Grass particles is one of the main products of biomass production line, grass particles as a kind of biomass particles, has a wide range of applications and unique advantages, not only the market demand is huge, and compared with other particles, the price is much higher.
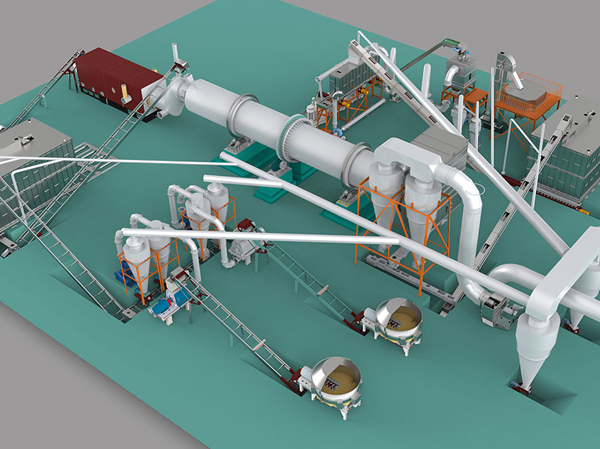
Grass pellet biomass production line
Advantages of Grass Granules
- Many raw materials can be made into pellets, and using grass pellets as fuel has always been a recognized method in Europe. Not only fuel, but also grass pellets as feed are a great choice.
- Using grass pellets as biofuels is economical, energy-saving, environmentally friendly, and sustainable. As a clean fuel, more and more people prefer to choose grass pellets because the raw materials are cheap and easy to obtain.
- In addition, grass pills can be used as feed for many animals such as horses and cows. As feed, grass pills can replace some dry hay and are rich in nutrients.
Simple process
The production of grass pellets, as a low tech and small-scale renewable energy system, has great potential for local production, processing, and trading, while also having a positive impact on agricultural and pastoral areas. Easy access to raw materials and convenient operation of small granulators have become the choice of more people.
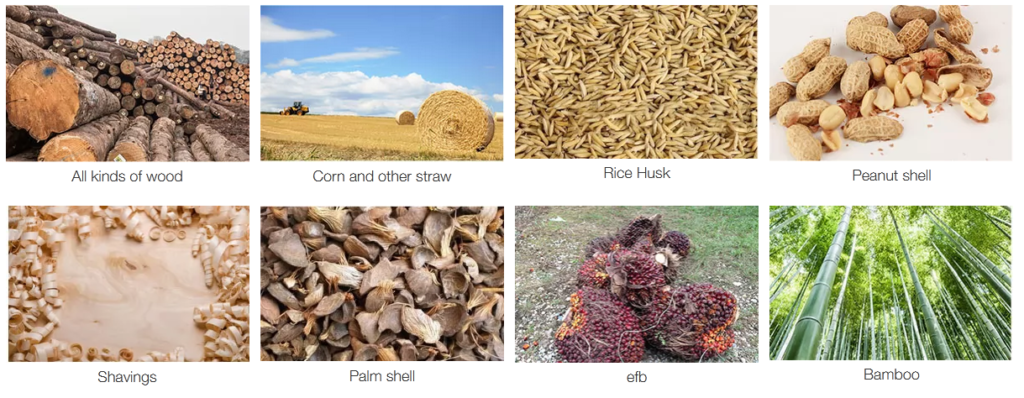
Precautions for processing grass pellet biomass:
- Before operating the machine, the operator should carefully read the user manual and familiarize themselves with the various process flows of the equipment.
- During the production process, it is necessary to strictly follow the regulations and sequence of operations, and carry out installation operations according to their requirements.
- The host equipment needs to be installed and fixed on a horizontal cement floor, reinforced with tight screws.
- Smoking and open flames are strictly prohibited in the production site.
- After each startup, it is necessary to idle for a few minutes to confirm that the pressing wheel is in contact with the mold before feeding.
- It is strictly prohibited to add hard debris such as stones and metals to the feeding device. Before granulation, iron removal should be done to avoid damaging the granulation chamber.
- During the operation of the equipment, it is strictly prohibited to use hands or other tools to remove materials to avoid danger.
- If there is any abnormal noise during the production process, the power should be immediately cut off, and the abnormal situation should be checked and dealt with before starting up to continue production.
- Before stopping the machine, first stop the auxiliary feeding, then add oil, and wait until the mold hole is filled with oil and the granulation room is empty of oil before stopping the machine. The purpose of adding oil is to make it easier to discharge during the next production.
