I will introduce the complete soybean oil pretreatment production line + soybean oil solvent extraction plant + soybean oil refinery plant one by one.Soybeans are used as raw materials through pretreatment and leaching processes to obtain soybean crude oil and soybean meal, the soybean crude oil is put into the market after advanced physical refining and dewaxing process. Soybean oil occupies an important position in the world’s vegetable oil production and consumption, mainly in cooking oil, food processing, pharmaceutical and other industries.
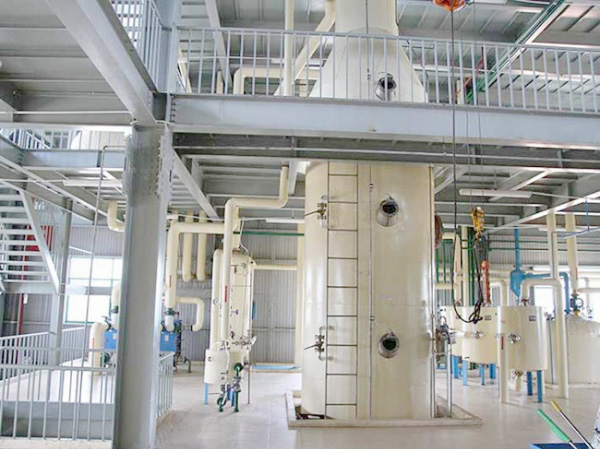
We provides intelligent soybean oil processing and soybean by-product deep processing solutions covering the entire supply chain – soybean pre-treatment workshop equipment, soybean embryo leaching workshop equipment, soybean crude oil refining workshop equipment, soybean oil dewaxing, soybean protein isolate, soybean protein concentrate, soybean lecithin production line.
Soybean Oil Production Line Overview
The soybean oil production line is the process of treating soya bean with the press method or leaching method to obtain more crude oil and then refined to obtain edible refined oil. Pressed soybean oil has natural colors, aromas and flavors, and retains raw material’s various nutritious ingredients when comparing with the leached oil. The physical pressing line requires raw materials to be carefully selected, and the soya bean is pre-treated through cleaning, crushing, softening, rolling and extruding. After that, the cleaned beans are added during the pressing process and the oil is extracted from the pressing machine, and the finished oil is produced by using high-tech physical refining filtration purification technology. The physical pressing method maintains the original flavor of soybeans, rich in vitamin E, and has a long shelf life. And the screw pressed oil has no additives, no solvent residue, and no soap content. Soybean oil pressing line is a combination of modern and traditional technology that produces pure natural soybean oil.

soybean oil processing line and technology processes
The main compositions of soybean meal are protein and amino acid. We provide specific processing solutions to obtain low temperature soybean meal and high temperature soybean meal. Low-temperature soybean meal can be processed as raw material for protein isolate and protein concentrate, and high-temperature soybean meal is mainly used for animal feed。
A full range of advanced soybean oil processing equipment and technology processes, including advanced physical refining technology and soybean protein processing technology, recover higher quality soybean protein and fatty acids from soybean meal, and reuse processing by-products while increasing annual output. Our innovative solutions help factories realize the economic benefits of sustainable development. Contact us now to learn more about how our solutions and equipment can help you achieve long-term, reliable, and more profitable operations.
