The complete set of machine technology for oat processing is developed based on the characteristics of oats at home and abroad. It is suitable for the processing of oat hulls and tablets, and has high automation capabilities. It locks in the nutrients of oats, and the soluble fast food oat flakes can be well absorbed by the human body, which conforms to the modern pace of life. Simultaneously supporting oat flour production and oat cleaning machine.
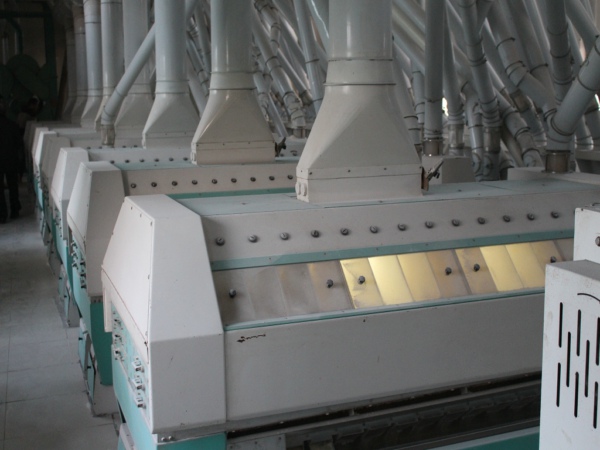
Finished product:Oatmeal, oat groat, instant oat flakes
Production capacity:200kg/h-1000kg/h
Core equipment:Suction Cleaner, Oat Scourer, Indented Cylinder Grader, Oat Huller, Hulls Separator, Oat Color Sorter, Oat Steaming Screw, Drying Box, Oat Drum Groat Cutter, Flakeing Mill, Fluidised Bed Drier, Plansifter, Aspiration Channel, Packing Machine
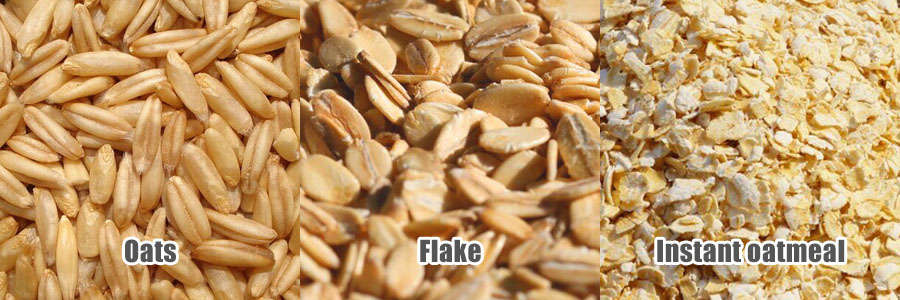
We offer a wide range of oat processing equipment, which includes the heart of our oat mills – the dehuller, kiln and flaking roller mill. We can help all the way – from planning your production line to installation, training and maintenance. Our oat processing is also highly automated, helping to improve yields and trace your product from intake to bagging.
The following overview shows all machines which are used for the processing of oats
Oat Cleaning Process
Pre-cleaning:
Pre-cleaning is key for an efficient and safe milling process. Grain contains impurities and foreign materials. If you remove these before storage, you can extend the service life of your machinery and provide hygienic storage conditions for your grain.
Cleaning:
Use the cleaning section to remove impurities, defective material and contaminants, including fungus. We offer both mechanical and optical sorting machines.
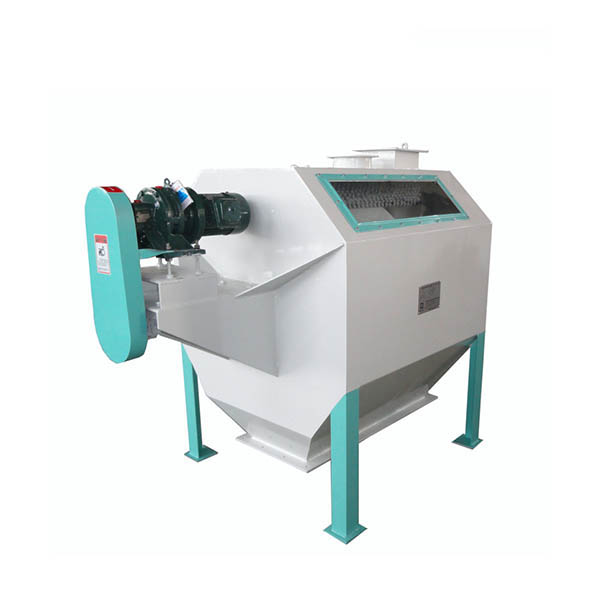
Drum type pre-cleaner
This machine is a pre cleaning equipment often used in grain storage, grain processing and other enterprises.
