Integrity of NFC Fresh Juice Production Line System: For products such as clear juice, cloudy juice, concentrated juice, and jam, the production line system includes cleaning, lifting, fruit inspection, crushing, juice extraction, preheating and enzyme inactivation, enzymatic hydrolysis, filtration, concentration, blending, degassing, homogenization, sterilization, filling, and final product packaging
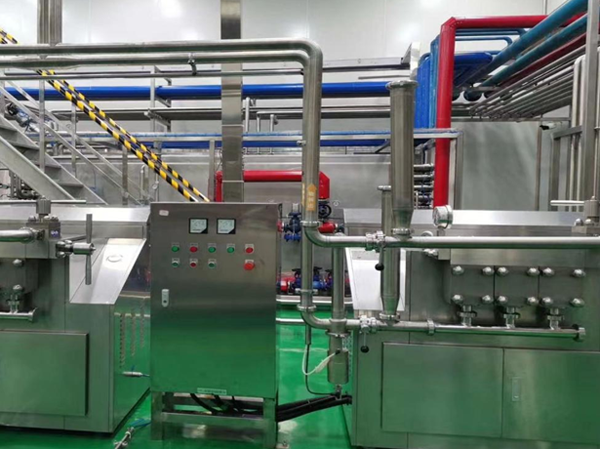
Manufacturer of automatic NFC juice production line
Most of fresh fruits or vegetables such as orange, apple, pineapple, kiwifruit, grape, berry fruits, watermelon, pomegranate, tomatoes, carrots, etc. can proceed into the NFC juice.
The processing capacity of the NFC juice production plant is 500L per hour to 10000L per hour, and most of the NFC juice will be filled into bottles or cartons.
Commercial Not-From-Concentrate (NFC) juice production involves the selection and preparation of ripe fruits, extraction of juice using a mechanical press or juice extractor, screening/filtering to remove pulp and seeds, pasteurization to extend shelf life, and packaging into the consumable containers.
The high-quality cold press NFC juice starts from fresh fruits, uses the cold juice extraction technology to get the juice, then filled into the containers, after that, the juice containers will be pasteurized by the HPP system to get a long stable shelf life of the end products. In the whole processing system, the juice will not be heat treated, to keep all the vitamins and nutrients of the juice at maximum.
Introduction to NFC Beverage Processing Technology
- Typical NFC beverage juice processing technology:
Raw material selection → cleaning → crushing → preheating → juice extraction → filtration → blending → degassing homogenization → sterilization → canning.
- Typical processing technology for beverage jam:
Cleaning crushing preheating pulping concentration blending degassing homogenization sterilization filling.
NFC Juice Production Line End Package
Bottled NFC juice: There are 3 types of bottled NFC juice according to the pasteurizing and filling method:
Pasteurized NFC juice: the juice is pasteurized and cold or hot filled into the bottles, and stored in the refrigerator, the shelf life is about 30 days-45 days.
HPP treatment NFC juice: it is cold extracted from fresh fruits, then directly filled into bottles, and the bottled NFC juice will be pasteurized by HPP system. The juice with this processing method has a shelf life of 60-120 days in the refrigerator.
UHT sterilized NFC juice: it is UHT sterilized and then aseptically filled into bottles, the shelf life can reach to 9-12months at room temperature.
Gable top carton NFC juice: The juice is pasteurized and then cold-filled into the gable top cartons. The shelf life is about 30 days-45 days in the refrigerator.
Aseptic brick carton juice: the juice is UHT sterilized and then aseptically filled into brick cartons, the shelf life can reach to 12 months at room temperature.
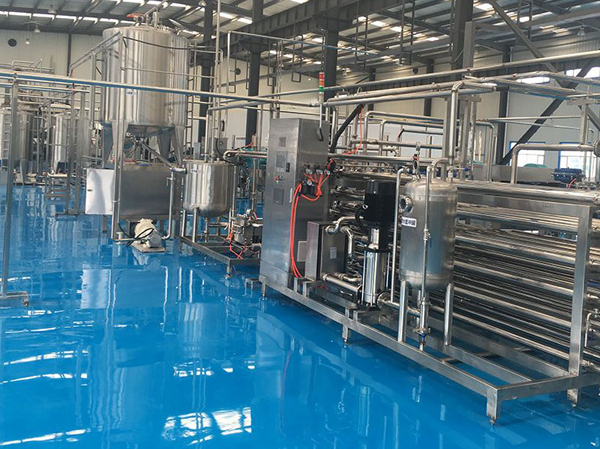
Introduction to NFC Beverage Processing Technology
NFC Beverage Juice Production Process Description
- Weighing materials
1.1 The batching personnel weigh the ingredients according to the batching table issued by the R&D department based on production needs.