Solutions for soybean oil processing
1, Soybean pretreatment workshop process:
Soybean → Weighing → Cleaning → Stoning → Conditioning → Cracking → Peeling → Aspiration → Flaking/Flattening → Extruder → Cooling → Solvent Extraction
2, Soybean meal leaching workshop process:
Soybean flakes→ Wet meal desolvation→ Mixed oil evaporation and desolvation→ Solvent cooling and water separation → Exhaust gas recovery→ Leaching oil to refining workshop
3, Soybean oil refining workshop process:
Crude soybean oil→ Continuous degumming and deacidification→ Continuous decolorization→ Continuous deacidification and deodorization→ Cooling – deodorized oil to dewaxing workshop
4, Soybean oil dewaxing workshop process:
Deodorized oil → Pre-cooling → Crystallization → Filtration and separation → Refined oil
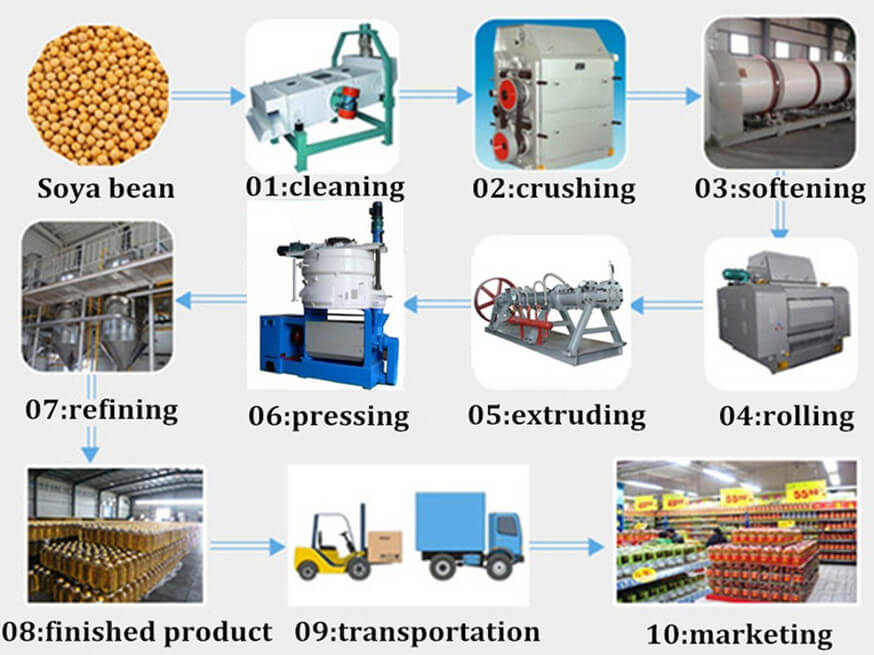
Main equipment introduction of Soybean oil production line
Pre-treatment section
Before the oil is prepared, the pretreatment of soybeans requires cleaning, crushing, softening, rolling, extruding, etc. for the soybean oil processing industry.
Soybean Cleaning
Soybean should be cleaned first. The main purpose of this section is to remove the impurities of soybeans. The impurities are mainly plant impurities (such as bean stems, pods, etc.), metal impurities and non-metallic impurities.
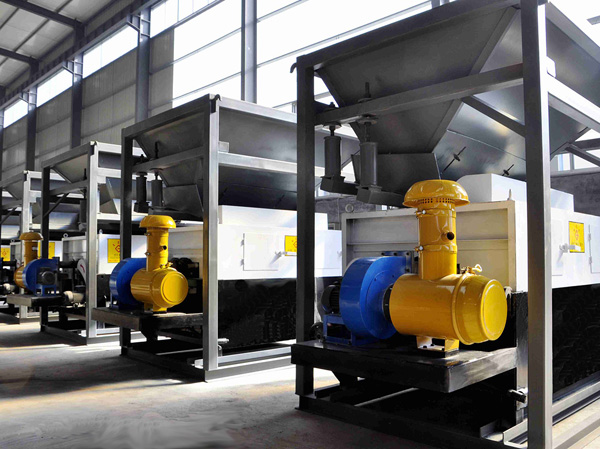
Magnetic separator: adopts magnetic force to remove metal impurities by using the magnetic difference of various ores or materials, the metal impurities are usually nails, small iron wire, etc. Removal of metal impurities avoids the abrasion on the machine in the subsequent work.
