Fully continuous pyrolysis plant can recycle some solid waste to renewable energy. With the development of maturity of the pyrolysis technology, fully continuous pyrolysis plant is increasingly welcomed by various countries because of its advantages of high environmental protection, high degree of automation and high oil yield. The following is the detailed description of the fully continuous pyrolysis plant

Raw materials suitable forfully continuous pyrolysis plant
The raw materials which can be treated by the fully continuous pyrolysis plant include waste tires, waste plastics, waste rubber, oil sludge and so on. Generally speaking, the main raw materials to be treated are waste tires, waste plastics and oil sludge. Here’s the list of oil yield about common waste tires and plastics. Oil sludge needs to see the specific composition ratio to determine the oil yield.
Main components of fully continuous pyrolysis plant Fully continuous pyrolysis plant mainly includes accurate calculated pyrolysis system, PLC control system, condensing system, desulfurization tower, unique slagging system, etc.
Final products and applications from fully continuous pyrolysis plant
If your raw materials are waste tyres or waste plastics, you mainly get fuel oil and carbon black which have widely uses in our daily life.
- Fuel oil
According to use, fuel oil can be divided into marine fuel oil, furnace fuel oil and other fuel oils. The fuel oil obtained from fully continuous pyrolysis plant can be widely used in marine boiler fuels, furnace fuels, metallurgical furnaces, and other industrial furnace fuels, such as used in steel factory, cement factory, glass factory, etc.
- Carbon black
Carbon black is mainly used for pressure ball combustion and refined milling. The refined flour can be used for new tires, rubber soles and various pigments.
The oil yield of common waste tires and plastics obtained from fully continuous pyrolysis plant
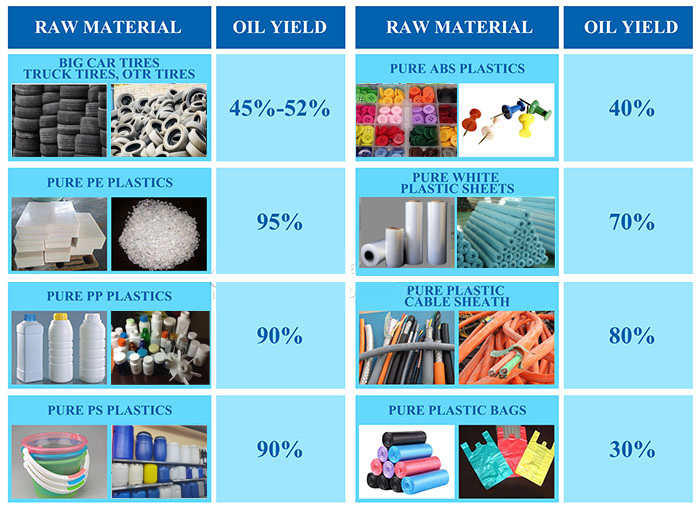
The main workflow of fully continuous pyrolysis plant
- Collect enough waste tires or waste plastics.
- The collected waste tires were broken into small pieces of 2-3 cm by a tire shredder. If your raw material is waste plastics, they needed be broken into small pieces by plastic crusher.
- Feed the raw material crumbs into the pyrolysis reactor through a sealed screw pusher .
- Heat the pyrolysis reactor, when the temperature reaches a certain level, oil gas will be cracked.
- Cracked oil gas entering the condensing system will liquefy into heavy oil and fall into the oil tank.
- Desulphurization and denitrification of tail gas are carried out and pollution-free gases are finally discharged.
7.The carbon black obtained in pyrolysis reactor is discharged outside the furnace through a sealed screw conveyor.