Correctly operating the pellet machine according to requirements and paying attention to relevant matters as required can not only improve the output and operational performance of the equipment, but also extend its service life.
Process flow of grass pellet biomass production line
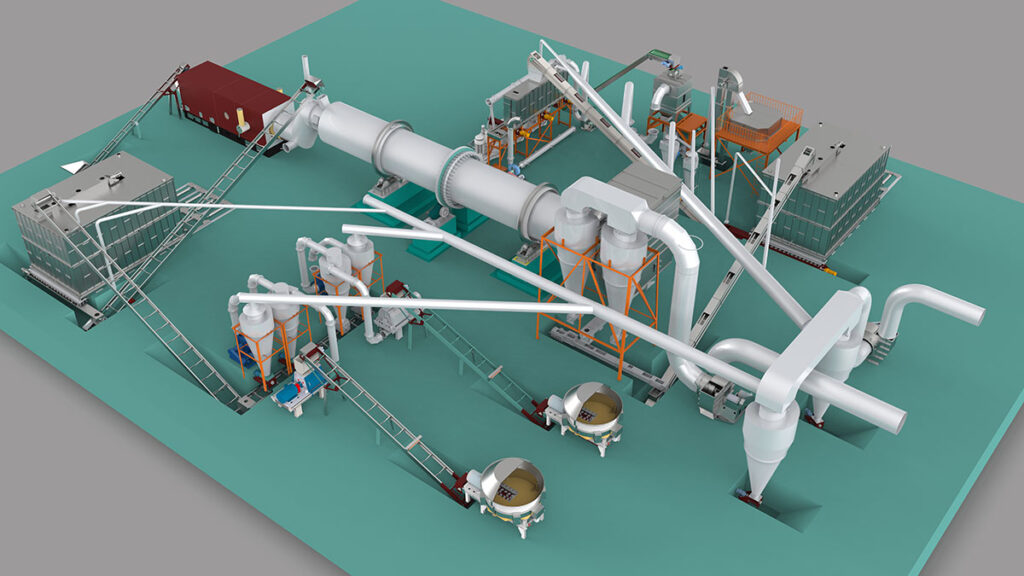
Process flow:
- Rotary grinding: Use rotary shredder to crush the straw to less than 8mm;
- Drying: The crushed material is dried by the tumble dryer;
- Granulation: The dried material enters the bin and enters the granulation mechanism through the spiral dragon.
- Cooling: high temperature particles through the conveyor belt into the cooling machine cooling;
- Packaging: cooled particles into the packaging machine packaging.
Process advantages: a wide range of applicable raw materials, good particle molding effect, government support.
The production line equipment of straw making granule is composed
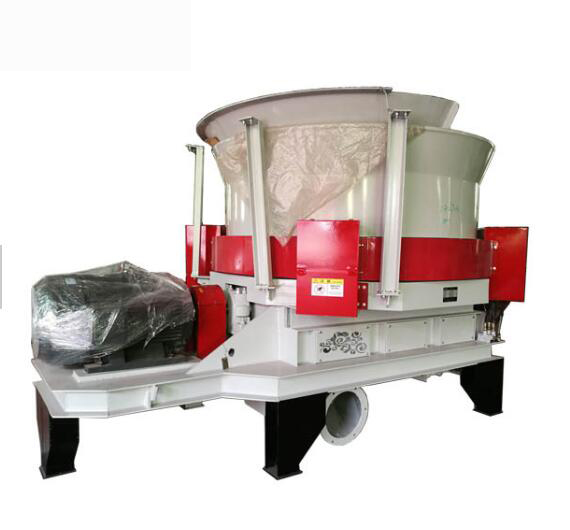
Straw rotary cutting machine
The rotary crusher has a wide crushing range and can be used for crushing fibrous materials such as thatch, corn stalks, sorghum stalks, etc. Widely used in various fields such as crop straw crushing and processing, straw scale pellet fuel, biomass power generation, etc., it is an ideal processing equipment for charcoal plants, straw coal plants, biomass pellet processing plants, etc.
The S rotary cutting and crushing integrated machine can crush various crop straw such as corn straw, wheat straw, rice straw, clover, wolfberry, etc. It can also crush wooden boards or strips with a size of less than 800x100x10mm (thickness), as well as board skins, etc. For bundled materials, they can be crushed directly into the drum without breaking the bundle.
High efficiency mill
High efficiency crusher is a company developed for the production of biomass fuel, our high efficiency crusher can be widely used in biomass energy and feed processing industry. This equipment can break wood chips, shavings, spun wheat straw, corn straw and other fiber materials, but also can break corn and other granular feed raw materials. According to the requirements of customers in different industries, the screen with different apertures is selected to ensure the size of the finished product after crushing.