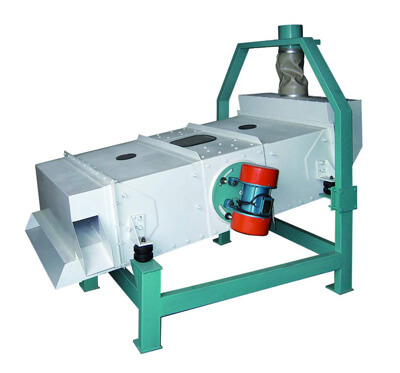
Vibrating cleaning screen: The raw material may contain soil, leaves, stems and other ball impurities, which need to be cleaned up before the subsequent process. High-frequency vibration equipment can effectively remove impurities by using differences between oil and impurities in particle size, with the help of the relative movement between impure oilseed and sieve surface, finally, the impurities larger than or less than oilseed can be removed through the sieve hole. This kind of cleaning sieve is suitable for medium and large factories.
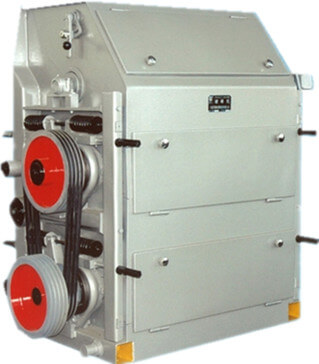
Soybean Crushing
After cleaning, the soybeans are sent to the crushing section, the main purpose is to crush the soybeans and separate the soybean skins from the bean kernels.
toothed roll crusher
Generally, soybeans are required to be broken into 4 to 8 valves, and the powdery degree (when crushed beans passing through 20 meshes screen) is less than 10%. The crusher is preferably a toothed roll crusher with cutting, impacting and bending effects. YPSG series toothed roll crusher is mainly used for crushing such large granular material like soybeans, so as to produce the excellent embryo and improve the yield. The machine has the characteristics of small noise, high output, uniform crushing granularity, low power consumption, small footprint, simple structure, flexible and reliable, convenient maintenance and so on.
Purposes of crusher
Crushing makes the oil material with a certain granularity to facilitate compact rolling.
Crushing increases the surface area of the oilseed, which is conducive to the transfer of temperature and moisture in the softening process of the oilseed and ensure the softening effect.
The seeds are crushed into small granules, which is good for the next oil press section.
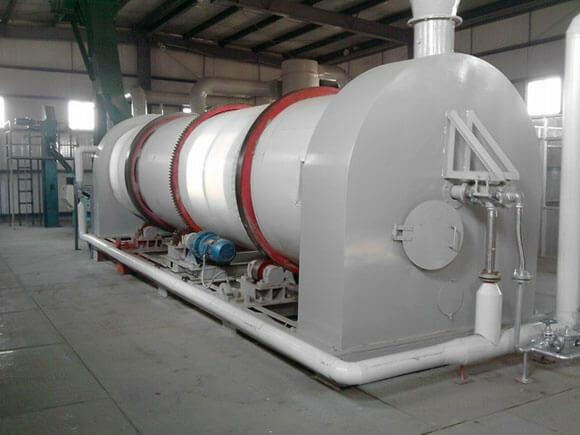
Soybean Softening
Softening is through the adjustment of oilseed moisture and temperature to improve the elasticity of seed so that it has the best conditions for rolling. Softening is mainly used for seeds with low oil content, low water content, poor physical properties and hard texture. Soybeans have low oil content and poor plasticity, which need to be softened before rolling. Softening temperature should be based on the level of soybean moisture. When soybean moisture is 13%~15%, the softening temperature is usually controlled at 70~80℃, and the softening time is 15~30 minutes. The commonly used softener for soybeans is a horizontal softening pot, which has a better softening effect.
The main function of softening
It gives the soybean kernel certain plasticity and makes it easy to roll out the thin flakes when flaking.
Softening can reduce the powder degree and sticky roller phenomenon, to ensure the quality of the flakes.
Working principle of horizontal softener
The material enters the drum through the inlet, and with the rotation of the drum, the material is constantly turned over. Meanwhile, the drum is equipped with a heating tube and steam is passed through the tube, the material is heated, steamed and rotated at the same time. According to the softening condition of the material, the softening time of the material can be controlled by adjusting the rotating speed of the rotary drum to optimize the softening effect.
