Our solutions come in a modular design so you can customize them to match your production process. At ZHI we focus on solutions that pay off, whether it’s supplying the smallest spare part or serving as a long term partner. Complete Wood Pellet Production Line includes the following equipments, from the storage of raw materials to the packaging of the final pellets. Each section has professional equipment to work. Of course, according to the different needs, it may be the particularity of the raw materials or the limitations of the site. Our engineers will redesign the process, and the equipment used will be increased or decreased. Click each module below, you will see the specific equipment information.
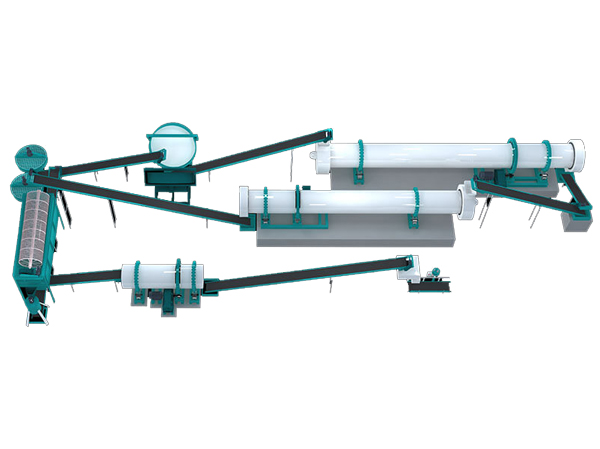
Wood pellet biomass production line
ZHI can provide the complete turnkey project biomass wood pellet production line, from design to install . Whether you want to produce wood pellet, sawdust pellet ,rice husk pellet, EFB pellet ,grass pellet or organic fertilizer pellet, the capacity is 1-100TPH can be choose. The main machine is wood chipper,wood crusher, drum dryer, wood pellet machine , cooling machine ,rotary sereener and others . Looking forward to your consultation !
The wood pellet production line is a high-efficiency, energy-saving and environmentally friendly biomass fuel production system. It handles and processes wood chips and converts them into wood pellet fuel, realizing the recycling of waste wood resources and environmental protection. The main equipment of wood production is wood pellet machine, wood chipper machine, wood hammer mill, rotary drum dryer, counter-flow cooler, packing machine, conveyors and electrical control equipment, etc. Our wood pellet plant establishments are staffed with qualified sales, engineering and service personnel and are well stocked with dies, parts and accessories. This ensures prompt, efficient processing of all customer service requirements.
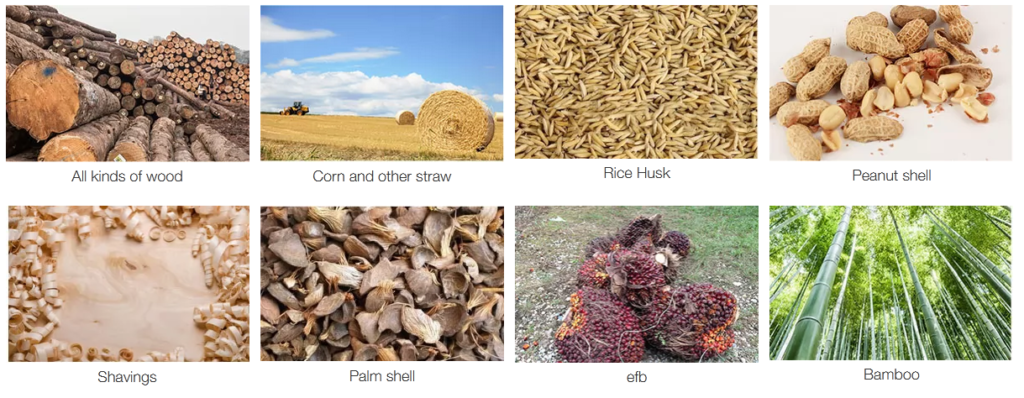
There are many types of wood waste, such as wood shavings, wood shavings, wooden blocks, wood chips, scraps, scraps, board scraps, branches, tree trunks, building templates, etc. We can process these waste wood materials that were previously considered useless and reuse them, which can effectively reduce the waste of wood resources and contribute to environmental protection.