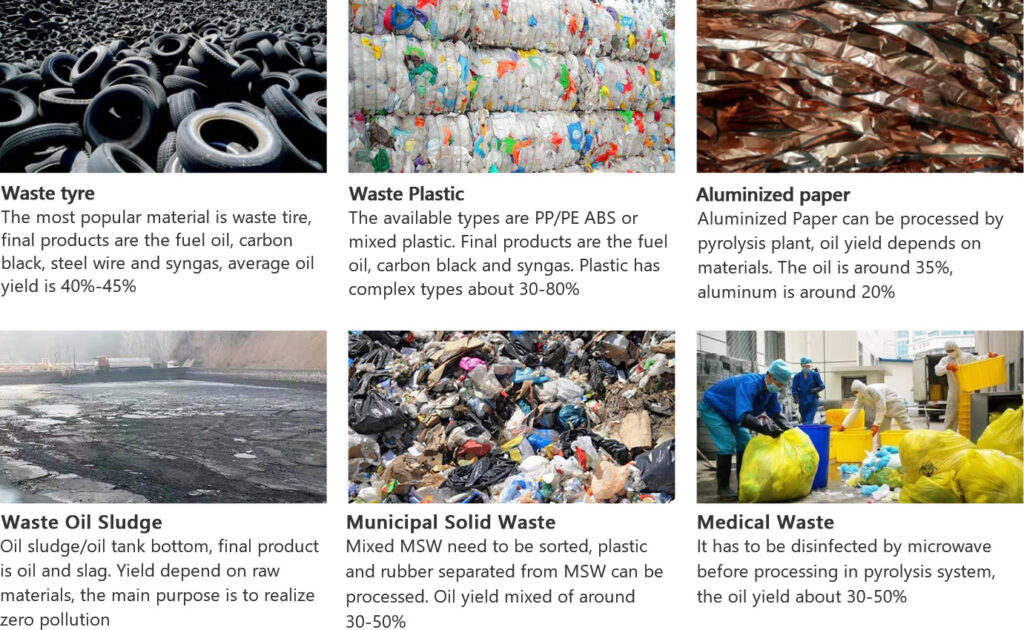
Final Product | Usage |
---|---|
Pyrolysis oil (40-55%) | 1.Can be reprocessed by oil distillation machine to extract diesel if the customers want to sell it at a better price. 2.The diesel can be used as fuel oil to many large types of machinery 3.Can be recycled to the furnace for heating the reactor 4.Can be sold directly, widely used in ceramic factory, cement factory, steel factory and so on 5.Can be used directly in the heavy oil generator to get electricity |
Carbon black (30-35%) | 1.Can be reprocessed through carbon black grinding plant, such as use in rubber industry , black dye, paint 2.Used in tire manufacturing, cables, conveyor belts, soles and other rubber and plastic products 3.To make briquette and construction brick 4.Sell directly |
Steel wires from waste tire(10%-15%) | 1.Sell directly on the market 2.Recycle them in steel factories to make steel bars |
Combustible gas(8%-10%) | 1.Can be reused to supply heat for the pyrolysis reactor 2.Can generator to power electricity 3. Compressed into liquid gas |
Main equipment of continuous pyrolysis plant
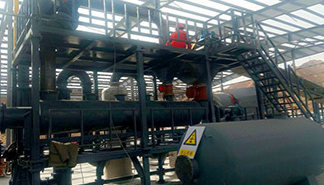
pretreatment
Waste tyre plastic through the steel wire drawing machine to pull out the steel wire in the waste tyre, and then put the tyre into the tyre crusher. After the treatment of the tyre crusher, the tyres are processed into 3-5 cm pieces.
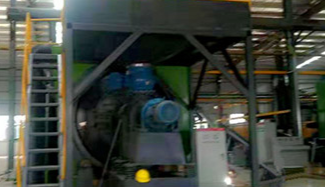
Feeding
Shredded tyres plastic are fed into the reaction system by an auto-feeder. The entire feeding process is sealed. Continuous waste tyre pyrolysis plant using PLC control system, with high degree of automation, feeding no longer need manual operation.
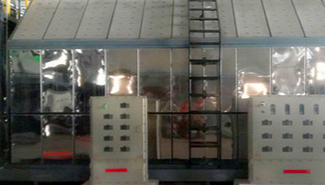
Continuous pyrolysis
The pyrolysis process is controlled by PLC, PLC system accurately calculates the reaction time which can ensure that Shredded tyres is fully cracked.