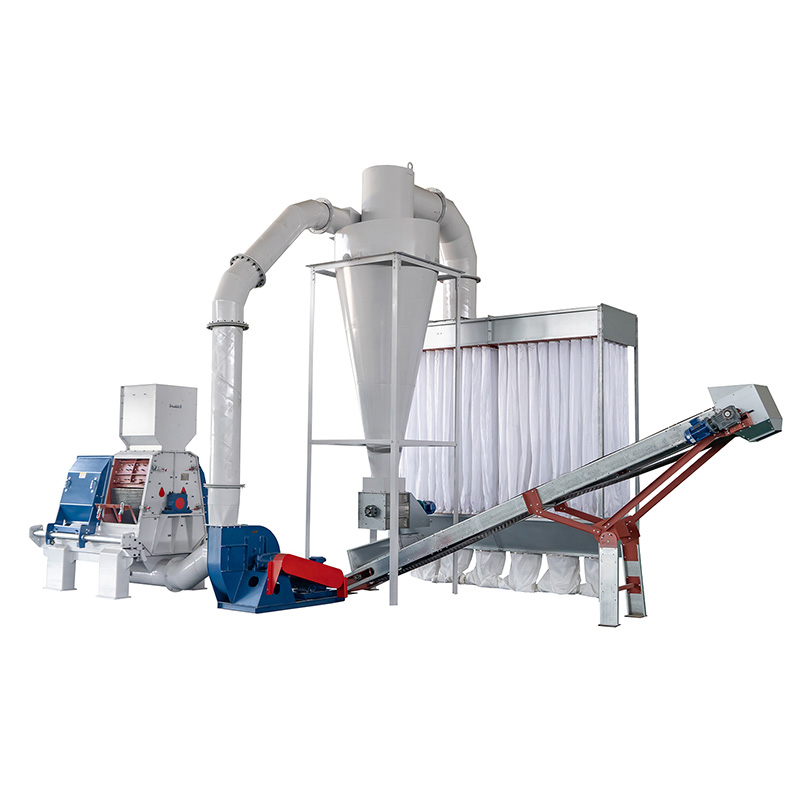
1, a set of crusher including crusher main engine, fan, Shakron, fan off, bag dust removal, etc.
2, the main part of the grinder rotor, before assembly through dynamic balance check, to ensure the stability of the machine during operation.
- The base assembly platform of the mill motor and the assembly platform of the rotor spindle are simultaneously processed by a large CNC machine tool to ensure horizontal accuracy, thus ensuring the smooth operation of the machine.
4, the wearing parts of the crusher hammer, the material is manganese steel, two corners of which are welded wear-resistant alloy material, improve the service life of the hammer, reduce the cost.
- The operating doors on both sides of the crusher can be translated and opened to facilitate maintenance and replacement of the screen.
6, the crusher screen is composed of two pieces, after installation, the overall discharge Angle is close to 360 degrees, the discharge area is large, and the production efficiency is high.
7, the crusher can be configured with two shakron according to customer requirements, this installation mode can make the dust containing gas through the two-stage shakron filter, into the bag dust, so that the filter is more full.
8, our crusher has a variety of different output models, single output from 1ton to 8ton, can meet a variety of needs.
9, the main factor affecting the crushing efficiency of the mill is the material moisture, the drier the material, the smaller the size of the finished product
For more detailed information about the efficient crusher, you can call the official website directly, and the switchboard customer service will assign a business manager for you to follow up.
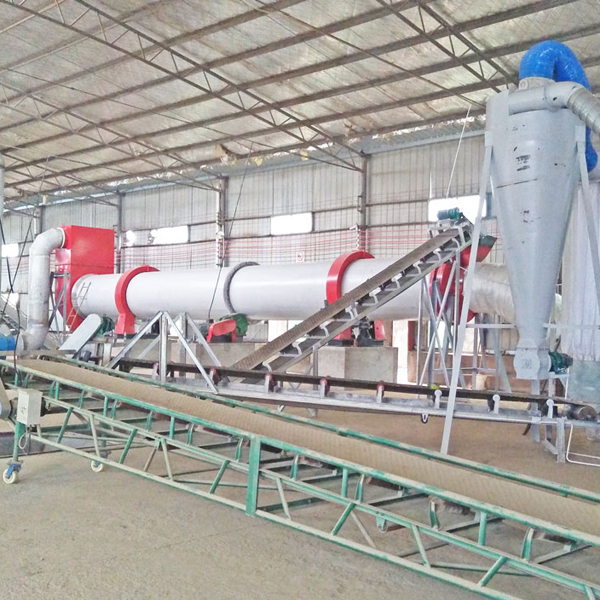
Tumble dryer
Drum dryer is mainly used for drying wet materials such as powders, granules, and small pieces, and is widely used in industries such as energy, fertilizers, chemicals, and pharmaceuticals. This product has the advantages of high drying capacity, stable operation, low energy consumption, easy operation, and high output.
