With sweet potato starch or potato starch or bean starch as the main raw material crystal vermicelli production line, by pulping (pasting), forming, cooling, drying or not drying (refrigeration or freezing > and other processes made of non-edible food crystal vermey machine in strips or filaments.
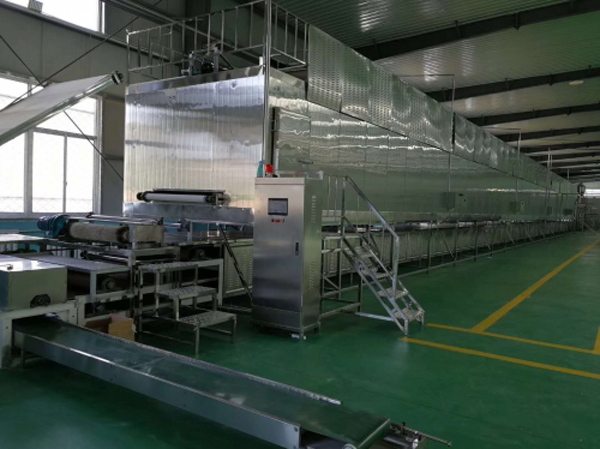
3-12tons/day of large automatic vermicelli production line
1, according to customer needs, can be designed separately.
2, steam boiler demand side.
A. If you have more information or special use requirements, please call the company’s sales hotline or visit the company’s production workshop to get an intuitive production process.
B. The configuration and parameters of this promotional material are for reference only, and the specifications should be recommended by the company’s sales staff and discussed with customers according to the needs of users.
automatic vermicelli production line
Based on the process of producing crystal vermicelli (bar) with starch as raw material, the equipment structure matches the production process requirements of crystal vermicelli (bar). In the production, large capacity mixer is used to stir, frequency conversion speed regulation to adjust the thickness of the powder sheet, frequency conversion speed regulation to adjust the aging time. The horizontal straight strip cutting method is adopted to make the strip shape uniform. Entrainment type drying, so that the dried vermicelli (strip) shape straight. The production of crystal fans, high quality, beautiful appearance, crystal clear, cooking resistance, foam resistance, not muddy soup, continuous strip, non-stick.
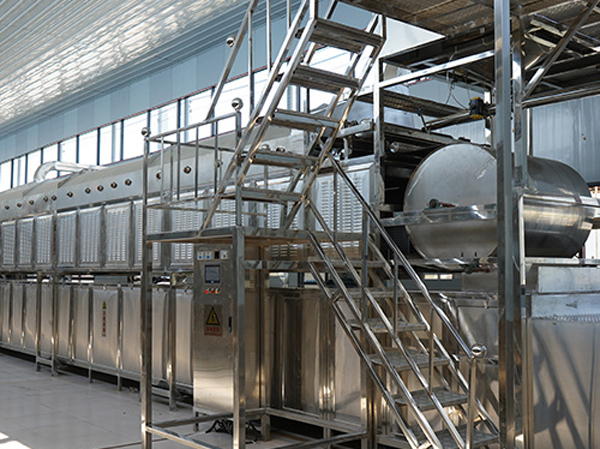
Process flow of automatic vermicelli production line
Process flow: preheating → spiral stirring (constant temperature storage) → vacuum stirring → scraping molding → steaming (steam) → cooling → disconnecting → normal temperature aging → low temperature aging (cold storage) → vertical cutting → quantitative weighing -→ bowl filling → automatic molding → continuous drying → moisture removal → cooling → finished product packaging.
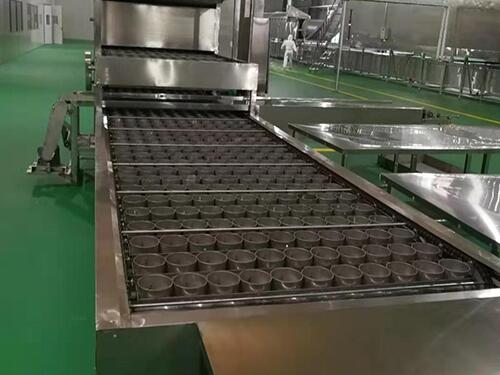
Automated instant vermicelli production line
- Fully automatic vacuum extraction process improves product brightness and reduces bubbles.
- Stainless steel paste scraper molding reduces thickness errors and ensures that product thickness is completely controllable.
