The large-scale pig feed production line is a highly automated feed machinery used by large and medium-sized feed factories and various breeding farms to produce powdered feed, concentrated feed, and pellet feed. It is an ideal equipment for animal husbandry.
It is composed of high-performance equipment such as crushers, pulse dust collectors, screw conveyors, mixers, granulators, bucket elevators, counter current cooled particle dryers, vibrating screens, etc. It integrates functions such as crushing, mixing, lifting, granulation, cooling, and screening, with automatic feeding, rapid feeding, and smooth discharge. It is a medium-sized feed unit with low investment and quick results that integrates automation.
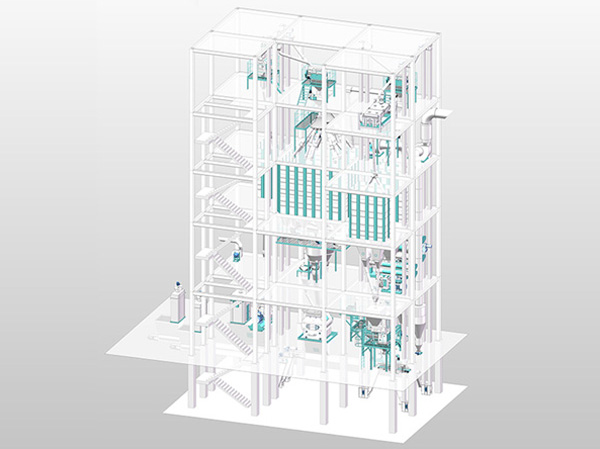
Automatic pig feed pellet production line
Project Name: Automatic pig feed pellet production line
Capacity : 1-60Ton/Hour
Raw Material: Corn, extruded corn, extruded soybean, extruded soybean meal, fish meal, salt, premix, etc.
Pellet Type : Pig feed, Livestock feed.
Installation Time : 30-60 days
The large-scale pig feed production line is of great significance for feed maturation, increasing nutrition, improving absorption rate, killing bacteria, storage and transportation, reducing costs, saving resources, adapting to the chewing function of animals, and improving the efficiency of animal husbandry.
The large-scale pig feed production line automatically heats up the material through the friction of the machine during production and processing, completing gelatinization, maturation, granulation, and cooling in one go. The packaging surface is smooth and the hardness is moderate, making it easy to seal and store. The particle size can be adjusted within 1.8mm-6mm according to the user’s needs, suitable for processing pellet feed for pigs, cows, sheep, rabbits, chickens, ducks, fish, and other animals.
The processing characteristics of high-end pig feed are fine crushing fineness (sieve aperture 1-2mm), high maturation requirements (double-layer conditioner and quality controller are used for the first granulation machine), low tempering temperature (low-temperature secondary granulation is used to reduce the deactivation of heat sensitive materials), and small particle diameter of the finished product (particle diameter is about 2-3mm). The annual production of 60000 tons of pig feed line adopts two crushing lines, one single ingredient mixing line, one single granulation line, two single mixing lines, two double granulation lines, and one fully automatic packaging line. The total power of the equipment is approximately 930KW;
The processing characteristics of ordinary fattening pig feed include moderate crushing fineness (screen aperture 2-4mm), moderate requirements for maturation and conditioning (double-layer conditioning machine is used for granulator), and large particle diameter of the finished product (particle diameter is about 2.5-4mm). The annual production of 600000 tons of fattening pig feed line adopts four crushing lines, two ingredient mixing lines, four granulation lines, four fully automatic packaging lines, and bulk lines. The total power of the equipment is approximately 2870KW
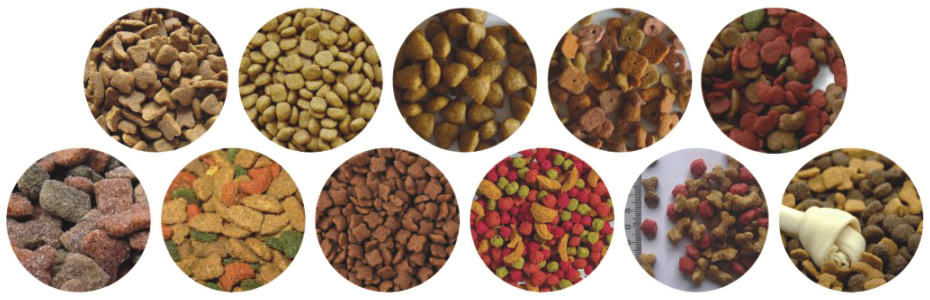
This pellet feed line are suitable for producing all kinds of feed pellets for various animals such as chicken, pig, cow, cattle, goat, rabbit and fish, etc.