In the biomass granulation process, if the moisture content of the raw materials does not meet the granulation requirements, drying is required. Drum dryer is a widely used drying equipment that can dry various materials such as sawdust, straw, rice, etc. The device is easy to operate and runs stably.
Hot air enters the dryer cylinder from the hot air stove, and materials enter from the feeding port. In the dryer, the materials are lifted by the lifting plate, and then the hot air comes into contact with the materials, taking away the moisture in the materials. The material comes out from the discharge port, and the hot air is drawn away from the upper end. The movement of materials mainly relies on the pushing effect of the lifting plate.
A drum dryer cannot work on its own and usually needs to be equipped with a heat source (hot air stove), fan, shaker, and sometimes dust removal equipment.
The drum dryer itself consists of a cylinder body, a feeding port, a discharging port, a ring gear, and an aperture.
Common drying materials: sawdust, straw, rice husks, peanut shells, etc.
Centrifugal high efficiency granulator
Biomass pellet machine is a kind of pellet equipment commonly used in the biomass energy industry, which is a new type of fuel molding machinery that compels biomass raw materials such as branches and stalks into rod particles after crushing to replace coal carbon. The vertical centrifugal high efficiency ring die granulator produced by our company combines the advantages of traditional horizontal ring die and flat die granulator, especially suitable for biomass granulation.
Common raw material
Wood: pine, poplar, fir, branches, bark, wood chips, shavings, etc
Straw: corn straw, wheat straw, straw, rice husk, peanut shell, cotton stalk, etc
Waste: building templates, furniture scraps, wooden pallets, municipal waste, pharmaceutical residue, mushroom residue, sludge, etc
In addition to the above common biomass raw materials, our company has specially developed a suitable pellet machine for activated carbon materials. If you need, please call our official website, we will assign professional sales staff to serve you.
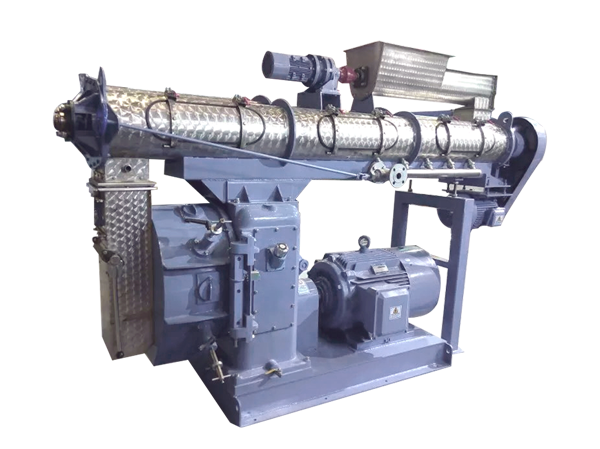
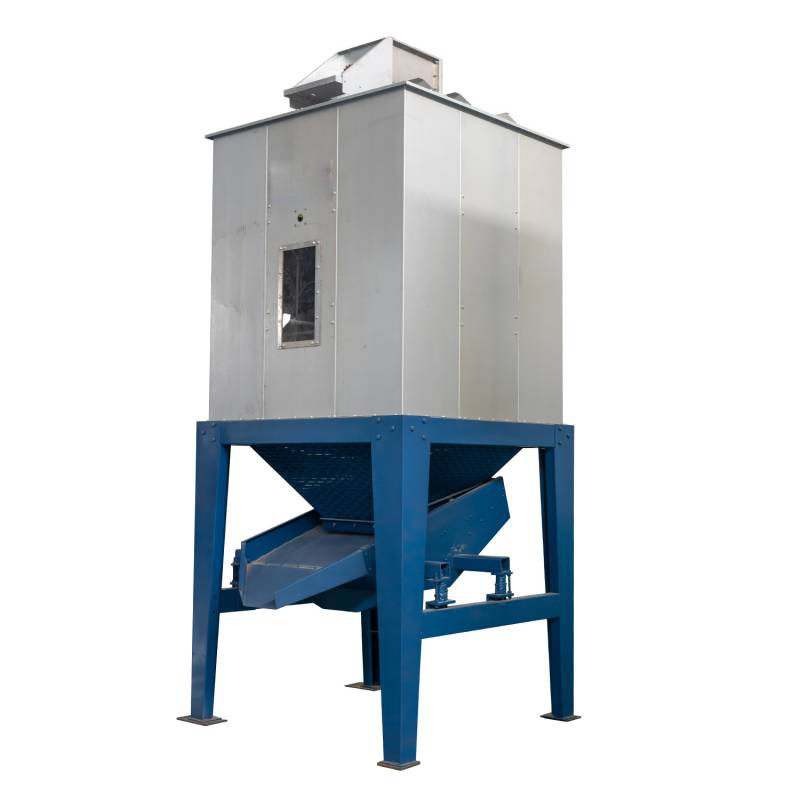
Cooling machine
Main components: upper shell, intermediate compartment, cooling network, vibrating screen, frame
The components include observation window, bag filter, fan, etc.
