automatic fruit juice beverage production line can also be called the juice repacking line, it uses fruit and vegetable concentrated juice or puree as raw material, blended with water, sugar and other flavor agents to make it into drinkable juice.
The capacity of the juice processing line can be 500LPH-100000LPH, and the end products can be filled into small bottles, pouches, tin cans or cartons according to client requirements.
The juice production machines includes water powder dissolving system, concentrated juice blending and diluting system, reconstituted juice sterilizing, homogenizing and degassing system, juice filling and packing system.
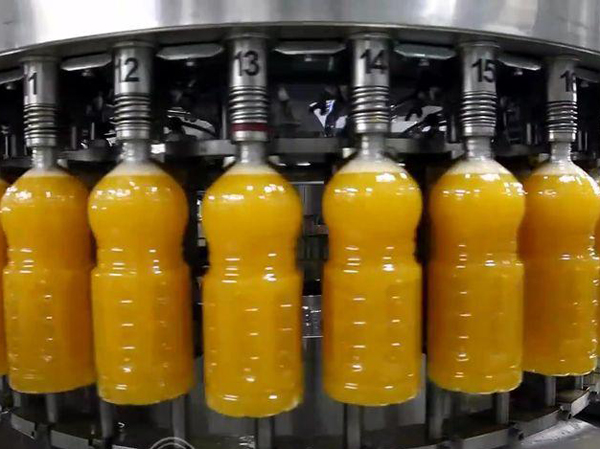
Manufacturer of automatic fruit juice beverage production line
100% NFC juice drinks: Use non-concentrated fruit puree or fresh fruit as raw materials, can be produced with or without the addition of sugar and water. Fruit content is 100% or less.
Mixed Juice drinks: Use single fruit or mixed fruit juice concentrates/juice powder as raw materials, then blend with water other ingredients and obtained the mixed fruit juice drinks. This type of juice drinks are clear and without pulp, fruit content is above 10%.
Fruit Nectar drinks: contain fruit pulp, the fruit content 30%-50% with high acidity and less juice like mango nectar. This type of drink does not contain any colorings or preservatives.
Fruit flavor drinks: Using pure water as the main material, add about 5% fruit content and mix with flavoring and sweeteners.
Juice drinks and fruit pulp drinks:
- Fruit juice (pulp) and fruit juice beverages (products). It is defined as a product made from fresh or refrigerated fruits through processing. Fruit juice (pulp) and fruit juice beverages (products) can also be subdivided into fruit juice Fruit pulp Concentrated fruit pulp Fruit pulp beverage Fruit juice beverage. Fruit juice beverage Fruit beverage syrup There are 9 types of fruit drinks, most of which use the pulping process to process fruits or edible parts of fruits into unfermented but fermentable slurries, or add an equal amount of natural water lost during concentration to the concentrated fruit pulp, resulting in a color with the original fruit flesh Products with flavor and soluble solids content.
- Juice beverage refers to a type of beverage made by extracting juice from fresh fruits. The juice of various fruits contains different nutrients such as vitamins, and is considered a beneficial beverage for health. However, its lack of all the fiber and high sugar content of fruits are sometimes seen as its drawbacks. Various common fruit juices: apple juice Grapefruit juice Strange juice Mango juice. Pineapple juice Watermelon Juice. Grape Juice. Cranberry juice Orange juice coconut milk. lemon juice. Cantaloupe Juice. Strawberry juice. papaya juice.
II Equipment and process flow for preparing concentrated fruit juice beverages:
Sugar conversion (according to customer needs) – filtration (according to customer needs) – cooling (according to customer needs) – blending – filtration – homogenization – sterilization – filling – sealing – warming bottle – labeling Shrinking – coding – packing – sealing – palletizing (the specific equipment used in the juice beverage production line depends on the situation)
III Process flow of juicing beverage from raw fruit:
Raw fruit – picking – cleaning – crushing – juicing – enzymatic hydrolysis – emulsification – blending – filtering – homogenization – degassing – sterilization – filling – sealing – labeling – shrinking – coding – packing – palletizing (the equipment used in the juice beverage production line depends on the customer’s situation)
Juice is a juice product obtained from fruits through physical methods such as pressing, centrifugation, extraction, and blending. It generally refers to pure juice or 100% juice. Juice is divided into clear juice and cloudy juice according to its form. Clear fruit juice is clear and transparent, such as apple juice, while cloudy fruit juice is uniformly cloudy, such as orange juice; According to the juice content, it is divided into pure juice and juice drinks. Juice contains a considerable amount of nutrients found in fruits, such as vitamins, minerals, sugars, and pectin in dietary fiber. It has the benefits of aiding digestion, moisturizing the intestines, and supplementing insufficient nutrients in the diet. Therefore, juice is highly favored by people. Our company specializes in non-standard manufacturing based on the characteristics of various fruit juice beverages. We have collaborated with multiple fruit juice beverage manufacturers and successfully designed and manufactured various fruit juice production line equipment, concentrated juice production line equipment, jujube juice production line equipment, soy milk, peanut milk, almond milk and other plant protein beverage production line equipment. The juice beverage production line equipment includes pre-treatment equipment, filtration equipment, blending equipment, filling equipment, etc. Customization is welcome! Our company can not only design and manufacture various juice beverage production lines, plant protein beverage production lines, and herbal tea production lines, but also install and debug the entire equipment, providing turnkey projects!
