There are many types of wood waste, such as wood bran, sawdust, wood chips, particleboard, wood blocks, wood chips, scraps, scraps, board scraps, branches, tree trunks, building templates, etc. We can process and reuse these waste wood materials that were previously considered useless, which can effectively reduce the waste of wood resources and play a good role in environmental protection.
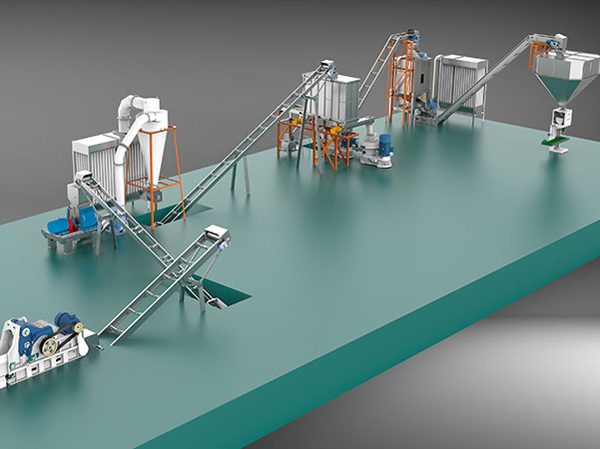
Sawdust pellet biomass production line
Capacity: 1000kg/h-80000kg/h
Raw materials: Waste wood with a moisture content of about 10% -15%, furniture factory scraps
Application: Granulation of sawdust.
Labor: 2-3 people.
6 tons/hour transformer ≥ 500 kVA.
8 tons/hour transformer ≥ 800 kVA.
Recommended users: Large fuel plants, furniture factories, wood processing plants, landscaping companies, and other users with raw material advantages.
Sawdust is a by-product or waste product of biomass or woodworking operations such as sawing, milling, planing, and routing. It’s composed of small chippings of wood, bamboo, husk, etc.. At zhi, we supply the necessary sawdust pellet making machines to complete the entire biomass production plants globally. We are your partner for the lifetime of your equipment for making compressed sawdust pellets, whether originally supplied by zhi Machinery or any other manufacturers.
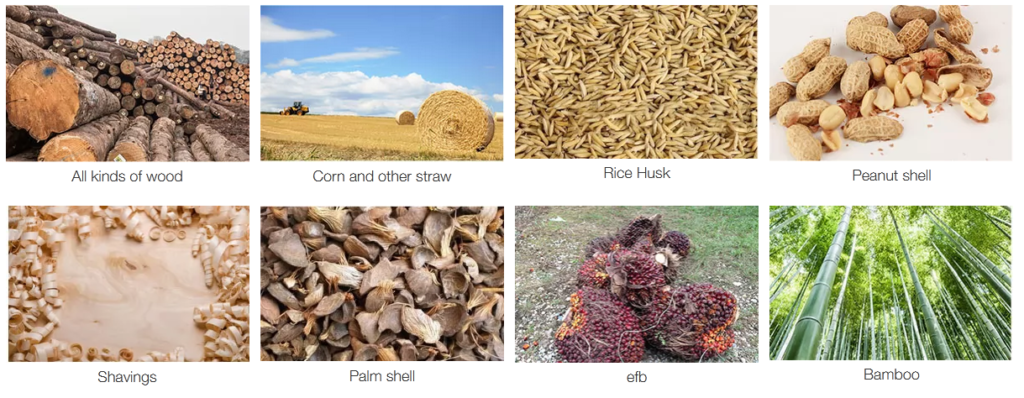
Why Make Sawdust Pellets with sawdust pellet production line?
Sufficient and cheap sawdust material source: Sawdust is the residue of wood processing factory. The amount of sawdust material is large and the price is cheap. Sawdust wood pellet mill and complete sawdust pellet production line can also be used to deal with life wastes such as leaves, straw and crops waste. It is a way to make waste profitable. And by making these biomass materials into fuel pellets, we no longer have worry how to dispose of these wastes.
