Fully automatic walnut milk production line: Walnut milk is a plant-based protein beverage made from walnut kernels Purified water is the main raw material, using modern technology Scientifically blended and refined, with a delicate taste It has a special walnut rich aroma and is a cold drink Hot drinks are acceptable, with a stronger aroma.
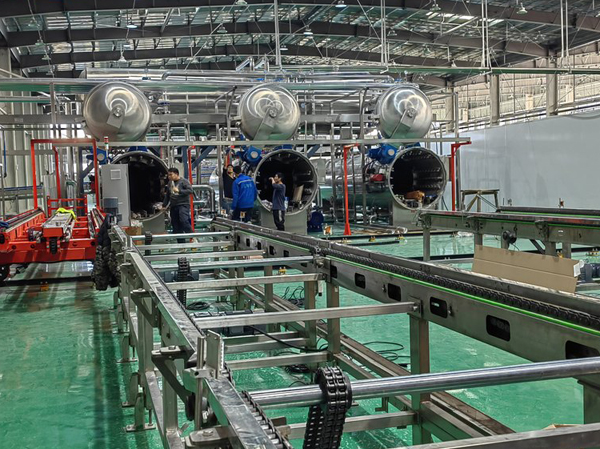
Manufacturer of fully automatic walnut milk production line
Main features of walnut milk production line:
(1) The machine has a compact structure, a complete control system, easy operation, and a high degree of automation;
(2) Changing the bottle shape only requires replacing the star wheel and arc-shaped guide plate of the cap part;
(3) All parts in contact with materials are made of high-quality stainless steel, with no dead corners in the process and easy to clean;
(4) Using high-speed filling valves, the liquid level is accurate without liquid loss, ensuring the requirements of the filling process;
(5) The sealing head adopts a magnetic constant torque device to ensure the quality of the sealing and will not damage the bottle cap;
(6) Adopting * * *’s lid system with complete self-control and protection devices;
(7) Equipped with comprehensive overload protection devices, it can effectively protect the safety of equipment and operators;
(8) The control system has functions such as production speed control, missing cap detection, automatic bottle stop, and output counting;
(9) The main electrical and pneumatic components are made of world-renowned products;
(10) The whole machine operation adopts advanced touch screen control, which can achieve human-machine dialogue operation.
Production process of walnut milk beverage:
Walnut kernels → selection → rinsing → soaking → peeling → color protection → grinding → filtering → blending → pre homogenization → vacuum deodorization → homogenization → filling → sterilization → cooling → inspection → finished product
Steps for making walnut milk beverage:
- Choose rinsing: Choose insect free No mold growth Fresh walnut kernels that do not spill oil should be rinsed with clean water to remove foreign substances such as mud, sand, and residual shells.
- Soaking: Soak the walnut kernels in clean water to make them absorb water and expand, soften the tissue, and facilitate peeling Grinding and extraction of nutrients. When soaking, the ratio of walnut kernels to water is about 1:2, and the soaking time is 4-5 hours, because later color protection treatment requires soaking for 3-4 hours.
- Peeling: Boil walnut kernels in a 3% NaOH solution for 3-5 minutes, then rinse with high-pressure water to remove the seed coat.
- Color protection: Soak the peeled walnut kernels in a mixture of 0.5% NaCl and 0.02% Na SO3 solution for 3-4 hours, perform color protection and bleaching treatment, and then rinse twice with clean water.
- Grinding: Using a grinding wheel grinder, the method of hot water grinding at 85 ℃ or above is adopted to passivate lipoxygenase. The ratio of water to walnut kernels is 7:1.
- Filtration: Use a 200 mesh centrifuge to separate the pulp and residue. To improve protein yield, the residue can be soaked and extracted with hot water, and the slurry can be used as water for the next grinding.
- Preparation: Mix white sugar Emulsifier. Dissolve thickeners, etc Filter, mix with walnut slurry according to the formula ratio, and stir evenly. Soft water with a hardness of less than 4 degrees should be used for mixing water to prevent protein aggregation caused by metal ions Precipitation phenomenon.