Wood materials are a renewable biological resource and are one of the four major materials in the world today (steel, cement, wood, and plastic). Only wood is a green material and biological resource that can be renewable and recycled. At present, the recycling of waste wood scraps is mainly applied in the following areas:
- Waste wood can be used for papermaking. By crushing and processing materials into paper, not only can waste wood be reused, but it can also bring economic value. This is a very good way to solve the problem of waste wood, saving wood resources while protecting the surrounding environment.
- Using waste wood to manufacture wood-based panels. Such as particleboard, MDF, gypsum particleboard, cement particleboard, etc.
- Using waste wood to make handicrafts, wood is often turned into art by handicraft enthusiasts.
- Using waste wood to manufacture wood pellets, charcoal, wood vinegar, and wood gas.
Processing technology of wood pellet biomass production line
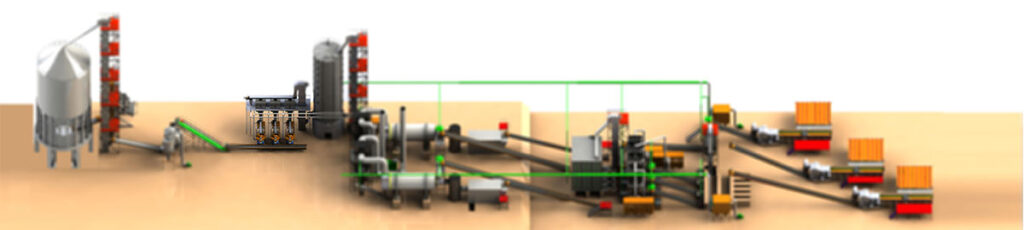
The wood pellet biomass production line is a mechanical equipment used to convert wood waste such as wood chips and sawdust into wood pellet fuel. It has the characteristics of high efficiency, energy saving, environmental protection and resource recycling, and plays an important role in the field of modern biomass fuel.
The working principle of the wood pellet biomass production line is to compress the raw wood chips into high-density pellet fuel through a compressor after crushing, screening and other processing processes. The entire production line includes multiple equipment, such as raw material processing systems, crushing equipment, drying equipment, pellet machines, cooling equipment, etc., which work together to complete the wood pellet biomass production process.
technological process:
- Wood powder raw materials (rice husks and peanut shells do not require a screening machine) are screened to remove impurities such as sand, stones, and iron blocks inside;
- The screened wood powder is transported by a conveyor belt to the hydraulic granulation material bin for buffering and homogenization. Automated connection reduces dust concentration, ensuring safety and cleanliness, and saving labor;
- Wood powder is fed through a variable frequency screw conveyor at the bottom of the warehouse to ensure continuous and stable feeding of the granulator, reduce wear, and achieve stable and efficient production;
- High temperature particles enter the cooling machine through the conveyor belt for cooling;
- The cooled particles enter the packaging machine for packaging.
Process advantages: equipped with hydraulic treatment chamber, automated connection, reducing manual labor; Sealed cache compartment, reducing dust concentration and minimizing dust storms; A hydraulic homogenization device is installed at the bottom of the warehouse to prevent material bridging and ensure stable feeding of the pellet machine.
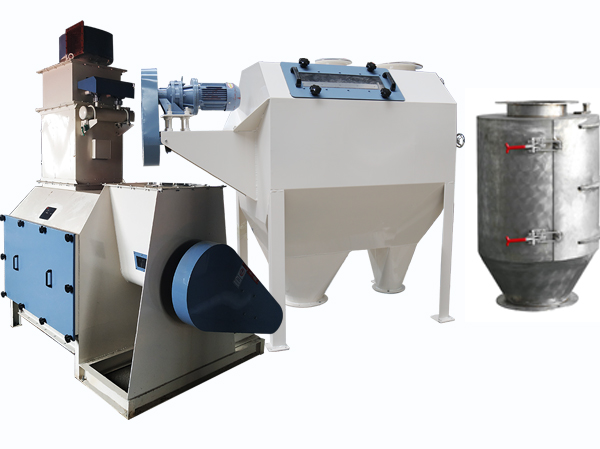
Raw Material Pre-cleaning
The first step in the wood pellet manufacturing process is the preparation of the wood waste raw materials, which includes selecting a materials suitable for this process, and its filtration, storage, and protection.
