The animal feed pellet production line is equipped with all kinds of feed processing equipment, including impurity removal, crushing, stirring, granulation, cooling, screening, and packaging. It can also customize the production of forced feeders, quality assurance devices, and screw winches according to the actual processing needs of customers, fully meeting their needs.
Our company specializes in the design and installation of animal feed processing production lines. A complete feed processing line has dedicated personnel responsible for drawing design, production ordering, loading and shipping, installation and commissioning, maintenance and upkeep to ensure product quality.
With rich experience, we have designed and installed over a thousand feed processing production lines for countless feed processing plants, large-scale breeding farms, and large-scale breeders over the years, and have received high praise from our customers.
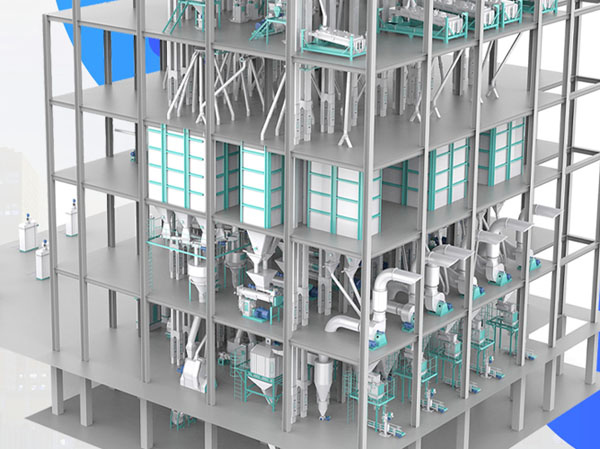
Automatic animal feed pellet production line
processing capacity:1-100T/h
Application scope:poultry and livestock Ruminant Concentrated feed processing machine
Raw materials: conventional livestock and poultry raw materials include corn, wheat, barley, oats, sorghum, soybeans, soybean meal, fish meal, amino acids, miscellaneous meal, whey powder, oil, meat and bone meal, grain, feed additives and other more than ten varieties of feed raw materials.
Provide animal feed (pig, etc.), poultry feed (chicken, duck, goose, etc.), ruminant feed (cattle, sheep, etc.), ordinary aquatic feed (four fish, etc.), special aquatic feed (shrimp, crab, etc.), expanded aquatic feed (floating and sinking fish feed, shrimp, etc.), premix (including various additives, etc.), pet food (cat food, dog food, etc.) complete sets of equipment
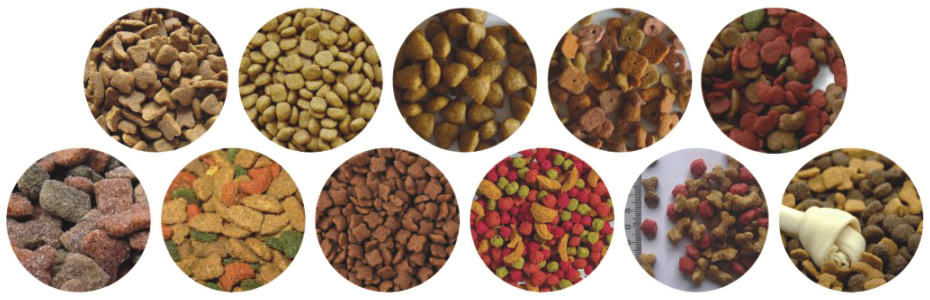
Type of animal feed production line
According to the type of animal, animal feed production line pellets can be divided into poultry feed production line, livestock feed production line, ruminant feed production line, aquatic feed production line, pet feed production line, fish feed production line, shrimp feed production line, grass feed production line, premix feed mill, pig feed plant, chicken feed production line, powder feed production line, concentrated feed production line, enzyme protein biological feed production line, etc.
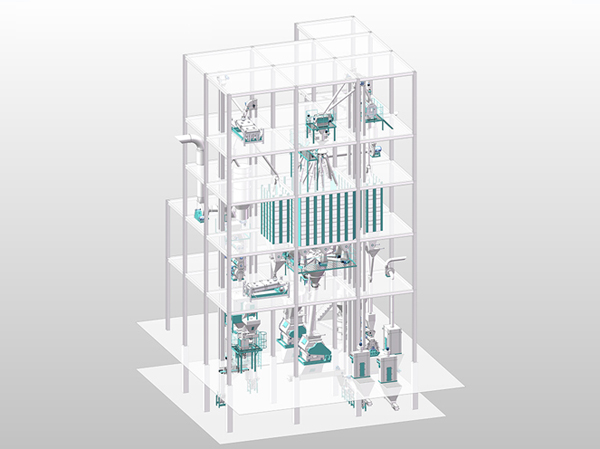
Poultry Feed Production Line
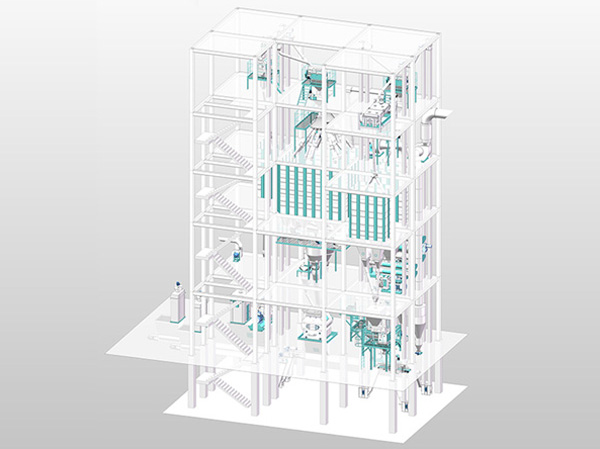
Livestock Feed Production Line
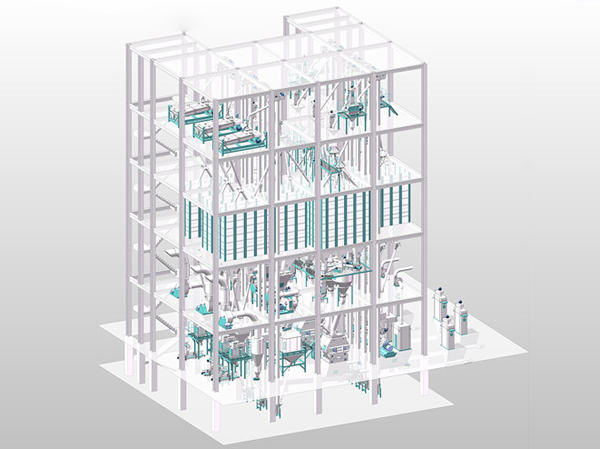
Ruminant Feed Production Line
According to animal physiological characteristics, nutritional requirements and raw material characteristics, combined with engineering construction and production practice experience, to provide you with excellent production process and engineering design services.
