The company specializes in the production of biomass pellet fuel complete production line equipment, can provide customers with logs, wood chips, shavings as raw materials of biomass pellet production line; Biomass pelleting production line with building templates and woodworking scraps as raw materials; Biomass pelleting complete production line with corn straw, wheat straw and straw as raw materials; The complete production line of biomass pelletizing with fruit shell, fruit residue and palm as raw materials; With crop waste, sludge, coal and other raw materials for the biomass pelleting complete production line, tailor-made for customers a variety of complete equipment solutions to meet the different needs of customers.
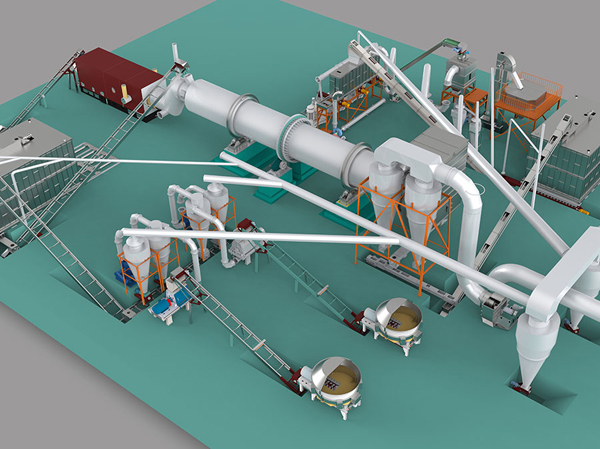
Pellet biomass production line
Capacity: 1000kg/ H-80000kg /h
Raw material: Moisture >20% wet sawdust.
Application: Milling of sawdust.
Labor: 3-4 people.
3-4 t/h transformer ≥440 kVA.
4-6 tons/hour transformer ≥800 kVA.
Recommended users: large wood processing plants, garden companies and other users with raw material advantages.
We can provide customers with a complete set of biomass granulation production lines using raw materials such as logs, sawdust, and shavings; A biomass granulation production line using building templates, woodworking scraps, and other raw materials; A complete production line for biomass granulation using corn straw, wheat straw, rice straw, and other raw materials; A complete production line for biomass granulation using fruit shells, pomace, palm and other raw materials; A complete set of biomass granulation production lines using crop waste, sludge, coal shavings, etc. as raw materials, tailor-made various complete equipment solutions for customers to meet their different needs.
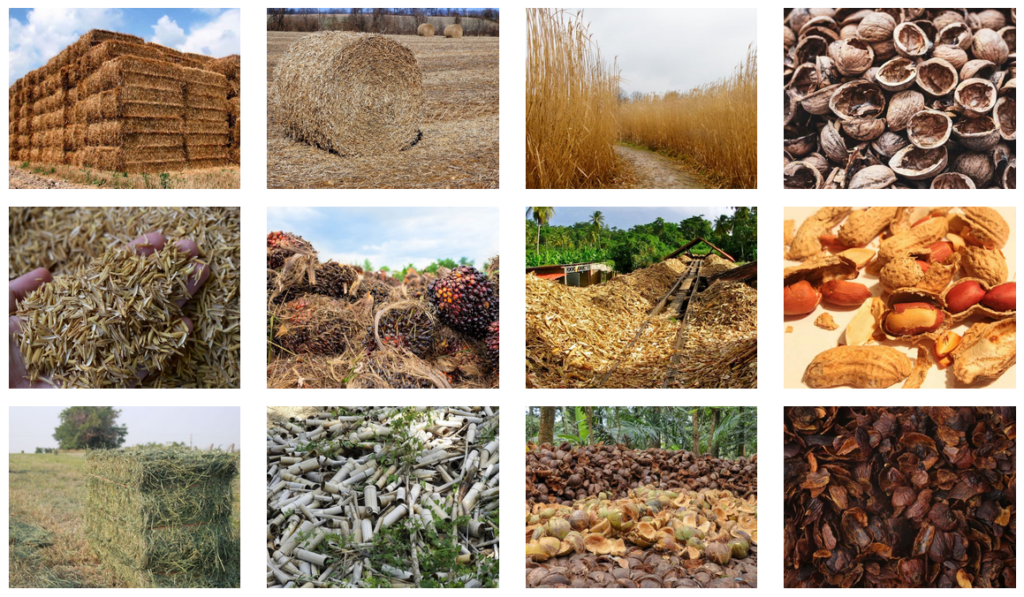
When it comes to fueling the future of your business, our commitment covers your operation’s entire lifecycle – from the first biomass raw materials analysis through decades of nonstop biofuel production. ZHI is vital to ensuring a reliable global supply of biofuel. With full biomass pellet processing lines we continuously support leading producers in achieving the highest levels in safety, quality, and control from feedstock to final product.
