The tomato sauce production line mainly processes fresh tomatoes through cleaning, lifting, sorting, crushing and pulping, concentration and sterilization, and aseptic filling, ultimately turning them into finished tomato sauce products in barrels. It is widely used in the pre-treatment of various fruit and vegetable processing, such as concentrated juice processing pre-treatment, fruit and vegetable packaging pre-treatment, fruit and vegetable beverage processing production line, fruit and vegetable powder processing production, fruit and vegetable pulp processing production line, tropical fruit processing production line, etc.
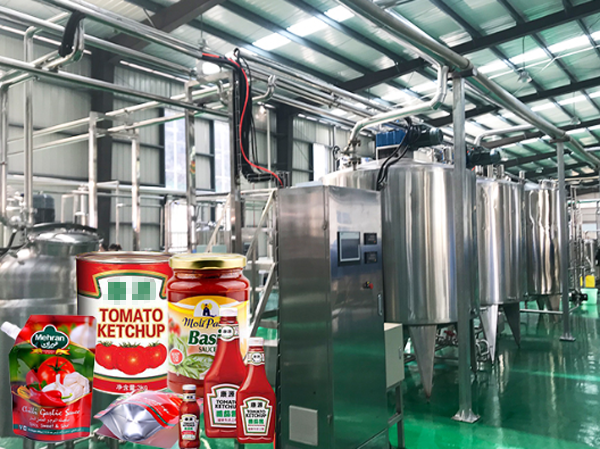
Fully automatic tomato sauce production line
The tomato sauce production line has multiple advantages. Firstly, the crushing system adopts pipeline crushing technology, which does not come into contact with air during the crushing process, effectively ensuring the color of tomato sauce. Secondly, the evaporator is energy-saving and recyclable, and the condensed water generated by the first effect is used for secondary evaporation, achieving recycling.
The sterilization machine is designed reasonably, with a system pressure not exceeding 7Mpa, and is safe and reliable. Fourthly, a conical mesh structure is adopted, with adjustable load in the gap, and dual frequency conversion speed regulation makes the semi-finished product more delicate and high-yield. Finally, the entire process design and pipeline connection layout considered the retention of natural aromatic components in tomato sauce products, effectively preventing the loss of flavor substances caused by thermal response and reducing the quality loss caused by high-temperature oxidation of tomato pulp.
Processing technology of tomato ketchup production line:
Fresh fruit → lifting → washing → fruit washing and sorting → crushing → preheating → sorting/pulping/refining → storage → concentration → storage → TIT disinfection → aseptic filling → finished product → pump → mixing system → F filtration → degassing → homogenizer → UHT sterilizer
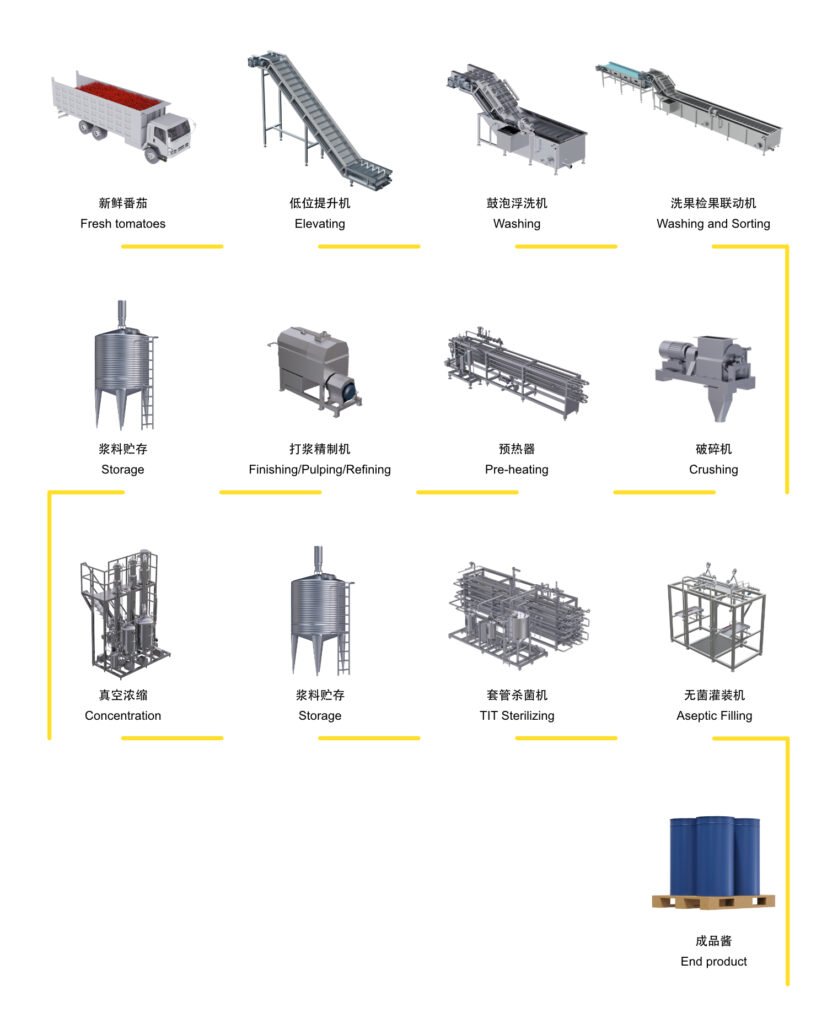
Tomato ketchup production line, tomato ketchup production equipment technological advantages:
The jam production line mainly processes fresh fruits through cleaning, lifting, sorting, crushing, pulping, concentration and sterilization, and then aseptic filling to produce finished fruit jam in barrels. The entire production line is designed specifically for fruit ketchup according to international quality standards.
- Crushing system: The whole fruit pipeline is broken, and the crushing process does not come into contact with air, ensuring the color of the fruit ketchup.