It is mainly used for cleaning the size of impurities in grain and granular materials, such as stones, hemp rope, sand and dust. It has the characteristics of large output, low energy consumption, high efficiency, stable and reliable operation.
The cleaning effect and output of different materials can be adjusted by adjusting the angle of screen cylinder.
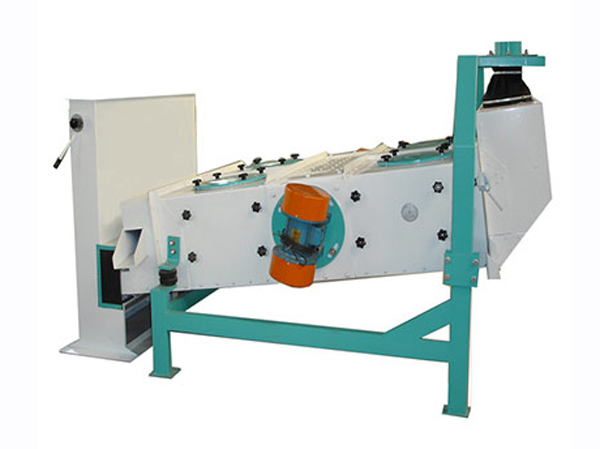
Vibrating Screen
Product Description:This machine is a pre cleaning equipment often used in grain storage, grain processing and other enterprises. It is mainly used for cleaning the size of impurities in grain and granular materials, such as stones, hemp rope, sand and dust.
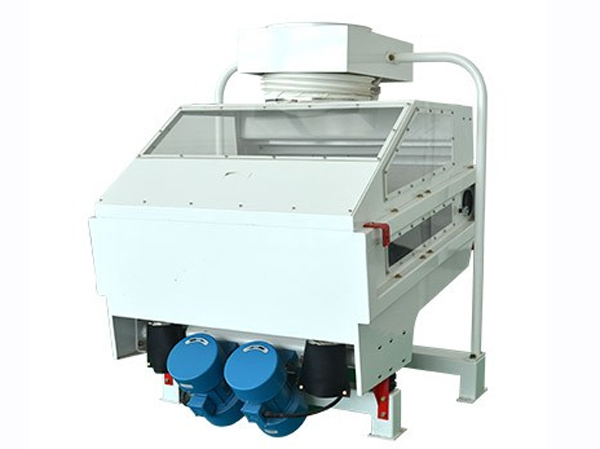
Universal Gravity Destoner
Besides the standard application of wheat, rice and corn, Gravity Destoner can also be used in the special processing of oat, buckwheat, barley, speles wheat and millet, and have been successfully applied in the production of wine making, distillation and ethanol products;
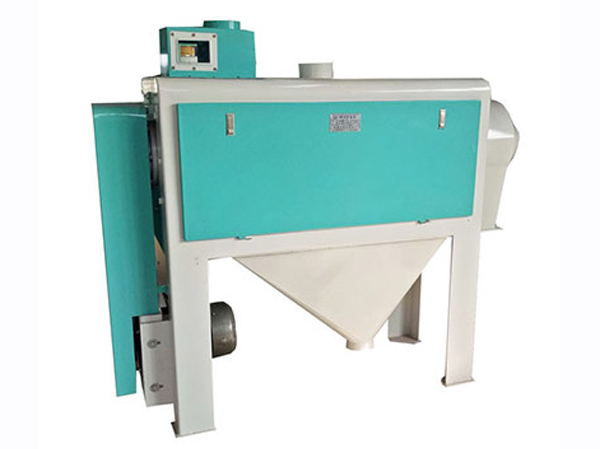
Horizontal Wheat Scourer
The scourer improves the hygiene of grain during processing by removing impurities such as earth, dust, and sand. It is mainly used in the first and second cleaning sections to treat the surface of wheat, durum and rye.