In general, the biomass resources available in biomass pellet production line, derived from large production areas, can be classified as follows:
Products from agriculture: (wheat, maize, potatoes, beetroot, sugar cane, rapeseed, sunflower, soya, palm and others) and livestock (fats in particular), all initially dedicated at least to food or feed, to which are added plants dedicated to energy crops, such as giant miscanthus for bioethanol, switchgrass or rapeseed for biodiesel.
Agricultural and livestock co-products and residues: straw, pulp, grains, oilcake, cattle manure, pig manure, poultry droppings, etc..
Fisheries resources: animal products from the sea and wetlands and their waste, algae and microalgae (the latter promising a great future because they are very rich in energy).
Fisheries resources: animal products from the sea and wetlands and their waste, algae and microalgae (the latter promising a great future because they are very rich in energy).
Natural waste from wood and forestry: (chips, sawdust) as well as from construction wood (chips, sawdust) and packaging wood industries (crates, pallets, cooperage), except those treated with toxic chemicals.
Waste from the food industry housing and urban communities: often wet or even liquid, including sewage sludge, household waste and organic waste from waste collection centers, waste from distribution and coffee shops or from green spaces.
Process design of Biomass Pellet Production Line
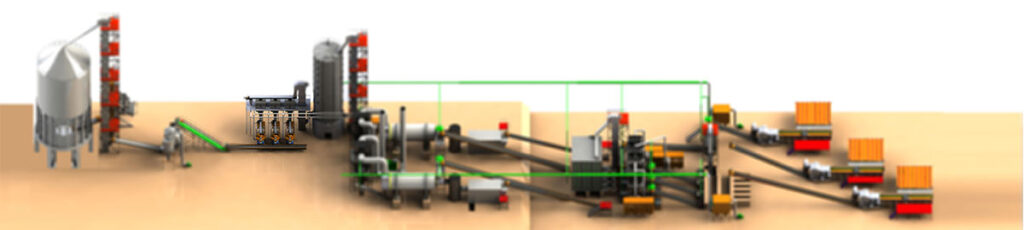
Biomass Raw Materials Storage
An effective feedstock storage system is necessary so as to keep biomass away from impurities and offer adequate protection from rain and moisture in general. Rain may actually damage the feedstock by increasing its moisture content to such a high level that the drying process becomes unviable.
Removal Of Undesirable Impurities
Raw material should be filtered before grinding to remove materials such as stones or metal fragments. Many biomass pellet plants are equipped with systems separating virgin biomass from inert materials such as stones and soil, or magnetic separators for metal impurity removal.
The presence of even the slightest amount of such materials in the final product is unacceptable. At the same time, they can cause serious damage to the biomass pellet line mechanical equipment, i.e. in the biomass sawdust hammer mill or in the biomass pellet machine.
Crushing Section
Raw materials before processing are relatively long or relatively large. The raw material must be reduced to a uniform size that is adequate for the biomass pellet mill. The milled material going into the biomass pellet making machine has to be smaller than the die holes to prevent blocking of the holes. Therefore, materials should be ground to a size no bigger than the diameter of the pellet (∼6 mm), producing a substance with a consistency similar to bread crumbs.
Generally, chippers/shredders are used as a first step. Then, once the size of the chipped material has been reduced, the hammer mill is used as a finishing mill.
Material Conveying Section
Once reduction has taken place, the material must be moved on to the next process. Screw conveyors are the most commonly used systems for transporting the material through the pelletization process because of the low cost involved.
Alternative options would include the use of a fan followed by a cyclone separator that separates air from the milled material. The air leaves the top of the cyclone, and the milled material is thrown to the outside edge of the cone and then falls out below.
