Pre mixed sugar powder processing production line equipment: The company uses vacuum conveying system, powder conveying, powder pneumatic conveying system and other equipment, with material non layering, non wear material, powder conveyor scheme, effective elimination of static electricity, stable use, etc. The vacuum conveying system is a conveying equipment for powder materials, granular materials, powder granules, and mixtures.
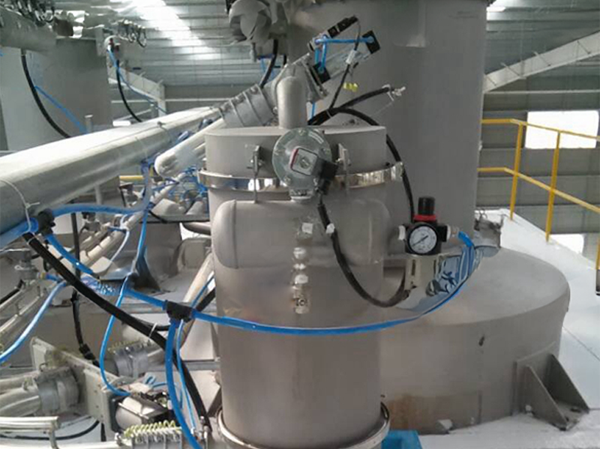
Pre mixed sugar powder processing production line
Processing capacity: 50-2000 tons/d
Application scope: Particle and powder materials
Product Introduction: Sugar cane, white sugar, glucose powder mixed in proportion
Pre mixed sugar powder processing production line equipment: The company uses vacuum conveying system, powder conveying, powder pneumatic conveying system and other equipment, with material non layering, non wear material, powder conveyor scheme, effective elimination of static electricity, stable use, etc. The vacuum conveying system is a conveying equipment for powder materials, granular materials, powder granules, and mixtures.
It is mainly a finished powder made by mixing 88% sugar with 12% glucose or other additives through the ingredient system, and its main properties are added to auxiliary foods such as food and beverages. This production process includes processes such as raw material transportation, temporary storage of ingredients, material mixing, and finished product packaging, and is equipped with auxiliary systems such as ventilation and dust removal, electrical control, and packaging. There are mainly the following sections:
Raw material transportation sequence; (2) Material batching and mixing; (3) Finished product weighing and packaging process;
We design and layout according to the different needs of our customers, providing services ranging from whole plant planning, equipment selection, installation and commissioning to operation training and maintenance.
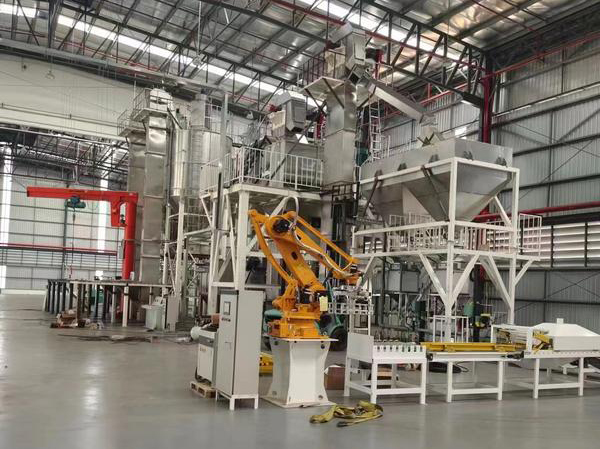
2.It includes the crushing, grading, purification, drying, conveying, mixing, testing, packaging, and environmental dust removal of powders. A closed powder conveying equipment and system that can isolate the pollution and harm caused by dust to the working environment, surrounding environment, and operators is important in the powder material handling process.
3.The air conveying system can automatically transport various materials to the hoppers of packaging machines, injection molding machines, crushers, mixers and other equipment, and can also directly transport mixed materials to the mixer. As it is a closed conveying, it solves the problem of dust overflow during feeding.From automatic feeding, warehousing arch breaking, pneumatic conveying, metering and batching, mixing and screening, homogenizing and stirring, to PLC intelligent control system, we are committed to providing customers with a series of material automation processing solutions.
1000 tons of pre mixed powder production line in the bonded zone
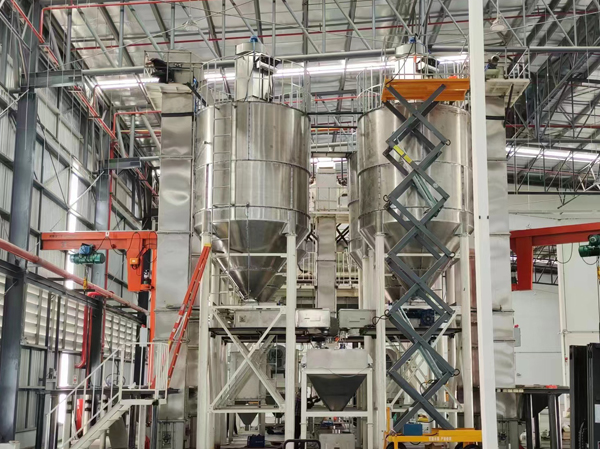
1000 tons of pre mixed powder production line in the bonded zone
The daily production line of 1000 tons of pre mixed powder in Jinan Free Trade Zone, designed, manufactured, and constructed by the company, mainly uses a computer batching system to accurately mix white sugar and auxiliary materials into finished pre mixed powder, which is used as a food auxiliary material additive.