Features of horizontal softener
The rotation of the horizontal softening pot makes the material turn over more evenly, and without dead angle. With the improvement of avoiding the dead angle of layer softening pot, which causes the phenomenon of burnt paste, the horizontal softener can soften the material evenly and thoroughly.
The horizontal softener avoids the abrasion of the scraper and heating layer, so the equipment has long service life, low failure rate and low maintenance cost.
Because of its unique structure, the volume of horizontal softening pot is much smaller than that of layer type, the arrangement of it in workshop is easier, the area of occupation is small, and the investment of equipment is greatly reduced.
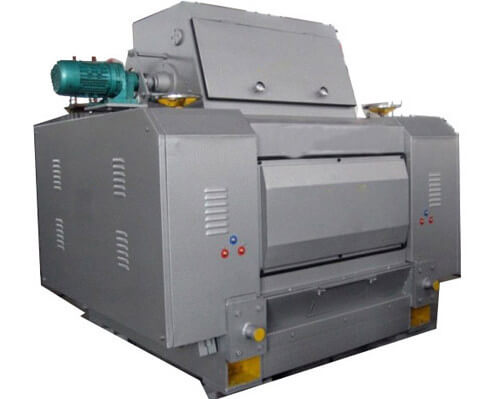
Soybean Rolling
Soybean rolling is the process of using the mechanical function to roll the oilseed from the granular to flake.
1.4.1 Purpose of soybean rolling
The purpose of rolling is to destroy the cell structure of oilseed, increase the surface area of seed and shorten the distance of oil flowing out, which is beneficial to the extraction of oil. In order to ensure the quality of rolled flakes, the moisture and temperature of materials before rolling should be strictly controlled.
Soybean rolling equipment structure
Feeding mechanism: keep flowing and distributing uniformly
Roller: main working part
Distance adjusting device: spring type, lever type, hydraulic type
Baffle and scraper
Transmission device
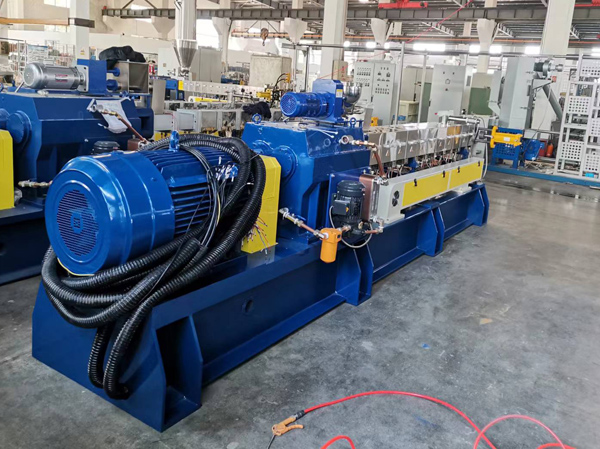
Soybean Extruding
Soybean extruding is the process of using extrusion equipment to break through the crushed, rolled soybean into porous, expanded granular material. Extrusion is a kind of high temperature and short time processing. At present, the commonly used soybean extruding machine is low moisture single-screw extruder, and the material is extruded by heating, pressing, gluing and vacuum extrusion. Generally, extrusion temperature can reach 110~200℃, and the residence time in the extruder is for the l~3 minutes.
Oil pressing section
Soybean meal leaching workshop process:
Soybean flakes→ Wet meal desolvation→ Mixed oil evaporation and desolvation→ Solvent cooling and water separation → Exhaust gas recovery→ Leaching oil to refining workshop
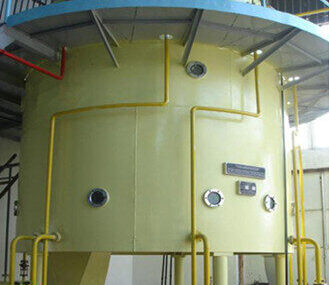
Soybean oil leaching: Pre treated soybean cake is subjected to hot fresh solvent countercurrent circulation spray extraction in the extractor, achieving separation of oil and meal. During the extraction process, the characteristic of oil and fat being soluble in solvents is utilized to achieve the transfer of oil and fat from the solid phase to the liquid phase. The main driving force for mass transfer is the concentration difference of oil in the solid-liquid phase, which is achieved through two methods: molecular diffusion and convective diffusion.