The specialized production process ensures the freshness of raw materials and the efficient balance of nutrition; High performance equipment and accessories to reduce operating costs, reduce residues and avoid cross-contamination; Excellent control technology to achieve automated, intelligent and traceable production to ensure feed safety. The design of raw material storage, the automatic entry of bagged raw materials, the automatic design of small material system, the automatic control of single equipment, the use of automatic packaging and palletizing devices reduce the use of labor.
Manufacturing process of animal feed pellet production line
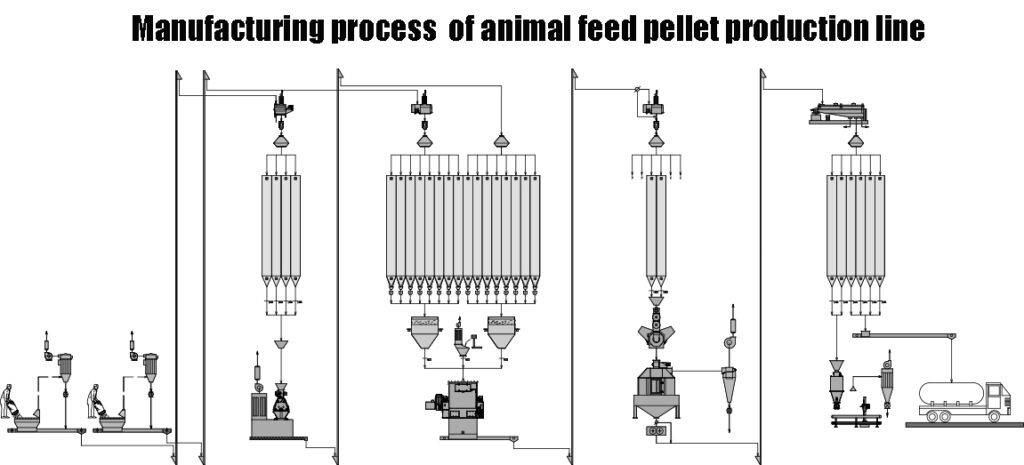
Animal feed production line processing flow introduction
1.Receiving and initial cleaning process
Bulk raw materials corn and soybean meal are received. The first thing to do in the initial cleaning receiving process is to remove impurities in the raw materials, and then transport them to the silo according to the plan through the receiving equipment and demagnetization equipment.
When loading and unloading, the raw materials should be checked and placed in the warehouse to ensure the cleanliness of the receiving environment.
2.Batching process
The feeder under each batching bin feeds the batching scale, and the batching scale weighs each raw material, and then transports it to the powder bin, and then adds a small amount of premix, which can improve the batching accuracy.
3.Crushing process
The crushing process refers to feeding the raw materials in the crushing bin into the crusher to crush them into powder, and then sending them to the mixing bin for standby through the conveying machinery. The purpose of this process is to control the particle size of the material.
The efficiency of the crusher designed in this process determines the production capacity of this set of process equipment. It is also the process with the highest energy consumption in the production of powdered materials.
4.Mixing process
Discharge the crushed raw materials into the mixer, then add oil to the feed in the mixer, mix all the components evenly, and mix the raw materials evenly. For the production of pellet feed, the mixed powder will be sent to the pelletizing bin.
5.Pelleting & Cooling process
The mixed materials are sent to the pelletizing chamber after magnetic separation and conditioning in the pelletizing bin, and pressed into pellet feed by animal feed pellet machine, cooled by the cooler, and screened out standard pellet finished materials by screening equipment.
During cooling, the cooling tower should be adjusted according to factors such as variety, indoor temperature and humidity, and season to achieve qualified pellet temperature and humidity.
6.Finished product packaging process
The finished feed is weighed by the packing scale in the finished product bin, packed in packaging bags, sealed with edible labels, and transported to the warehouse. In some feed production line designs, qualified pellet products enter the bulk bin and are transported out of the factory by bulk trucks.
The main commonly used equipment in animal feed production line
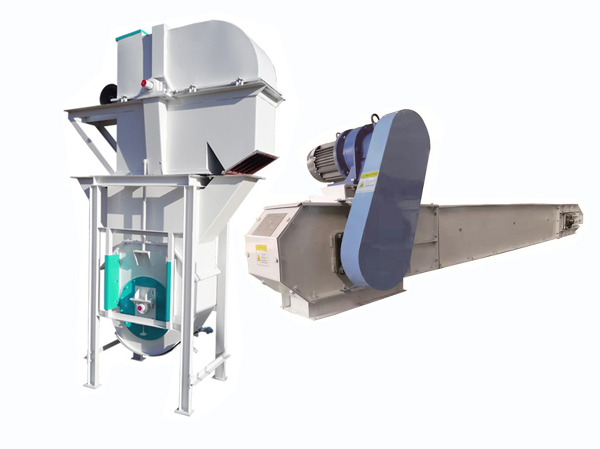
Conveying and distribution equipment
materials, semi-finished products and finished products and conveying them to the corresponding work sections or silos. Conveying equipment can be divided into two categories: mechanical conveying and pneumatic conveying. Mechanical conveying for animal feed production line is further divided into two categories: vertical conveying and horizontal conveying.