The entire production line adopts scientific design technology and professional production equipment, combined with the different needs of customers in the comprehensive bonded zone, targeted design, reasonable layout, efficient production, and rapid production, helping customers seize market opportunities. While meeting personalized needs, we provide one-stop services from whole plant planning, equipment selection, installation and commissioning to operation training, maintenance, and subsequent upgrades.
Introduction to Process Flow:
The production line for 1000 tons of pre mixed powder in the bonded zone designed for this project is mainly used to accurately mix white sugar and auxiliary materials through a computer batching system, and evenly mix them to make finished pre mixed powder, which is used as a food auxiliary material additive.
The entire production line is built inside the existing standard factory building, divided into a raw material feeding purification workshop, a pre mixed powder mixing and processing workshop, and a finished product packaging and storage workshop. The main processing equipment is installed in the form of a steel frame platform. The batching and mixing processing workshop covers an area of 11x7m, with a height of about 14m. The raw material feeding and purification workshop covers an area of 100 square meters, and the fully automatic packaging and palletizing line covers an area of 12x5m.
Main processing technology: After the raw materials white sugar and auxiliary materials are fed into the purification workshop feeding platform, they are sent into stainless steel seamless pipes through a closed air feeding valve, and enter the batching bin through negative pressure dilute pneumatic conveying. The automatic weighing and batching process is used, controlled by a computer, with precise batching and high automation, saving labor; After the ingredients are completed, in order to reduce the height of the rack, negative pressure dilute pneumatic conveying is used again to temporarily store in the mixing bin, and then mixed in the mixer. The evenly mixed finished products are directly dropped and enter the packaging process. The fully automatic packaging line is used to automatically bag, weigh, sew and seal the mouth. Finally, the high-level palletizer automatically stacks the products, and the forklift sends them to the finished product stacking area.
The entire production process is concise and clear, with a high degree of automation, which reduces the labor cost of the enterprise and improves economic efficiency; The material is conveyed using negative pressure pneumatic conveying, which has no residue or cross contamination, and is convenient for pipeline cleaning, improving the hygiene and safety of production.
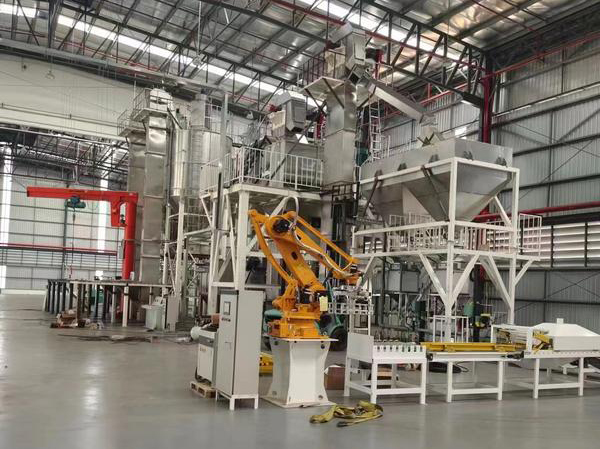
The process characteristics and section introduction of the 1000 ton per day pre mixed powder production line in the bonded zone:
1、 Raw material receiving process
Store the required raw materials for production in the purification feeding workshop in advance. During production, each raw material is fed into the feeding hopper according to the formula requirements and sent into the stainless steel seamless pipeline through a closed air feeder. The material is then pumped to the designated batching bin by a Roots blower
2、 Ingredient process
After the materials enter the batching bin, the batching system automatically discharges the materials in sequence according to the formula, controlled by the batching program, and enters the batching scale for measurement. The entire process is controlled by a computer. The dynamic batching accuracy error of the batching system is ≤ 3 ‰, and the static batching accuracy is ≤ 1 ‰, with high accuracy and efficiency.
3、 Mixing process
In order to reduce the height of the entire production line, materials are conveyed to the mixing bin through negative pressure pneumatic conveying after batching is completed, and then enter the stainless steel single axis blade mixer for mixing. The mixing time of the mixer is about 120-300 seconds (the specific time is adjusted according to different formulas), and the mixing uniformity is ≥ 95%.
4、 Finished product packaging process
The mixed materials enter the packaging system, which is a fully automatic packaging line with automatic bagging, weighing, sewing, and sealing. Finally, an automatic high-level palletizing system is used, and the products are transported to the finished product stacking area by forklift.
5、 Auxiliary process
Workshop dust removal: After raw material feeding and batching are completed, they enter the mixer and are all transported by negative pressure pneumatic conveying system, without dust overflow; The packaging area is also equipped with a suction hood for dust removal.
6、 The equipment area is fully enclosed and separated, and personnel must undergo air shower and purification before entering the equipment processing area; After feeding, the raw materials should be cleaned up in a timely manner, and the conveying system should be kept idle for more than 2 minutes to ensure that various raw materials do not cross contaminate during the conveying process.