In the production process of soybean oil, leaching is an important technique. The pretreatment process of leaching method includes steps such as cleaning and removing stones, crushing, softening, rolling, drying, and leaching. This process can efficiently extract oil from soybeans and has the characteristics of environmental protection and energy conservation.
The leaching system adopts a unique exhaust gas absorption system, which can effectively absorb exhaust gas. At the same time, the energy-saving design enables multiple uses of heat energy, significantly reducing the amount of steam used. These characteristics make the leaching method widely used in soybean oil production.
Oil pressing is a mechanical extracting method by using screw press to squeeze oil out from clean materials under pressure. The capacity of oil screw press is from 1 to 50 tons per day, which are commonly used for continuous mechanical extraction of oil these days, regardless of the size of the operation. There are many factors that affect the efficiency of oil extraction, such as vegetable seed types, temperature, press configuration, etc. Usually, the physical pressing method has an oil output of 65-70%, which is suitable for commercial processors to build small and medium screw pressing oil plant.
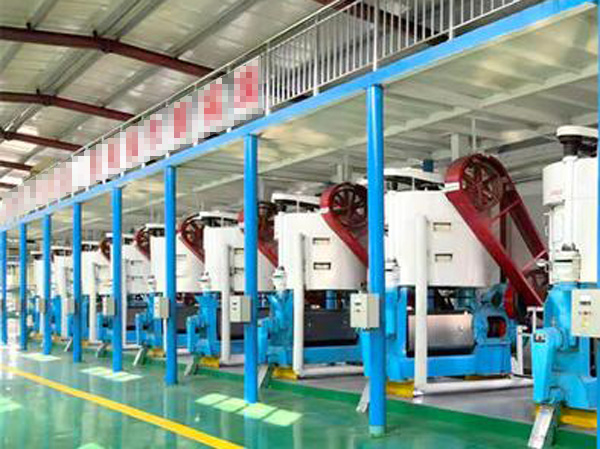
Cold Pressing
Today, the soybean oil is divided into cold pressed oil and hot pressed oil. The cold-pressed soybean oil has a lighter color and a lighter raw smoky taste. The hot-pressed soybean oil has high oil yield due to the high-temperature treatment of the raw materials, but it has a darker color and a stronger green bean odor. Therefore, the commonly used oil screw pressing method is cold pressing: the physical pressing method has irreplaceable technological advancement for the pursuit of green, authentic, healthy food. In order to achieve additional oil recovery, the seed material must be subjected to a longer retention time of high pressure in the screw press. Higher pressure is mainly achieved by lower seed moisture, resulting in high friction in the press. Because of the mechanical strength, the maximum diameter of the press cage is determined. The higher the pressure, the more limited the capacity of the press is. Moreover, the longer the retention time is required, the lower the shaft speed is required. This further limits the capacity. Therefore, the cold press is characterized by a capacity of only 1/10 of the capacity of the modern pre-pressing machine. But cold press machine can screw out 80~90% oil from seeds. This means that the total remaining oil content in the full-pressed cake is around 10~20%.