Bucket elevator is suitable for lifting and transporting large and medium-sized feed processing plant in the production process of materials, and other powder lifting. 2. Working principle: When working. The material flows evenly from the feed port of the bucket elevator into the bucket of the base and is then raised to the head of the machine. When the bucket goes around the drive wheel, the material is poured out and flows from the discharge port into the required container or the equipment of the next process. The whole process is divided into three stages: loading, lifting and unloading, mainly loading and unloading
Cleaning (impurity removal) equipment
Mainly removes impurities in feed raw materials, especially large and medium impurities and iron impurities, to protect equipment and personal safety. Cleaning equipment for animal feed production line mainly includes screening equipment and iron removal equipment. Screening equipment mainly includes cylindrical screens, cone screens, rotary screens and vibrating screens. Iron removal equipment mainly includes permanent magnetic cylinders, plate magnetic separators, etc.
Conical powder screen:used for the initial cleaning of powder auxiliary materials, effectively crushing the aggregates in powder auxiliary materials, separating large impurities such as stones;
Cylinder primary cleaning screen:good cleaning effect, high impurity removal efficiency, impurity removal efficiency ≥99%;
Permanent magnet cylinder:strong separation of magnetic metal inclusions in raw materials
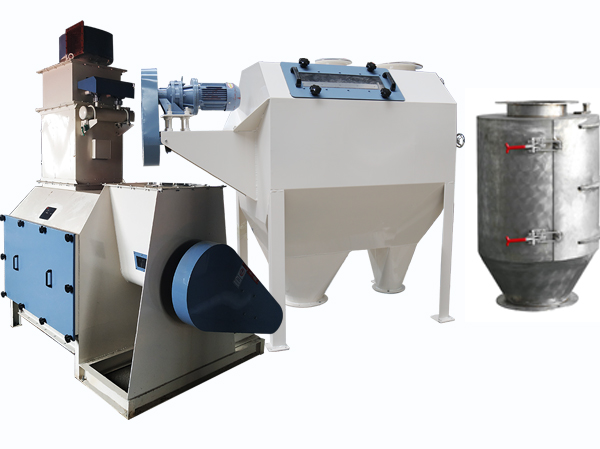
Crushing equipment
mainly used to crush feed raw materials with unqualified particle size to meet the requirements of feed particle size. According to the different requirements of the crushing particle size, the crushing equipment for animal feed production line also has different forms, mainly including hammer mill, vertical crusher, roller crusher, micro-crusher, ultra-fine crusher, etc.
High output and low energy consumption
◆ Advanced droplet crushing chamber design, reasonable secondary crushing structure, the output increased by 20% compared with other models;
◆ Both sides of the feed port are equipped with wear-resistant tooth plates, which can effectively destroy the logistics circulation, increase the impact, rubbing and shearing of the material, and improve the crushing efficiency;
◆ The “star triangle” arrangement is adopted to increase the screening area, improve the screening rate, and effectively improve the crushing efficiency;
◆ Set the shaft end air supplement device to supplement the air volume of the crushing chamber, destroy the crushing circulation while reducing the bearing temperature rise;
◆ Set two kinds of hammer screen gap, two different rotor configuration, suitable for aquatic feed and livestock feed raw material grinding, respectively improve their efficiency.
Ultra-stable and durable
◆ The whole base is milled and processed to ensure the stability of the whole operation;
◆ The hammer is made of special alloy steel and hardened by suspended tungsten carbide surface treatment to achieve higher strength and durability;
◆ Rotor can work in positive and negative direction, longer service life;
◆ High-precision dynamic balance detection rotor, more stable operation, lower noise;
◆ Test machine by machine, running time > 45min, stability is better than the national standard, vibration speed up to 2-4mm/s (national standard ≤16mm/s).
Easy to operate more user-friendly
◆ Shiftable operation door and linkage screen press mechanism, more convenient operation and maintenance;
◆ Equipped with safety interlock device to protect personal safety;
◆ Various feeding devices such as screw and impeller can be selected according to actual needs.
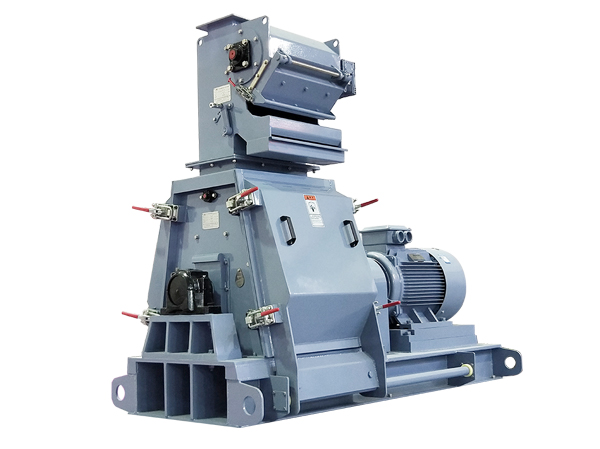
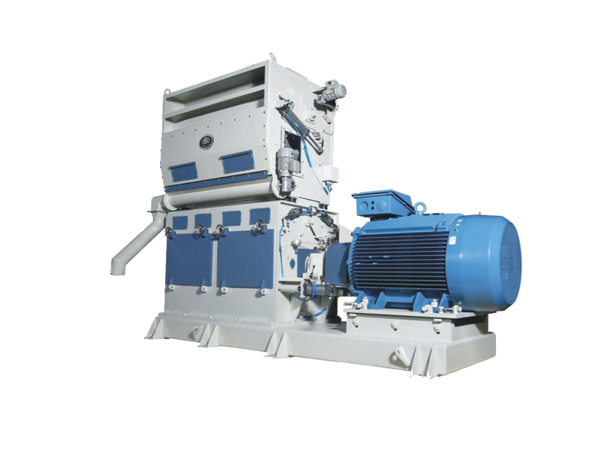
On-line quick screen changing design, improve screen changing efficiency;
Screening track anti-stuck material design, screening more smoothly;
Up to 3000rpm/3600rpm(60HZ), improve grinding fineness and grinding efficiency;
Reasonable feed and fixed hammer design to destroy the grinding circulation;
Equipped with SKF progressive self-lubricating bearing and bearing seat;
Overall heavy precision milling anti-vibration base, better stability.
