plant. The residual oil rate in the cottonseed meal is lower than 1%. Cottonseeds contain a toxic pigment which called gossypol, of which the content is 0.15%-1.8%. Cottonseed kernels contain 0.5%-2.5% of gossypol. After processed by the cottonseed oil refinery plant, the gossypol content in the oil is less than 0.01%. The products of the cottonseed oil processing plant are cottonseed oil, cottonseed meal, cottonseed hull, and soapstock
COTTONSEED SEED PRETREATMENT PROCESS
Cottonseed Seeds → Screening → Cleaning Impurities → Shelling → Crushing → Steaming And Frying → Pressing Crude Oil → Cottonseed Oil And Cake
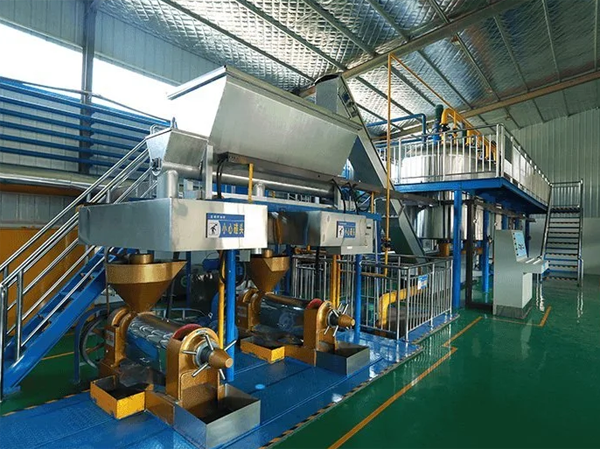
1.Cottonseeds Delinting
If your cottonseeds are with lint, then you need to add cottonseed delinting machine in the cottonseed oil plant.
2.Cottonseed Cleaning
Cleaning is to remove the various impurities in the cottonseeds by cottonseed cleaning equipment. Cleaning cottonseeds can reduce oil loss, increase oil yield, increase the quality of oil, cake and by-products, reduce the abrasion of equipment, increase the handling capacity and improve the work environment.
Cottonseed cleaning equipment for the cottonseed oil plant includes winnower, vibrating screen, magnetic separator, etc. The winnower can remove light impurities and dust as well as heavy impurities like stone and metal in the cottonseeds; The vibrating screen is to remove the large and small impurities; The magnetic separator is to remove the metal impurities in the cottonseeds.
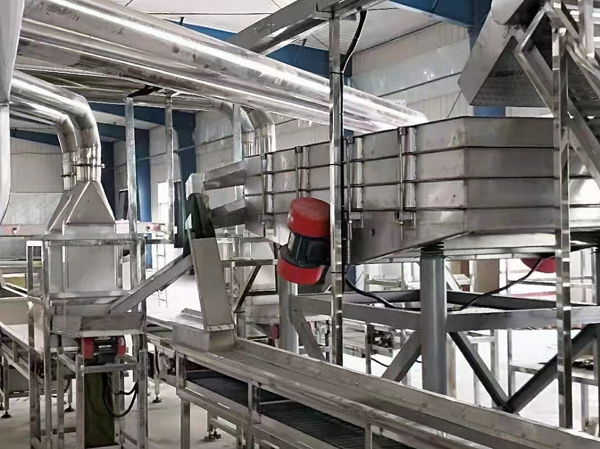
3.Cottonseed Dehulling
Cottonseed contains 40%-55% of hulls and the hull contains only 0.3-1% of the oil. Cottonseed contains 14%-25% of oil and the kernels contain 30-40%. In addition, the hulls also contain brown pigment, pesticide residue, wax, and lint. Hulling cottonseeds can increase the handling capacity of oil press and increase oil yield, improve the quality of crude oil and meal. Cottonseed hulls can be used for cultivating mushroom and used as livestock feed, etc.
The toothed roller crusher in the cottonseed oil mill plant adopts two tooth rollers with different speed to remove the hull. By the extruding and shearing action of the counter-rotating rollers, the hulls are crushed and removed. The toothed roller crusher has the features of large capacity, low power consumption, easy maintenance, high hulling rate, low fines content, high whole kernel rate and the kernels and hulls are easy to be separated.