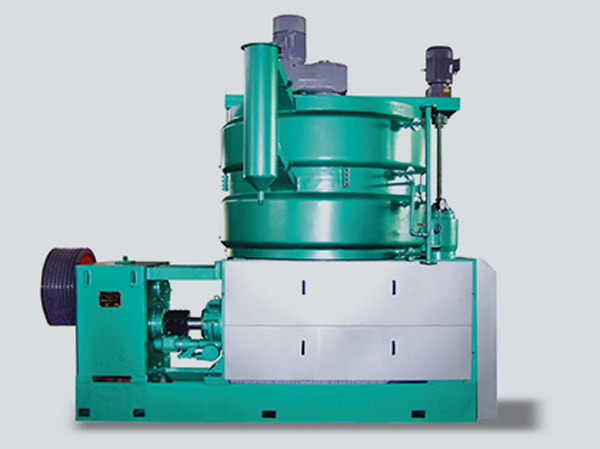
cold pressing machine
cold press is a new generation of spiral oil press designed for the cold pressing of various oils, especially suitable for mechanically squeezing organic plants and high value-added commercial crops. The cold pressing machine is suitable for squeezing soybean, rapeseed, peanut, etc., Lyzx24 pressing machine could be equipped with single-screw or twin-screw structures. Based on the single-screw press, a twin-screw cold-pressing machine is developed with the improvements of superior mechanical properties and high oil production rate and optimized stamping process, which produces high-quality oil and cold-pressed cakes with high efficiency. If the seed has high oil content, it should be added double press to obtain maximum yield.
Cold pressing features
The pressing temperature is low, the oil yield is high, the residual oil is low, the cake protein is less denatured, the processed oil color is relatively shallow with good quality and rich nutrition, which meets the oil standard on the international market.
The cold pressing machine is suitable for squeezing soybean, rapeseed, peanut, teaseed kernel, sunflower seed kernel, cottonseed kernel, etc., widely applicable and multifunctional.
Lyzx24 pressing machine is equipped with temperature and moisture control devices, easy operation.
Soybean oil refining workshop process
Crude soybean oil→ Continuous degumming and deacidification→ Continuous decolorization→ Continuous deacidification and deodorization→ Cooling – deodorized oil to dewaxing workshop
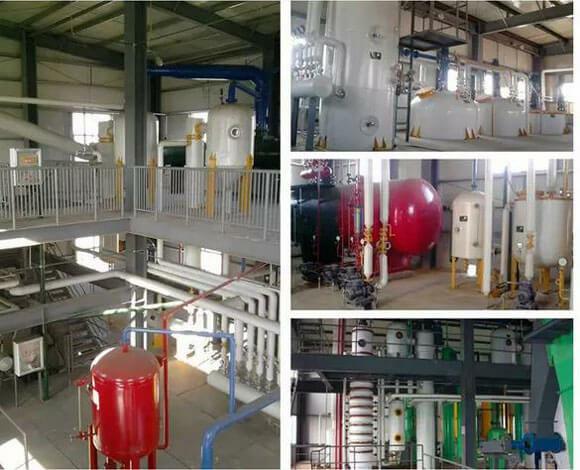
Superfine Fragrant Soybean Oil Refining Process
This workshop adopts the production technology of batch refining. According to the type and quality of the crude oil, the process parameters are adjusted and different refining methods are selected to produce the first and third-grade oils. The process equipment we provide has the following features:
Flexible and convenient adjustment system, slight changes in raw material quality can still be normally produced.
Maximum heat recovery, significant energy savings.
The fully enclosed operating system avoids the oxidation of oil and ensures the high quality and stability of the products.
The use of advanced physical refining processes has effectively increased the refining rate. At the same time, the amount of sewage and the sewage treatment costs are greatly reduced.
Soyoil Refining Process Instructions
Alkaline refining operation: Adjust the oil temperature to around 60℃, then, add 20~30°Bé into the pot within 5~10 minutes and stir for 5~10 minutes under the mixing speed of 60r/min. Observe the separation of soap particles after the reaction, meanwhile, start to heat the mixture and slow the speed of stirring. When the temperature reaches 65℃(Approximately 1 degree per minute), separation of oil soap is obvious, stop stirring, start to stand still the mixture to settle soap foot, it generally takes 4 to 6 hours to release the soap foot.
Washing: After releasing the soap foot, the oil is further heated to 75℃, and then hot water is added for washing and stirring. The water temperature should be 5℃warmer than the oil temperature since too low water temperature is easy for emulsification. After the addition of water, continue to stir the oil for five minutes, then it takes four hours for the oil sedimentation, and finally, soap water is discharged. Oil washing can be repeated 1 or 2 times, depending on the quality of the oil.