Just use different size of ring die mould to produce different animal feed pellet according to the requirement of different animal and poultry.
The replacement of the ring die mould is very easy.
Feed Pellets Processing Technology
Raw Material → Feed Grinding → Feed Mixing → Feed Pelletizing → Pellet Cooling → Pellet Crushing → Screening & Grading → Pellet Packing
Equipment Related to Complete Feed Pellet Production Line
Feeding pit →Feed Grinder →Feed Mixer → Feed Pellet Mill → Counter Flow Cooler → Feed Pellets Crumbler → Feed Pellets Grading Sieve → Automatic Weighing and Packing Machine
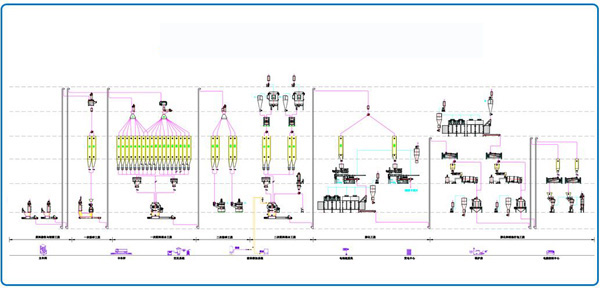
Process characteristics and section introduction
Raw material receiving and cleaning section: In this section, the cleaning of granular material feeding and powder material feeding are separated independently, with separate dust removal and good dust removal effect.
Cleaning equipment: Particle sieve SCY80, designed to produce 20-30T/H; The powder sieve SQLZ60 × 50 × 100 is designed to produce 10-15 T/H.
Crushing section: This section uses one crusher and three crushing bins, which can be alternately replaced with different crushing varieties. Before entering the warehouse, impurities are removed by a magnetic separation device to ensure the safe operation of the crusher. Due to the fine crushing fineness of high-end pig feed and the need for one crusher in this section to perform both primary and secondary crushing, a high-power crusher is used.
Crushing equipment: Crushing machine SFSP668 × 1000160KW, designed to produce 8-10T/H (fine powder).
Ingredient mixing section: This section adopts 18 ingredient warehouses and two ingredient scales for simultaneous batching. It is controlled by our company’s independently developed batching program, achieving precise fast and slow feeding, fast batching speed, and high accuracy.
Weighing equipment: ingredient scale PCS10/PCS05, ingredient accuracy: dynamic ≤ 3 ‰, static ≤ 1 ‰. Mixing equipment: SHSJ2 mixer (18.5KW, 1000kg/batch), designed to produce 10-15T/H. Mixing uniformity CV ≤ 5%.
Expansion section: The raw materials are subjected to extrusion expansion treatment. For thermosensitive raw materials, they are added to the secondary ingredients after expansion, and then subjected to low-temperature granulation to reduce the loss of thermosensitive elements. The expanded material is cooled and then crushed twice before being transported by a conveyor to the batching bin as raw material.
Expansion equipment: SPZS225200KW, designed to produce 8-10T/H (mix material)
Granulation section: This section adopts a single double-layer tempering granulator, and there are two granulation bins above the granulator. After granulation, they are separately sent to the cooler (as high-end piglet feed does not contain crushed materials, this process does not include crushers), and then enter the rotary classification screen for screening through the elevator. The finished products enter the packaging bin, and the rest are returned to granulation or bagging.
Granulation equipment: SZLH420110KW, designed to produce 6-8T/H (¢ 2.5mm piglet feed). Cooling equipment: SKLN6, designed to produce 10-15 T/H.