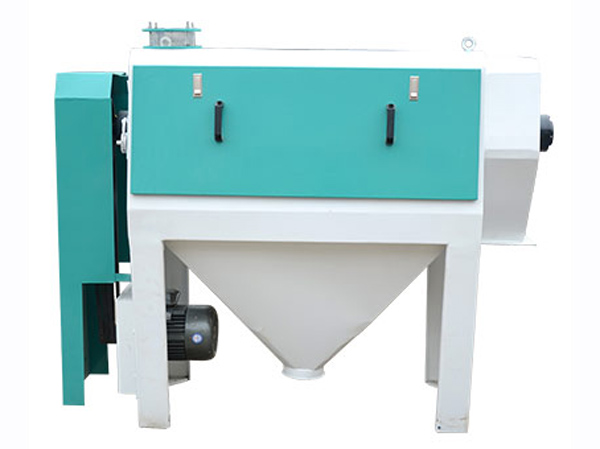
Powder/Bran Brushing Machine
The flour brushing machine can effectively separate and extract the flour adhering to the surface of the material, so as to improve the flour yield and the cleanliness of the finished product. It is used in corn and bean processing line.
Oat Dehulling and Kilning Process
Dehulling:
Hulling removes the indigestible husk from the kernel. The groats are then separated so that only top-quality groats enter the kiln.
Kilning:
Hydrothermal treatment of the oats in a kiln increases shelf life, reduces total germ count and produces the typical nutty taste.
Centrifugal Oat Huller
Oat huller is designed with centrifugal type for precise and efficient hulling of oats. Oat kernels are throws out under the action of a high-speed rotating centrifugal disk. There are some guide paths in the centrifugal disc to make oat grains keep a fixed direction and impact the surrounding circle, sothat the husk is separated from the kernel and deflected downwards to the two product outlet pipes. It is a professional hulling machine for Chinese naked oats or Australian hulled oats. The energy consumption of equipment operation is low, and the production line can run stably and continuously
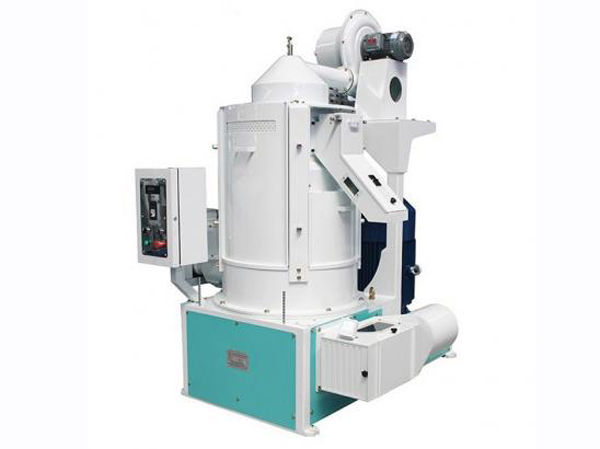
Gravity Paddy Separator
The friction coefficient produced by different specific gravity of husk and brown rice was used to separate husk and brown rice under the action of reciprocating shaking sieve plate.
In the use of rice, millet, oats grain processing line, the shelling and shelling products can be effectively separated to prevent excessive processing of rice and improve the economic benefits of processing.
Low noise, low energy consumption and large sieve area;According to different kinds of coarse cereals, the convex or concave convex sieve plate was selected to improve the separation effect; Matching the suction and dust removal device to improve the workshop production environment.