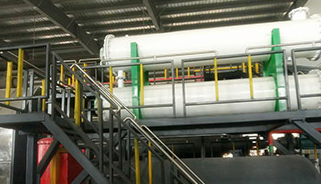
Cooling
The pyrolyzed oil gas passes through the circulating water cooling system and becomes liquid oil.
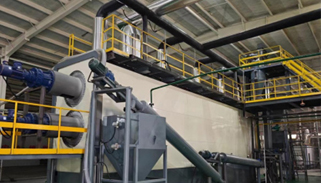
Oil product collection
Liquid oil is collected into the tank. No fireworks around the oil tank.
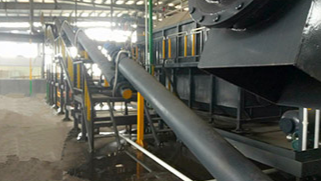
Discharge carbon black
After the reaction, carbon black will be automatically discharged from the other end by a unique slag discharge system.
Technical parameters of fully continuous pyrolysis plant
No. | Item | Specifications | ||||||
1 | Model | ZY-10 | ZY-20 | ZY-30 | ZY-50 | ZY-60 | ZY-80 | ZY-100 |
2 | Cpacity | 10T/D | 20T/D | 30T/D | 50T/D | 60T/D | 80T/D | 100T/D |
3 | Power | 35Kw | 50Kw | 65Kw | 80Kw | 90Kw | 105Kw | 120Kw |
4 | Working type | Continuous | ||||||
5 | Reactor deisgn | Mutiple reactors (The quantity and size depends on the raw material condition) | ||||||
6 | Rotating | Internal rotating | ||||||
7 | Cooling system | Recycled waster cooling | ||||||
8 | Reactor material | Q245R/Q345R boiler plate | ||||||
9 | Heating method | Indireact hot air heating | ||||||
10 | Heating fuel | Fuel oil/gas | ||||||
11 | Feedstock | Waste tire/plastic/rubber | ||||||
12 | Output | Fuel oil, carbon black |
Fully-continuous Pyrolysis System
1 Feeding size shall smaller than 10mm, Tire need to be shredded before feeding to pyrolysis, all steel wire shall be removed in advance
2 Fully-continuous system can run for 24 hours a day uninterrupted feeding,slaging,heating and there is no need to cool down the reactor before the second furnace
3 Its 310S stainless steel reactor is stable and not rotary, which makes the temperature rise 600-800 degree and pyrolysis react quickly. This special design makes the whole pyrolysis process much more efficient and the energy saving
4 Realize” discontinued feeding in minutes, seconds automatic slag discharge, continuous oil production day and night”
5 The fully-continuous high temperature of 600-800degree is very beneficial to the plastic pyrolysis wax oil, because the wax oil will block the pipe
Semi-continuous Pyrolysis System
1 Feeding size shall smaller than 50mm, which the shredder machine is required
2 Equipped with auto feeder spiral feeding system, must be sealed under the reactor 300-350degree condition. First feeding 8-10tons to pyrolysis reactor , then feeding next furnace auto discharging, stop 3-4h in the middle! Two furnace one day,high temperature feeding and slaging, automatic sorting and packing. The whole process will cost 20-22hours
3 From Feeding to Discharging, the whole process is sealed, operation environment is clean
4 Equipped with water cooling discharging, no ash flying, high efficiency. Discharging carbon black at high temperature is available, loading and discharging in 300-350 degree, no need to wait long time cooling of reactor
5 Equipped with carbon black and steel wire separator, which can separate the small steel in the tyre from the carbon black
6 When the raw material enter the reactor, the reaction immediately produce waste gas,which is directly used for heating, so its can save energy and less labor
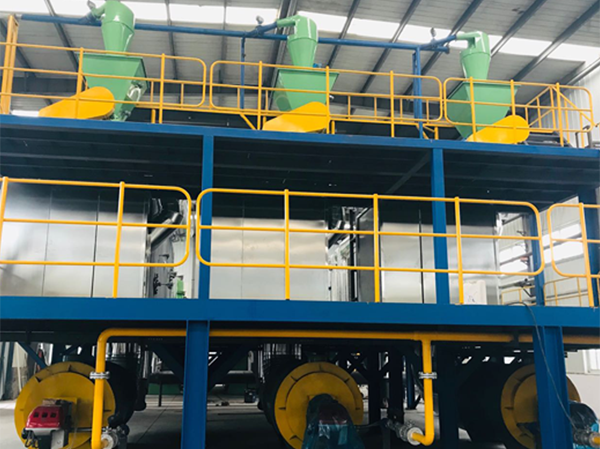
Fully Continuous Waste Plastic Pyrolysis plant
Fully continuous waste tyre to fuel oil recycling plant is a kind of high efficiency pyrolysis plant developed by Doing Group on the basis of intermittent pyrolysis plant(batch pyrolysis plant). In order to better meet the needs of customers, the fully continuous waste tyre to fuel oil recycling plant adopts PLC control system, can continuously feed, continuously discharge slag, is a continuous operation of pyrolysis production line. Both in terms of operating costs and efficiency to meet the requirements of customers.
