The equipment composition of the fully automated fruit and vegetable juice beverage production line includes a water treatment system, raw fruit treatment system, blending system, automatic bottle blowing machine, wind conveyor line, UHT ultra-high temperature sterilization machine, capping machine, lid cleaning machine, bottle filling and capping three in one machine, bottle pouring sterilization machine, cold bottle machine, blow dryer, labeling machine, inkjet printer, palletizer, winding machine, solid bottle conveying system, box conveying system, electrical control system, and a complete set of filling and packaging production lines. Optional equipment: automatic bottle sorting machine or manual bottle sorting system, fully/semi automatic bottle washing machine, fully automatic bottle unloading machine, bottle warehouse, labeling machine, carton packaging machine, etc.
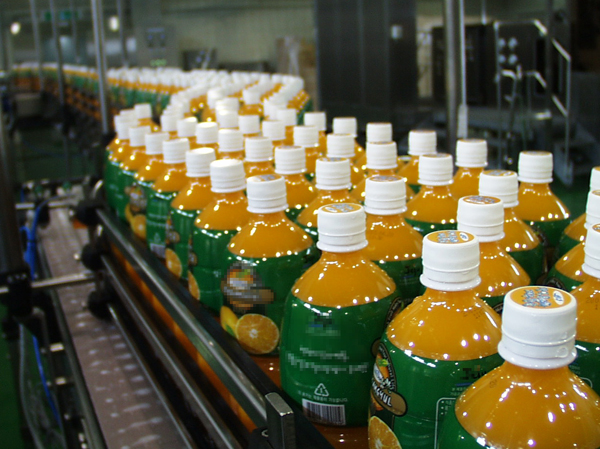
Manufacturer of automatic beverage production line
The beverage production line can process a wide variety of beverages, including but not limited to the following:
Carbonated beverages: such as cola
Lactic acid beverages: such as yogurt
Tea beverages: such as green tea
Juice drinks: such as orange juice drinks
Milk containing beverages: such as milk drinks
Plant protein drinks: such as peanut juice drinks
Functional beverages: such as a certain cow
Flow Chart of Beverage Production Line
1.Tea Drink/Fruit Juice Production Line
Flow Chart of Tea Drink/Fruit Juice Production Line
Main components of this beverage production line: RO water treatment, preform injection line, cap injection line, PET bottle blowing line, fully automatic bottle unscrambler, air conveying system, tea/fruit juice/vegetable juice accessory equipment for filling line, 3-in-1 filling system, sterilizing machine, bottle cooling machine, CIP auto cleaning system, auto conveying system, air purification system, OPP/PVC labeling machine, wrap shrinking packing machine.
2.Carbonated Drink Production Line
Flow Chart of Carbonated Drink Production Line
Main components of this beverage production line: RO water treatment, preform injection line, cap injection line, PET bottle blowing line, fully automatic bottle unscrambler, air conveying system, carbonated drink accessory equipment for filling line, 3-in-1 filling system, bottle warming machine, CIP auto cleaning system, auto conveying system, air purification system, OPP/PVC labeling machine, wrap shrinking packing machine.
3.Carbonated Drink Production Line
Flow Chart of Carbonated Drink Production Line
Main components of this beverage production line: RO water treatment, preform injection line, cap injection line, PET bottle blowing line, fully automatic bottle unscrambler, air conveying system, carbonated drink accessory equipment for filling line, 3-in-1 filling system, bottle warming machine, CIP auto cleaning system, auto conveying system, air purification system, OPP/PVC labeling machine, wrap shrinking packing machine.