Drying Section
Since the raw material is relatively large in water recovery. If the user of the large biomass pellet machine can dry the raw material, the small processing needs to be air-dried, and the moisture of the raw material is generally controlled between 15% and 25%. Excessive moisture can easily block the ring die of the biomass pellet press machine.
Drying solid biofuels is a key factor, since wet raw materials result in low combustion temperatures, low energy efficiency and high emissions of hydrocarbons and particles. In addition, it is very important to choose the right dryer, which may constitute the largest capital expenditure in a biomass pellet production plant and can dramatically increase the production cost per tonne.
Mixing And Conditioning Section
Not all raw materials require mixing and conditioning. It is generally used in the process of processing biomass raw materials such as grass (alfalfa, licorice), straw, shells, bagasse, etc. into animal feed pellets. Nevertheless, if necessary, mixers are used after the raw material has been milled and dried to:
Once the raw material has been mixed and its consistency is high enough, it may require the addition of other constituents able to increase the productivity of the pellet mill and enhance the final properties of the pellets produced.
Pelletization Section
The raw material has a moderate moisture content after being dried and can be molded without pressing any additives when the particulate fuel is pressed by the biomass pellet maker machine. It can produce a smooth and lustrous pellet fuel. Biomass pellets are finally made by biomass pellet mills, also known as pellet presses or extruders, which are available in a range of sizes. Generally, every 100 horsepower provides a capacity of approximately 1 ton of pellets per hour.
Cooling And Screening Section
Moisture resistance is an important pellet property. The biomass pellet line pelletizing process implies high temperatures, and attention must be paid to proper cooling and heat removal before the pellets leave a biomass pellet production plant, especially with regard to the storage stage. The produced biomass pellet fuel has a relatively high temperature and needs to be cooled through the cooling machine before being packaged. If the temperature is too high, the packaging is easy to produce water droplets to loosen the particles. Which is not conducive to sales.
Once biomass pellets have cooled, they pass over a vibrating screen to remove any fine material. These ‘fines’ are augured back into the biomass pelletizing process to ensure that no raw material is wasted. Screening ensures that the fuel source is clean and as near to dust free as possible. Once screened, pellets are ready to be packaged for the desired end use.
Packing Section
Biomass pellet fuel can be packaged in a quantitative packaging machine. It can be packaged into 5kg, 10kg, 25kg, and so on, which is convenient for small users to use. It can also be made into tons of bags, which is convenient for large users to use and unload.
The main categories of biomass production lines

Palm residue cassava biomass granulator pellets production line
The high humidity material drying and forming company develops biomass pellet fuel production equipment targeted at market demand, suitable for drying and forming materials with moisture content of 35-65% such as palm, cassava residue, sawdust, sawdust, bamboo chips, wooden chips, shavings, barley straw, oat straw, wheat straw, rye straw, straw, sorghum straw, corn straw, potato vines, bean stems, peanut vines, etc. Optimize the drying and molding process technology based on the characteristics, yield size, application requirements, cost control, automation level, and on-site conditions of each biomass material.
Bagasse pellet biomass production line
Main Equipment Included in Complete Pellet Plant: electric cabinet, packing machine, dust collector, cooler, hoisting machine, wood pellet machinery, conveyor, dryer and wood crusher.
(Bagasse chips, Sugarcane bagasse etc.).
In this process, the crushed materials will be dried to appropriate moisture content. To make premium wood fuel pellets, drying is one of the most important parts you should pay attention to. 12-16% is suitable in most wood pellet production process. High moisture could result in easy split pellets and low moisture could cause pelletizing difficulty problem. If you plan to build a large integrated wood pellet line, drum dryer is the best choice. Due to its big drum and structure, the price might be relatively higher than normal dryer. If your budget is limited, air flow dryer is also a good choice.