Great demands for sawdust pellets: As the price of coal rise, finding coal fuel replacement is urgent. More and more people turn to biomass pellets. The market demand is large. Sawdust pellets not only be used at home in our daily life, but also can be applied to industrial production such as power plant.
Advantages of Sawdust Pellets
- They are a sustainable resource.
- They reduce energy imports and contribute to the national economy.
- The amount of waste released to the environment after use is negligible.
- They can be used to produce electrical energy.
- They generate CO emissions below the threshold.
- They are easy to transport and the need for storage is less compared to wood etc.
- They are manufactured from residual sawdust and similar waste materials without harming nature.
Production process of Wood chips sawdust pellet biomass production line
Process flow:
- Crushing: Wood through the crusher for coarse powder, can be broken scraps, slender material, fine logs and other weight is not light crushing materials and pure logs ≤Ø500.
- Crushing: The crushed material is fine powder through an efficient crusher, with a single output from 1ton to 80ton, which can meet a variety of needs.
- Granulation: The crushed material enters the silo and enters the granulation mechanism through the spiral dragon.
- Cooling: high temperature particles through the conveyor belt into the cooling machine cooling;
- Packaging: cooled particles into the packaging machine packaging.
Process advantages: relatively low raw material cost, good particle molding effect, profit margin is relatively large.
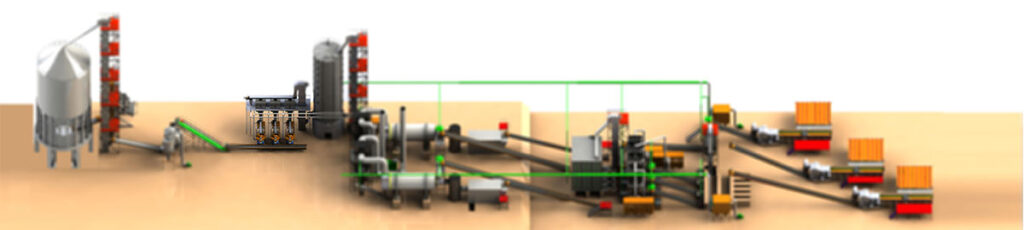
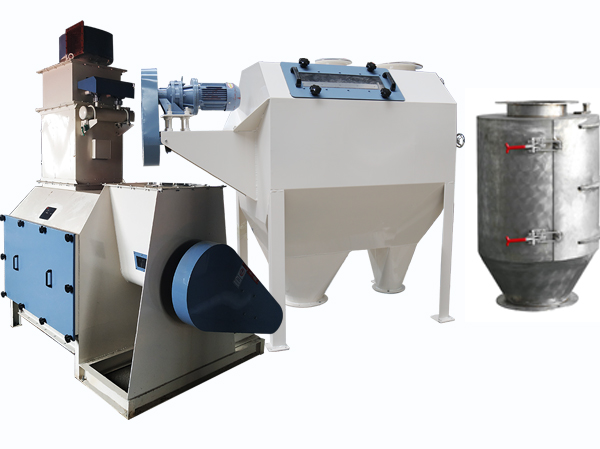
Raw Material Pre-cleaning
As the wood chips raw materials are mainly forest felled materials, woodland miscellaneous irrigation materials, etc., it is necessary to collect the raw materials at this stage and remove the large wood blocks and debris through the roller screen.
Transport sawdust or other kinds of biomass materials to your factory. Locate the plant near the source of raw materials, so that to minimize the transportation cost. As the wood sawdust arrived in the sawdust pellet machine plant, the moisture content should be tested.
The moisture content gives the proportion of evaporable water in the total weight of material. The sawdust with high moisture content should be stored separately from the low moisture content sawdust. The production of 1 ton pellets needs the about 7 bulk m³ sawdust with the moisture content around 50-55%.
The optimum moisture content of the sawdust is 10-15%. The sawdust with higher moisture content should be dried before entering the sawdust pellet machine while the lower one can skip the procedure.