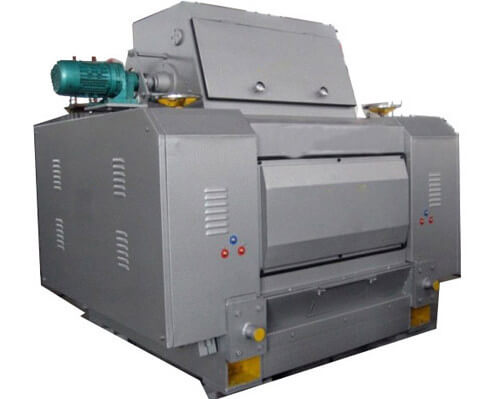
4.Kernel and Hull Separation
The effect of kernels and hulls separation can affect the oil yield and the quality of oil and meal. Vibrating screen is adopted in the cottonseed oil mill plant to separate kernels and hulls. The hulls are further processed by the hull beater to separate the kernel pieces in hulls. The shaft of the hull beater rotates in different speed and direction with the screen drum. The beating sticks arranged in the spiral on the shaft beat and push the cottonseeds. The hulls and kernels flow out from different outlets of the hull beater.
5.Flaking
Flaking process makes the cottonseeds into flakes and destroys the cell walls, which can largely shorten the oil path so that to increase the oil-yielding speed and oil yield. Cottonseed oil processing plant adopts hydraulic flaking roller which can guarantee the uniform thickness of the cottonseed flakes. The roller has high hardness and stable performance.
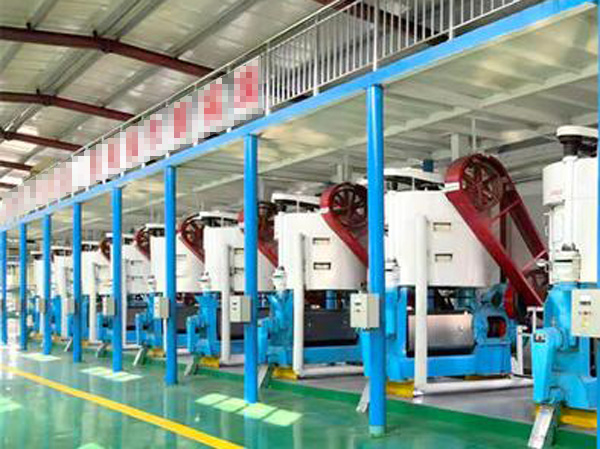
6.Cooking
To reduce the toxicity of gossypol, usually high moisture cooking is adopted in the cottonseed oil plant. The phospholipids absorb water and agglomerate so that do not dissolve in oil, reducing the binding with free gossypol. Free gossypol combines with protein to form bound gossypol which has no toxicity and is left in the meal. Cottonseed oil processing plant adopts vertical cooker for the cooking process. The flakes from the flaking roller enter the vertical cooker. By high temperature and high moisture cooking, the temperature and moisture of cottonseed flakes are adjusted, the free gossypol content of the crude oil is reduced and the quality of the crude oil is improved.
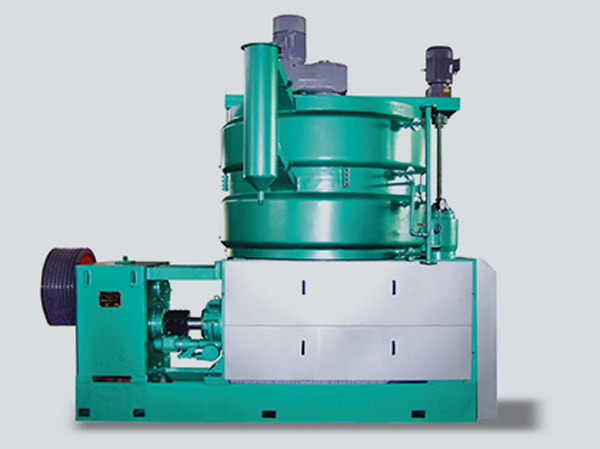
7.Prepressing
Cottonseeds can be once-pressed and then sent to the cottonseed oil refinery plant directly. For the capacity of more than 20 tons per day, usually, solvent extraction method is adopted with cottonseed oil pre-press used to extract part of the oil. The machine has a large capacity and the cake has low residual oil rate and is easy for solvent penetration.
