Bamboo is a commonly used raw material for biomass pellet production lines and is considered a promising renewable resource. The advantages of bamboo are fast growth rate, easy processing, good mechanical properties, low cost, and wide range of uses.
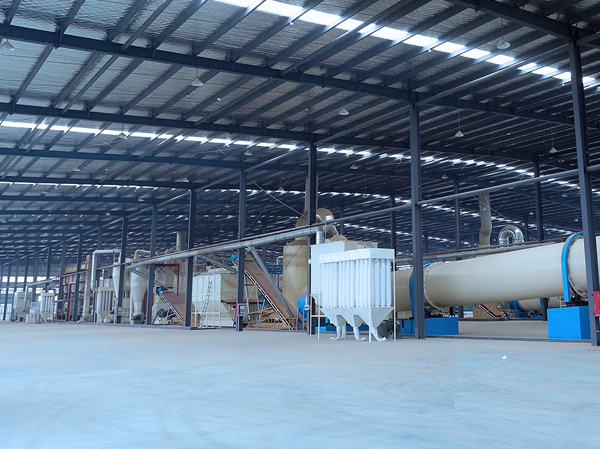
Bamboo pellet biomass production line
Bamboo can be easily processed into pellets through a pellet machine. The calorific value of dried bamboo is about 16 MJ/kg, and its moisture content is about 13%. The fixed carbon content is about 15%, while the volatile substance content is almost as high as 80%. The above characteristics make bamboo comparable to wooden materials and superior to crop residues such as grass and straw.
The inorganic ash content of biomass particles depends on the composition of mineral components in the source fuel and the combustion process. The main ash forming elements are Na, Mg, Si, Al, Fe, Ca, Na, K, Zn, and Ti.
The value of bamboo as a biomass energy source
Bamboo is considered a new energy source. The biomass fuel processed from bamboo has a low calorific value of about 4400-4500 kcal/kg and an ash content of about 0-1%, which is similar to or slightly higher than that of oak, spruce, eucalyptus, etc. The fuel particles made of this material can be used for fireplaces and stoves.
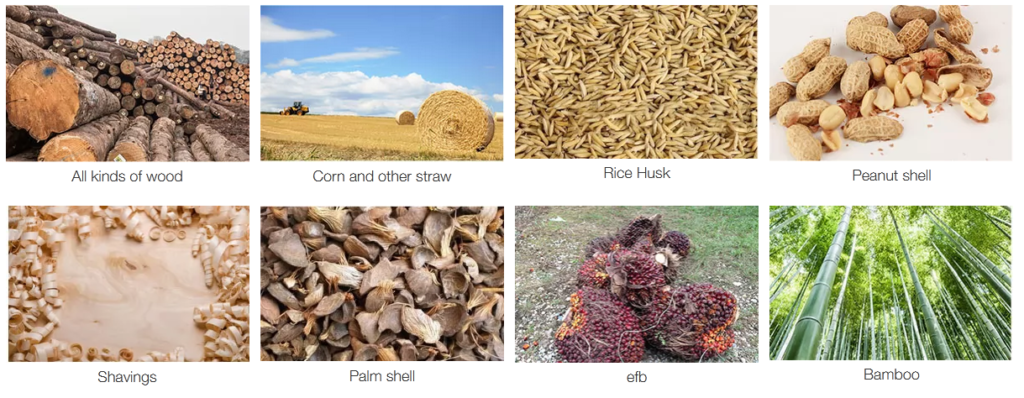
Production process of bamboo granules
The bamboo slag transported to the pellet factory is crushed into appropriate sizes, and the processed bamboo chips are dried and sent to the bamboo pellet machine for compression into pellets. Cool and solidify the newly extruded bamboo shavings into a solid and enhance their strength, while screening them to separate the bamboo particles and shavings, and then package, store or transport them. The entire process is shown in the following figure.