The final products of fully continuous waste tyre to fuel oil recycling plant can be used in all aspects of life:
- Pyrolysis oil: mainly used in steel mills, boiler heating, heavy oil power generation, cement plants, etc. A further application is that it can be refined into diesel fuel through waste oil distillation plant.
- Carbon black: mainly used for pressing ball combustion and refined grinding. Among them refined grinding powder can be used to manufacture new tires, rubber soles, pigments and so on.
- Steel wire: sold as scrap or remelting.
Unique advantage of fully continuous waste tyre to fuel oil recycling plant:
- Accurate calculation system can ensure that the waste tyre is fully cracked to improve the oil yield. And the pyrolysis reactors and condensors of continuous waste tyre pyrolysis recycling plant are well designed to achieve the high oil yield.
- Continuous feeding, continuous slag discharge, having very high production efficiency.
- PLC control system can save manpower and achieve the intelligent control of the whole continuous tyre pyrolysis process.
- Single plant has large processing capacity and takes up less space.
- It is equipped with mutiple stages of environment protection devices to improve the environmental protection standard. It can meet different countries’ EIA standards, even EU countries.
Automatic continuous waste Tyre pyrolysis machine
The whole fully automatic continuous waste tyre pyrolysis machine composite by 13 parts, those are reactor ,driving device ,vertical catalytic chamber, vertical condenser, oil and water separator, horizontal condenser ,heavy oil tank ,light oil tank , anti-back fire device, vacuum system , dedusting device, draft fan, chimney.Reactor is one of the most important parts. The material and welding technology of reactor will have a direct impact on safety and durable life. In order to guarantee the quality of reactor, we use auto welder .The welding seam will get X-ray detection and heating treatment.Condensers adopt water cooling way and the inner cooling tube are made of seamless steel pipe ,the diameter is 48mm.the heat exchanging area is about 13 square meter ,the total heat exchanging area is 40 square meter to get the best temperature for oil gas liquefied.
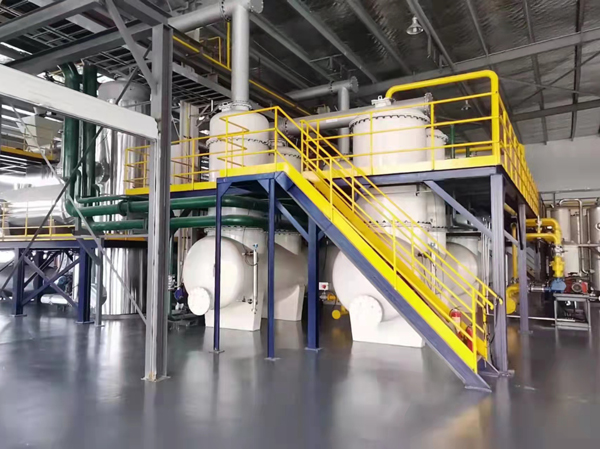
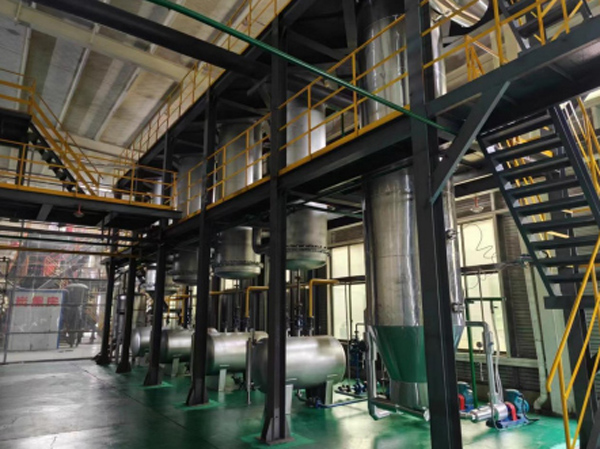
Continuous Oil Sludge Pyrolysis Plant
Oil sludge is a kind of hazardous waste produced in industrial production, which contains much oil and a few impurities such as wax, asphaltene and colloid. Therefore, the oil sludge has a high recovery value. The continuous oil sludge pyrolysis plant can recycle and treat the oil sludge to reduce the environmental pollution brought by the oil sludge, in addition, the oil obtained from the oil sludge can also bring economic benefits.