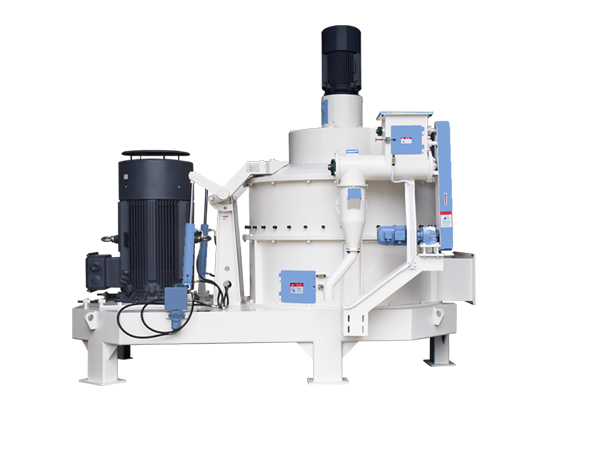
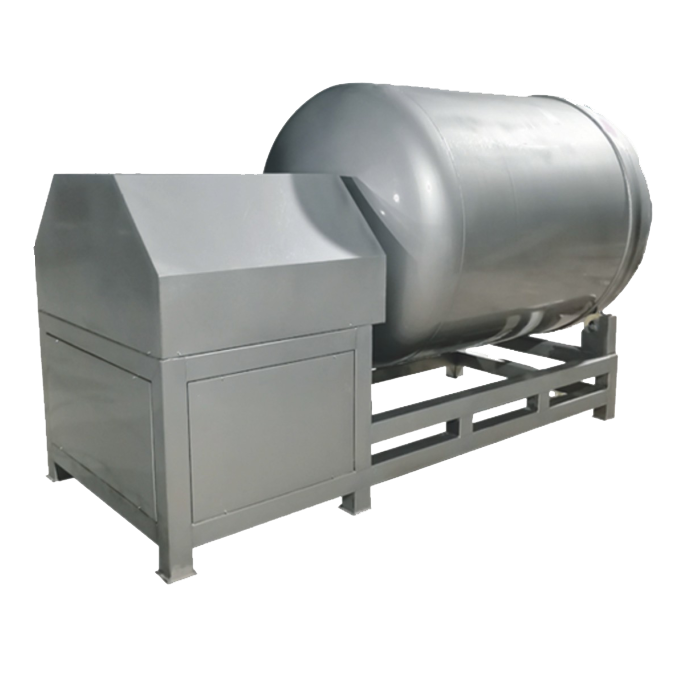
Batching equipment
It is a device that mixes the animal feed raw materials in a certain proportion (weight) according to the requirements of the formula. Batching equipment for animal feed pellet production line is divided into automatic batching and manual batching. Automatic batching equipment generally uses computer-controlled batching scales. Manual batching is only suitable for small feed factories, and scales are used for batching
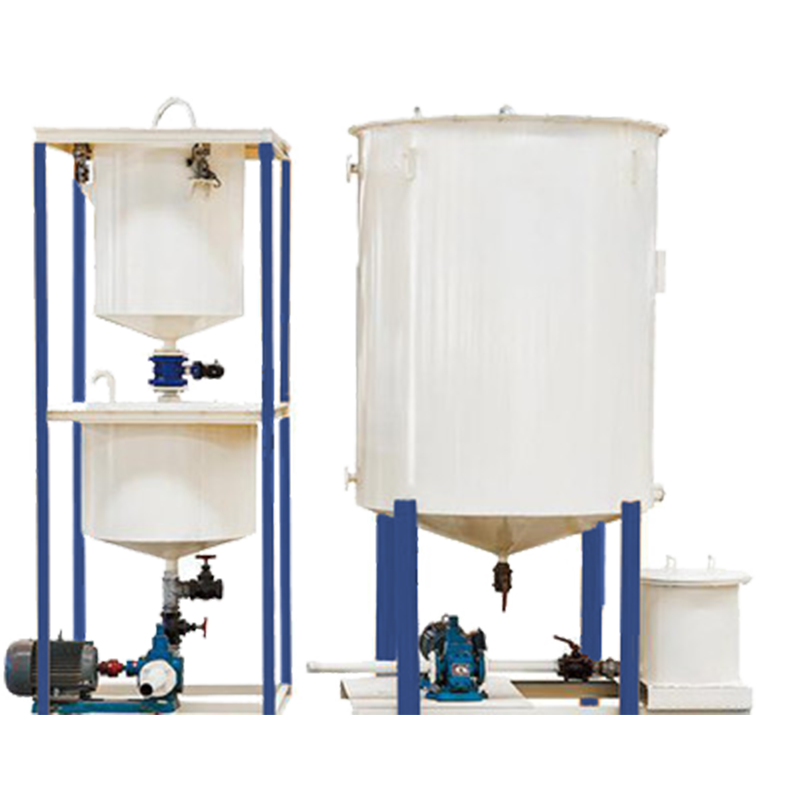
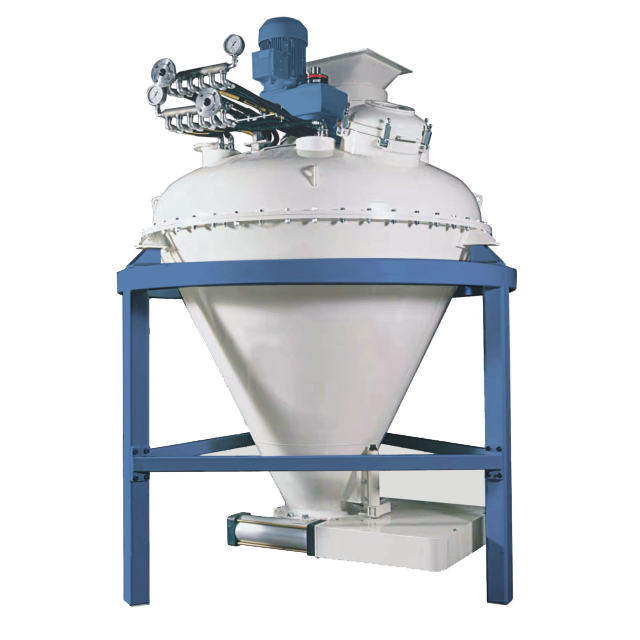
Perfect combination with the batching system, simple and convenient operation;
◆ Real-time reflection of all data batches, automatic/manual adjustment accuracy;
◆ Can add a variety of liquids at the same time, convenient combination;
◆ Liquid dispensing and drawing are fully automated, without manual operation;
◆ Using advanced spraying technology, there is no caking residue in the mixer;
◆ Efficient pipeline cleaning, anti-drip technology, uniform no caking;
◆ Perfect heating and insulation function, save worry and effort.
Mixing equipment
