Our company is an enterprise that produces various types of papermaking machinery equipment, paper pulp production line equipment, finishing equipment, paper processing machinery, papermaking accessories and consumables. Since its establishment, the factory has undergone continuous development and now has complete testing methods and an excellent processing team. Committed to providing users with high-quality and advanced papermaking machinery and pulp equipment. The equipment can be used for papermaking enterprises that produce various household and industrial paper, as well as pulp enterprises that produce straw pulp, wood pulp, bamboo pulp, and recycled pulp. Provide 1092-8200 circular web paper machines, long web/short long web paper machines, toilet paper production lines (napkins), household paper production lines, kraft paper production lines, corrugated paper production lines, coated whiteboard paper machines, cardboard boxes, packaging paper production lines, cultural paper production lines (writing paper), specialty paper production lines, waste paper production lines, hydraulic pulpers, disc grinders, rinses, vibrating screens, horizontal paper rolls, drum paper rolls, various rewinding machines, calenders, thrusters, Dutch pulping machines, roughing mills, pulp tank mixers, single blade paper cutters, double blade paper cutters, pulp pumps, rewinding embossing and punching machines, etc.
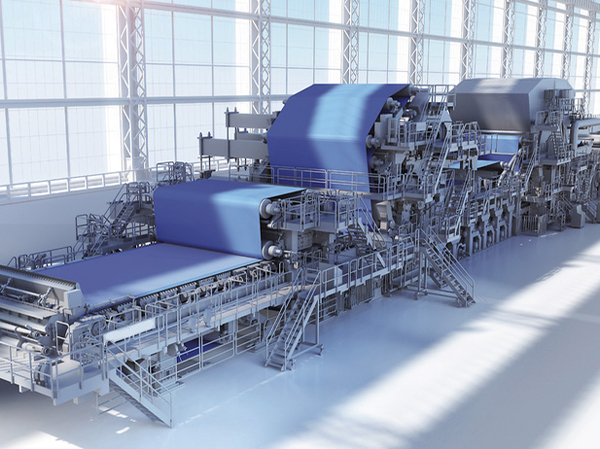
Fully automatic paper pulp production line
Main equipment for pulp making in paper mills
The main equipment for pulp making in a paper mill includes a main unit such as a flow box, a mesh section, a pressing section, a drying section, a calender, a paper winding machine, and a transmission section, as well as auxiliary systems such as steam, water, vacuum, lubrication, and heat recovery. These devices work together to form a paper web from pulp.
Specific equipment and its functions
Slurry box: used to evenly distribute pulp to the mesh, forming the initial structure of the paper web.
Net section: Dehydrate pulp through a sieve to form a wet paper web.
Pressing section: removes moisture from the wet paper web through pressing and further dehydrates it.
Drying staff: Use hot air or steam to dry wet paper web to the desired degree of dryness.
Polishing machine: The paper is processed by a calendering roller to improve its smoothness and flatness.
Roll paper machine: Roll dried paper into rolls for easy storage and transportation.
Transmission Department: Responsible for the entire transmission system of the paper machine, ensuring coordinated work among all parts.
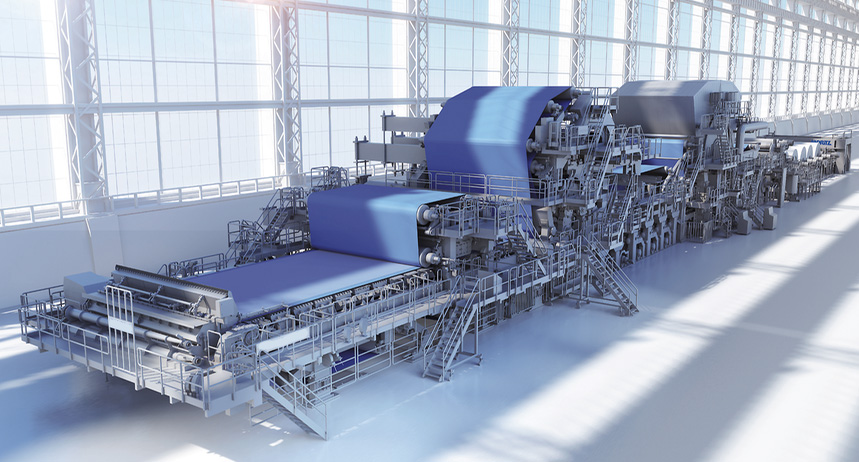
Pulp production line auxiliary system
The paper machine also includes auxiliary systems such as steam, water, vacuum, lubrication, and heat recovery to ensure the normal operation and maintenance of the equipment. For example:
Steam system: Provides steam for heating the dryer body.
Water system: used for cooling and cleaning equipment.