Raw Material Crushing
The task at this stage is to further crush the wood chip raw material into small wood sawdust.Only wood chips that meet the size requirements can be directly fed into the hammer mill, or those that have passed the chipper and coarse crushing and require further fine powder. Due to the wide range of screen sizes on the hammer mill, it can produce particles of various sizes, so it is the most common choice for wood pellet manufacturers.
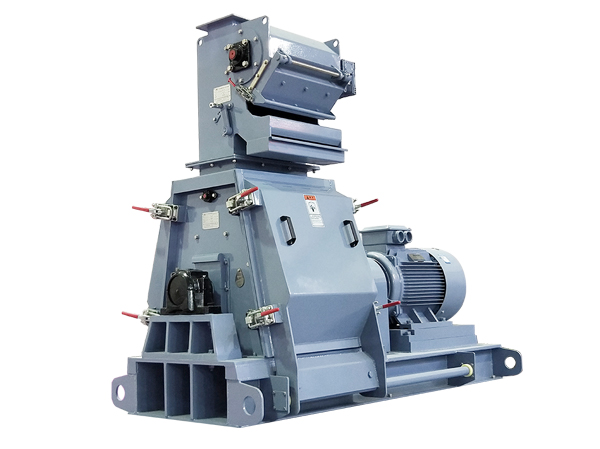
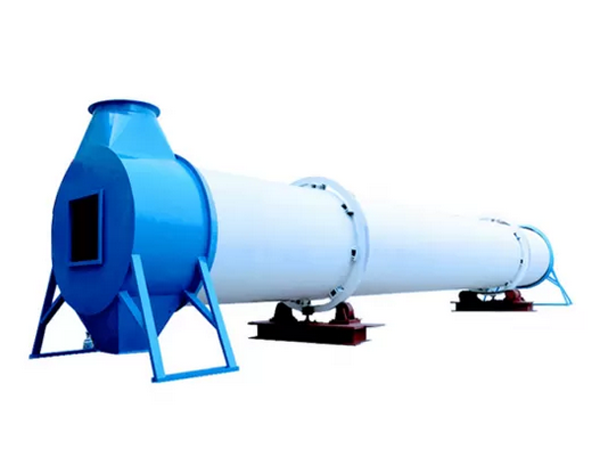
Drying system
For drying part, you can adjust the feeding speed, the rotating speed of the drying machine, and the inlet air temperature to adjust and to get the required moisture to make wood pellets. And the suitable moisture to make wood chip pellets is 15%-17% . ( About how to adjust, our engineer will train your labors) Different capacity, the diameter and length of the drying machine is different.
The wet sawdust should be dried before size reduction because the wet sawdust consume more power to be hammered than the dried one does. And also the wet sawdust may risk the screening by clogging or smearing the screen. Drying can be done by the wood sawdust drying machines.
Crushing system
The grinding section is meant to homogenize the sawdust to an even-size. In the piles and piles of sawdust there are might be wood lumps, dead knots, etc. which needed to be hammered so that they can pass the die holes of the sawdust pellet mill machines.