Packaging section: There are 2 finished product warehouses in this section, and the granular materials are finally automatically weighed and packaged by packaging scales.
Packing equipment: Belt scale (can handle both powder and granular materials), packing range 20-50kg/bag, 6-8 bags/minute.
Auxiliary section: dust removal system to improve the working environment for workers; Oil and fat addition system, commonly added at the mixer to improve feed palatability.
Main machine of pig feed production line
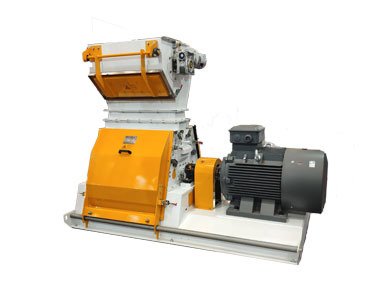
Hammer Mill
Type: Hammer Mill
Capacity(t/h):2-60
Power(kw):37-220
Application:corn, sorghum, wheats, beans, cottonseed meal,canola,etc.It can do coarse grinding and fine grinding processes.
1.This series Grinder can grind kinds of granules feed materials, like: corn, sorghum, wheats, beans,cottonseed meal,canola, etc. It can do coarse grinding and fine grinding processes, and also apply to high moisture, high fiber feed crushing. Multi-function hammer mill, using high-quality tungsten carbide spray hammer, longer life.
2.It can apply to aquatic feed and special feed plants` fine powder grinding, and also the fine powder processing of the medicine,and so on.
3.The motor is set on the same base with the rotor, direct drive.Compact structure, quick and easy to changing the seive.It have the safety device on the operating door,The rotor is calibrated by strict dynamic balance.
Double Shaft Paddle Mixer
Type: Double Shaft Paddle Mixer
Mixing time: 60-90s
Mixed yield (kg/ batch): 500-2000
Uses: Feed, chemical industry, medicine and other industries in the powder, granular, flake, block the mixture of materials.
1.The mixing chamber to increase the design, the biaxial paddle rotor, good mixing effect. The top is provided with a spraying system, which can effectively improve the atomization effect of the liquid and prevent the agglomeration.
2.It adopts three rows of chain transmission, stable operation, low noise, long service life.The mixing time is short (30 to 90 seconds per batch), mixing uniformity variation coefficient is less than 5%.
3.Specially the shaft ends and the door sealing structure, good sealing, ensure no leakage.It is widely used in mixed feed, food, chemical, medicine and other industries in powder, granular, flake, lump material.
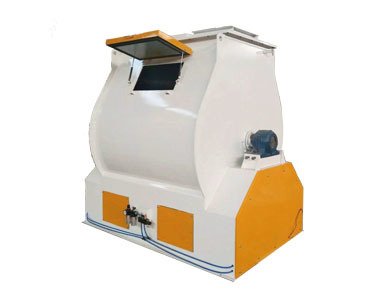
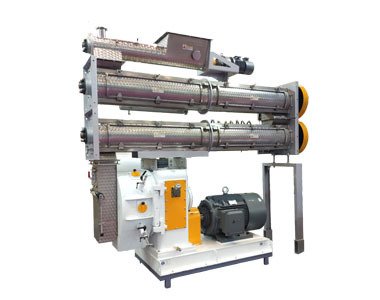
Animal Feed Pellet Mill
Type: Animal Feed Pellet Mill
Capacity(t/h): 0.5-60
Pellet size(mm): 2-12
Application: Can be used for poultry,livestock,ruminants and aquatic pellet feed production.
1.Main drive adopts high accuracy gearbox for high efficiency.Full stainless steel increased conditioning device ensure high quality of feed pellet.
2.Main parts of the bearing and standard parts are imported.High output, low noise, convenient operation and maintenance.
3.Frequency conversion (Electromagnetic speed control) feeder, with overload protection device,equipped strong magnetic security device.
Animal Feed Pellet Mill
Type: Animal Feed Pellet Mill
Capacity(t/h): 0.5-60
Pellet size(mm): 2-12
Application: Can be used for poultry,livestock,ruminants and aquatic pellet feed production.