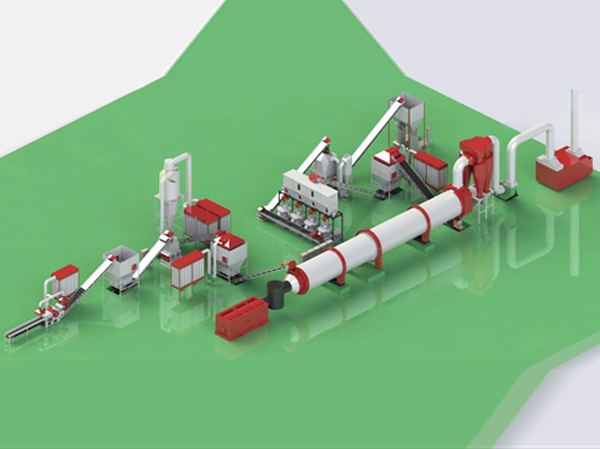
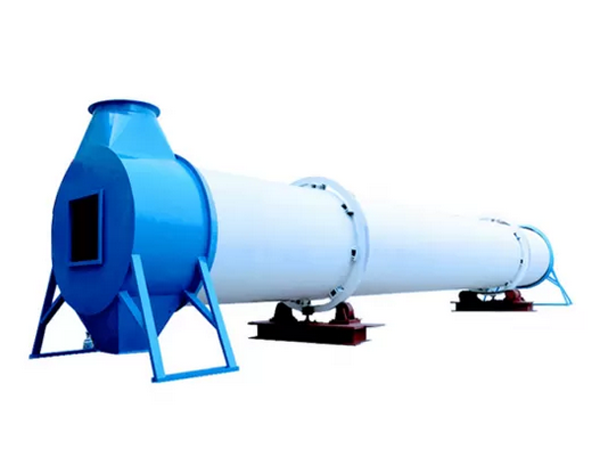
Rice husk pellet biomass production line
Our company specialized in developing, manufacturing, installing and debugging various feed machinery and bio-fuel machinery, and undertakes the construction of complete set of animal feed projects and complete set of biomass pellet projects. Wood pellets refer to the conversion of compressed materials into granular materials through compression and processing, which are usually used as solid fuel and are a renewable energy source.
Bamboo pellet biomass production line
Bamboo can be easily processed into pellets through a pellet machine. The calorific value of dried bamboo is about 16 MJ/kg, and its moisture content is about 13%. The fixed carbon content is about 15%, while the volatile substance content is almost as high as 80%. The above characteristics make bamboo comparable to wooden materials and superior to crop residues such as grass and straw.
The inorganic ash content of biomass particles depends on the composition of mineral components in the source fuel and the combustion process. The main ash forming elements are Na, Mg, Si, Al, Fe, Ca, Na, K, Zn, and Ti.
The value of bamboo as a biomass energy source
Bamboo is considered a new energy source. The biomass fuel processed from bamboo has a low calorific value of about 4400-4500 kcal/kg and an ash content of about 0-1%, which is similar to or slightly higher than that of oak, spruce, eucalyptus, etc. The fuel particles made of this material can be used for fireplaces and stoves.
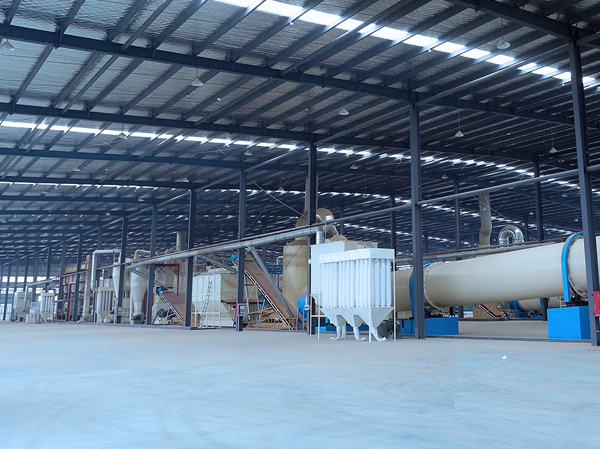
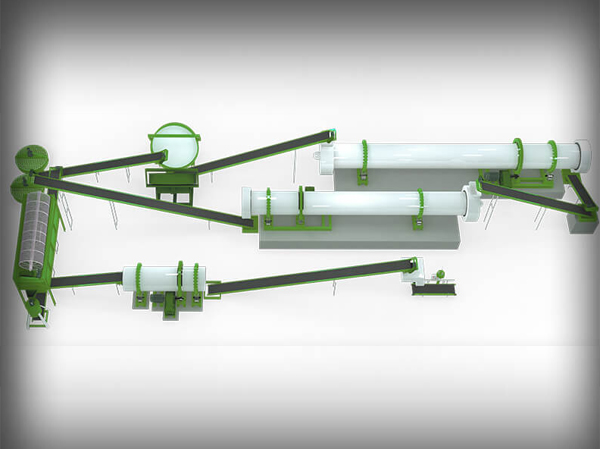
Alfalfa pellet biomass production line
The alfalfa pellet production line is a pellet feed made by processing alfalfa using a ring die pelleting process. It is rich in nutrients such as protein, minerals and vitamins, has high nutritional value, and is widely used in animal husbandry. Alfalfa pellets are products obtained by drying alfalfa and pelleting it. This form is conducive to storage and transportation. It is usually fed to ruminants such as cattle and sheep, and is mainly consumed by dairy cows. Alfalfa pellets have high protein content and can reduce the amount of concentrated feed to a certain extent. The alfalfa pellet line can be flexibly customized in modular form. Your raw materials can be grass meal, dehydrated alfalfa, or baled alfalfa.