This equipment is mainly used for cooling high-temperature particles after granulation, reducing the temperature and humidity of the particles, thereby facilitating transportation, storage, and preservation.
After the granules come out of the granulator, the temperature can reach nearly 70 degrees. High temperature granules are very prone to breakage and the generation of water vapor,
But the cooled particles have a temperature close to atmospheric temperature and can be directly packaged.
So it is an essential part in large-scale production lines, facilitating the entry of particles into the next section (packaging section).
Compared to traditional cooling machines, modern cooling machines use thick galvanized steel plates with high density,
Not easily deformed and corroded, with a long service life.
- The machine adopts a modular structural installation, which is convenient for transportation and on-site assembly by customers;
- Adopting a unique vibration mechanism for material discharge, the operation is smooth and the discharge is smooth
- Set up a level indicator to monitor the real-time position of materials in the silo, with a high degree of automation
- By utilizing the principle of counterflow cooling, the particles are cooled thoroughly and uniformly.
Biological particle packaging equipment
Small bag packaging machine
Small bag packaging can be used to package granules or powders; Automatic weighing, manually assisted sealing, packaging weighing range of 10-40 kilograms per bag; Approximately 200 bags can be packed per hour.
Ton bag packaging machine
The ton bag packaging machine is a large-scale weighing packaging equipment used for ton bag packaging materials. It is a multi-purpose packaging machine that integrates electronic weighing, automatic bag removal, and dust removal. It has a high degree of automation, high packaging degree, adjustable packaging speed, and a hydraulic lifting system that is particularly easy to handle ton bag packaging. It is also very convenient for the processing of subsequent processes. It is a commonly used equipment in the packaging process of biomass pellet production.
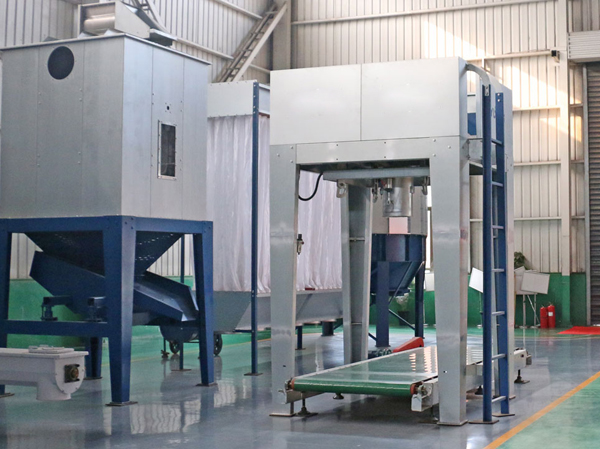
Characteristics of ton charter flight:
- The ton bag packaging machine is tailor-made and designed according to the characteristics of different materials and the requirements of different manufacturers. Equipment technology, durable and with few vulnerable parts.
The feeding and packaging of the ton bag packaging machine have no speed regulation, the equipment performance is stable, the packaging degree is high, and the speed is fast. - Programmable electronic control system with highly reliable control process.
- Dust prevention and dust removal design to reduce dust pollution in the working environment.
- The weighing system is an electronic platform scale measurement system that uses panel digital calibration and parameter setting. It has functions such as weight accumulation display, automatic peeling, automatic zero calibration, and automatic drop correction. It has high sensitivity and strong anti-interference ability.
- The instrument is equipped with a communication interface, which facilitates online networking and enables real-time monitoring and networked management of the packaging machine.