The fully automated functional beverage production line equipment adopts PLC, frequency converter, and human-machine interface control system. It has control technologies such as variable frequency speed regulation, automatic filling with cans, and no filling without cans. Through various sensors on the device, accurate production speed and quantity can be displayed on the touch screen. The production speed can be set on the touch screen according to user requirements. The whole machine has various protections for the main motor and other electrical appliances, such as overload, overvoltage, etc. At the same time, various corresponding faults will be automatically displayed on the touch screen, making it convenient for users to find the cause of the fault.
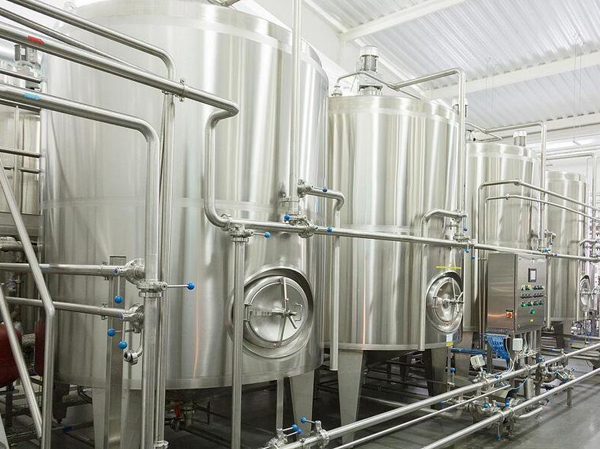
Manufacturer of automatic functional beverage production line
With the popularization of health concepts and the increasing demand for healthy drinks among consumers, functional health drinks have gradually taken a place in the market. These beverages attract consumers of all ages with their unique formulas and benefits.
Processing technology of fully automated functional beverage production line
Production process of functional beverages: water treatment → ingredients → gas-liquid mixing → filling → warming bottle → labeling → drying → coding → film packaging → packaging finished products
This production line is used for the production of functional beverages in plastic bottles/glass bottles. It can customize a production line of 2000-36000 bottles/hour according to customer requirements and production volume. The entire production line includes water storage tanks, water treatment, blending, gas-liquid mixing equipment, blow molding machines, bottle sorting machines, air delivery, filling machines, lamp inspection, labeling machines, blow drying machines, inkjet printers, film wrapping machines, conveying, and lubrication systems. The degree of automation can be configured according to customer requirements, and the entire equipment design is advanced. The electrical part adopts internationally or domestically renowned brands, providing process flow and workshop layout design, and full technical guidance throughout the process
Optional configuration:
Bottle body label: set label/labeling
Spray code: laser spray code/ink spray code
Packaging: cardboard box/PE film
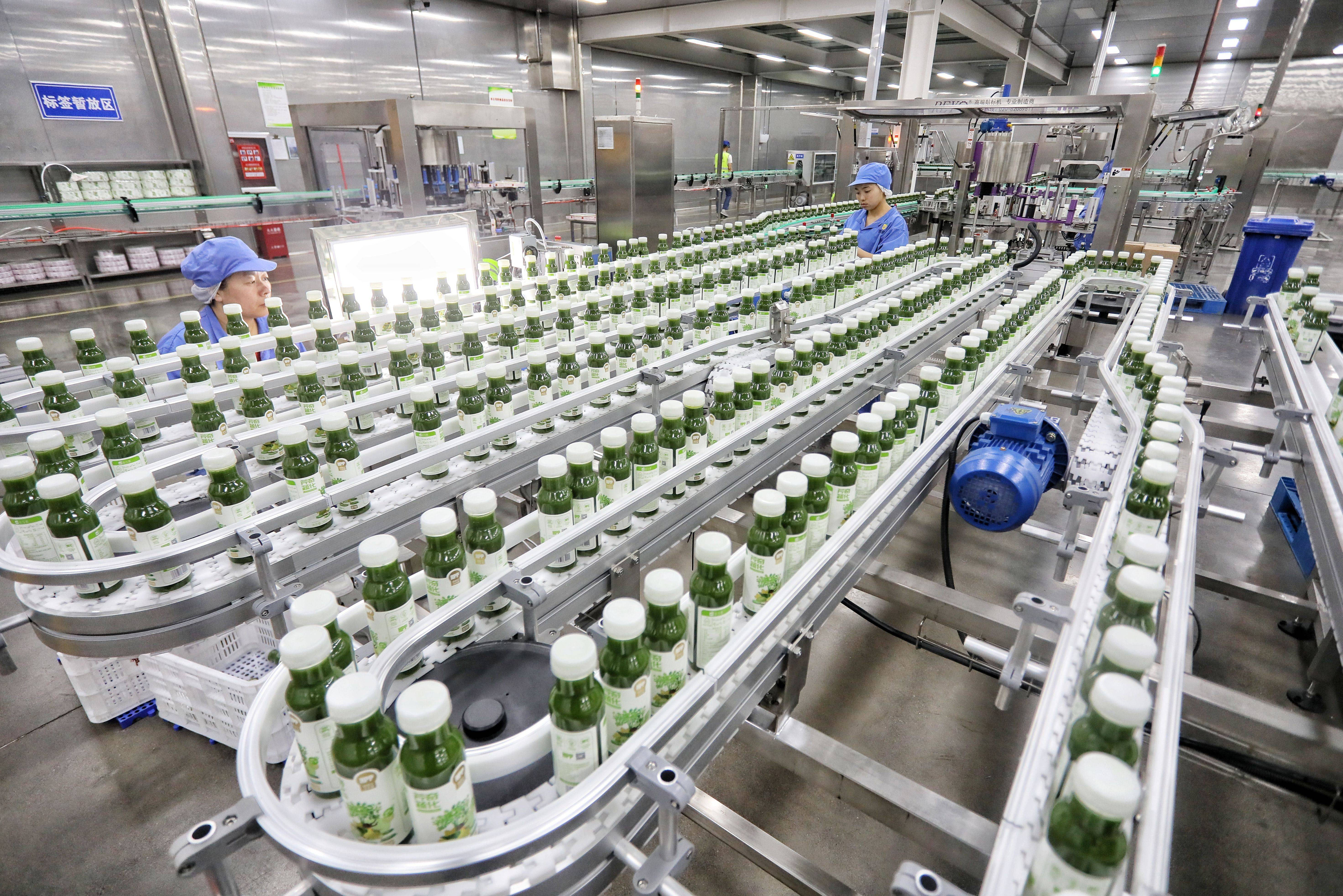
Overview of Equipment and Process Operations Required for Functional Beverage Production Line:
1、 Equipment requirements
- Raw material processing equipment:
Water treatment equipment: used to purify water sources and ensure the cleanliness of production water.