Equipment involved in the production process of bamboo chip granules
Electric control cabinet (controlling the power equipment of the entire production line)
The Tyrannosaurus crusher crushes materials of appropriate size and dryness into powder for granulation
The drum dryer dries the raw materials to the required moisture range for granulation
The biomass pellet machine granulates the prepared materials into pellets
The particle cooler cools the newly extruded hot particles and makes them harder
Biological particle ton bag packaging equipment (packaging particles according to requirements, can be small or ton bags
Conveyor equipment (placed at the front and back ends of the host equipment to assist in the transportation of raw materials during the production process)
As the core of bamboo pellet production, the pellet machine determines the quality of bamboo in the entire production line. The vertical ring model biomass fuel pellet machine is highly recommended due to its strong adaptability, simple operation, and easy maintenance.
For large-scale production of bamboo pellets, it is recommended to use a vertical ring mold pellet machine because of its high production capacity.
Case of 20t/h Bamboo Biomass Pellet Production Line
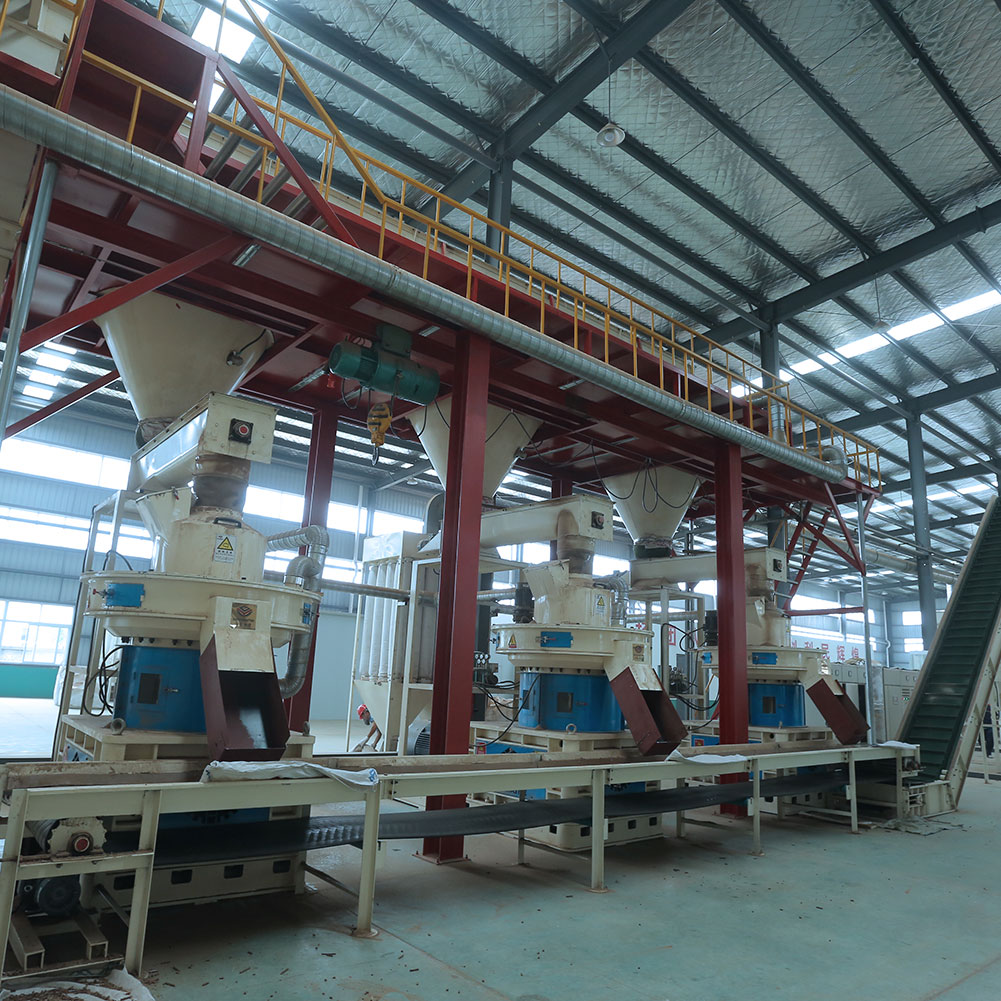
20t/h Bamboo Biomass Pellet Production Line
Product Item : Separate design
Category: Bamboo Pellet
Capacity:20t/h
Anual production capacity:100 hundred thousand tons
Cotrol system:full automatic computer control
Product description: 20t/h bamboo pellet production line,This is the largest complete biomass pellet project in Asia Area. Annual processing of 500,000 tons of waste straw, capacity 20 tons/h biomass pellets, annual
20t/h bamboo pellet production line.This is the largest complete biomass pellet project in Asia Area,Annual processing of 500,000 tons of waste straw, capacity 20 tons/h biomass pellets, annual output of 100,000 tons pellets.
