With the continuous increase of car ownership in China, waste tire treatment has become a topic of environmental protection, which also gave birth to a number of waste tire oil refining equipment. At present, there are three main forms of waste tire refining equipment in the domestic market, which are intermittent, semi-continuous and continuous waste tire refining equipment.
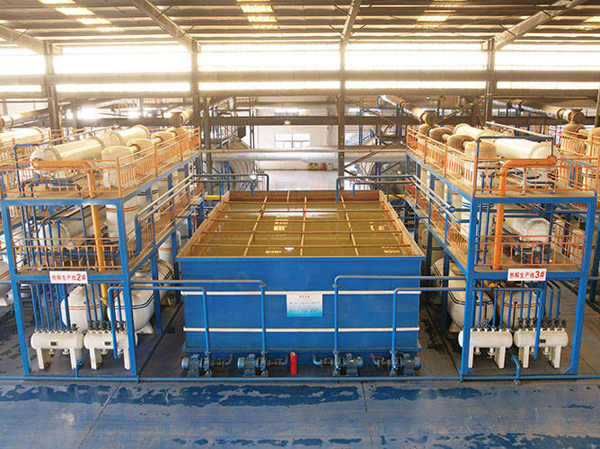
Waste tyre pyrolysis plant
The main process of waste tire oil pyrolysis plant includes pretreatment, heating, cracking, condensation and collection. The pre-treatment stage is mainly to break the waste tire into small pieces for subsequent heating and cracking. The heating and cracking process is the core of the entire process and requires the use of professional equipment for high temperature cracking. The condensation and collection process is to cool and collect the cracking product to obtain the required oil product.
In this process, different equipment manufacturers may use different combinations of processes and equipment, so the efficiency of the equipment will vary. In general, high-quality equipment can deal with waste tires more effectively, get more oil, and ensure the quality of oil.
In addition, the stability of the equipment is also very important. A good equipment should have high reliability and long life, can continue to run stably. If the equipment fails frequently or requires frequent maintenance, it will affect the operating efficiency and production cost of the equipment.
The process of waste tire pyrolysis oil refining cracking plant is divided into three kinds: automatic continuous type, semi-continuous type, intermittent type, etc. No matter which of the above tire oil making equipment, its equipment is mainly composed of reaction kettle, buffer tank, condensation system, oil-water separator, water seal, desulfurization tower, slag removal system, thermal oil furnace, negative pressure device, etc., equipment configuration details may be adjusted according to the size of the processing capacity, capital budget, investment scale and other needs.
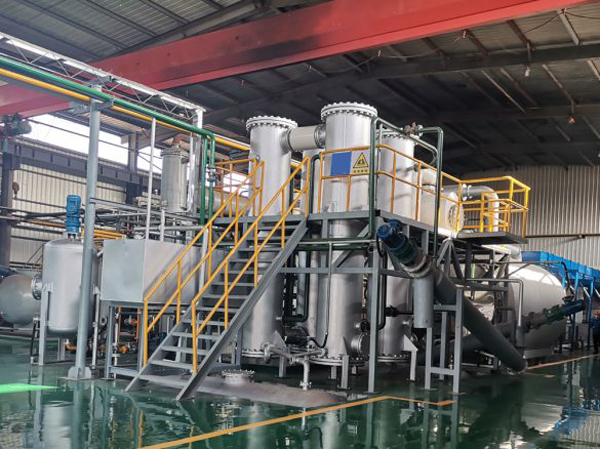
Intermittent waste tyre pyrolysis manufacturing process
1.No pre-treatment is required, the entire tire can be directly fed into the reaction vessel.
2.Heating method: direct heating
3.Production efficiency: one furnace per day
4.Column condenser: Two vertical condensers, each with four 108 tubes inside, and two horizontal condensers with 38 seamless tubes inside.
5.Slag discharge method: Side slag discharge, which needs to be cooled before discharging.