Powder ingredient system: used for precise measurement and mixing of various raw materials, such as caffeine, taurine, vitamins, etc.
Syrup preparation equipment: used for preparing sugar solutions, usually including steps such as dissolution, filtration, and storage.
- Mixing and blending equipment:
High speed mixer: used to evenly mix various raw materials to ensure consistent product taste.
Mixing tank: used for secondary mixing of mixed raw materials with purified water to achieve the optimal ratio.
- Filling and sealing equipment:
Filling machine: used to inject pre mixed beverages into bottles or cans of various specifications.
Sealing machine: used to seal bottle caps to prevent beverage leakage during transportation and storage.
- Sterilization and cooling equipment:
Sterilization equipment: such as high-temperature instantaneous sterilizers, used to kill harmful microorganisms in beverages and ensure product safety.
Cooling equipment: used to quickly cool sterilized beverages to a suitable temperature for subsequent operations.
- Packaging and logistics equipment:
Packaging machine: used for outer packaging of filled beverages, such as paper boxes, cartons, etc.
Logistics equipment: such as conveyor belts, forklifts, etc., used to transport products from production lines to warehouses or shipping areas.
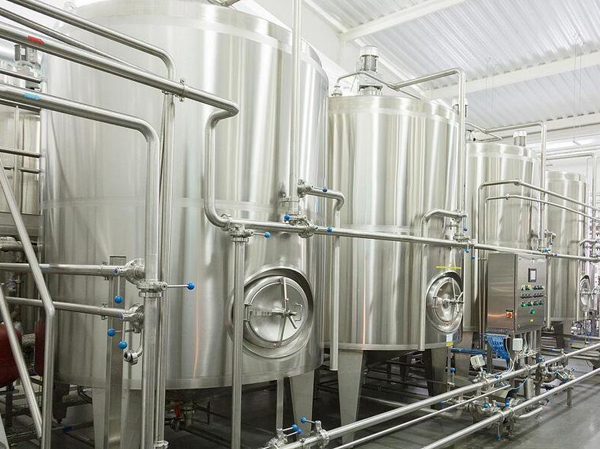
Process operation of health functional beverage production line
- Raw material preparation:
Check and confirm the quality and quantity of all raw materials to ensure compliance with production standards.
Accurately measure and prepare the raw materials according to the formula requirements.
- Mixing and blending:
Add the raw materials measured by the powder batching system into the mixing tank.
Add an appropriate amount of purified water and mix thoroughly using a high-speed mixer.
Monitor the quality of the mixed beverage to ensure it meets the predetermined standards.
- Filling and sealing:
Send the prepared beverage into the filling machine for filling.
After filling, use a sealing machine to seal the bottle cap.
- Sterilization and cooling:
Send the filled beverage to the sterilization equipment for high-temperature instantaneous sterilization.
After sterilization is completed, quickly send the beverage into the cooling device for cooling.
- Packaging and Logistics:
Send the cooled beverage into the packaging machine for external packaging processing.
Check and confirm the packaging quality, and send qualified products to the warehouse or shipping area.
- Quality control and testing:
Regularly conduct quality inspections on raw materials, semi-finished products, and finished products throughout the entire production process.
Record and analyze the test results, promptly identify problems, and take corrective measures.
- Health and Safety:
Regularly clean and maintain production equipment to ensure the hygiene and safety of the production environment.
Train employees to comply with hygiene and safety operating procedures to ensure the smooth progress of the production process.
In summary, the equipment and process operation of the functional beverage production line is a complex and sophisticated system engineering. Through reasonable equipment configuration and precise process operation, the quality and production efficiency of products can be ensured to meet market demand.