The raw materials used are sawdust, wood wastes, agricultural and forestry residues, etc. Filtration is done to remove unwanted materials like stone, metal, etc. The materials is stored in such a manner as to prevent contamination by impurities and moisture.
Drying
In cases where there are different types of biomass wood materials, a blending process is used to achieve consistency. The moisture content in biomass wood waste can be considerably high, and hence needs to be reduced to 10 to 15%. Drying increases the efficiency of wood, and it produces almost no smoke on combustion.However, the wood materials should not be over-dried, as a small amount of moisture helps in binding the biomass wood particles. The drying process is the most energy-intensive process and accounts for about 70% of the total energy used in the wood pelletisation process.
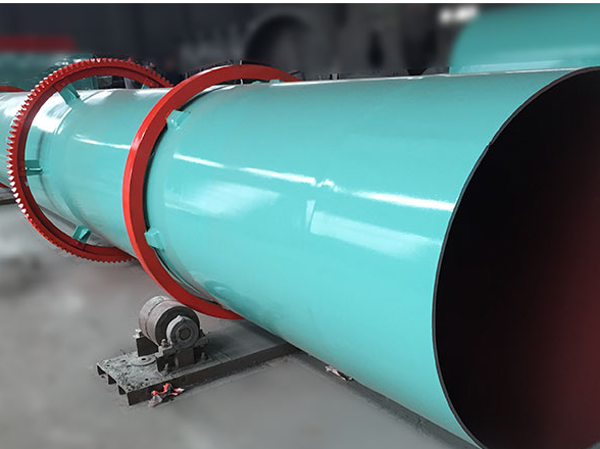
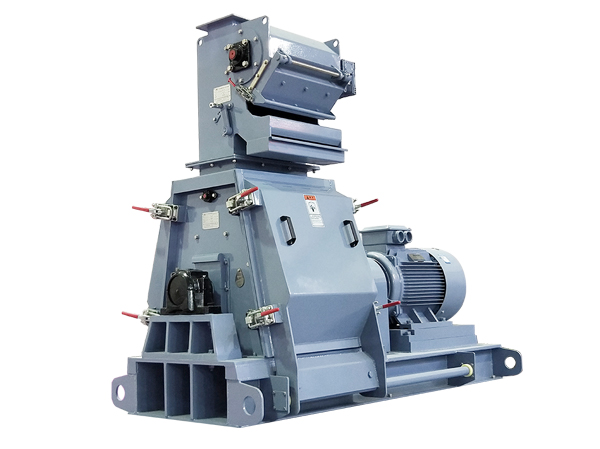
Chipping & Crushing
The wood materials is reduced to small particles of not more than 3 mm before it is fed into the wood pellet mill machine. Size reduction is done by grinding, using a wood hammer mill equipped with a screen of size 3.2 to 6.4 mm. If the wood feedstock is quite large, it is put through a wood chipper machine before grinding.
Pelleting
The next and the most important step is pelletizing where the wood is compressed against a heated metal plate (known as a ring die) using a roller. The die has holes of fixed diameter through which the wood is passed under high pressure. Due to the high pressure, frictional forces increase, leading to a considerable rise in temperature. The high temperature causes the lignin and resins present in the biomass to soften, which acts as a binding agent between the biomass wood fibres. In this way, the biomass wood particles fuse to form pellets. During wood pellet line pelleting process, a large fraction of the process energy is used to make the biomass flow into the inlets of the press channels. Binders or lubricants may be added in some cases to produce higher quality pellets. Binders increase pellet density and durability. Wood contains natural resins which act as a binder. Similarly, sawdust contains lignin which holds the pellet together.