Continuous oil sludge pyrolysis plant manufactured adopts the principle of pyrolysis, which can pyrolysis the oil sludge, chemical sludge, residue and other wastes at high temperature to obtain fuel oil. Continuous oil sludge pyrolysis plant is a completely closed operation of the system. Its degree of automation control is relatively high. Feeding and discharge slag do not need manual operation. Most operations are mechanical automatic execution.
The main components of continuous oil sludge pyrolysis plant include continuous feeder, continuous rotary pyrolysis reactor, continuous slag discharge, continuous heat exchanger, continuous dry gas recovery unit, continuous flue gas purification discharge unit and continuous automatic dust collector, etc.
The main working process of continuous oil sludge pyrolysis plant
- Feeding
Take different feeding modes according to the state of raw materials. If it is solid, it can be directly fed. If it is liquid, it needs to be fed in a ton bag, and then the oil mud is sent into the pyrolysis reactor through a sealed screw feeder.
- Heating
Heating the pyrolysis reactor of continuous oil sludge pyrolysis plant by any fuels such as coal, natural gas, liquefied petroleum gas, etc. When heated to 100 degrees Celsius, the moisture in oil sludge will take the lead in evaporation, internal temperature rise along with the pyrolysis reactor, to a certain extent, oil sludge pyrolysis to produce oil gas, and then flow into the buffer tank, the oil gas in the large molecules will liquefied the collection for the heavy oil into heavy oil tank, small molecules of oil gas rose up into the cooling system.
- Cooling
The light oil gas enters the condenser uniformly. Through the three-stage condensation system, the oil gas will be liquefied to fuel oil and stored in the tank. The non-condensable gas will be desulphurized in the water seal and then circulated to the pyrolysis reactor to provide heat as heating fuel, thus saving fuel cost.
- Slagging
After all the above operations are completed, the slag can be discharged through the automatic screw unloading machine. The slag is mainly composed of soil.
Advantages of continuous oil sludge pyrolysis plant
- The pyrolysis reactor is rotated in vitro, and the reactor body is evenly heated at 360 degrees, which can extend the life of continuous oil sludge pyrolysis plant.
- There is a turnover device inside the reactor, which needs to be turned over more than 4000 times in the process from feed to discharge. The waste oil sludge is continuously forced to turn in the reactor and is highly dispersed. In this way, the oil sludge can be fully pyrolyzed and the oil yield can be improved.
- The pyrolysis reactor adopts the rotary varus continuous heating mode. The waste oil sludge runs along the inner wall of the reactor and is in direct contact with the surface of heat transfer. So that heat transfer speed is fast, which can save the reaction time.
- The production scale can be adjusted. The continuous oil sludge pyrolysis plant can combine multiple pyrolysis reactor in tandem to achieve large-scale production, and can also be further adjusted according to customer requirements.
