The value of natural gas liquids, such as ethane and propane, is increasing due to growing global demand for petrochemical feedstock, heating and power. natural gas liquids (NGL) recovery solutions are specialized to maximize recovery while providing you with high operational flexibility and greater returns on plant investments.
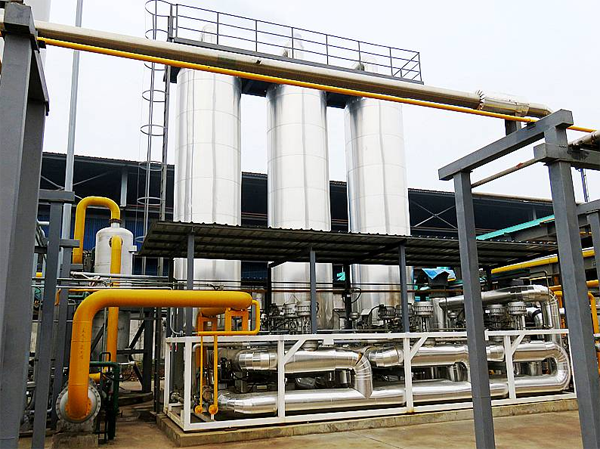
Liquefied gas ngl recovery purifying unit
Whether you need high, ultra-high or flexible recovery, NGL recovery technologies can meet stringent product specifications and operational demands more efficiently. solutions provide up to 99-plus percent NGL/LPG recovery and offer flexibility for changing economic or operating conditions.
For challenging scenarios such as remote locations and short project timelines, the line of modular plants offer high NGL recovery through pre-engineered, skid-mounted units. The factory-built approach allows for predictable costs and schedules and quick construction with superior quality.
Light ends fractionation NGL recovery device
The value of natural gas liquids, such as ethane and propane, is increasing due to growing global demand for petrochemical feedstock, heating and power. natural gas liquids (NGL) recovery solutions are specialized to maximize recovery while providing you with high operational flexibility and greater returns on plant investments.
Model No. | NGLC 65-35/25 | NGLC 625-35/15 | NGLC 625-35/30 | NGLC 625-35/60 | NGLC 625-35/80 | NGLC 625-35/140 |
Standard gas volume X104 Nm3/d | 1.5 | 1.5 | 3.0 | 6.0 | 8.0 | 14.0 |
Device elasticity X104 Nm3/d | 0.7-2.25 | 0.7-2.25 | 1.5-3.6 | 4.5-6.5 | 4.0-9.0 | 8.0-15.0 |
Process method | Alcohol injection and hydrocarbon collection | Dehydration and hydrocarbon collection | ||||
Product Type (mixed hydrocarbon + dry gas) | Dry gas (into pipe network) | Dry gas (CNG / inlet pipe network) | ||||
Dry gas content | Meet the requirements of pipeline transportation | <1 ppm | ||||
C3 yield | >80% (Improve efficiency according to user requirements) | |||||
Applicable ambient temperature | -40-50 ℃ | |||||
Inlet pressure | 0.1-10.0 MPa | |||||
Dry gas outlet pressure | 4.0-23.0 MPa | |||||
Design pressure of hydrocarbon mixing tank | 2.5 MPa | |||||
Explosion-proof grade | ExdIIBT4 | |||||
The control mode | PLC + upper computer | |||||
Skid sizes | L*W*H: 8000-17000X3500X3000 mm |
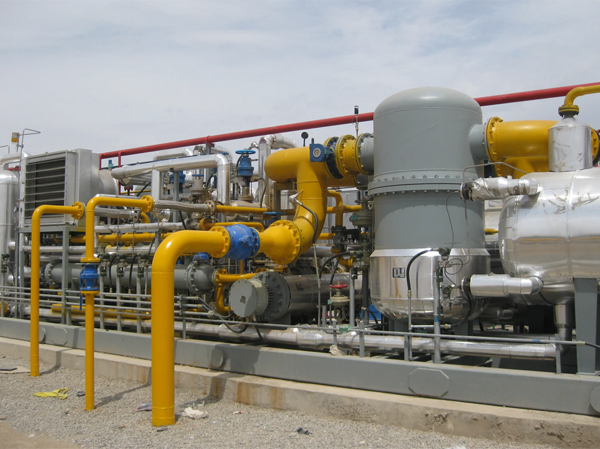
LPG recovery skid liquefied petroleum gas recovery plant
For the recovery of LPG/C3+ the Engineering Division offer an absorber process, which guarantees recovery rates as high as 99.9 %, while at the same time featuring low specific energy consumption. Furthermore the tolerable CO2 content of the feed gas is higher than for conventional expander processes.
To achieve high C3 recovery rates, implements an absorber column upstream of the deethanizer. Here the feed gas is scrubbed by using a light hydrocarbon reflux coming from the top of the deethanizer. LPG is separated from the heavier hydrocarbons down-stream of the deethanizer using a destillation column.
LPG is liquefied petroleum gas, which is produced when refining crude oil or volatilized from the process of oil or natural gas exploitation. LPG is a mixture of oil and natural gas formed under appropriate pressure and exists as a liquid at room temperature.
LPG (Liquefied Petroleum Gas) is widely used as alternative fuel for cars, but is also suitable as a chemical feedstock. It consists of propane and butane (C3/C4).