It is a device that fully stirs the prepared feed raw materials to make them into a powdered feed product with qualified chaos and uniformity. Feed factories often use intermittent mixing equipment, mainly horizontal spiral blade mixers, double-shaft paddle mixers, single-shaft paddle mixers, etc.
Biaxial blade mixer is mainly used for processing coal, tar residue and other materials, mixing, stirring, widely used in feed, food, chemical, pharmaceutical, pesticide and other industries in the powder, granular, flake, block and thick material mixing, effectively improve work efficiency.
Performance advantage:
★ High mixing uniformity, less material residue in the machine;
★ According to the needs of users, the use of large door or small door, pneumatic, electric or manual door discharge;
★ According to user needs, add liquid adding device.
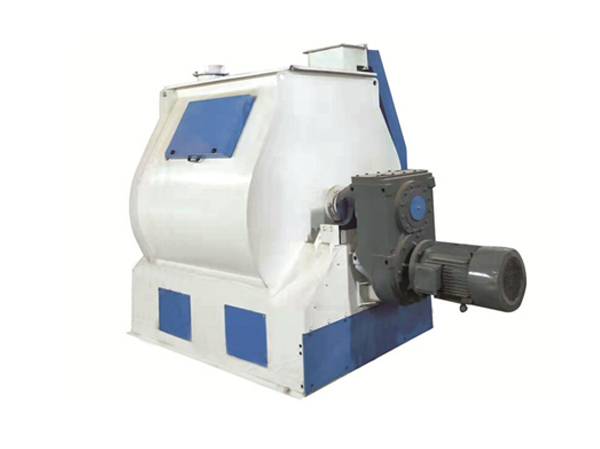
Granulating pellet equipment
It is a device that makes powdered compound feed into granular compound feed. There are two forms: ring die and flat die. At present, animal feed factories mainly use ring die granulators. Animal feed pellet mills for animal feed line are usually equipped with feeders and conditioners. Depending on the requirements of conditioning, they can be equipped with single-layer conditioners, double-chamber conditioners, three-chamber conditioners or double-shaft differential conditioners.