Vacuum system: helps remove moisture from the paper web.
Lubrication system: Ensure smooth operation of equipment and reduce wear and tear.
Heat recovery system: Recycling and utilizing waste heat from the production process to improve energy efficiency.
These devices and systems together form the complete system of the paper machine, ensuring that pulp can be efficiently and stably converted into paper products.
Pulp manufacturing methods include: mechanical grinding method, chemical treatment method and combination method of chemical treatment with mechanical grinding. During the process, plant raw materials shall be separated into the morphology of single fiber to meet the requirements of cleanness in use.
Pulping methods are basically divided into three categories:
Mechanical pulp manufacturing methods
It is the method mainly based on mechanical grinding (mechanical dissociation) for fiber separation. Pulping yield, that is, the weight percentage of paper pulp obtained from a certain amount of raw material, Mechanical pulp manufacturing has the highest yield in all the methods. About wood raw material, it can reach up 95%.
Chemical pulp manufacturing methods
It is the method of obtaining pulp by use of chemical agents to cook plant raw materials for paper pulp. Its pulping yield is about 40% to 50%. The high yield of chemical pulp can reach up 65%.
Combination pulping pulp manufacturing methods
It is to use chemical agents to make some certain of pretreatment on raw material and then adopt mechanical grinding method to obtain pulp.
According to chemical pretreatment, its pulping yield is between 65%-94%. It is popular to call a pulping method with a yield of 65%-84% as semi-chemical pulping method but call the pulp manufacturing method with a yield of 85%-94% as chemical mechanical pulping. But both are made by chemical mechanical pulp manufacturing methods.
Pulps obtained by various pulp manufacturing methods must be treated through appropriate washing, screening, impurity removal or further bleaching and refining to improve the quality and meet the requirements for producing different types of paper. Waste paper fiber can also be properly treated and re-made into paper pulp. But its process principle and production flow are different from those of the above pulp methods.
The Category of Pulp Manufacturing Methods
1. According to different manufacturing methods, it is divided into chemical pulp (Including caustic soda pulp, sulfate pulp, sulfite pulp, etc.), mechanical pulp (Including SGW pulp, RMP pulp, TMP pulp, etc.) and Chemical mechanical pulp.
2. According to different raw materials for paper pulp, it is divided into wood pulp, straw pulp, bamboo pulp, cotton pulp, waste paper pulp.
3. According to different processing grades, it is divided into unbleached pulp, half-bleached pulp, bleached pulp, refined pulp, etc.
4. According to different pulp yields, it is divided into chemical pulp (40%-50%), high yield of chemical pulp (50%-65%), semi-chemical pulp (65%-84%), chemical mechanical pulp (85%-94%), mechanical pulp (94%-98%).
5. According to different application purposes, it is divided into self-use pulp and commodity pulp. For a specific category, it is often named by several different classification methods, for example, bleached sulfate softwood pulp, unbleached sulfite reed pulp, poplar wood pulp and others, so that the user can generally understand the properties and uses of pulp from their names.
Of all categories of pulps, chemical pulp still occupies the largest proportion. In 1987, chemical pulp manufacturing production reached 111,350,000tons in the world, accounting for 71% of the total pulp production (155,860,000tons) and mechanical pulp accounts for 21%. Chemical mechanical pulp grew rapidly in recent years although it is used relatively late. Due to continuous improvement of pulp manufacturing recycling rate of waste paper and relative increases in the amount of fillers and coatings used in paper, pulp consumption reduces. So the growth rate of pulp is generally lower than that of paper and cardboard.
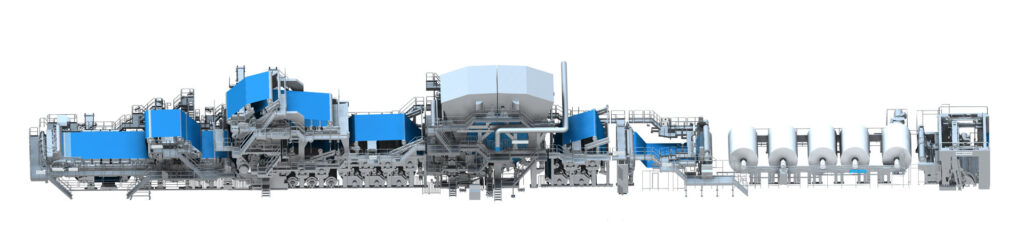
Papermaking processes consist of the following major procedures:
- Pulping section: paper pulp raw material selection→ cooking for fiber separation→ washing →bleaching→ screening→ concentration and production for pulp chips→ storage
- Papermaking section: pulp scattering→ impurity removal →pulp refining→ pulp beating → preparation of various additives → mixing of paper materials →convey of paper materials → head box → mesh section → press section → dry section → surface sizing → drying → calender →paper reeling
- Coating section: raw paper coating→ coating → drying → reeling → re-reeling → super calendar.