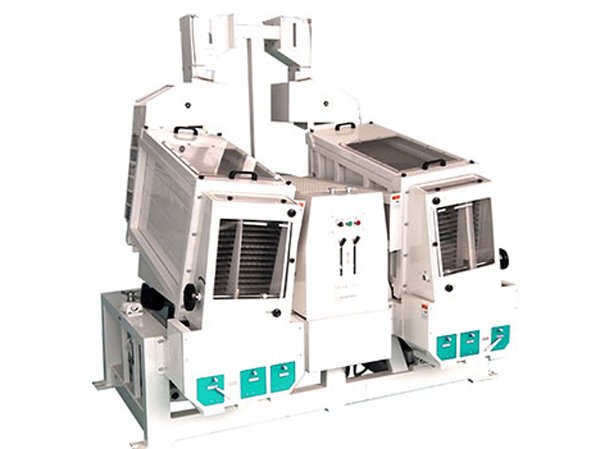
Oat Cutting and flaking Process
Complete oat kernels or cut groats are then steamed ready for flaking. In the flaking mill, starch gelatinization increases the nutritional properties of the oats. Flaking also helps to produce a good-looking end product.
Cutting, aspiration, grading.
The groats cutter cuts the dehusked oats. An indented separator removes the uncut groats.
Steaming, flaking.
Uniform steaming ensures optimal preparation of the product prior flaking. In the flaking roller mill, starch gelatinization promotes the food-specific values of the oats while at the same time ensuring an attractive appearance of the end product.
The steamer in conjunction with the flaking roller mill and the fluid-bed dryer fulfills the highest sanitation requirements and ensures a consistent flake quality.
Our flaking roller mill has a constant high roll pressure, to produce a high-quality and uniform product with highly automated, helping to improve productivity.
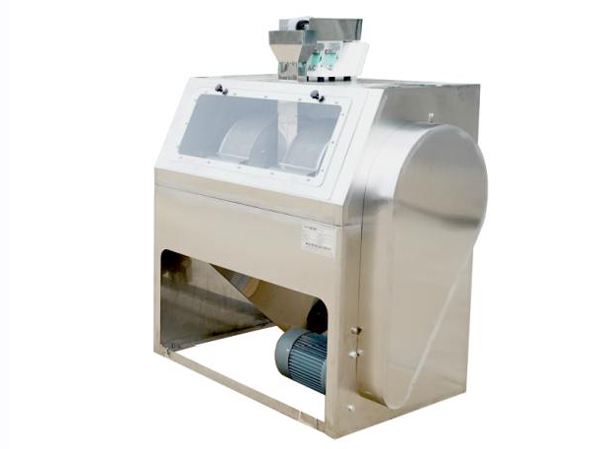
Stainless Steel Oat Groat Cutter
Oat roller granulator is the core equipment in the oat processing project. It is commonly used for granulation of oats, barley, rye, rice grains, especially in the oat press processing section to produce evenly sized pointy oats.
Among them, the oatmeal granulation is cut into 1/2-1/4 size granules by rotating barrel granulator.
The granulation is for the overall size of the oatmeal is the same when the oatmeal is pressed, and it is easy to be pressed into flakes and not powder.
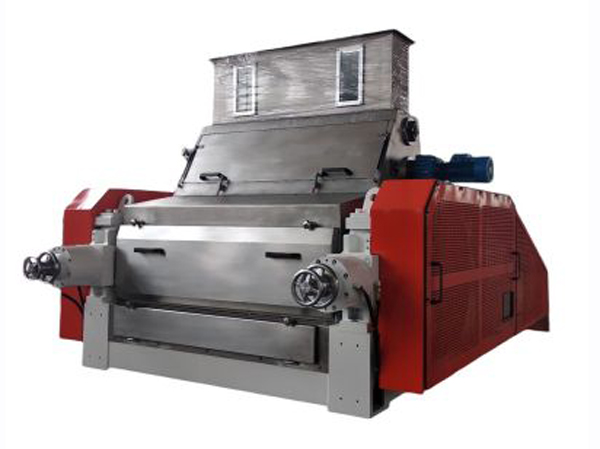
Roller Flaking Mill
Oat Flaking Mill is used to squeeze the grain grains such as oats and corn.Through the relative rotation of the counter roller, the granular material is extruded into a thin flakes.
Besides,the frequency conversion speed reducer is used to accurately distribute the material evenly to the whole roll length range.Therefore,the finished products of the tablet are evenly distributed and are less broken.In addition, the thickness of the finished grain slice can be adjusted by adjusting the clearance between the counter rollers.