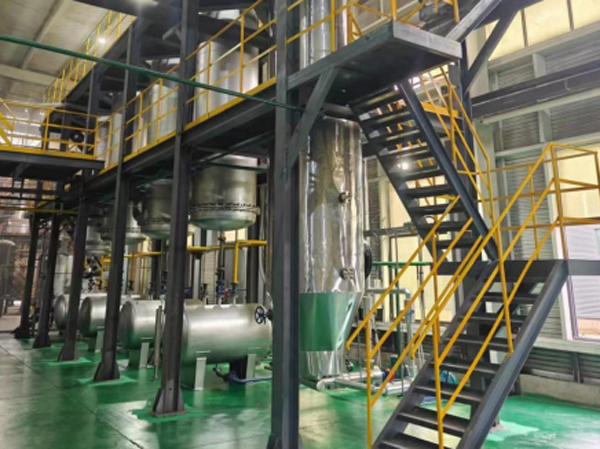
semi-continuity waste tyre pyrolysis manufacturing process
1.Pre treatment is required to grind the tires into 16-18 mesh rubber powder using a grinding machine.
2.Heating method: direct heating
3.Production efficiency: Three furnaces in two days
4.Column condenser: Two vertical condensers, each with four 108 tubes inside, and two horizontal condensers with 38 seamless tubes inside.
5.Slag discharge method: Can discharge slag at high temperature

Continuous waste tyre pyrolysis manufacturing process
1.Pre treatment is required to grind the tires into 16-18 mesh rubber powder using a grinding machine.
2.Heating method: indirect heating
3.Production efficiency: Can produce continuously for more than 40 days 24 hours a day without interruption
4.Column condenser: 3 buffer condenser tanks, 3 vertical condensers (each with over 30 pipes)
5.Slag discharge method: Material sealing technology, which can continuously discharge slag.
Waste tire pyrolysis refining oil machine can be divided into three types based on their working modes: intermittent, semi continuous, and continuous. So, what are the differences between these three types of waste tire refining equipment and how should they be selected
The intermittent waste waste tire pyrolysis equipment directly feeds the whole tire into the refining process, with a daily processing capacity of 1-15 tons. Currently, the most commonly used equipment by customers are 10 tons, 12 tons, and 15 tons. The external dimensions, processing capacity, and intermittent equipment of semi continuous refining equipment are the same, but the difference lies in the improvement of the inlet and outlet ends. The first excellent material end has been changed from a large furnace door to a spiral, which means that the feed can only be rubber powder blocks. If it is a whole tire, it needs to be crushed and ground for pre-treatment. The outlet end adopts water-cooled spiral slag discharge, which can achieve high temperature slag discharge at 200 ° C, while intermittent refining equipment can only discharge slag when the furnace is lowered to below 70 ° C, so it will effectively improve production efficiency. Under the same specifications and sizes, intermittent waste tire refining equipment can only refine one furnace per day, while semi continuous refining equipment can refine three furnaces in two days.
The continuous waste tire pyrolysis refining equipment is currently an excellent process on the market, with a daily processing capacity of 20-50 tons and a spiral feeding inlet. Unlike intermittent and semi continuous equipment, the entire production line operates in a continuous state, without the need for frequent shutdowns, equipment opening and closing, cooling and reheating operations. It can complete slag and oil discharge, and can operate continuously for about 45-60 days. The furnace is shut down for maintenance once a day, making it more automated, intelligent, and continuous.