Pellet feed press machine
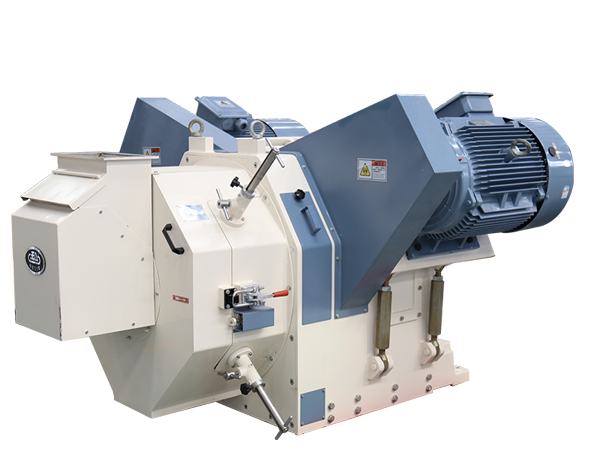
◆ Double motor drive of “▽”, reduce the floor area, more uniform bearing capacity of the spindle, extend the service life;
◆ “flywheel effect” of large belt pulley, more energy saving operation;
◆ Fine processing, reasonable design of ring mold, granulation efficiency is higher;
◆ The whole casting frame, running more smoothly;
◆ The granulator door is made of stainless steel;
◆ Unique oil filling device, more convenient lubrication;
◆ The main bearing adopts “SKF” bearing;
◆ Almost perfect structure, high standard material selection, low maintenance cost;
◆ Equipped with safety interlock device to protect personal safety;
Pellet feed press machine
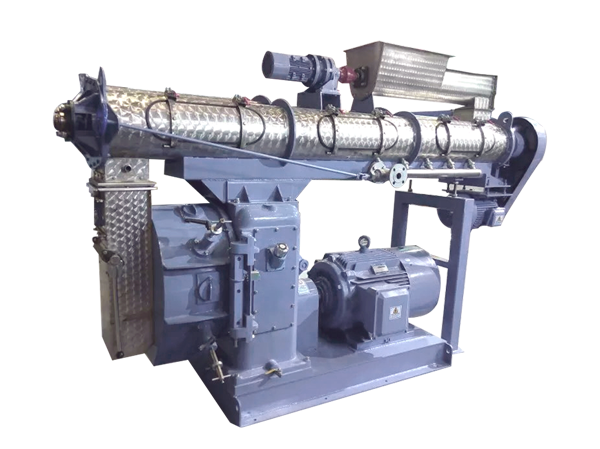
◆ Fine processing, reasonable design of ring mold, granulation efficiency is higher;
◆ Casting box, finishing base, more stable operation;
◆ The granulator door is made of stainless steel;
◆ Unique oil filling device, more convenient lubrication;
◆ The main bearing adopts “SKF” bearing;
◆ Almost perfect structure, high standard material selection, low maintenance cost;
◆ Equipped with safety interlock device to protect personal safety;
◆ Single layer, multi-layer, dual-axis differential or combination tempering equipment can be selected according to actual needs.
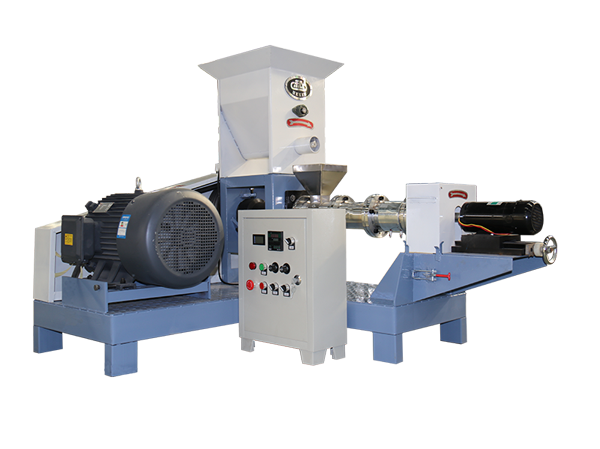
Feed puffing machine
◆ Automatic speed feeder, feeding amount can be changed according to the situation;
◆ The extrusion screw is a telescopic combination structure, and the screw sleeve adopts an inner cylinder structure. According to different expansion requirements, the corresponding extrusion screw group can be flexibly formed, and then equipped with different export parts, which can adapt to different processing conditions;
◆ The overall shape is exquisite, the structure is simple, easy to operate and repair;
◆ Equipped with independent electronic control system;
◆ Suitable for different production requirements, such as the detoxification treatment of extruded full-fat soybeans, extruded corn, cotton embryo meal (or rapeseed meal) or extruded pet feed, aquatic feed, fox feed or other special feed.
Cooling equipment
The temperature of pelletized feed is generally around 80℃~90℃, and the moisture content is around 16%. It must be cooled and hydrated. The cooling equipment uses suction to reduce the material temperature to a temperature close to room temperature, and reduces the moisture content of the feed while cooling.
Dryering equipment
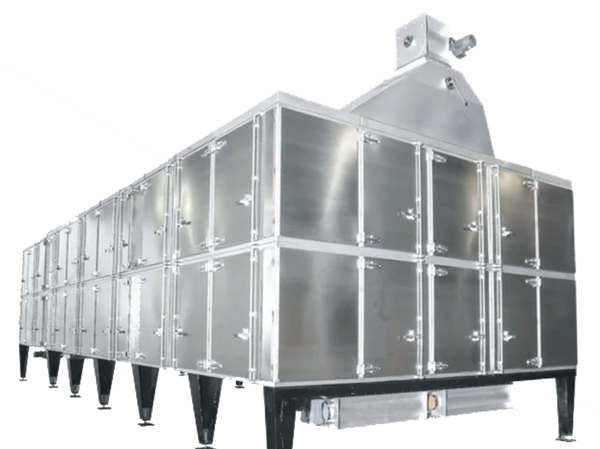
Performance characteristics
Rotary valve inlet and outlet to prevent dry air leakage;
Swing type material spreader ensures that materials are evenly spread on the dryer tray;
Fully insulated cabinet;
Quickly fasten the inspection door for easy maintenance and upkeep;
Independent and controllable airflow;
Each drying zone can independently and accurately control the temperature;
Sanitary design, each floor is equipped with a fine debris removal screw conveyor;
The porous tray design can achieve optimal airflow distribution;
A frequency converter that can control the fan speed and dryer tray speed to control the airflow speed and set the dwell time;
HMI touch screen control system;
Heat source: indirect steam heat exchanger or gas burner.
