Fully automatic premix feed production line,A mixture of one or more additive raw materials (or monomers) mixed evenly with a carrier or diluent, also known as additive premix or premix, aimed at facilitating the uniform dispersion of trace amounts of raw materials in a large amount of compound feed. Premixed feed cannot be directly fed to animals
Pre mixed feed can be regarded as the core of compound feed, as the trace active components it contains are often the determining factor of the feeding effect of compound feed
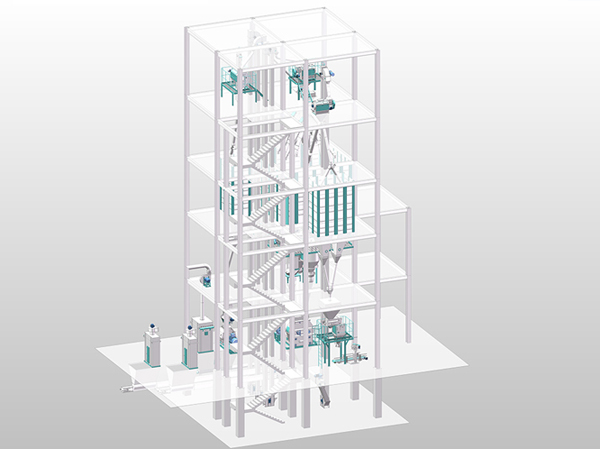
Fully automatic premix feed production line
Premix feed is the brief name of Additive premixed feed. It is proportioned with one kind or various kinds of micro element(include all kinds of micro mineral element, vitamins, Synthetic amino acid, some medicine and some other additive, etc.) with diluent or isotopic carrier, and then evenly mixed to be made into intermediate type feed products.Premix feed is the important part of complete formula feed.
We are specialized in manufacturing feed machinery and engineering, we can offer customer complete machine solutions for livestock feed(pig and others) , poultry feed(chicken, duck, goose and others), ruminant feed(cattle, sheep and others), normal aqua feed(four major Chinese carps), special aqua feed(shrimp, crab and others), extruding aqua feed(floating and sinking fish feed, shrimp and others), premix feed(including various additives), pet food(cat food, dog food and others), we can meet customers’ kinds of needs.
Classification of premixed feed
- Single premixed feed It is a uniform mixture of a single additive raw material or a variety of feed additives of the same kind and a carrier or diluent, mainly because the use of a certain or a certain type of additives is very small, the primary premixed to be more evenly distributed to the bulk feed. In the production, a single vitamin, a single trace element (selenium, iodine, cobalt, etc.), a variety of vitamins, and a variety of trace elements are first premixed to make a single premix respectively.
- Composite premix feed It is a uniform mixture made by mixing various kinds of feed additives with carriers or diluents according to the formula and actual requirements. Such as trace elements, vitamins and other ingredients mixed together premix.
Now we take the case of 1000 automatic batching premix feed set, make introduction based on process diagram and each process as follows:
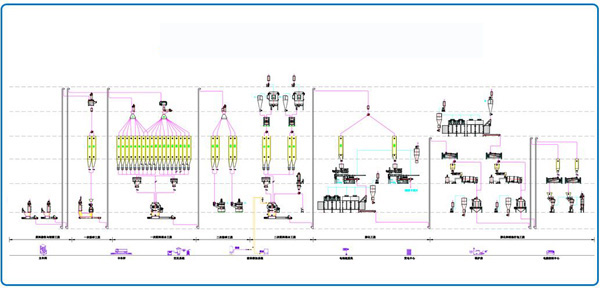
Raw material:
The raw materials are mainly diluent or isotopic carrier, adding kinds vitamins, minerals, and medicines. The feature of premix raw material is small amount, numerous varieties and mainly powder type.
Brief introduction for flow process
1000 automatic premix is designed by 1t/batch (about 6tph), which the carrier and the micro element are separated to be weighed automatically by computer. One unit of single shaft mixer, one unit of automatic bagging machine especially for premix feed. The total power is about 63kw. The construction area of the production workshop is about: 121133m. The whole line is with compact design, reasonable structure, suitable to environmental requirement, which can be customized specially by customers demands.