Technical index of waste tire pyrolysis oil refining plant
item | details | ||
Treatable raw material | Waste tire, waste rubber, waste plastic, waste aluminum plastic, sludge, coal tar residue, medical waste, urban solid waste, etc | ||
Final product | Fuel oil, carbon black, steel wire, combustible gas, aluminum slag, asphalt, etc | ||
Specification and model | Processing capacity (tons/day) | Main furnace size (m) | Power (KW) |
ZH-10 | 10 tons/day | Φ 2.6, H 6.6 | 5KW |
ZH-12 | 20 tons/day | Φ 2.8, H 6.6 | 5KW |
ZH-15 | 15 tons/day | Φ 2.8, H 8.6 | 8KW |
ZH-18 | 18 tons/day | Φ 3, H 8.6 | 12KW |
ZH-20 | 20 tons/day | Φ 3, H 8.9 | 12KW |
ZH-50 | 50 tons/day | Φ 3.6, H 10 | 20KW |
ZH-100 | 100 tons/day | Φ 5, H 13 | 35KW |
Working form | Intermittent, continuous | ||
Structural design | ① Horizontal rotary furnace ② internal rotary equipment, the cracking furnace inner tank rotation, the material through the guide device inside the cracking furnace to promote the material from one end to the other end evenly run, so as to complete the entire operation | ||
Reactor material | Q345R/Q245R/ Boiler plate +/304/316 stainless steel | ||
thickness | 15 mm /16 mm /19 mm | ||
Heating method | Direct heating, indirect heating | ||
Heating fuel | Oil, gas, coal, wood, etc | ||
Cooling type | Circulating water cooling | ||
machine space | Take a 15-ton machine for example, 600 square meters | ||
Workers needed | 2-3 | ||
Flue gas emission | Reach the standard |
Technical principle of waste tire pyrolysis plant
The core process of waste tire refining equipment is low-temperature pyrolysis treatment. Tires are mainly composed of rubber (including natural rubber, synthetic rubber), carbon black, and various organic and inorganic additives (including plasticizers, anti-aging agents, sulfur, and zinc oxide). Most organic compounds have thermal instability characteristics. If they are placed under anaerobic and high-temperature conditions, under the combined action of decomposition and condensation, large molecular organic compounds will undergo cracking and transform into gaseous, liquid, and solid components with relatively small molecular weights.
Thermal cracking of waste tires is a complex and continuous chemical reaction process. This includes chemical reactions such as bond breaking, isomerization, and condensation of small molecules, ultimately resulting in the formation of smaller molecules. During the pyrolysis process, there are two trends in the intermediate products: one is the transformation from large molecules to small molecules, until the gas undergoes cracking; The second is the polymerization process of extremely small molecules into larger molecules. This reaction does not have a clear stage, and many reactions are cross occurring. The pyrolysis process can be expressed as follows: organic solid waste → gases (H2, CH4, CO, CO2)+organic liquids (organic acids, aromatics, tar, kerosene, alcohols, aldehydes, etc.)+solids (carbon black, slag).
Working process waste tyre pyrolysis plant
The main raw material processed by the waste tire refining equipment is purchased clean waste tires, which do not require pre-treatment processes such as cleaning, crushing, and wire drawing. They are directly fed into the rotary cracking furnace under the spiral action of the furnace, and the feeding process is highly automated, safe, convenient, and time-saving. The specific process flow for refining waste tires is as follows:
- Tyre pretreatment
Waste tyre through the steel wire drawing machine to pull out the steel wire in the waste tyre, and then put the tyre into the tyre crusher. After the treatment of the tyre crusher, the tyres are processed into 3-5 cm pieces.
- Feeding
Firstly, the worker drives a forklift to put the waste tires into the automatic feeding machine. One end of the feeding machine is connected to the cracking reaction kettle, and the waste tires are pushed into the cracking reaction kettle by the thrust of the hydraulic push rod. The feeding time is 2-3 hours. After the cracking reaction kettle is filled with waste tires, close the furnace door, ignite and heat to ensure that the waste tires are heated and cracked under closed and oxygen free conditions.
- Continuous pyrolysis
Next, during the heating process of waste tires, there will be a process from solid to gas and then to liquid. When the temperature inside the Pyrolysis reactor reaches the tire Pyrolysis temperature (180 ℃), the rubber macromolecular bonds in the tire break and become small molecules, starting to crack and release gas. The oil and gas produced by Pyrolysis enter the buffer tank/separator, and the gas moves from front to back. After passing through the buffer tank, the volume of the oil and gas rapidly expands, the flow rate slows down, and the carbon black impurities carried in the oil and gas can also settle to the bottom of the tank.