Counterflow cooler
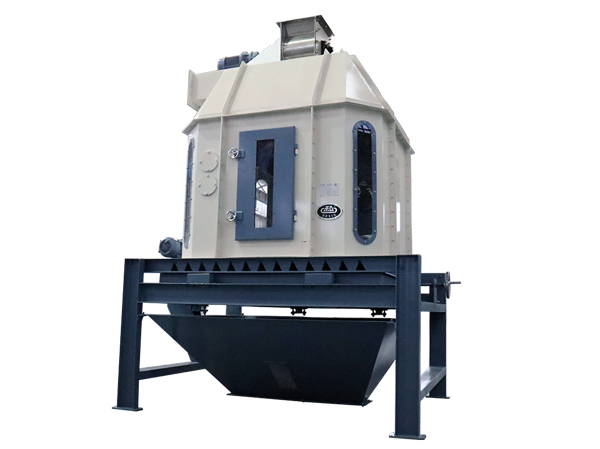
The new generation of cooling models is suitable for cooling various granular materials;
Using the principle of counter current cooling to cool high-temperature and high humidity granular materials, the materials are gradually cooled from bottom to top, avoiding sudden cooling caused by direct contact between cold air and hot materials, thus preventing surface cracking of particles;
The octagonal box body eliminates cooling dead corners, making it more conducive to uniform cooling treatment of granular materials. It is equipped with an adjustable stainless steel cone shaped dispersing mechanism, making the fabric more uniform;
Sliding grid/flip plate reciprocating discharge mechanism, flexible discharge, greatly reducing material damage, smooth discharge, adjustable flow rate;
The front of the equipment is equipped with a maintenance door and the side is equipped with an observation window, making it easy to observe the operation status of the equipment;
The new cooling chamber works smoothly and reliably, with no material leakage during shutdown.
Grading equipment
It is used to separate a small part of the powder that cannot be made into particles during granulation and part of the powder caused by crushing particles with grading equipment to ensure the quality of the finished pellet feed. The separated powder needs to be sent back to the animal pellet mill for granulation. The grading equipment mainly includes rotary screens, vibrating screens, etc.
Vibration grading screen
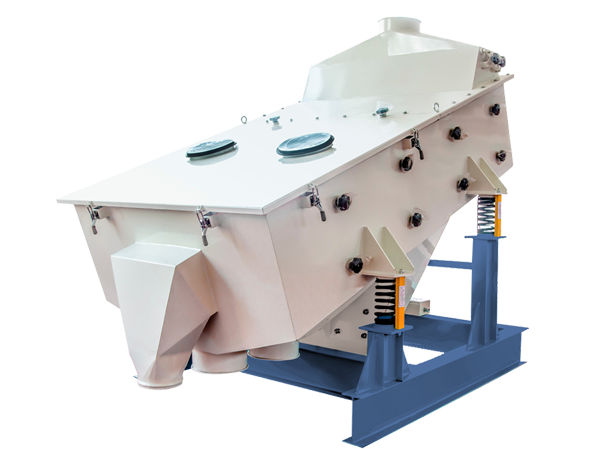
◆ Drive mode adopts self-balancing vibration mode, good screening effect, small size, smooth movement;
◆ The discharge port internal streamlined design, material does not deposit, avoid cross contamination;
◆ No oil lubrication, to avoid oil leakage;
◆ Screen pressing mechanism is simple and convenient, quick screen change;
◆ Mainly used in powder removal of finished particles, can be selected single or double screen.
Rotary grading screen
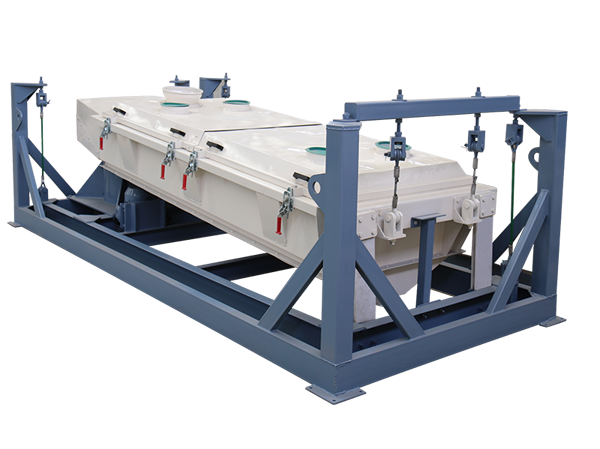
◆ Combined circle, ellipse, straight line three kinds of motion, screening effect is good;
◆ Screen body adopts belt drive, biased balance, low noise; The rear of the screen is an improved elastic support with low vibration and noise.
◆ Enhanced frame to ensure more balanced operation of equipment;
◆ Adopt one or combined screen cover screen frame structure, screen cover light weight, strong rigidity, good sealing, more convenient and faster screen change;
Pulse dust collector
◆ The use of tangential centrifugal air intake is conducive to reducing the resistance of the air network and reducing the load of the filter bag;
◆ High pressure solenoid valve spray multiple filter bag technology, better dust removal effect;
◆ According to the needs of the site, the combination of dust collector and discharger, compact structure;
◆ There are two discharging forms of cone and flat bottom for choice.
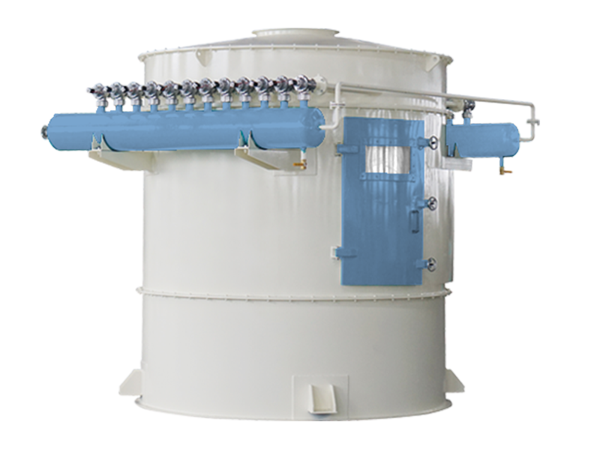
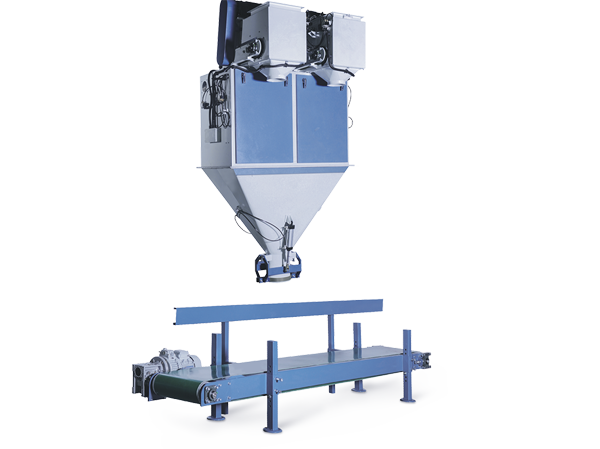
Finished product packaging equipment
Packaging can be divided into two methods: automatic packaging and manual packaging. Automatic packaging generally uses a computer-controlled automatic quantitative scale with a conveyor and a sewing machine. Manual packaging generally uses a scale plus a portable sewing machine.