Vacuum drying and decolorizing: First, turn on the vacuum pump: the vacuum degree≥ Next, the washed, alkali-refined oil is sucked into a decolorizing pot, and the oil is heated to about 100℃ while stirring under vacuum condition, then stirring for 10 minutes to reduce oil’s moisture content to 0.1% or less. After that, clay or active carbon is added to the pot(the additive amount of decolorizing agent is 2~4% of oil amount), stirring for 20 minutes. Next, stop heating until the temperature is less than 90℃, after the vacuum pump is turned off and the decolorization of the pump is turned on, oil is pumped to the oil filter for filtering. The product oil is separated in the oil filter to obtain the refined oil.
Deodorization(alternative): Decolored oil→oil-feed pump→No. 1 oil heat exchanger→No. 2 oil heat exchanger→No. 3 heat conduction oil heat exchanger→Deodorization tower→ Shielding pump→No. 2 oil heat exchanger→No. 1 oil heat exchanger→Product oil
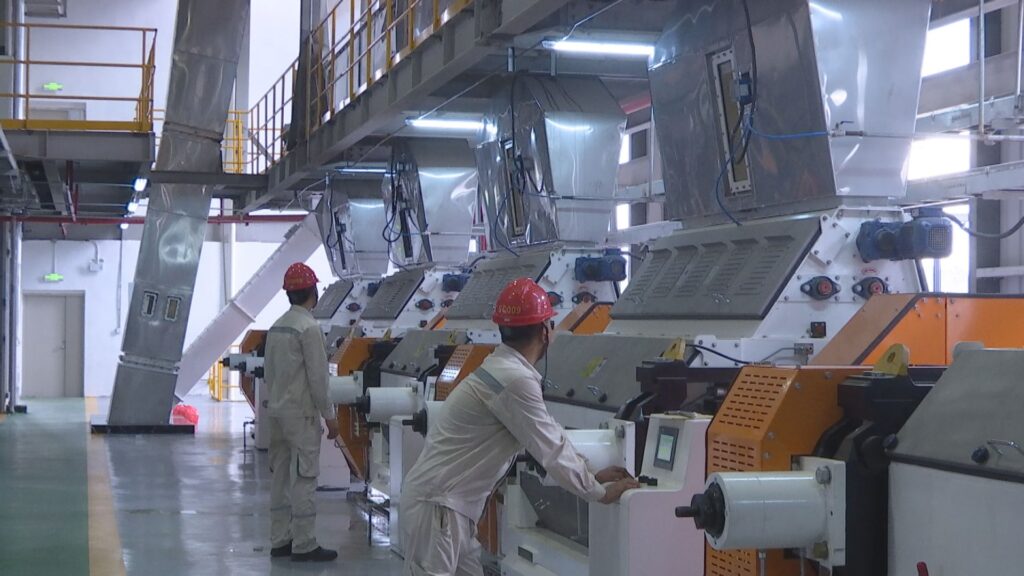
soybean oil processing plant
Benefits of our professional solutions for soybean oil processing equipment
The complete set of soybean pretreatment equipment is full continuously and mechanized operation, ensure advanced process indicators, while reduces equipment investment, such as land cost, operating and maintenance costs.
The leaching workshop adopts the international level leaching system and low temperature desolventizing machine, achieve higher mixed oil concentration and lower residual oil. Reduce the amount of solvent circulation, energy and dissolution consumption, thus ensuring the lowest level of residual oil and dissolution consumption.
The fully closed operation system of the leaching workshop, the full negative pressure evaporation avoids oil oxidation; the separation of crude oil and solvent can be realized at a lower temperature condition, which ensures the quality of leaching crude oil, improves the refining rate and significantly reduces energy consumption.
The advanced physical refining process reduces the loss of refining oil and improves the oil quality. The by-products – fatty acids can be directly obtained, helping factories realize the economic benefits of sustainable development. There is no waste water pollution during the process, while meeting the environmental and health requirements.