8.Filtration
The oil residue is separated from the oil by the oil residue scraper, and then the oil is filtered by the leaf filter. The filtered oil is pumped into the crude oil tank. The pre-pressed cake is sent to the solvent extraction workshop. The leaf filter used for the cottonseed oil processing plant has the features of high precision, easy to discharge the residue.
COTTONSEED CAKE SOLVENT EXTRACTION PROCESS
Cottonseed Oil And Cake → Extractor → Solvent Recovery → Steam And Remove Wet Meal → Mixed Oil Treatment → Crude Oil And Meal
The pre-pressed cottonseed cake is sent to the leaching workshop, where the cottonseed oil in the pre-pressed cake is extracted by spraying and soaking with hexane solvent. The cottonseed oil leaching workshop consists of solvent leaching system, wet meal desolvation system, mixed oil evaporated stripping system and solvent recovery system.
Since there is more residual oil in one-time pressing, the method of pre-pressing and solvent leaching can obtain more cottonseed oil and bring high economic benefits. we design negative pressure evaporation technology, innovative technologies are dedicated to saving energy and reusing materials, ensuring excellent quality of cottonseed oil, helping to improve energy efficiency and heat recovery, and reducing steam consumption.
Oil Extraction
Oil extraction is using the organic solvent to extract oil from the pre-pressed cake inside the oil extractor. Multiple oil extractors such as loop type extractor, rotocel extractor and towline extractor can be used for the cottonseed oil extraction plant. After oil extraction, miscella and the solvent containing wet meal are obtained. The miscella is pumped into the hydrocyclone to remove the fines and then the miscella enters the miscella tank in the cottonseed oil extraction plant.
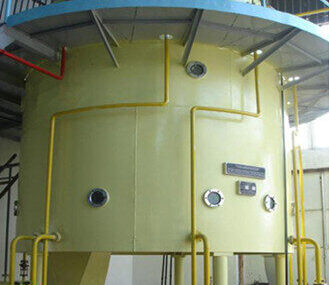
Wet Meal Desolventizing
The wet meal from the oil extractor enters the DTDC desolventizing the cottonseed oil extraction plant.After pre-desolventizing, desolventizing, drying, and cooling, the solvent is removed and the dry meal is obtained and sent to the meal storehouse for packaging. There is automatic feed valve on the desolventizing layer to keep constant material level.
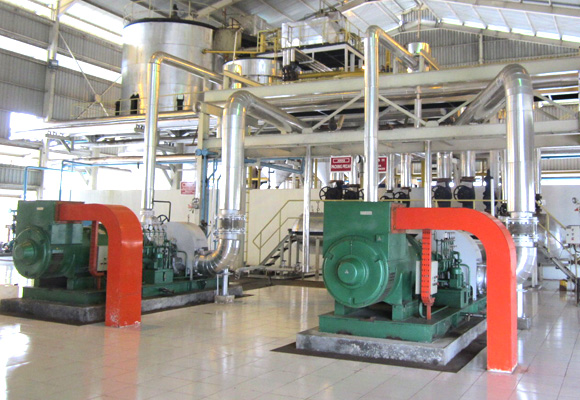
Evaporating and Stripping
The miscella in the miscella tank enters the first long tube evaporator, the second long tube evaporator and the disk stripping column to remove the solvent. The whole system works under negative pressure. The crude oil obtained goes to the cottonseed oil refinery plant.
d. Solvent recovery: The solvent vapor enters the condensing system. The solvent recycled enters the solvent holding tank for circulation. The wastewater is discharged into the water seal tank. The vent gas in the cottonseed oil extraction plant enters the mineral oil system for further recovery of solvent. Solvent recovery can reduce solvent consumption and ensure safe production.