Oat Bagging and load out
Bagging and load out:
The finished products are either bagged or loaded in bulk. It is important to handle the flakes gently. Precise dosing and weighing are also key. We offer a wide range of manual and fully automated loading and bagging systems.
Color sorter
Intelligent operation interface, visual analysis of images, one-click analysis of the proportion of impurities to be removed and transfer of sorting parameters, easier operation;
Support remote control for mobile phone apps and monitoring equipment operation, convenient and fast;
Support Internet remote control, system upgrade function, HD image acquisition, visual system adaptive correction technology, self-learning statistical analysis technology, and one-key automatic parameter adjustment technology;
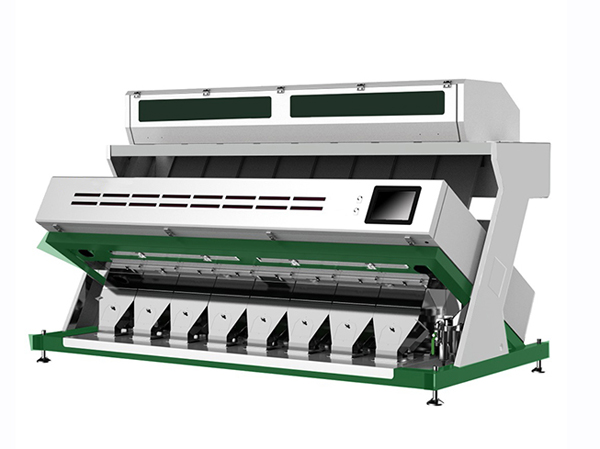
Computer Measuring Packaging Machine
packing scale is suitable for accurate measurement and packaging of finished materials for coarse cereals, grain processing enterprises, starch enterprises, chemical industry and other industries.
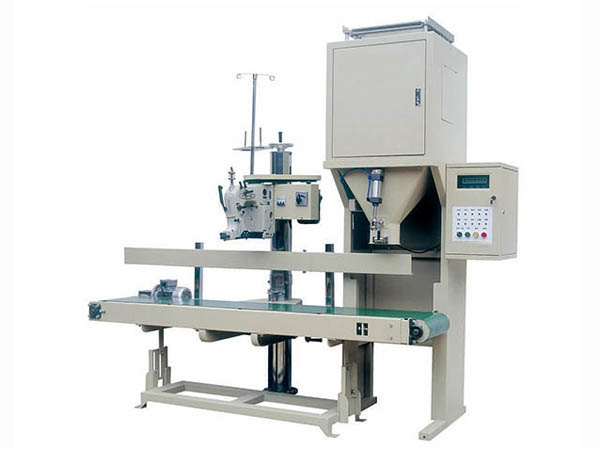
Oat Flour Milling Process
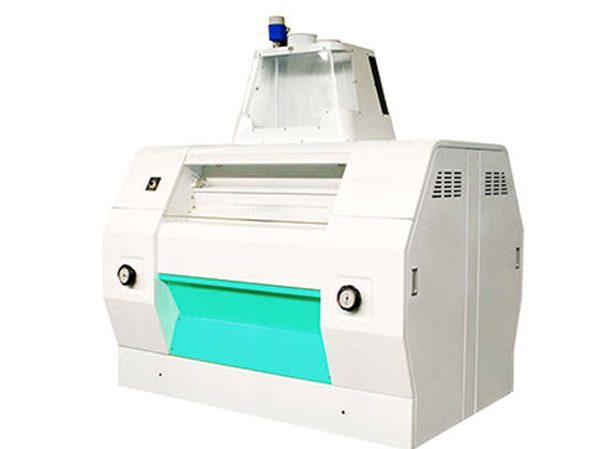
The double roller mill has a simple maintenance system, high efficiency and low noise. It can be supplied four or eight horizontal rolls with a diameter of 250/300mm. It has level sensors and continuous and balanced feeding, with feeding rolls control to ensure and improve the efficiency of milling. All the rotating parts are controlled by speed sensors and the control system ensures the immediate process shutdown in case of incorrect working. The structure allows the immediate rolls substitution, the cleaning and emptying system.