The complete biomass pellet project finishes production and installation within eight months time adopts full automatic computer control system, completely achieves environmental without any dust it has a milestone significance among domestic competitors.
Including chipping section,the first drying section,grinding section,the second drying section,storing materials section,pelletizing section,cooling section,packing section,the whole dust removal section and computer control terminal system.
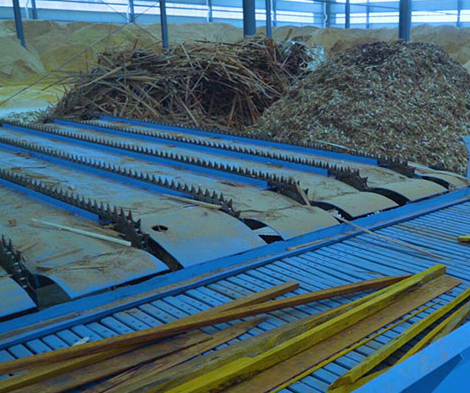
Chipping Section:
The mechanical gripper put the bamboo on the buffer platform then the vibration conveyor send it into the chipper machine crushing into bamboo chips .
Chipping Section:
The mechanical gripper put the bamboo on the buffer platform then the vibration conveyor send it into the chipper machine crushing into bamboo chips .
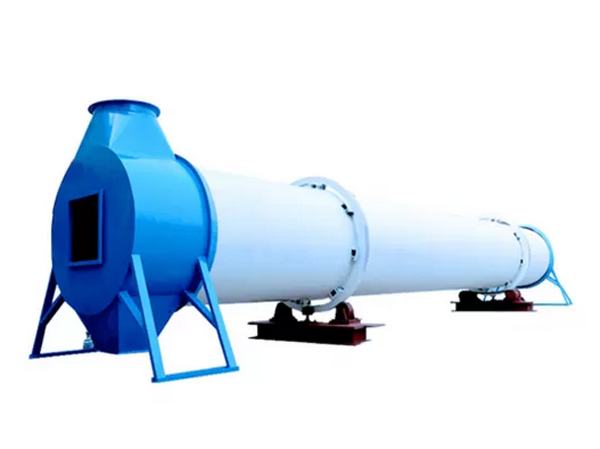
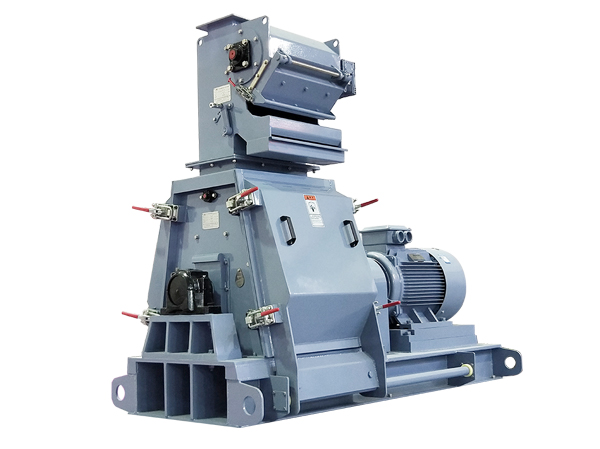
Grinding Section:
First, the roller conveyor will convey out the dried wood chips from buffer silo to belt conveyor,then wood chips will be conveyed by the belt conveyor into the double rotor hammer mill evenly, to be grinded there , then grinded powder move into the cyclone.