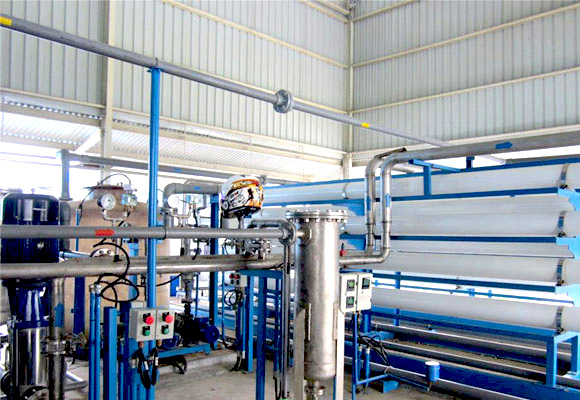
CRUDE OIL REFINING PROCESS
Cottonseed Crude Oil → Alkali Refining → Degumming → Centrifugal Drying → Continuous Decolorization → Dewaxing → Continuous Deodorization → Filtration → Finished Cottonseed Oil
Cottonseed contains a kind of glyhol that is harmful to the human body. Whether it is squeezing or leaching cottonseed oil, it must be must be refined. we provides three types of cottonseed oil refining equipment: batch refining equipment, semi-continuous refining equipment of cottonseed oil, and full continuous refining equipment.
Cottonseed oil refining equipment can remove various impurities such as collagen -soluble impurities, free fatty acids, pigments, and odors in puff seed oil, and improve the stability of cottonseed oil.
The cottonseed oil refinery workshop has the water degumming process, deacidification process, deodorization process, bleaching and filtration process and fractionation process, after these processes are refined, the oil can be removed from harmful substances and most impurities.
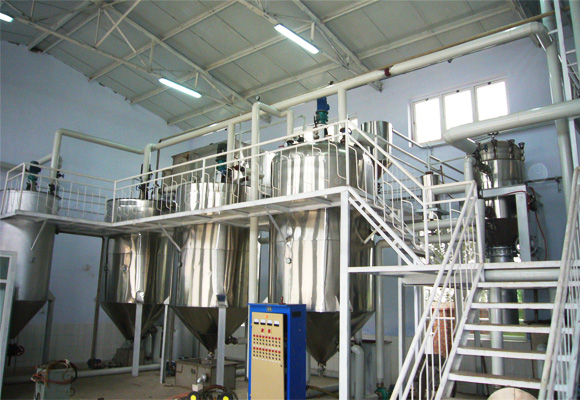
Cottonseed oil degumming is generally used in water dehydration process. Adding a certain amount of phosphoric acid solution to condense the colloid impurities, and then sink the colloid impurities and separate the oil.
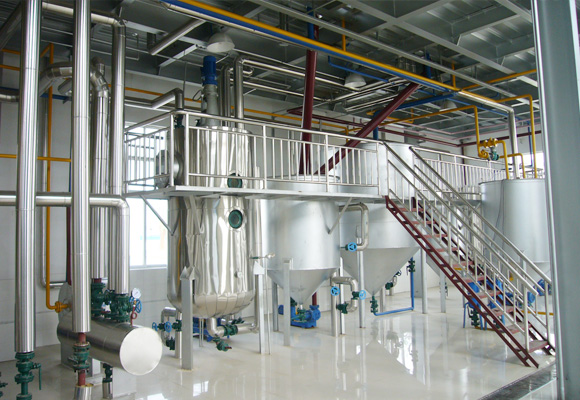
Cottonseed oil deacidification process has two kinds: chemical and physical. The chemical deacidification process is to add alkali liquor to react with FFA to generate nigre and the physical deacidification process is using high temperature steam to distill the FFA out.