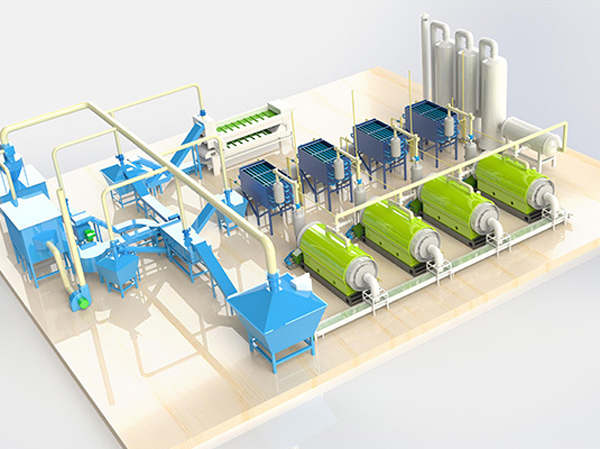
Waste Aluminum Plastic Pyrolysis Plant
The aluminum and plastic pyrolysis machine uses the principle of pyrolysis to convert waste aluminum and plastic into fuel oil, combustible gas, aluminum slag and other energy sources in a high temperature and oxygen-free environment. In addition to core components such as reactors and condensers, the machine is also equipped with environmental protection and safety equipment such as exhaust gas purification system, desulfurization tower, water seal, vacuum device, etc.
Aluminum and plastic pyrolysis machine is a key factor in determining whether you are profitable, so choosing a good machine will do more with lewith less. Doing’s waste aluminum and plastic pyrolysis machine has a high degree of automation, high oil yield, and can handle products of various scales. The quality has been recognized and trusted by more than 90 countries and regions around the world. Our factory has a complete set of complete and advanced prototype, welcome to visit and inspect at any time.
Aluminum and plastic pyrolysis machine working flow
- Feed
Fully automatic continuous equipment is used to transport waste aluminum and plastics to the reactor, and the entire process is sealed to ensure safety and environmental protection.
- High temperature pyrolysis
When the reactor is heated, the waste aluminum and plastics will be pyrolyzed under high temperature and oxygen-free conditions, oil and gas will be generated after reaching a certain temperature.
- Cooling
The oil gas passes through the vertical condenser and the horizontal condenser in turn through the buffer of the buffer tank, then the oil gas is condensed into oil under the action of low temperature cooling.
- Exhaust gas purification
After passing through the condensing system, the non-condensable oil and gas can be used as fuel to heat the reactor through the tail gas purification system.
- Deslagging
After the oil and gas are exhausted, the continuous aluminum and plastic pyrolysis machine will automatically discharge the remaining aluminum and plastic slag in the furnace and collect it in a sealed manner.
- Flue gas treatment
The flue gas generated during the heating process of the reactor enters the desulfurization tower for purification, it can be discharged into the atmosphere in accordance with the national environmental protection emission standard.
Products and applications of aluminum and plastic pyrolysis machine
Pyrolysis oil: it mainly used as industrial fuel and used in the production of steel plants, cement plants, power plants and other factories, and can also be further extracted from non-standard diesel or gasoline.
Advantages of aluminum and plastic pyrolysis machine
- Environmental protection
The waste aluminum and plastic pyrolysis machine is equipped with environmental protection devices. After the non-condensable combustible gas is processed by the tail gas purification system, it is used as fuel for the heating of the reactor. The flue gas generated during the heating process of the reactor enters the desulfurization tower for purification treatment, and reaches the national environmental protection emission standard. The entire process is well sealed to prevent dust pollution.
- Security
The reactor adopts a standard arc-shaped pressure head design, which can bear high temperature and high pressure, one-piece pressing, and it is not easy to crack. The heat source does not directly contact the reactor and indirect heating makes the heating uniform and prolongs the service life of the reactor. The equipment is equipped with safety devices such as thermometers, pressure gauges and safety valves to ensure the operating conditions of the equipment at any time. In addition, it is equipped with water seals and vacuum devices to prevent the backflow of oil gas.
- High oil yield
In the cooling stage, a vertical condenser and a horizontal condenser are set up in sequence. The most commonly used and most effective condenser in the pyrolysis industry is used to ensure that the pyrolysis oil gas is fully cooled and the oil output rate is high.