1.Main drive adopts high accuracy gearbox for high efficiency.Full stainless steel increased conditioning device ensure high quality of feed pellet.
2.Main parts of the bearing and standard parts are imported.High output, low noise, convenient operation and maintenance.
3.Frequency conversion (Electromagnetic speed control) feeder, with overload protection device,equipped strong magnetic security device.
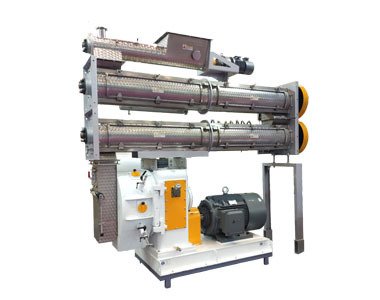
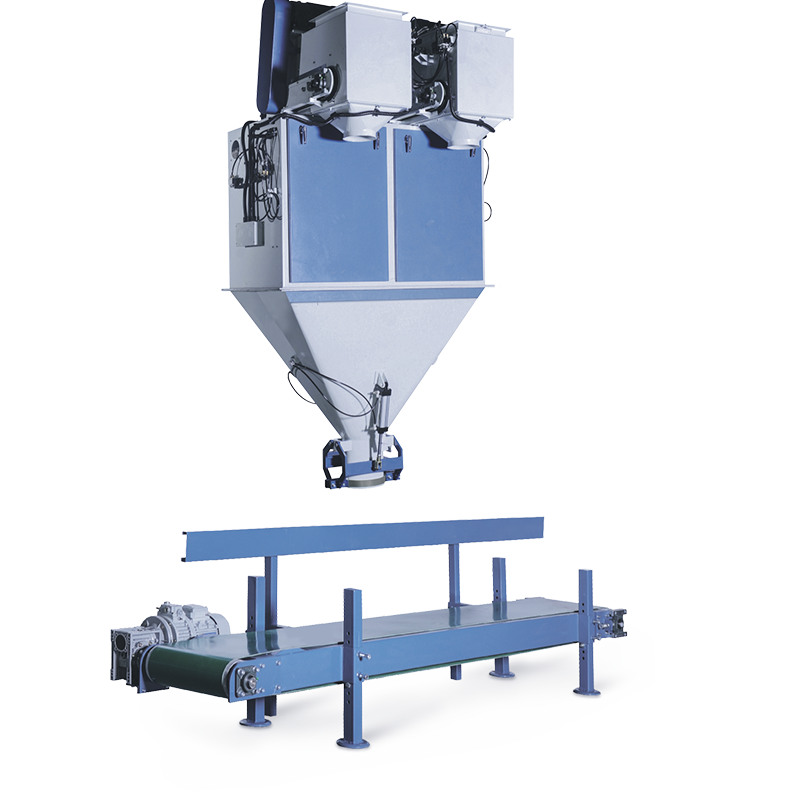
Packing Section
After cooling and screening, the feed pellet must be protected from moisture and other environmental conditions. For this there is the packing process, which is effectively handled by our Semi-Auto Packing Machine.
pig Feed Pellet With Several Advantages
- High feed hygiene: The temperature is 81° or more easily obtained during the chicken feed production line process, it can destroy the most common bacteria and fungi,like Salmonella in raw materials. The heating system will send steam to feed pellet machine by conditioner ,through automatic feeder and high pressure die ,the materials be steam curing and pressing into pellets.
- Increased nutritional value: The digestibility of the feed is increased as a result of the heat treatment and the subsequent cooling in the feed pelleting process resulting in improved performance of the livestock (feed conversion rate)
- Waste avoiding: The pellet transportation will be much cleaner and less dust than meal feed,the pellet do not get stuck in pipes, bins, etc.The pellet storage time is also longer for pellets than for meal feed,it can reduce much more waste.
- Easy dosing: Using pig feed pellet makes dosing easier and more accurate,the user can add additives in the mixing steps.
- No separation: In general, pellets have a 15% higher bulk density compared to the meal,heavy particles such as minerals and the like do not segregate, hence it is not possible for the pigs to be selective,it will make their feed much more balance.