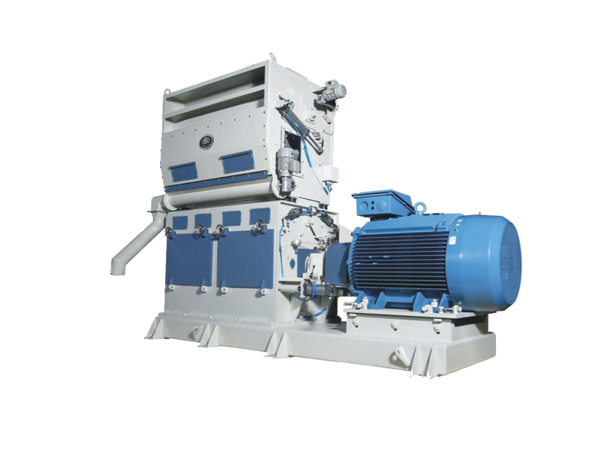
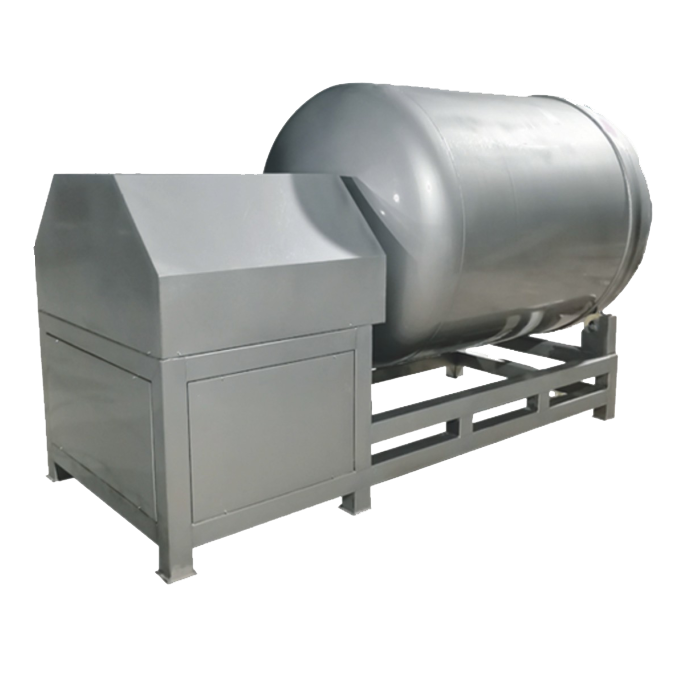
Raw Material Mixing
Whether producing single raw material pellets or mixed pellets, maintaining the consistency of raw materials is very important for pellet production plants. After the raw materials are grinded and dried, binder(vegetable oil, molasses, starch, gluten, dried lees, rapeseed cake, etc.) need to be added,so it is necessary to use a mixer machine. After mixing, the raw materials are mixed more fully and evenly, and then sent to the pellet making machine.
This is an optional section, only a few customers who use special processes will choose. If your raw materials contain enough natural lignin to be glued together,you do not need additives and can completely ignore this section.
Pelleting system
The wood chip pellet making machine is the heart of the wood pellet production line. The pellet machine is widely used for pelletizing wood, straw and other biomass energy. The output ranges from 1 to 10 tons / hour. The biomass wood pellet machine adopts Swedish bearings and Siemens motors, which can fully guarantee the wood pellet equipment capacity and stable operation.
When the sawdust goes into the pelletizing chamber of the sawdust pellet mill machine, the lignin of the sawdust will be heated up to 120-130 ℃ by the heat produced by the running sawdust pellet machine and by which the lignin will be plasticized and binds the particles together to help to mold the pellets. The sawdust pellets are molded by being pressed through the pellet dies of the sawdust pellet machines and then are cut off by the cutter with the desired length. During the pelletizing, the binder may be needed to improve the pellet strength and durability. Watch this video to see how a sawdust pellet mill works.