1.2 Keep a record of material weighing, seal the material after weighing, and place it in the designated location with clear markings.
1.3 Weigh easily hygroscopic small materials before mixing
- Raw material dissolution:
2.1 Dissolve stabilizer: Dissolve the stabilizer in 85 ℃ hot water in a high-speed mixing tank for about 20 minutes. After fully dissolving without particles, transfer it to the mixing tank through a colloid mill at normal pressure.
2.2 Dissolve Aspartame and AK Sugar: Mix aspartame and AK sugar evenly, slowly add 85 ℃ hot water, and stir until fully dissolved without particles, then pour into the mixing tank.
2.3 Dissolve Fructose Syrup: Dissolve Fructose Syrup in cold water (about 7 times the amount of water) in a mixing tank, stir at high speed for 10 minutes, then stop stirring and transfer to a mixing tank (with a cloth filter). Rinse the mixing tank with purified water and transfer to the mixing tank.
2.4 Potassium sorbate, pigments, color protectants, salts, etc. should be dissolved in warm water.
Dissolve 2.5 sodium citrate, citric acid, and malic acid together in warm water (three times in total) and dilute to 7-10 times.
2.6 Vc, essence, opacifier, etc. shall be dissolved in cold water.
- Adjustment of fixed volume:
3.1 Feeding sequence: stabilizer+sugar substitute+potassium sorbate+Vc+acid (including sodium citrate)+pigment+color fixative+salt+opacifier+essence.
3.2 Acid addition: Slowly add the fully dissolved citric acid and malic acid solution.
3.3 Constant volume: 4.5 tons, stir for 20 minutes after constant volume, and homogenize only after passing the quality inspector’s inspection. The sample pH is 3.0-3.5, the sugar content is 1.2 ± 0.1 ° Brix, and the total acid is 0.2565 ± 0.015% (calculated as citric acid).
- Homogenization: primary pressure: 30MPa, secondary pressure: 10MPa, homogenization effect: eccentricity ≤ 1mm.
- UHT (Ultra High Temperature Instant Sterilization): Sterilization temperature is 125-130 ℃, sterilization time is 4-6 seconds, and discharge temperature is 72 ± 2 ℃.
- Insulation: The temperature of the insulation cylinder is 70 ± 2 ℃.
- Filtering: Use a 300 mesh pipeline filter to filter.
- Bottle disinfection: (Old bottles need to be disinfected and cleaned in advance: soak and disinfect with 2% Kangle disinfectant for 4 minutes). During production, rinse and disinfect the bottles with 1.0% Kangle disinfectant, and then rinse them with hot water at 60-65 ℃.
- Cover disinfection: Just open the bottle cap and place it directly into the storage container for UV sterilization for 30 minutes; Bottle caps that have been opened or lightly contaminated should be disinfected with 1% Kangle disinfectant for 3 minutes, then rinsed with clean water for 3 minutes, dehydrated with a spin dryer, and placed in an ozone disinfection cabinet for 30 minutes before being put into production use; Lids with severe pollution are not allowed to be used.
- Filling screw cap: filling temperature 67 ± 2 ℃, filling capacity 500 ± 15ml, average net content not lower than the labeled content; After filling, there should be no residual syrup at the thread of the bottle mouth. The production self inspection and quality control personnel should check the screw cap and whether there are any foreign objects before filling can be carried out; Before starting up, it is required to inspect each head product (self inspection by production operators and supervision by quality control personnel) to ensure that the screw cap does not leak liquid or air, and the tightness is moderate; The bottle cap body is clean and free of foreign matter adhesion.
- Spray code: It is required to be complete, clear, accurate, with characters 2-3 millimeters high. The spray code position is on the bottle cap, and the spray code style is “Previous line 2010/01/21 Next line 08:28:08B corresponds to parallel lines, B is the shift”.
- Lamp inspection: Detect products with impurities, flat bottles, low liquid level, poor coding, poor labels, etc., and prohibit defective products from entering the next process.
- Rinsing: The temperature requirement for rinsing the bottle is to use hot water at 50-60 ℃ to rinse off the slurry attached to the bottle wall and keep it warm.
- Packing: The packing quantity is accurate, and the outer packaging box is tidy.
- Sealing and palletizing: The sealing tape is tightly sealed, smooth, and aesthetically pleasing; The finished product box is square and beautiful; The stacking should be arranged neatly and aesthetically pleasing, and the stacking height should be based on the principle of not affecting product quality (the stacking height should not exceed 5 layers); Print the production date in the “Production Date” section of the certificate of conformity, ensuring clarity and accuracy.