The production process of fruit juice mainly includes the following key steps:
- Raw material selection and pretreatment: Choose fresh, ripe, and pest free fruits as raw materials. Pre processing includes steps such as cleaning, peeling, removing the core, and cutting into pieces to ensure the hygiene of the fruit and the smooth operation of the juicer.
- Juicing: Send the pre treated fruit into a juicer for juicing, commonly using mechanical pressing and centrifugal separation methods. During the juice extraction process, it is necessary to control the speed and pressure to ensure the quality and taste of the juice.
- Clarification and filtration: The extracted juice is clarified and filtered to remove impurities and pulp particles, ensuring the clarity and taste of the juice.
- Blending: according to the product formula, the juice is mixed with other raw materials (such as sugar, acid, essence), and the proportion is controlled to ensure the nutritional value and taste of the product.
- Homogenization and degassing: Homogenization treatment refines the particles in the juice, and degassing removes oxygen to prevent oxidation. This step helps to maintain the freshness and taste of the juice.
- Sterilization and cooling: Use methods such as pasteurization or ultra-high temperature instantaneous sterilization to ensure the hygiene and safety of fruit juice. Quickly cool after sterilization to prevent loss of nutrients.
- Filling and packaging: Fill the sterilized and cooled juice into a container, select suitable packaging materials, and label and code according to market demand to ensure the appearance and quality of the product.
The factors that affect the quality of juice production include the freshness, maturity, and absence of pests and diseases of the raw materials. During the production process, it is necessary to strictly control the temperature, time, and pressure to avoid affecting the quality of the juice.
By following the above steps, high-quality juice products can be produced to meet the needs of consumers
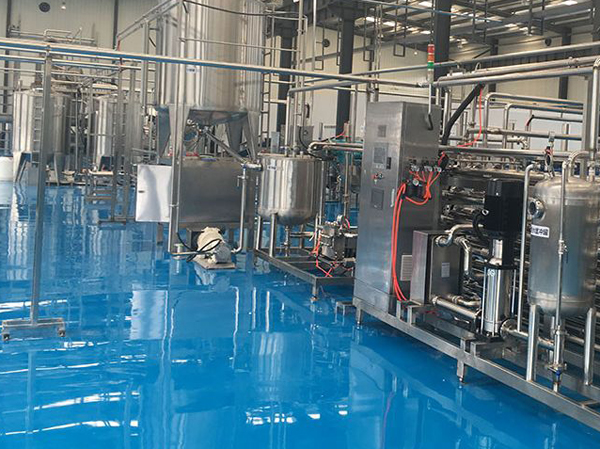
The production of fruit juice beverages generally includes the following equipment:
- Water treatment equipment: Using original American nanofiltration membranes (such as RO membranes for purified water), the water source can be groundwater or tap water, ensuring that the effluent quality meets the standards of purified water. The conductivity of primary water is below 40, and that of secondary water is below 10. This system includes quartz sand tank, activated carbon tank, raw water tank, water treatment, ozone sterilization equipment, etc
- Mixing tanks (raw water tank, pure water tank, ingredient tank). The mixing tank mainly mixes materials Mix and match reconcile. Homogenization, etc. The stainless steel mixing tank can be designed with standardized structure and configuration according to the requirements of the production process, and can be humanized. The mixing tank can achieve feed control during the mixing process Mixing control and other manual operations Automatic control, etc. The structure of the mixing tank is composed of a mixing tank body Mixing tank cover Blender Support transmission. The materials used for bearings can be made of carbon steel or stainless steel according to different process requirements. Due to different production process requirements of users, the mixer can be configured with a slurry type Anchor type Frame style Spiral and other forms.