- Steel belt full chain transmission improves the service life and flatness of steel belts, mesh belts (driven by conveyor belts), and powder belts.
- Aging: Once used at room temperature, closed brake, constant temperature and humidity, natural aging automatically switches to low-temperature aging system.
- The drying oven adopts multi-layer drying, which improves the heat utilization rate and adds a steam heat exchanger waste heat reuse device, making it more energy-efficient.
- High degree of automation, chain drive; From quantitative weighing into the machine to integrated production of finished product packaging; The operating speed is adjustable.
- High hygiene standards for finished products; During the closed operation of powder, the food contact parts are all 304 stainless steel.
Process flow of automated instant vermicelli production line
Process flow: preheating → spiral stirring (constant temperature storage) → vacuum stirring → scraping molding → steaming (steam) → cooling → disconnecting → normal temperature aging → low temperature aging (cold storage) → vertical cutting → quantitative weighing -→ bowl filling → automatic molding → continuous drying → moisture removal → cooling → finished product packaging.
Vermicelli production line flow explanation
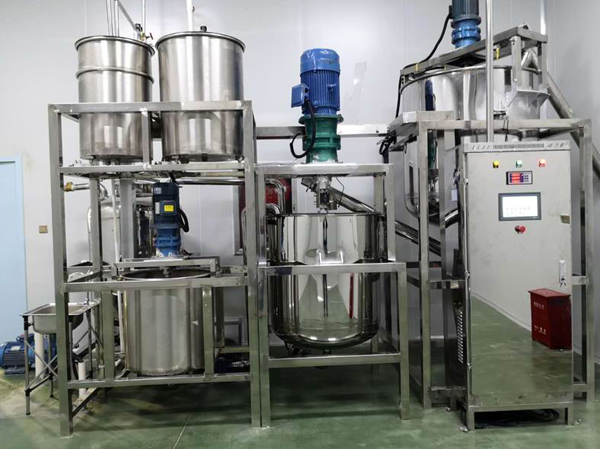
Fully intelligent pulping equipment
Raw material preparation : First choose the appropriate starch as the raw material, such as the national standard starch, and starch beating, the water and starch in proportion into the mixing bin.
Vacuum pumping
Through vacuum pumping can effectively prevent the production of vermicelli bubble, while increasing the hygiene of the product.
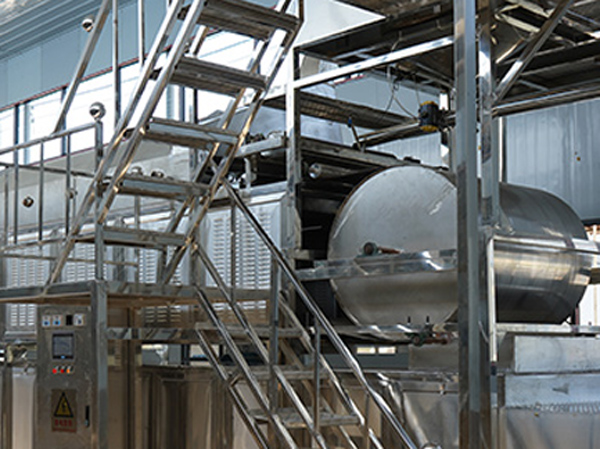
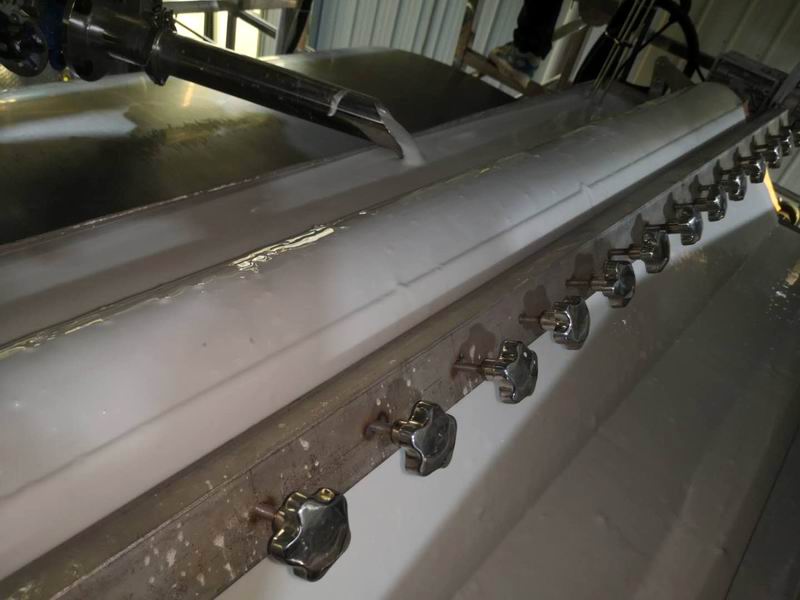
Coating slurry laying process
Laying: Adopting a coating laying process can more accurately control and adjust the laying thickness, ensuring the uniformity and quality of the vermicelli.