Technological process chart:
RM receiving and cleaning process — batching and mixing process– packing process– Auxiliary process
Considering the characteristics of easy cross contamination and grading of premixed materials, this design adopts a process where the material flows completely by gravity from the silo to the packaging after carrier lifting, which can effectively prevent cross contamination and grading risks caused by further lifting and transportation.
Raw material receiving and cleaning section: Clean up impurities in raw materials to ensure product quality and the safety of subsequent processing equipment.
Cleaning equipment: SQLZ60 × 50 × 100 powder sieve, 5.5KW, designed to produce 10-15 T/H.
Ingredient mixing section: This section uses two ingredient scales, with four carrier bins weighing separately and eight small bins weighing separately. Trace elements are manually added and equipped with inspection scales. The material ingredients are mixed in the mixer after completion, and finally directly fall into the finished product warehouse.
Weighing equipment: ingredient scale PCS-05/PCS-02, ingredient accuracy: dynamic ≤ 3 ‰, static ≤ 1 ‰. Mixing equipment: mixer SDHJ.2, 18.5KW, 1000kg/P, designed to produce 6 tons (premix). Mixing uniformity CV ≤ 5%.
Packaging section: The pre mixed finished product after mixing is directly placed in the finished product warehouse, and then enters the buffer hopper of the packaging scale through a closed air feeder. Finally, it is weighed by an automatic packaging scale and inserted into a label by a dedicated packaging outlet for sewing.
Packaging equipment: Pre mixed material special packaging scale, packaging range 20-50kg/bag, 3-5 bags/minute.
Auxiliary section: Dust removal system, dust removal at feeding and packaging ports to improve the working environment for workers.
According to the needs of different customers, this solution can optimize the configuration:
- In this plan, trace elements are manually added, and customers can choose an automatic feeding element addition system according to their needs;
- The quantity of carrier silos and small silos can also be adjusted according to factors such as customer formulas and raw material characteristics to achieve the highest utilization rate and effectively control production costs;
- The packaging area is equipped with a dust removal system to improve the working environment for workers. Customers can choose whether to configure it according to their needs.
Production technology of automatic premix feed production line
(1) Prevent and reduce the loss of active ingredients, ensuring the stability and effectiveness of the premix. Choose raw materials with good stability. In terms of vitamins, it is advisable to choose raw materials that have undergone stabilization treatment; When using trace elements such as sulfates, efforts should be made to minimize their crystal water, or use oxides instead. Organic trace elements can also be selected; Control the dosage of choline chloride, as it has strong water absorption and a destructive effect on vitamins; Vitamins should be added in excess, especially when stored for more than 3 months; Good quality antioxidants, anti caking agents, and mold inhibitors should be added.
(2) Stability of trace components: Under normal storage and use conditions, the physical and chemical properties of trace elements, vitamins, and other components in the premix are stable. However, when the moisture content is high, its stability is poor and the loss rate is high. Therefore, the moisture content of the premix should be strictly controlled, preferably not exceeding 5%.
(3) Amino acid addition issue: Many experiments have shown that adding rumen methionine and lysine can increase milk production and economic benefits, which can be added by the dairy farm according to specific circumstances.
(4) Measurement and mixing: For the measurement of trace components, electronic scales should be used, accurate to 0.01 grams, and scales can be used for large quantities of raw materials. There are various types of mixers, and ordinary vertical mixers have the disadvantages of slow feeding speed, easy automatic separation, and slow unloading speed. It is best to use horizontal double screw belt mixers or cone mixers.
(5) Packaging and Storage: Pre mixed packaging bags are mostly made of three in one paper bags, which have the advantages of being waterproof, light proof, leak proof, and not easily damaged. Usually 20-25 kilograms per bag. Due to the presence of multiple active trace components in the premix, there is an increased opportunity for their interaction. Therefore, moisture prevention should be taken into account during storage.