◆ Suitable feeding mechanism to ensure the rapid flow of weighing materials;
◆ All parameters are input by the panel, fast, slow feed, bag clamping, loose bag all automatic control;
◆ Intelligent weighing instrument can display gross and net weight at the same time;
◆ Automatic tare function; Automatic detection and correction of weighing errors;
◆ With a cumulative package number display function, to achieve quantitative management of the production process;
◆ The whole system is equipped with dust suction to improve the working environment.
Cost to start animal feed pellet production line
In the animal feed processing industry, the investment in animal feed production lines has always been a hot topic. So, how much does an animal feed production line cost?
The configuration of the animal feed production line is carefully designed according to the on-site survey or the actual requirements of the customer, which fully reflects the rationality, effectiveness, applicability, large output, low wear and low operating cost of the animal feed mill design.
According to different technological requirements, various types of animal feed machinery are combined to meet customers’ different animal feed manufacturing process requirements.
Scale | Total Power | Site Requirements | Installation Cycle | Animal Feed Mill Cost(USD) |
---|---|---|---|---|
1-2T/H | 48-75KW | 300-500m² | 7-15 Days | 9000-50000 |
3-4T/H | 55-165KW | 300-700m² | 15-20 Days | 5,0000-11,0000 |
5-7T/H | 68-259KW | 400-800m² | 20-40Days | 6,0000-23,0000 |
8-10T/H | 125-410KW | 800-2000m² | 45-60 Days | 160,000-300,000 |
12-20T/H | 350-620KW | 1500-3000m² | 60-90 Days | 250,000-580,000 |
25-40T/H | 550-870KW | 2000-4000m² | 90-120Days | 45,0000-850,000 |
50-60T/H | 715-1120KW | 3000-5000m² | 100-140 Days | 900,000-1,400,000 |
60-80T/H | 810-1370KW | 5000-8000m² | 130-160 Days | 1,550,000-1,700,000 |
80-100T/H | 1250-1700KW | 8000-20000m² | 160 -190Days | 2,100,000-2,700,000 |
Choose the advantage of our intelligent animal feed production line
- Intelligent production process
In the traditional production process of livestock and poultry feed, a large amount of manual operation is often required, which is not only inefficient but also prone to errors. The intelligent livestock and poultry feed production line can achieve full automation production, greatly reducing labor costs and improving production efficiency. At the same time, intelligent production processes can ensure stable quality of feed and reduce quality problems caused by human factors.
- Environmental protection and energy conservation
In the traditional production process of livestock and poultry feed, there are often problems of energy waste and environmental pollution. Intelligent livestock and poultry feed production lines can achieve efficient energy utilization and reduce energy waste through advanced energy-saving technologies. At the same time, intelligent production lines can effectively reduce the generation of pollutants such as noise and dust, achieving green and environmentally friendly production.
- Information management
In the traditional production process of livestock and poultry feed, information transmission is often carried out manually, which is not only inefficient but also prone to information loss. The intelligent livestock and poultry feed production line can achieve real-time transmission and sharing of information through IoT technology, thereby achieving effective monitoring and management of the production process. This can not only improve production efficiency, but also provide more scientific and reasonable decision-making basis for enterprises.
- Improve production efficiency
The feed automation equipment adopts advanced control technology and intelligent operation mode, which can achieve high-speed operation of the production line and improve production efficiency. Compared with traditional manual operations, feed automation equipment can complete a large number of production tasks in a short period of time, greatly improving production efficiency.
- Ensure product quality
Feed automation equipment can achieve precise batching and mixing during the production process, ensuring accurate proportions of various raw materials. In addition, feed automation equipment can also monitor various parameters in real-time during the production process, such as temperature, humidity, pressure, etc., to ensure stable and reliable product quality.
- Reduce production costs
Feed automation equipment can avoid waste and losses caused by human operational errors through precise production control. Meanwhile, due to the fast operating speed and low energy consumption of the equipment, production costs can also be reduced. In addition, the long service life and low maintenance cost of feed automation equipment also help to reduce overall production costs.
- Improve the layout of the production line
When laying out a complete feed production line, factors such as the arrangement sequence of equipment should be fully considered to ensure the smooth operation of the entire production line. At the same time, attention should be paid to the mutual coordination and coordination of equipment to improve production efficiency.
- Improve breeding efficiency
From the above analysis, it can be seen that intelligent livestock and poultry feed production lines can bring many advantages to farmers, thereby improving breeding efficiency. Intelligent production processes can improve production efficiency and reduce production costs; Environmentally friendly and energy-saving production methods can help reduce the operating costs of aquaculture enterprises; Information management can achieve effective monitoring and management of the production process, providing enterprises with more scientific and reasonable decision-making basis.