The complete set of technology for plant essential oil extraction production line and multifunctional static extraction tank are suitable for various process operations in the traditional Chinese medicine, plant, animal, food, and chemical industries, such as atmospheric pressure, pressurized water decoction, warm soaking, hot reflux, forced circulation, percolation, aromatic oil extraction, and Ji solvent addition. They have the characteristics of high efficiency and easy operation, and are widely used in the pharmaceutical, food, chemical and other industries. This equipment can be selected in the form of straight tube, regular cone, oblique cone mushroom according to the extraction process.
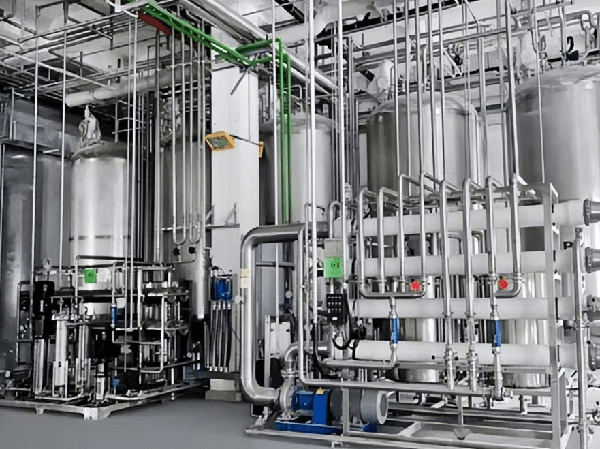
Manufacturer of plant essential oil extraction production line
We have extensive industry experience and professional skills in the field of plant essential oil extraction production lines. Not only does it provide comprehensive services from project planning, equipment design to installation and commissioning, and technical training, but it also constantly innovates and integrates concepts such as automation, intelligence, and environmental protection into the design of production lines, creating efficient, environmentally friendly, and customized solutions for extracting medicinal plant essential oils for customers.
Working principle of plant essential oil extraction production line
(1) Such as water extraction: Water and traditional Chinese medicine are loaded into the extraction tank, and the interlayer heat source is started. After the tank boils, the supply of heat source is reduced, and the boiling inside the tank is maintained. The maintenance time depends on the extraction pharmacological process. If closed extraction is required, cooling water is given to cool the steam vapor and return it to the extraction tank, maintaining circulation and temperature.
(2) As for alcohol extraction: First, add the medicine and alcohol into the tank, which must be sealed. Steam the interlayer heat source, turn on the cooling water to reach the required temperature in the tank, and reduce the supply of heat source. The rising vapor state alcohol can be refluxed after passing through the condenser into liquid alcohol. In order to improve the Xiao rate, a pump can be used to force circulation, so that the medicine is sucked out from the lower part of the tank through the pump and then imported back into the tank from the upper part of the cylinder to relieve local channeling.
(3) Oil extraction: First, add the traditional Chinese medicine containing volatile oil and water into the extraction tank. Open the circulation valve of the oil separator, adjust the bypass reflux valve, and open the supply heat source valve. When the volatilization temperature is reached, turn on the cooling water for cooling. The cooled liquid should be kept at a certain height in the separator to separate it, and then use the oil-water separator alternately.
(4) Recycling oil essence: Add alcohol to the cylinder, open the cooling water for steam, and then open the recycling valve.
Extraction process of plant essential oil extraction production line
- Preparation of raw materials
(1) Harvesting of raw materials: Generally, fresh, intact, and clean plant parts are harvested at maturity.
(2) Storage and preservation of raw materials: Raw materials containing essential oils should be distilled immediately after harvesting to prevent mold and affect the quality of the oil. If not processed in a timely manner, it can be stored in a dry, cool, and well ventilated warehouse.
(3) Grinding of raw materials (selected according to the type of raw materials): Leaves are generally cut into shreds by machinery; Flowers generally do not need to be crushed and can be directly distilled; Fruits and seeds must be crushed into coarse powder or crushed; The roots, stems, and xylem are mechanically cut into thin slices or small sections, or crushed into coarse powder.
- The commonly used methods for extracting essential oils include steam distillation, extraction, and pressing.
Steam distillation method: Pour the raw materials into a container and add water, heat it, and steam and oil gas enter the condenser through the top outlet to condense. As the relative density of essential oil is lighter than water, it will float on the water surface. The essential oil on the water surface is the highest quality refined oil extracted from the first Ci. Flower water/crystal dew: Essential oils are slightly soluble in water, and a small amount of essential oil substances remain in the water that condenses together with the essential oils. These waters, like the essential oils, have therapeutic properties. Due to their low concentration, they can be used directly without dilution. This method is simple to operate, cost-effective, and is a commonly used and clean method for extracting essential oils. 95% of essential oils from aromatic plants can be extracted by distillation. The parts suitable for distillation extraction of aromatic plants are flowers, rhizomes, leaves, and sawdust.
Extraction method of plant essential oils:
Common methods for extracting plant essential oils include steam distillation, freeze compression (pressing), chemical solvent extraction, oil separation (liposuction), carbon dioxide extraction, and soaking. Distillation is the most commonly used method for extracting aromatic plant essential oils, and 95% of aromatic plant essential oils are extracted by distillation.
Distillation can be said to be an ancient and widely used method for extracting essential oils. The processing procedure involves heating plants with water or steam (or a combination of both) in a distillation vessel to remove the water vapor, thus producing a concentrated solution. The liquid mixture of oil and water produced by the above program usually floats on water, so water is heavier than oil. If the oil is heavier than water (such as clove oil), the oil will sink to the bottom, and it is easy to separate the oil and water.
Introduction to the operation method of static extraction tank:
- Alcohol recovery: With high recovery capacity, vacuum operation method is adopted, and the process flow of the equipment is improved. The recycling rate can reach over 95%, alcohol loss is less than 5%, and energy consumption is reduced by 30%. It is an energy-saving equipment with low investment and high recycling efficiency.
- After alcohol recovery, the equipment adopts external heating natural circulation and vacuum negative pressure evaporation, which has high evaporation speed and heavy concentration ratio. The liquid material is concentrated under the condition of full seal without foam.
- When collecting the paste, it is not necessary to do it inside the heater. Close the upper and lower butterfly valves of the heater and collect the paste at the bottom of the evaporator. The specific gravity can reach 1.35 or above.
- This device can automatically drain water, reducing labor intensity, and has semi-automatic function. When ordering, please indicate whether automatic drainage is required.
Installation instructions for multifunctional static extraction tank:
- After the equipment is positioned, it should be fixed on the platform with bolts or spot welding, and all four supports should be evenly stressed.
- The process pipeline relies on the gravity flow section of the liquid medicine, and a certain liquid level difference should be left in order to avoid liquid stagnation in the pipeline.
- The external pipeline at the joint of the quick change rotary pipe should be supported so that the rotary joint can rotate together with the slag discharge door cover, avoiding damage to the discharge connection hose of the slag discharge door.
- A liquid flow meter should be installed at the inlet of the liquid pipe to facilitate the recording of the liquid inlet volume.
- Steam pipes must be equipped with safety accessories such as pressure reducing valves, safety valves, and pressure gauges.