Steam stage
Using its own steam box system, it can steam through intelligent temperature control.

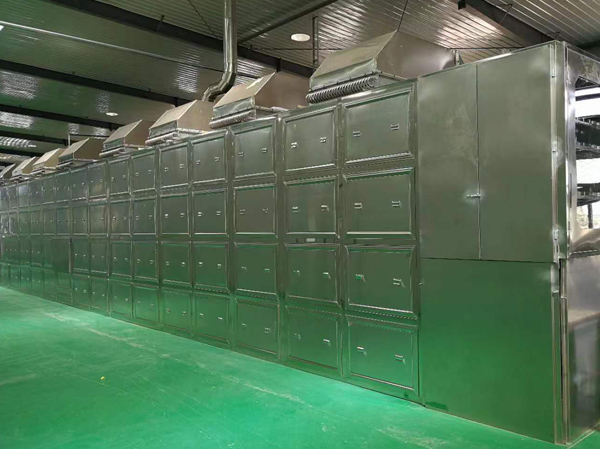
Crystal vermicelli drying.jpg
With its own drying system, there is no need for drying space, and the finished products are packaged directly.
The silk cutter
Adjust the length and thickness of the finished wire cutting product according to the demand to ensure that the product specifications meet the market demand.
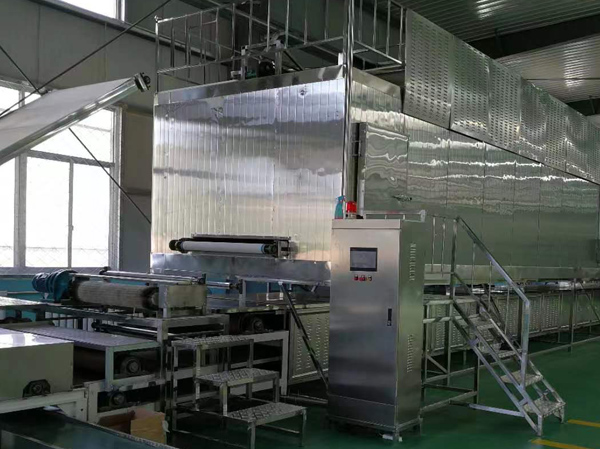
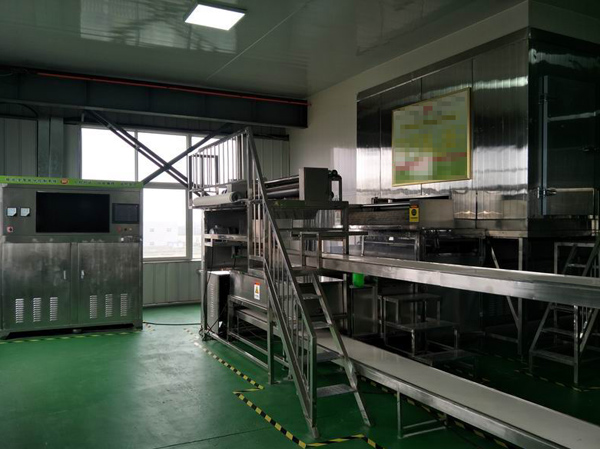
Finished product packaging
Finished product packaging : The cut vermicelli are weighed and packaged directly, ready for sale.