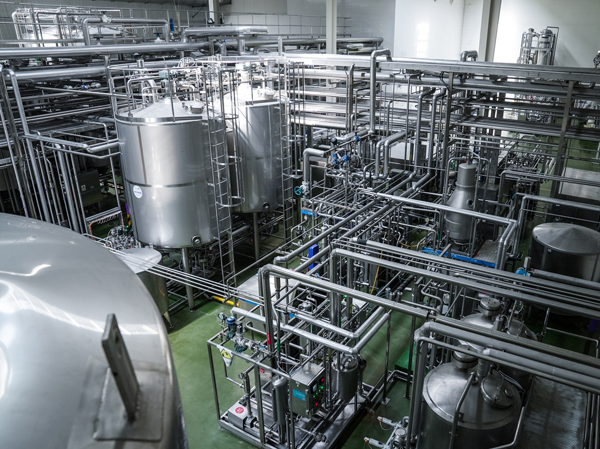
- Pre homogenization: Use colloid grinding once, which is called pre homogenization, to thoroughly mix and refine the material liquid for degassing, deodorization, and high-pressure homogenization.
- Vacuum deodorization: The feed liquid is deodorized in a vacuum deodorization tank under a vacuum degree of 20-30 kPa. It also plays a role in degassing. And quickly cool the liquid to below 85 ℃.
- Homogenization: Use a high-pressure homogenizer to homogenize the liquid twice, with a homogenization pressure of 40 MPa and a liquid temperature of around 75 ℃.
- Filling Capping: Fill while hot with a filling machine. For future observation convenience, this experiment will be conducted in glass bottles and sealed with a crown roller cap.
- Sterilization: Use a sterilization formula of 10-15 minutes/121 ℃ in a high-pressure sterilization pot for wet heat sterilization.
- Finished product storage: Bottled beverages that have been sterilized and cooled should be labeled and stored at room temperature.
Common packaging forms and equipment for walnut milk beverages:
- Composition of PET bottle production equipment: including water treatment system Original fruit processing system Deploy the system Automatic bottle blowing machine Wind power transmission line UHT ultra-high temperature sterilization machine Cover sterilization machine Lid cleaning machine Three in one bottle filling and sealing system Bottle sterilizer Cold bottle machine Blow dryer Labeling machine Spray coding machine Stacking machine Winding machine. Real bottle conveying system Container transport system A complete set of filling and packaging production lines, including electrical control systems. Optional equipment: automatic bottle sorting machine or manual bottle sorting system Full/semi-automatic bottle washing machine Fully automatic bottle unloading machine Bottle storage Labeling machine Carton packaging machine, etc. Production capacity: Our company has formed a complete series of product lines, with a supply capacity ranging from 2000 bottles/hour to 36000 bottles/hour (calculated based on 500ml PET bottles).
- Composition of can loading equipment: including water treatment system Original fruit processing system Deploy the system Fully automatic tank unloading machine Can flushing machine Filling and capping machine UHT sterilizer Cold can machine Tank platform Spray coding machine Liquid level detection machine Shrink film packaging machine Real tank transportation system A complete set of filling and packaging production lines, including electrical control systems. Optional equipment: cardboard packaging machine, etc. Production capacity: Our company has formed a complete series of product lines, with a supply capacity ranging from 1000 cans/hour to 30000 cans/hour (calculated based on 355ml cans)
- Composition of glass bottle equipment: It includes a water treatment system Original fruit processing system Allocation system Bottle washing machine Bottle preheating machine UHT ultra-high temperature sterilization machine Cover sterilization machine Filling and capping machine Bottle sterilizer Cold bottle machine Labeling machine Spray coding machine Packing machine Stacking machine Winding machine. Real bottle conveying system Container transport system A complete set of filling and packaging production lines, including electrical control systems. Optional equipment: If it is a new bottle, a fully automatic bottle unloading and stacking machine can be selected. Production capacity: Our company has formed a complete series of product lines, with a supply capacity ranging from 2000 bottles/hour to 36000 bottles/hour (calculated based on 250ml glass bottles)