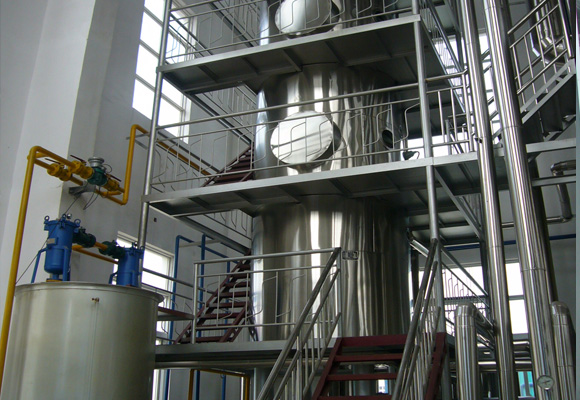
After deacidification, the crude cottonseed oil need to be decoloried by bleaching process. It is usually to use white clay to absorb the pigments, at same time absorbing residual gums and soapstocks. And then through filtering by plate filter, the waste clay will be filtered out. Cottonseed oil decolorization process is mainly to make the oil color more lighter, and qualified the national standard.
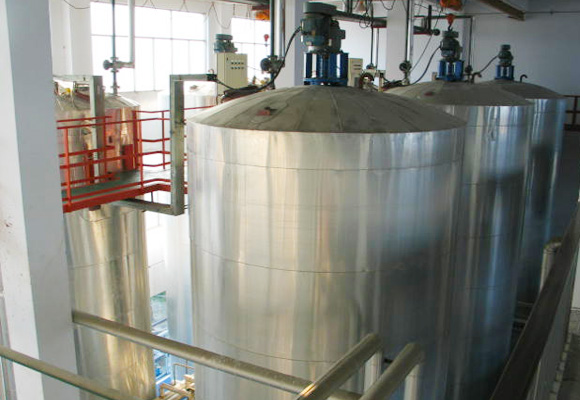
Cottonseed oil deodorization process often uses distillation principle, injecting high temperature steam to distill the odors out. The deodorization process can not only remove the odors from crude cottonseed oil, but also improve smoke point, flavor, steadily and quality of final oil.
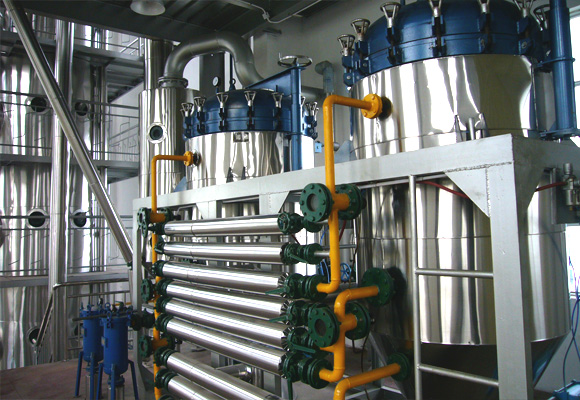
At last, cottonseed oil refining has a special process — cottonseed oil fractionation process. It is to seperate the solids and liquids in cottonseed at a specific temperature. Similar with palm oil fractionation process, through cooling, crystallization and filtration, you can get two parts: cottonseed oil olein and cottonseed oil stearine.
We provides complete plant solutions for converting cottonseed to cottonseed oil and cottonseed protein. Our comprehensive range of products helps you to increase yield while meeting increasingly stringent environmental and health requirements. When you have a project plan for the cottonseed oil processing plant, please contact us soon.
Technology Feature
The project uses cotton meal (46% of protein content) as raw material, and separates the cottonseed hulls and lint from the cottonseed meal through the pretreatment workshop to produce cottonseed meal by-products with high protein content;
The pressing efficiency and the stability of the oil press equipment are the key to the oil pressing process. Our oil press machine with large output, low cake residue and good cake quality.
The protein content of cotton meal reaches 57%. The cottonseed meal (57% of protein content) enters the solvent extraction workshop, and the gossypol and raffinose components in the cottonseed meal are extracted by a low-concentration methanol solution in the extractor to produce cottonseed protein concentrate products and crude raffinose products.
The advanced physical refining process reduces the loss of refining oil and improves the oil quality. The by-products – fatty acids can be directly obtained, helping factories realize the economic benefits of sustainable development. There is no waste water pollution during the process, while meeting the environmental and health requirements.