- Cooling
The buffered oil and gas enter the first Cooling system through the skytube – two parallel vertical condensers. The vertical condensers consist of four 108 pipes, surrounded by condensed circulating water. The oil and gas exchange heat with the condensed water through the pipes. After the temperature of the oil and gas decreases, it changes from a gaseous state to a liquid state, and is converted into cracked oil for temporary storage in the oil tank. In the future, the condensed oil and gas will continue to enter the second and third Cooling systems – oil-water separators and two parallel horizontal condensers. The Cooling principle of horizontal and vertical condensers is the same, but their Cooling pipes are more and thinner, and the heat exchange area is larger. At this stage, the most condensed cracked oil is produced.
After passing through the front-end three condensation systems, almost 80-90% of the oil and gas have been condensed into oil. However, our company has also set up a fourth condensation system – two vertical condensation towers. The oil and gas flow from bottom to top, with a slow flow rate as much as possible, in order to cool down the generated oil and gas as much as possible. At the same time, it can also avoid improper temperature control during the ignition process by the burner, resulting in too fast oil and gas production speed and insufficient time for the front-end condensation system to condense, leading to a decrease in oil yield. Therefore, we have added a condensation device to increase the tolerance.
5.Exhaust gas purification section
The remaining non condensable but highly flammable gases cannot be recovered by the condensation system and enter the desulfurization and deodorization device for purification treatment. The non condensable gas flows from bottom to top, and after being evenly dispersed by the packing, it will undergo a thorough chemical reaction with sodium hydroxide alkali solution. The acid-base fusion will remove gases such as hydrogen sulfide, sulfur dioxide, and sulfur monoxide from the non condensable gas. The non condensable gas after desulfurization and deodorization is returned to the cracking reactor as fuel for heating.
6.Flue gas purification section
The dusty flue gas generated during non condensable gas combustion and waste tire refining process will enter the desulfurization and deodorization tower. The dusty flue gas flows from bottom to top and is evenly dispersed by four sprays and four layers of ceramic fillers. Through layer by layer spraying, the gas is mixed and reacted with alkali solution to achieve desulfurization. Dust particles are separated by centrifugal force, and smoke particles are adsorbed by the water film layer generated by spraying. They flow with the water to the bottom cone and are discharged through the dust outlet to achieve the purpose of dust removal.
7.Slag discharge section
After the cracking is completed, open the vacuum negative pressure and continue working for half an hour to remove the residual high-temperature oil and gas in the reaction kettle, reduce the oil and gas concentration, and avoid flash explosion when opening the furnace door and coming into contact with oxygen. Close the heating system again, open the induced draft fan and 4 air inlet valves. The induced draft fan will extract the hot air from the furnace, and the cold air will enter through the air inlet to achieve rapid cooling and furnace cooling. Using the cold air system to cool the furnace takes 4-5 hours, saving half of the time.
After the furnace temperature drops, the slag discharge system can be opened for slag discharge. Adopting the side slag discharge method, a slag discharge port is opened every 180 degrees on the rear side of the furnace, and slag is discharged twice for each rotation. The reaction kettle rotates in the opposite direction, and carbon black is discharged from the slag discharge port. The slag discharge time is 2-3 hours.
8.Wire pulling section
After the coarse carbon black slag discharge is completed, only the wire pulling section is left. The wire pulling section pulls out the rough wire inside the reaction kettle and collects it uniformly. Finally, collect the cracked oil from the temporary storage tank of the equipment into the on-site large oil storage tank.
9.Oil product collection
Liquid oil is collected into the tank. No fireworks around the oil tank.