Grass pellet biomass production line
Advantages of Grass Granules
- Many raw materials can be made into pellets, and using grass pellets as fuel has always been a recognized method in Europe. Not only fuel, but also grass pellets as feed are a great choice.
- Using grass pellets as biofuels is economical, energy-saving, environmentally friendly, and sustainable. As a clean fuel, more and more people prefer to choose grass pellets because the raw materials are cheap and easy to obtain.
- In addition, grass pills can be used as feed for many animals such as horses and cows. As feed, grass pills can replace some dry hay and are rich in nutrients.
Simple process
The production of grass pellets, as a low tech and small-scale renewable energy system, has great potential for local production, processing, and trading, while also having a positive impact on agricultural and pastoral areas. Easy access to raw materials and convenient operation of small granulators have become the choice of more people.
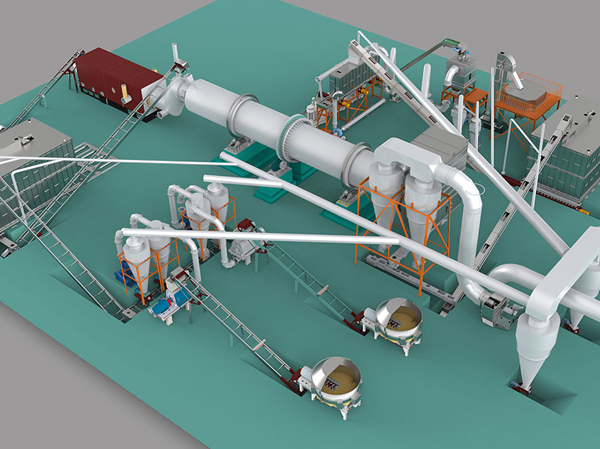
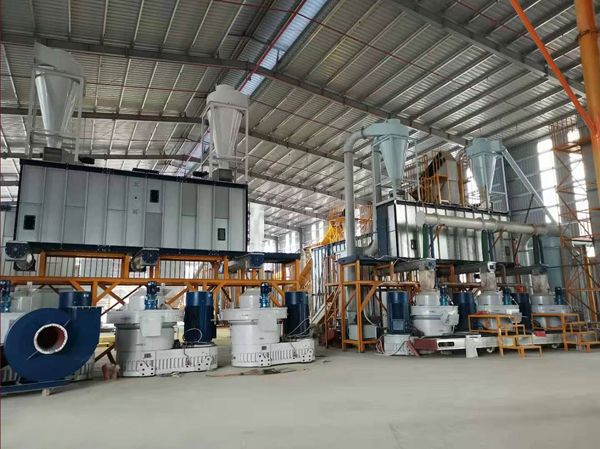
Straw pellet biomass production line
Straw pellet production line is a complete system that crushes, compresses and forms pellets of various crop straws, usually including cleaning, crushing, granulation, cooling, screening, packaging and other sections. Its basic principle is: through mechanical coercion, the raw materials are subjected to mechanical effects such as extrusion and friction, so that their own moisture content gradually decreases, becoming stable pellets without water or with extremely low moisture content. This production line is mainly used in the fields of feed, biomass fuel, etc., which can effectively utilize resources and reduce environmental pollution. In the future, straw pellet production line will have a wider application prospect and play an important role in the field of environmental protection and energy conservation.