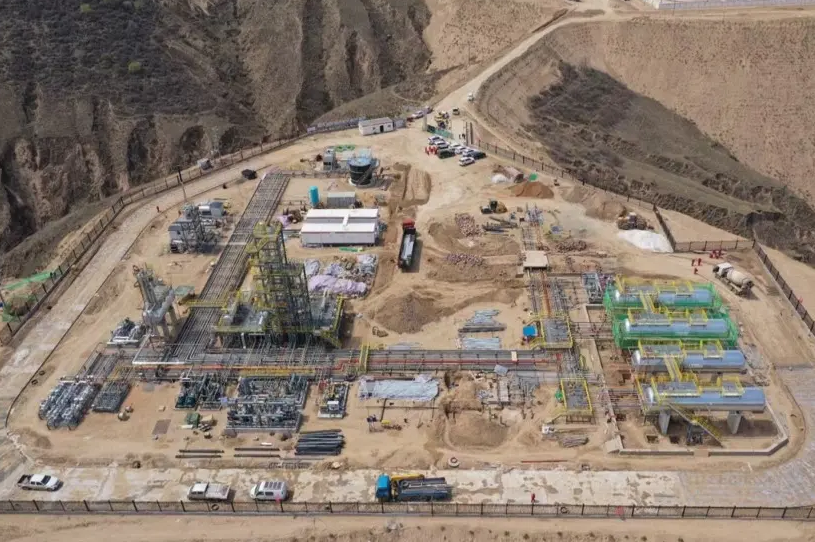
8MM Liquefied Petroleum Gas recovery skid for natural gas
Why to recover natural gas liquids: Improve the quality of natural gas, reduce hydrocarbon dew point and prevent liquid hydrocarbon condensation in pipeline transportation; The recovered condensate products are important civil fuel and chemical fuel; The comprehensive utilization rate of resources is provided, which has good economic benefits.
LPG ( is widely used as alternative fuel for cars, but is also suitable as a chemical feedstock. It consists of propane and butane (C3/C4).
For the recovery of LPG/C3+ the Engineering Division offer an absorber process, which guarantees recovery rates as high as 99.9 %, while at the same time featuring low specific energy consumption. Furthermore the tolerable CO2 content of the feed gas is higher than for conventional expander processes.
To achieve high C3 recovery rates, Rongteng implements an absorber column upstream of the deethanizer. Here the feed gas is scrubbed by using a light hydrocarbon reflux coming from the top of the deethanizer. LPG is separated from the heavier hydrocarbons down-stream of the deethanizer using a destillation column.
Why to recover natural gas liquids: Improve the quality of natural gas, reduce hydrocarbon dew point and prevent liquid hydrocarbon condensation in pipeline transportation; The recovered condensate products are important civil fuel and chemical fuel; The comprehensive utilization rate of resources is provided, which has good economic benefits.
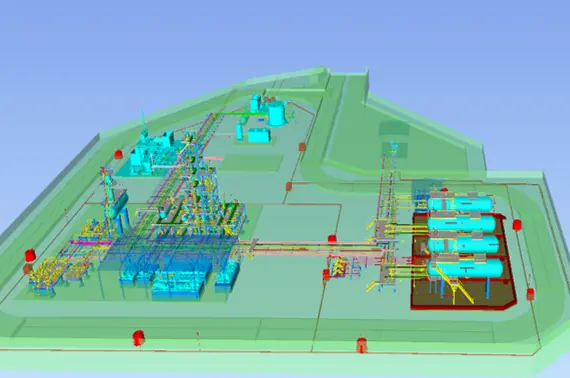
2 MMSCFD LPG recovery plant
The raw natural gas enters the inlet separator to filter out mechanical impurities and separate the free water, then enters the compressor after precision filtration by the dust filter, and is cooled to 40 ~ 45 ℃ by the cooler of the compressor itself, and then separates some water and heavy hydrocarbons (in case of excessive heavy components), and then enters the dehydration unit for deep dehydration. The dry feed gas from the dehydration skid enters the condensation separation skid, then it enters the refrigeration unit after precooling to ~ 10 ℃ through the heat exchanger. Next after cooling the feed gas to – 35 ℃ and cooling again through throttling, it enters the low-temperature separator for gas-liquid separation after
The separated gas phase and liquid phase enter the deethanizer respectively, the tower top gas returns to the heat exchanger for reheating and output outside the boundary, and the tower bottom liquid enters the depropane and debutane tower for separation again. LPG at the top of the tower and stable light hydrocarbon at the bottom of the tower enter the storage tank respectively for loading and export
Table power consumption of process electric equipment
Electrical equipment | Power kw | remarks | |
Shaft power | Motor power | ||
refrigerator | 130 | 150 | 380V/50HZ |
Natural gas compressor unit | 220 | 250 | 380V/50HZ |
Instrument air compressor | 3 | 5.5 | 380V/50HZ |
Power consumption of instrument control system | 2 | 2 | 220V/50HZ |
Regeneration gas heater | 40 | 50 | 380V/50HZ |
Regeneration gas fan | 5 | 7.5 | 380V/50HZ |
Deethanizer reboiler | 100 | 120 | |
Depropane and debutane Reboiler | 130 | 150 | |
total | 530 |