- Homogenizer. The application of homogenizers in food processing: Homogenizers in food processing refer to the triple action of squeezing, strong impact, and expansion to refine the material liquid, so that the material can be more evenly mixed with each other. For example, homogenizers are used in dairy processing to break down the fat in milk more finely, making the entire product system more stable. Milk will look whiter. Homogenization is mainly carried out through homogenizers. It’s food dairy. Important processing equipment in the beverage industry.
- Ultra high temperature sterilization machine. Suitable for fresh milk Juice Drinks. Bang Bing And ice cream paste Soy sauce Soybean milk Condensed milk Instantaneous sterilization of liquid materials such as alcohol can also be used for sterilization of fluid materials. The feeding and discharging of this equipment are both equipped with three-way valves, and the flow rate can be adjusted as needed, ensuring reliable use.
- Multi functional bottle blowing machine. The whole machine operation adopts touch screen operation to achieve human-machine dialogue. Specially designed secondary blowing system ensures stable quality of bottle molding. The heater adopts a four stage infrared temperature control and a digital automatic voltage stabilization temperature control system, which can set the corresponding heating temperature according to different bottle preforms of the user. It has a reasonable structure Small footprint Low power and gas consumption Strong stability and other characteristics.
- Bottle sorting machine. PLC control combined with variable frequency speed regulation ensures synchronous operation of the entire production line. Adopting a three time recommendation bottle dispensing mechanism to improve bottle dispensing efficiency. The unique design of the bottle dropping component adapts to bottles of different lengths. The bottle extraction wheel is equipped with a bottle jam detector. The umbrella shaped tower is equipped with detectors that control the storage volume of bottles in the main engine compartment by starting and stopping the hoist. The reverse bottle is connected to the bottle mouth of the air duct during the bottle extraction wheel to prevent the bottle from getting stuck halfway. The bottle discharge is controlled by a synchronous belt and star wheel to ensure stable discharge No inverted bottle Squeeze bottle phenomenon. The whole machine adopts a centralized lubrication system for fixed-point lubrication Timed Quantitative lubrication.
- Bottle loading equipment (palletizer, PET bottle air delivery equipment). The air duct conveyor line is designed for conveying empty PET bottles of various shapes and sizes. Modular design, easy and fast installation of air ducts and layout of workshop production lines. Different conveying methods can be designed for bottles of different specifications. By measuring wind pressure The adjustment of wind speed realizes the control of conveying speed.
- Bottle cap cleaning machine. Rinsing bottle caps with liquid medicine can solve the dust generated during transportation and storage of bottle caps.
- Three in one filling machine. The three in one filling machine adopts star wheel transmission technology to achieve fully automatic bottle washing Filling Sealing and other processes. The air duct is directly connected to the bottle feeding wheel, and the bottle transmission adopts full process bottleneck technology. Changing the bottle shape does not require adjusting the height of the equipment. The three in one unit completes bottle washing in one go internally Filling The three sealing processes result in minimal bottle wear Accurate and stable transmission. High speed and high flow gravity filling valve, fast filling speed, accurate liquid level without liquid loss. The bottle bottom support plate of the bottle dispensing wheel adopts a spiral descent method, and changing the bottle shape does not require adjusting the height of the bottle dispensing conveyor chain.
- Lamp inspection box. The lamp inspection box adopts lamps with a power of 60W and a rated voltage of 220V. The lamp inspection box is mainly used for quality inspection of transparent bottled liquids after filling and before packaging.
- Sealing machine. The high-pressure fan blows air, causing the high-speed flowing air to spray out from the narrow slit and blow away the residual water droplets on the bottle body. The slit is arranged in an inclined manner, and all sides of the bottle can be blown by high-speed winds.
- Labeling (labeling) equipment. Modular design, static cutting. Adapt to various bottle shapes and bodies.
- Laser coding machine. Safe and non-toxic. Energy saving and energy-saving.
- Packaging machine. The membrane packaging machine adopts imported PLC automatic control and human-machine interface Accurate tracking, secondary package entering status, eliminating bottle shortage Pour the bottle and adjust it flexibly. Adjustable hot air circulation structure, suitable for various heat shrink films (including color printing), with fast and easy film replacement.