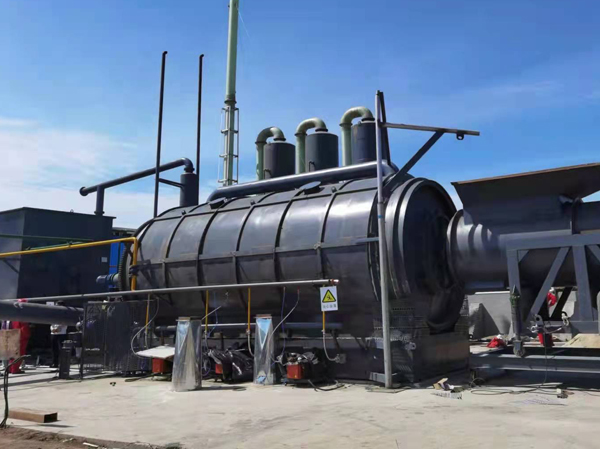
Special insulation layer with good insulation effect
The main reactor is made of standard boiler steel
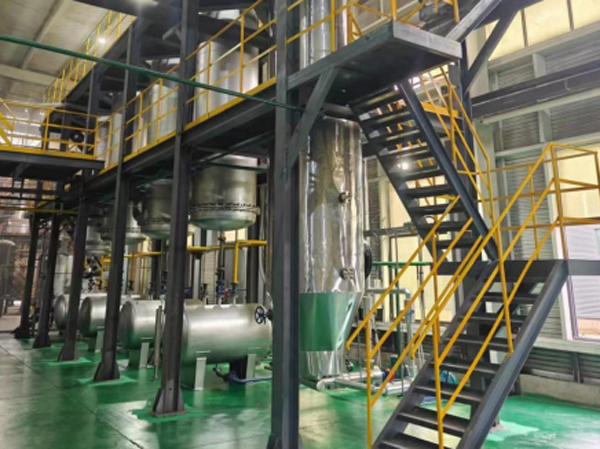
Compact feeding, fast feeding speed, capable of high-temperature feeding
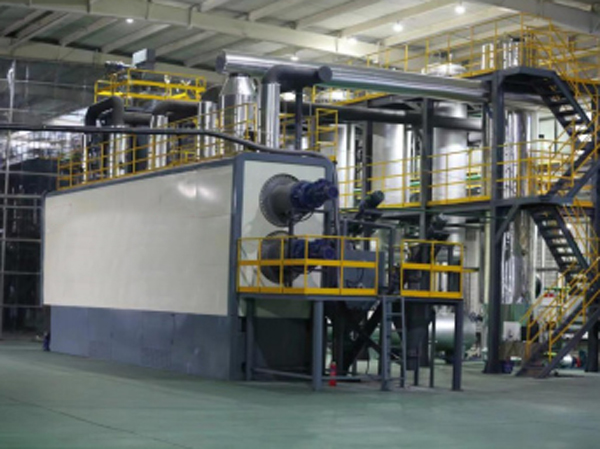
Carbon black unload by high temperature is cooled in this reactor and stored after reaching a certain temperature
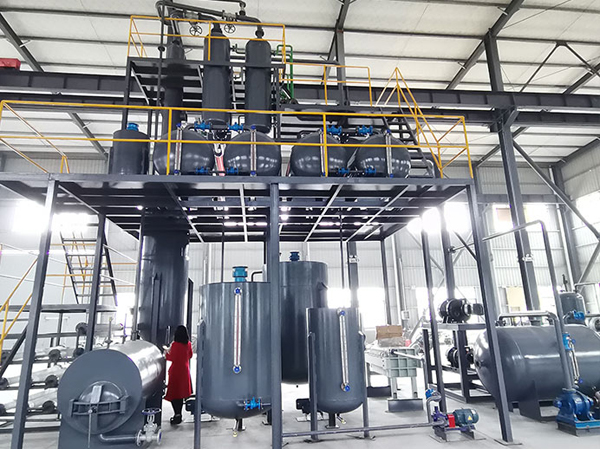
The uniquely designed box type condenser enjoy good cooling effect and easy to clean.