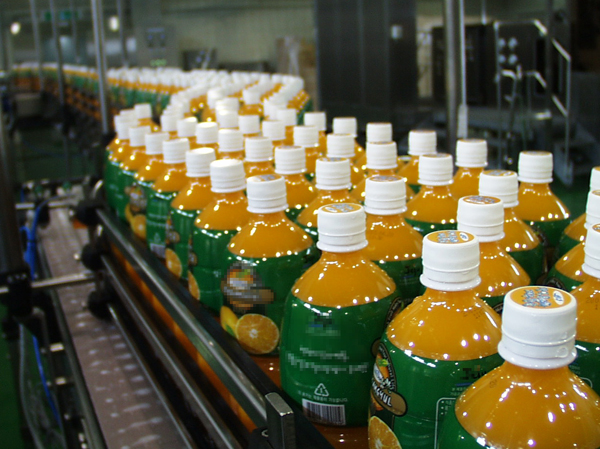
The components of a fully automated beverage production line are relatively complex, but can be mainly summarized into the following aspects:
- Raw material processing system: This system mainly preprocesses raw materials, such as cleaning, crushing, mixing, etc., to improve the quality and hygiene of plateau materials.
- Ingredient system: This system mainly mixes various raw materials in a certain proportion to achieve the desired taste and nutritional value.
- Mixing system: This system mainly stirs the mixed raw materials to ensure thorough and uniform mixing, resulting in the taste and quality of well-known products.
- Filtration system: This system mainly filters the mixed raw materials to remove impurities and particles, resulting in clear and transparent products with high reputation.
- Filling system: This system mainly fills filtered beverages into bottles or cans, ensuring the packaging quality and sealing of well-known products.
- Sealing system: This system is mainly used to seal the filled beverage, ensuring the hygiene and safety of well-known products.
The application field of fully automatic beverage production line is very wide, which can be applied to the production of various types of beverages such as fruit juice drinks, tea drinks, carbonated drinks, dairy drinks, etc. With people’s pursuit of health and deliciousness, the demand in the beverage market is increasing, and the prospects for fully automated beverage production lines are also becoming broader.
The fully automatic beverage production line is an efficient, automated, and intelligent production equipment, which has brought revolutionary changes to beverage production. In the future, with the continuous advancement of technology and the expansion of the market, fully automated beverage production lines will become more perfect, efficient, and intelligent, bringing a better future to beverage production.
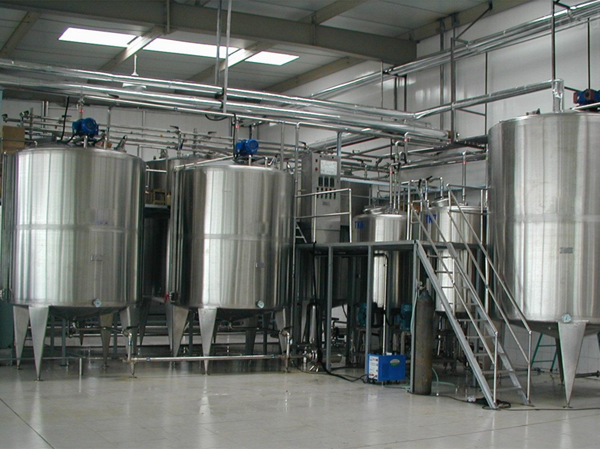
How to choose suitable beverage production line equipment
Choosing appropriate beverage production line equipment is crucial for the production and development of enterprises. Here are some suggestions:
- Clarify production requirements: Before selecting equipment, it is necessary to clarify one’s own production requirements, including product types, output, production cycles, etc., in order to choose suitable equipment.
- Consider equipment performance: Equipment performance is the key to selection, including equipment stability, production efficiency, automation level, etc. Choose equipment with stable performance, high production efficiency, and high degree of automation.
- Consider equipment cost: Equipment cost is one of the important factors in selection, including equipment price, installation cost, maintenance cost, etc. Choose appropriate equipment based on your budget and financial situation.
- Consider after-sales service: High quality after-sales service can ensure the normal operation and production efficiency of well-known equipment, and equipment suppliers with good after-sales service should be selected.
Beverage production line equipment is one of the core equipment for beverage production enterprises, which plays an important role in improving production efficiency, increasing product quality, and reducing production costs. When choosing equipment, it is important to clarify one’s production needs, consider factors such as equipment performance, cost, and after-sales service, and choose the equipment that is suitable for oneself. Enterprises should also strengthen the maintenance and management of equipment to ensure its normal operation and production efficiency.