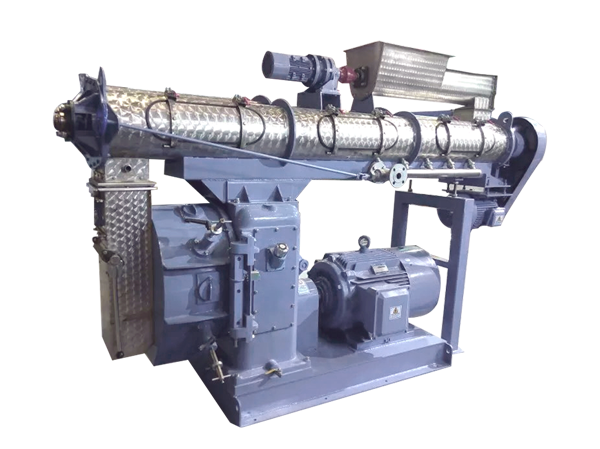
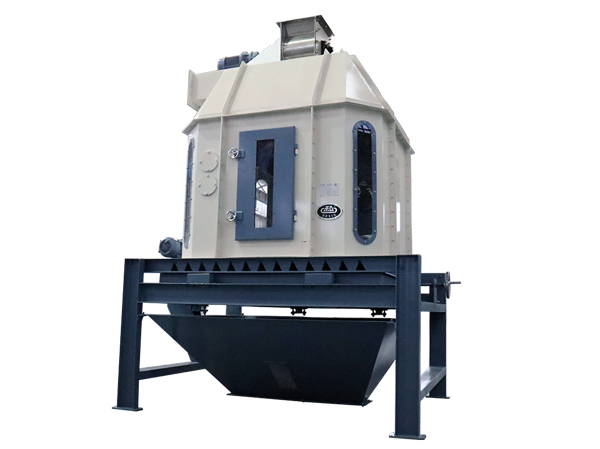
Cooling system
The temperature of the biomass wood chip pellets after granulation is as high as 80-98 degrees, the structure is relatively loose, and it is easy to break. It must pass through a counter-flow cooling system and be cooled to room temperature before entering the warehouse.
The moment when the pellets leave the sawdust pellet machines, they are hot and plastic. Then they need to be cooled down to become hard and rigid and to dry up so that the final moisture content after the cooler can be as low as 6% which may be increased up to 8 to 10 % by absorbing moisture from the surround air.
Packaging system
Before packaging, the pellets will be screened again for recycling the fines. And then the pellets will be packaged. For domestic users, the wood sawdust pellets are preferred to be packed into bags with the sizes of 12, 15, or 20 kg. While for exporting, the sawdust pellets are usually shipped in one tone bags or in bulk which are usually wrapped in plastic to keep the moisture out. Compare with the large bulks or bags, the small bags are better for the pellets because the pellet are subject to less abrasion during delivery.
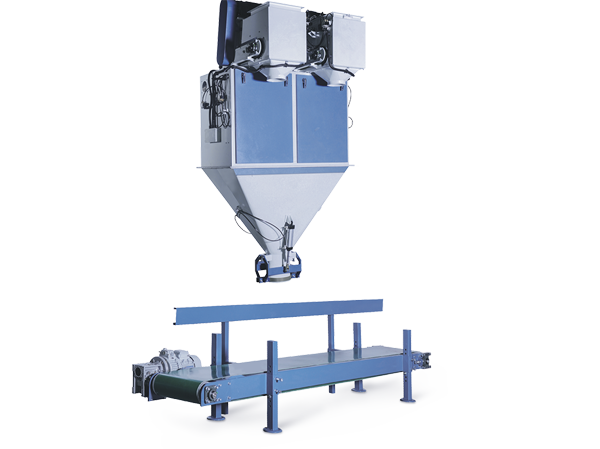
How to start a complete sawdust pellet production line?
- Raw materials
Which is the best choice for your pellet production, sawdust, wood chips, tree branches, straw, stalk, palm fiber? It is also necessary to consider overall quality of raw material such as, size, moisture, heat values, ashes, etc.
When it comes to raw material, we are talking about not only what kind of pellets you are producing, but also the equipments you need with your pellet plant, as different material need different equipments. It decides the construction of wood pellet plant and the quality of final sawdust pellet products, that is, your investment and your profits.
- Sawdust pellet quality
Quality is another factor affects your profitability when the market price is fixed. Superior quality will be your competitive advantage while bad sawdust pellet quality or a bad reputation for wood pellet quality will be lethal disadvantage. So quality sawdust pellet mill is the most important choice you are going to make. - Financing
Financing is very important for wood pellet plant construction and your profits . Generally, the investment and your sawdust biomass pellet production line size are in direct ratio.