- Energy saving and recycling of evaporator: The condensed water generated by the first effect is used for secondary evaporation and recycling in the second effect.
- Safety of sterilization machine: The design of the sterilization agent is reasonable. The Bix36-38 system pressure does not exceed 7Mpa, and exceeding 10Mpa is more dangerous.
Raw materials: Fresh tomatoes
Terminal product: Tomato ketchup (concentration of 28-30%, 30-32%, 36-38%)
Processing capacity: 10-1500T fresh fruits/day
Ingredients of jam: pure fruit pulp, vitamins, sugar and other flavor additives.
Sterilization methods: Pasteurization, UHT high-temperature sterilization, ultra-high temperature sterilization. (Adjustable according to requirements)
Terminal packaging: sterile large barrel, box in bag sterile small bag, tinplate small packaging, small bag packaging.
Control mode: Manual control or automatic control can be used for quantities below 300 tons.
System composition: Raw fruit lifting system, cleaning system, sorting system, crushing system, preheating and enzyme inactivation system, pulping system, vacuum concentration system, blending system, sterilization system, sterile large bag filling system, small packaging and packaging system.
Technical details:
- Shared equipment includes water treatment reverse osmosis equipment, screw air compressor units, and cooling water units.
- The preliminary raw material processing includes bubble cleaning machine, selection conveyor belt, blanching machine, cooling machine, peeling machine, etc.
- Raw material preparation includes a sauce maker, colloid mill, storage tank, slurry pump, diaphragm pump, etc.
- The emulsification part includes an emulsifier, a rotary pump, a finished product storage tank, and a metal removal machine.
Next are steam jacket pot, diaphragm pump, cooling bucket, homogenizer, finished product storage tank, rotary pump, metal remover, etc.
Next are the sandwich pot, diaphragm pump, cooling bucket, tubular sterilizer, finished product storage tank, rotary pump, metal remover, etc.
Next is the small packaging stage, which includes vertical small packaging machines, conveyor belts, weight detection machines, metal detection machines, sterilization kettles, etc.
Next is the large packaging stage, which includes vertical vacuum packaging machines, conveyor belts, cooling water tanks, air drying machines, packaging platforms, sealing machines, bundling machines, etc. - Alternatively, there can be an automatic bottling line with a bottle feeding turntable, cleaning machine, drying tunnel, lamp inspection, filling machine, capping machine, labeling machine, coding machine, laminating machine, heat shrink machine, bottle receiving turntable, etc.
- Customization is also available upon request