Instant crystal vermicelli drying
Crystal vermicelli undergoes a process of spreading, steaming, and then shredding into vermicelli. Crystal vermicelli is then placed in a bowl drying device according to its desired weight and dried at high temperatures to become ready to instant vermicelli
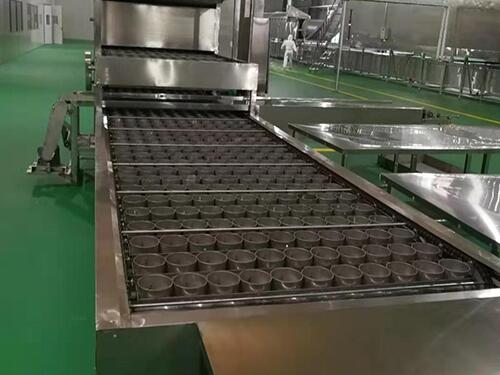
Highlights of Vermicelli Production Line Technology Upgrade
A、 The widening and lengthening of the cold storage has extended the freezing aging time of the powder strip, resulting in stronger toughness of the product
B、 Raise the oven, increase the number of drying layers, prolong the drying time, and improve the product’s gluten;
C、 Using vacuum stirring, the product has fewer bubbles and higher brightness;
D、 Suitable for a wider range of raw materials, with adjustable and controllable space;
E、 Lower equipment energy consumption and greater profit margin;
F、 Technological upgrades have greatly improved product productivity, resulting in significant returns and profits. The whole machine has design features, compact equipment, energy saving and consumption reduction, small footprint, high degree of automation, low production labor, uniform quality of terminal products, high yield rate, and high return on investment. The significant advantages of the equipment include: achieving fully automatic, fully enclosed, multifunctional, automatic feeding, automatic temperature control and other integrated production, with high-tech content and high added value. It is a good choice for enterprises engaged in convenient fan (strip) machine scale and original ecological production.
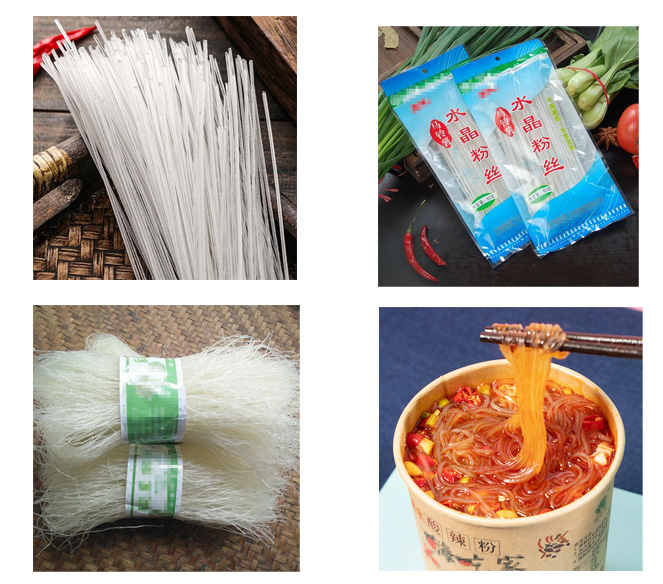
The production line of crystal vermicelli (strips) is fully enclosed and automated, from starch entering the machine to finished vermicelli exiting the machine. The entire production process does not use any additives (alum), preservatives, or food coloring, fully reflecting the production concept of green and nutrition. It can produce various types of crystal vermicelli according to different production areas, market demands, and consumer groups. The products produced have a neat appearance, uniform strip shape, uniform color, crystal clear and transparent, clean and hygienic, easy storage, and convenient transportation. Durable and long-lasting, with a chewy and refreshing taste, it is a nutritious and reassuring food that people pursue for health. The equipment is not affected by weather and seasons during the production process. The equipment operates at low speed, with a line speed of around 3.5 meters per minute, making it easy to operate. Through practical application in the production process, the machine has increased its output by more than 25% compared to similar products in the market without increasing its original size and ensuring product quality.
Infrastructure requirements:
- Factory design: (minimum required size)
A. 11-12 ton vermicelli production line: 80 meters long, 8 meters wide, and 6 meters high
B. 9-10 ton vermicelli production line: 75 meters long, 8 meters wide, and 6 meters high
C. 7-8 ton vermicelli production line: 75 meters long, 7 meters wide, and 6 meters high
D. 4-5 ton vermicelli production line: 50 meters long, 7 meters wide, and 6 meters high
E. 2-3 ton vermicelli machine production line: 40 meters long, 7 meters wide, and 6 meters high
- The indoor floor is flat and can be secured with foot screws;
- Ventilation and transparency, no dust pollution, convenient water supply and drainage, equipped with water, electricity, and steam that match the equipment.