With the popularity of natural gas, especially the promotion and application of liquefied natural gas (LNG) and compressed natural gas (CNG), natural gas has become the preferred fuel for newly-built coke oven ovens, when natural gas gas source is available, natural gas ovens are selected, and the temperature control is accurate, which not only has good oven effect, high safety, convenient management, and low cost.
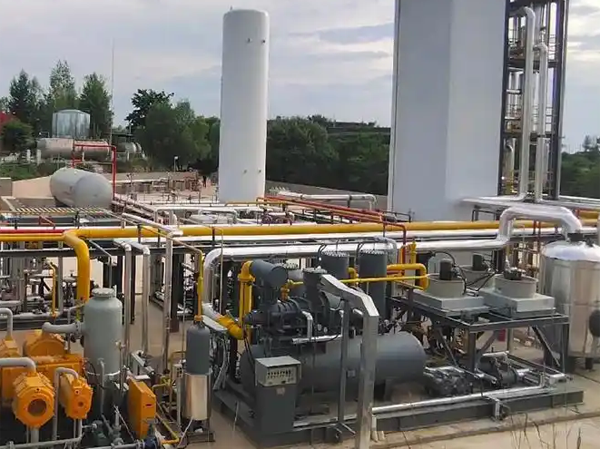
Natural gas liquefaction production plants
Natural gas is a multi-component gas mixture whose composition varies with the field. The main component is methane, accounting for about 80%, followed by nitrogen, C2 ~ C5 alkanes, water vapor, and a small amount of hydrogen sulfide, carbon dioxide and helium. The complete set of natural gas liquefaction equipment includes natural gas impurity removal pretreatment and purification equipment, natural gas liquefaction and storage equipment, liquefied natural gas regasification and cold recovery equipment, as well as safety technology system. Natural gas liquefaction equipment is divided into two categories according to the use of basic load type and peak load type. The former has a large processing capacity and large equipment set, and is mainly used for on-site liquefaction of associated gas in oil fields. Liquefied natural gas is transported by tanker, or by infusion pipeline into the transport cabin for ocean transport. The peak-type equipment is small and is often used for air supply load regulation or civil fuel supplement.
There are three kinds of natural gas liquefaction cycle: cascade refrigeration cycle, mixture refrigeration cycle and liquefaction cycle with expander, which can be selected according to the composition of natural gas and the scale of processing capacity. Natural gas must be pre-treated before liquefaction to remove hydrogen sulfide, moisture and carbon dioxide. Natural gas with higher nitrogen content must also be treated with nitrogen removal. Natural gas pretreatment generally adopts purification equipment corresponding to absorption method and adsorption method.
A low energy consumption cascade refrigeration cycle is commonly used to liquefy natural gas in the liquefier section (Figure 2). It uses a cascade refrigeration cycle consisting of propane, ethylene and methane refrigerants. Propane is compressed by a compressor and cooled by a water cooler to liquefy. Liquid propane is depressurized after throttle and cooled to approximately 232K, liquefing the compressed ethylene in a propane cooler. The liquid ethylene is depressurized by a throttle valve and cooled to 173K, where the compressed methane is liquefied in an ethylene cooler. Liquid methane is depressurized and cooled to 113K after a throttle valve, where the gas is liquefied in a methane cooler. Propane, ethylene, and methane are evaporated and reheated before returning to their respective compressors. The pre-treated purified natural gas is cooled in propane and ethylene coolers, then condensed and slightly supercooled in methane coolers, and finally pumped into storage tanks.
Natural Gas Dehydration Unit
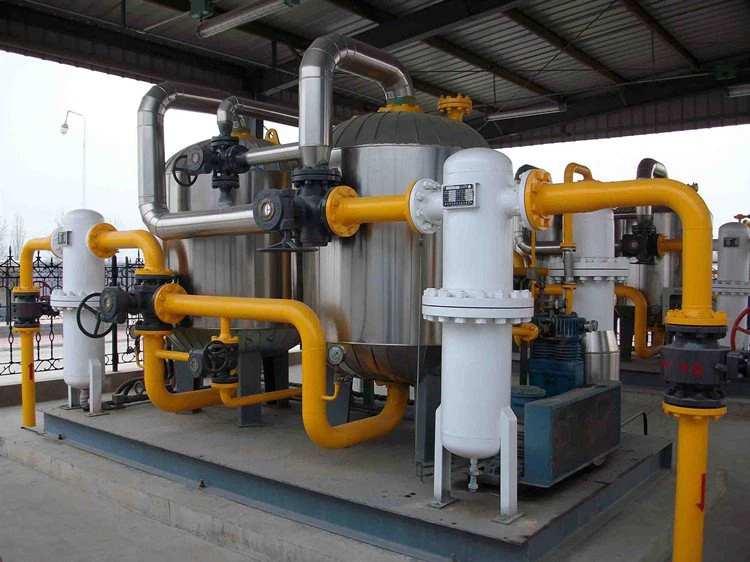
Natural Gas Dehydration Unit
Natural Gas Dehydration Unit is an essential product for oil and gas industries, providing high-quality gas with low dew point. Our product helps to remove water vapor from gas streams, making it ready for transportation and usage. Our manufacturing plant is situated in China, which is equipped with advanced machinery and highly-skilled personnel to produce high-quality and efficient equipment.
Features:
Our Natural Gas Dehydration Unit comes with several features that make it stand out from our competitors. Firstly, it has an innovative design that maximizes its performance while minimizing its footprint. Secondly, it is effortless to operate and maintain, making it convenient for users. Lastly, it is made of high-quality materials to withstand harsh weather conditions, ensuring durability and reliability in its performance.
Advantages:
Our Natural Gas Dehydration Unit provides several advantages to the users, making it an ideal choice for the oil and gas industry. Firstly, it offers a low-cost solution to remove water vapor from gas streams, saving users from expensive alternatives such as refrigeration and chemical drying. Secondly, it reduces the risk of pipeline corrosion and damages caused by water vapor, protecting users’ investment in the pipeline network. Lastly, it is environmentally friendly, as it does not require any chemicals or refrigerants that pose a threat to the environment.
Applications:
Our Natural Gas Dehydration Unit is suitable for a wide range of applications in the oil and gas industry. It is commonly used in natural gas processing plants, gas gathering stations, and transmission pipelines to remove water vapor. It is also used in gas storage facilities and gas-fired power plants to ensure clean and efficient fuel supply.
Conclusion:
Our Natural Gas Dehydration Unit is an efficient and cost-effective solution for users in the oil and gas industry. Its innovative design, high-quality materials, and low-cost operation make it an ideal choice for various applications in the industry. We are committed to providing our customers with the best product quality and service, and we welcome all interested parties to contact us for further inquiries and orders.
Product Information
The Natural gas dehydration unit adopts the principle of temperature swing adsorption, and the adsorption is carried out at normal temperature and high water vapor partial pressure. The regeneration is carried out at a higher temperature and a lower partial pressure of water vapor, that is, the moisture absorbed by the adsorbent during the adsorption process depends on the high-quality regeneration during the regeneration process and can be completely removed by the action of the thermal diffusion mechanism (heated by dry air) of the air. The whole set of equipment consists of two parallel drying towers, heaters, circulating fans, coolers and filters.