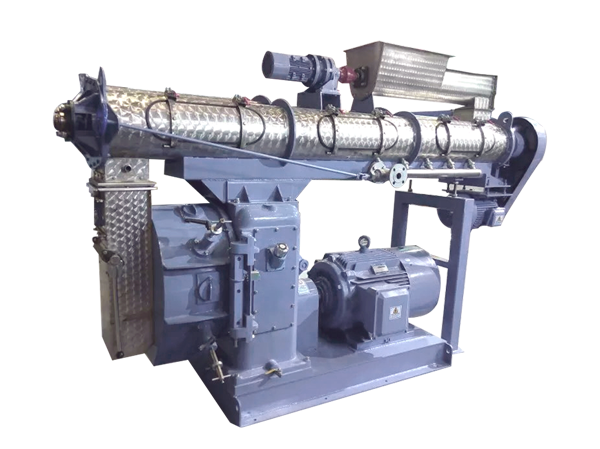
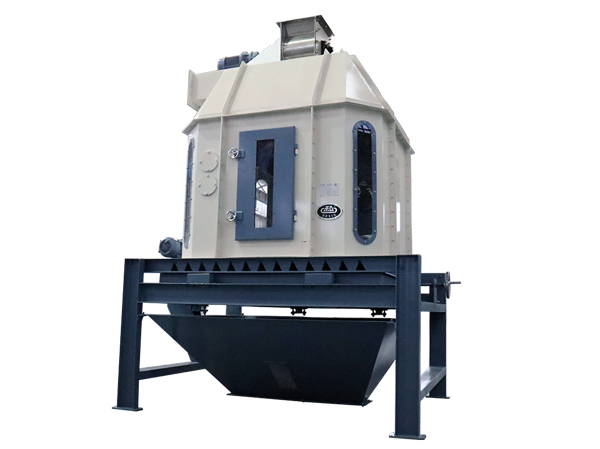
Cooling & Screening & Bagging
Excess heat is produced by the friction generated in the die. Thus, the pellets produced are very soft and hot (about 70 to 90℃). They need to be cooled and dried before they are stored or packaged. After they have cooled, they are packaged in bags or stored in bulk. Wood pellets can be stored indefinitely, but they must be kept dry to prevent deterioration.
Packaging system
Before packaging, the pellets will be screened again for recycling the fines. And then the pellets will be packaged. For domestic users, the wood sawdust pellets are preferred to be packed into bags with the sizes of 12, 15, or 20 kg. While for exporting, the sawdust pellets are usually shipped in one tone bags or in bulk which are usually wrapped in plastic to keep the moisture out. Compare with the large bulks or bags, the small bags are better for the pellets because the pellet are subject to less abrasion during delivery.
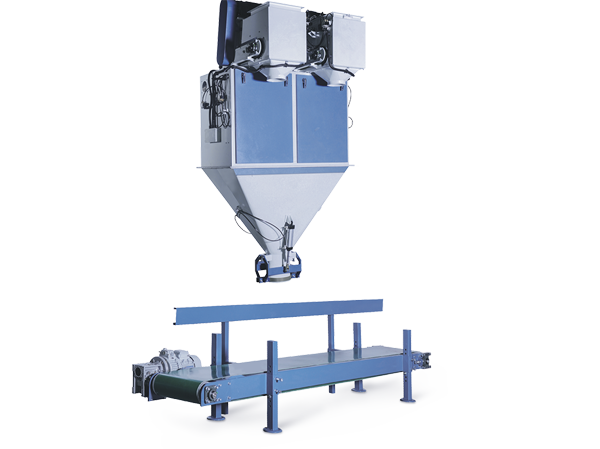
Because the wood pellet machine has requirements on the size of the raw materials entering the machine, for example, to produce wood pellets with a diameter of 8mm, the size of the raw materials needs to be no larger than 8mm. Therefore, if the size of the raw materials is too large, a wood chipper and a crusher are needed to slice the raw materials and process them into fine powder. , so that the raw material size meets the requirements of the wood pellet machine.
Similarly, the wood pellet machine also has requirements for the moisture content of the raw materials. The moisture content of the raw materials is required to be 10~15%. If the moisture content of all raw materials is too high, it needs to be naturally dried to a moisture content of 10~15%, or a drum dryer can be used to dry the moisture content of the raw materials. Moisture is dried.
When wood pellets are just produced, the temperature can reach 80~90 degrees Celsius. Under such circumstances, there is no way to package them immediately. All the pellets need to be cooled in a counterflow cooler, and the temperature can be lowered to room temperature before entering the vibrating screen for processing. Screening, and finally packaging machine.