Pelletizing Section:
There are 6 sets 220kw YGKJ850 vertical ring die bamboo pellet machine in pelletizing section, after some time’s storage ,the moisture of material in the material, silo is evenly, easy to formation,220kw YGKJ850 vertical ring die bamboo pellet machine , high efficiency, strong stability, low maintenance cost ; each device highly independent, more reasonable program design.
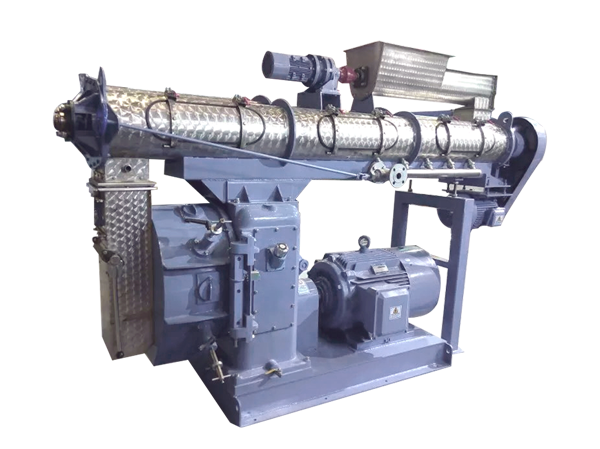
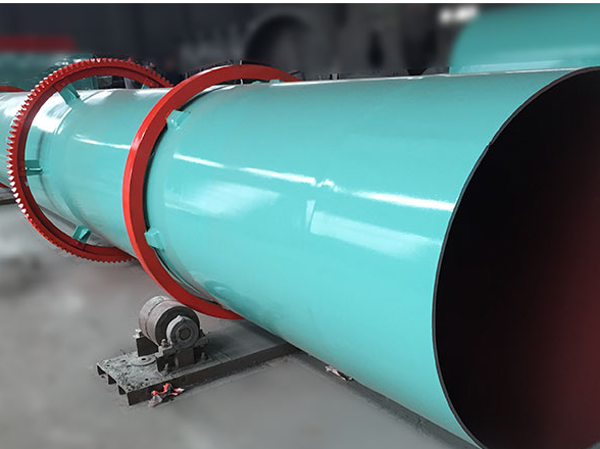
Cooling Section:
The counter flow circulating wind cooling bamboo pellets to room temperature . The cyclone collecting the dust , ensure clean. There is a simple screener below the cooling silo, screening cooled bamboo pellets, make pellets quality better, more standard.
Packing Section:
Screened bamboo pellets are transported to the finished product silo by the big-angle belt conveyor. The finished product is equipped with an automatic weighing of the tonnage scale, and the pellets are packed according to the set weight, and the net bag conveyor delivers the packaged pellets to the specified location.
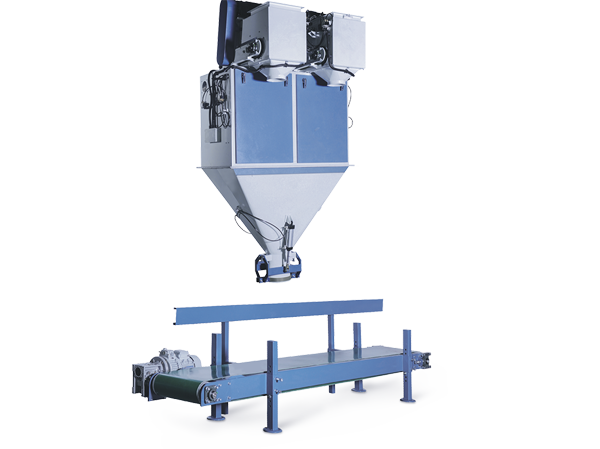
Dust Removal And Computer Control Terminal System:
The whole line use pulse dust collection and bag dust collection We use big wind pipe to collect all dust which produced in transport process into dust collection room,which protect the cleaning of all workshop.
The overall electric control system using the combination of centralized control and distributed control, so that the centralized management of the whole production line running will be better, distributed emergency control more timely.