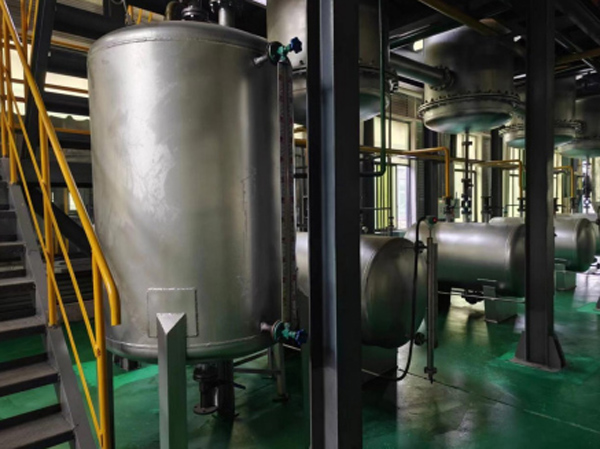
Non condensable combustible gas recycle system safely recycling waste gas into the combustion chamber to burn to save fuel
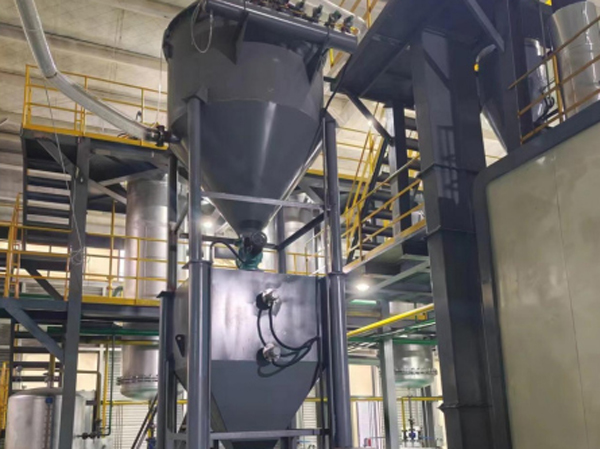
Purify the exhaust gas generated by combustion and discharge it after meeting the emission standards.
Technology of Continuous Waste Tyre Pyrolysis Project Plant
- Our pyrolysis plant has auto feeding system. The material goes from underground to the feeder and then goes into reactor,which is automatic operation. And no flying dust in workshop at all.
- We have energy saving technology:the fuel is heated at the bottom of the reactor indirectly (flame towards to the ground),with 8 burners evenly installed on the reactor,which can transfers heat energy equally to the reactor all around in 360 degree. In this way,it will save a lot of fuel energy and also protect the reactor for longer service life.
- At present, the biggest problem for continuous production of rotary reactor is thicken coking which will be formed continuously when feeding materials are affected by high temperature in the reactor, which not only makes the reaction unable to proceed, but also damages the equipment quickly. We have special advanced technology which can constantly remove the coke in the reactor to ensure the continuous feeding and pyrolysis that will greatly extend the life of the equipment and also increase production efficiency.
- During heating process, the reactor will rotate automatically and slowly,regularly 3mins per round, the material will pyrolysis completely after from one end to the other end. And the carbon black quality are much better with oil content less than 0.3% only. The carbon black quality is fine powder.
- The syn gas generated from the system will be used to support continuous heating. The fully continuous system even dose not need any extra fuel once the system is started up. Because the syn gas will be far enough for the heating purpose. It will save much of the fuel cost.
6,High oil yield technology. Generally,there is still big quantity of rest syn gas after burning,we have technology to convert syn gas into fuel oil again,thus it will increase the oil yield rate to 42-48% (regular rate around 40% only).
- With our special soft sealing technology,the whole pyrolysis plant is totally air tight without leakage problem. So there is no harmful gas or bad smell coming out from the system. And the system has automatic depressur-ization valve,so the pressure inside of the reactor wont never be dangerous.
- All the carbon black and steel wire collecting system covered in air tight system and connected to the dust collecting equipment. So the whole workshop will be tidy and with lower noise.
- We use water pools for cooling only (not N2). The water are used circularly from equipment into pool,which will save a lot of cost per day.
- Muti-graded discharging system with water jacked promise low temperature while discharging.
- All of our system has passed the ISO,SGS and CE certificates.