Sawdust pellet biomass production line
Capacity: 1000kg/h-80000kg/h
Raw materials: Waste wood with a moisture content of about 10% -15%, furniture factory scraps
Application: Granulation of sawdust.
Labor: 2-3 people.
6 tons/hour transformer ≥ 500 kVA.
8 tons/hour transformer ≥ 800 kVA.
Recommended users: Large fuel plants, furniture factories, wood processing plants, landscaping companies, and other users with raw material advantages.
Sawdust is a by-product or waste product of biomass or woodworking operations such as sawing, milling, planing, and routing. It’s composed of small chippings of wood, bamboo, husk, etc.. At zhi, we supply the necessary sawdust pellet making machines to complete the entire biomass production plants globally. We are your partner for the lifetime of your equipment for making compressed sawdust pellets, whether originally supplied by zhi Machinery or any other manufacturers.
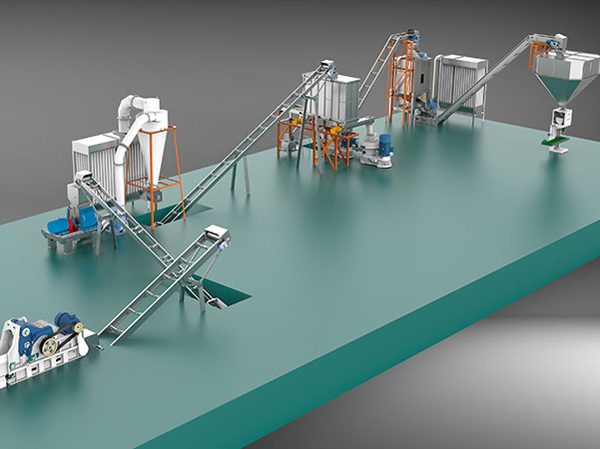
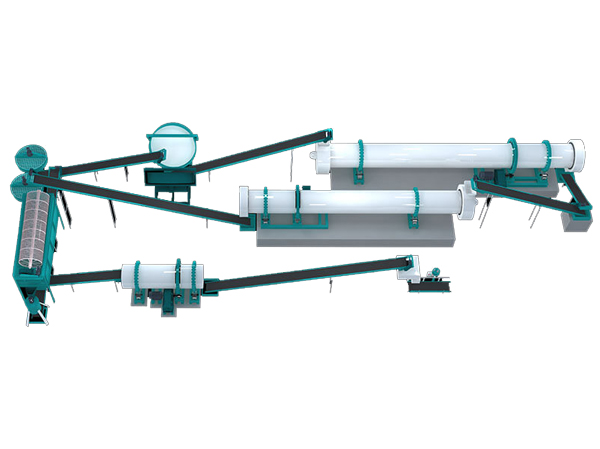
Wood pellet biomass production line
ZHI can provide the complete turnkey project biomass wood pellet production line, from design to install . Whether you want to produce wood pellet, sawdust pellet ,rice husk pellet, EFB pellet ,grass pellet or organic fertilizer pellet, the capacity is 1-100TPH can be choose. The main machine is wood chipper,wood crusher, drum dryer, wood pellet machine , cooling machine ,rotary sereener and others . Looking forward to your consultation !
The wood pellet production line is a high-efficiency, energy-saving and environmentally friendly biomass fuel production system. It handles and processes wood chips and converts them into wood pellet fuel, realizing the recycling of waste wood resources and environmental protection. The main equipment of wood production is wood pellet machine, wood chipper machine, wood hammer mill, rotary drum dryer, counter-flow cooler, packing machine, conveyors and electrical control equipment, etc. Our wood pellet plant establishments are staffed with qualified sales, engineering and service personnel and are well stocked with dies, parts and accessories. This ensures prompt, efficient processing of all customer service requirements.