- Processing section: rewinding → cutting plate (or reel) → sorting and packaging → storage
The main equipment of pulp production line
Conveying and Bale handling
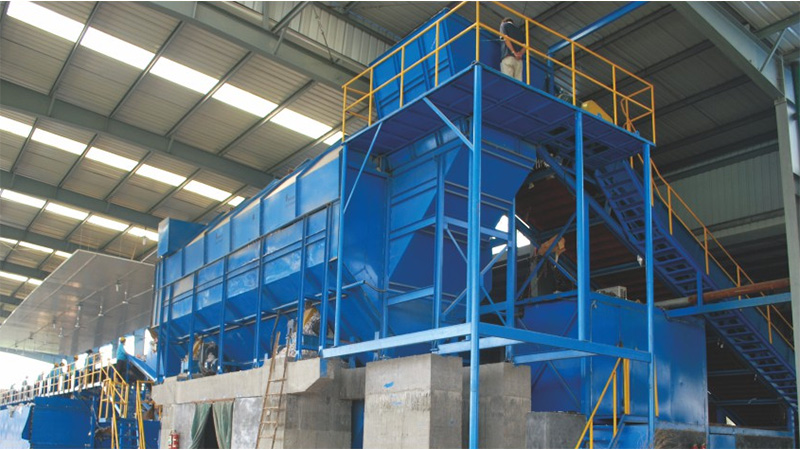
Bale Breaker
Advantages
- Scientific arrangement of screen holes on the screen cylinderand internal stock guide plates provides favorable conditions for removingsmall-size rejects mixed in waste paper.
- Dry screening process greatly reduces wear of cutting wheel, disc, pump, pipe, cleaner, pressure screen and other downstream pulping and screening equipment.
- Greatly improve the efficiency of pulping system, especially re-pulping system. Broken waste paper increases the pulping efficiency by 15-25% and saves energy by 10-20%.
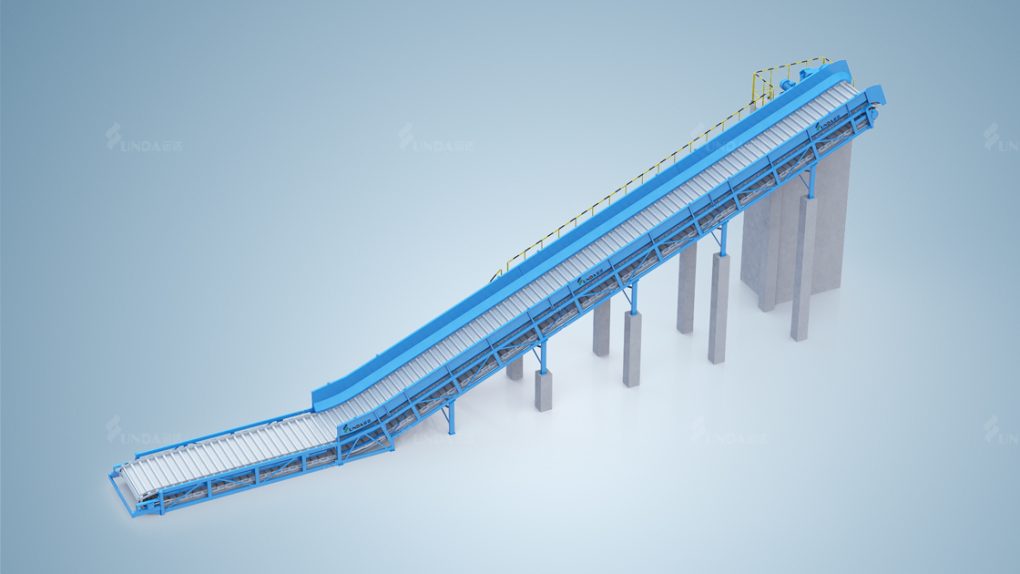
Slat Conveyor
Structural principle
The chain plate conveyor is composed of five parts: head driving device, tail wheel device, tension device, chain plate and frame.
Stern gear
The reversing part of the chain plate of the machine is composed of a tail wheel shaft, two tail wheels and bearings.
Tension device
The tensioning device adopts a spiral tensioning method to adjust the tightness of the traction chain.
Chain plate portion
It consists of a traction chain and a trough plate. Traction chain adopts impact-resistant, stable and reliable chip traction chain, the inner chain is equipped with a roller in the middle, rolling on the track to reduce friction resistance and wear. The grooves are bolted to the traction chain.
rack
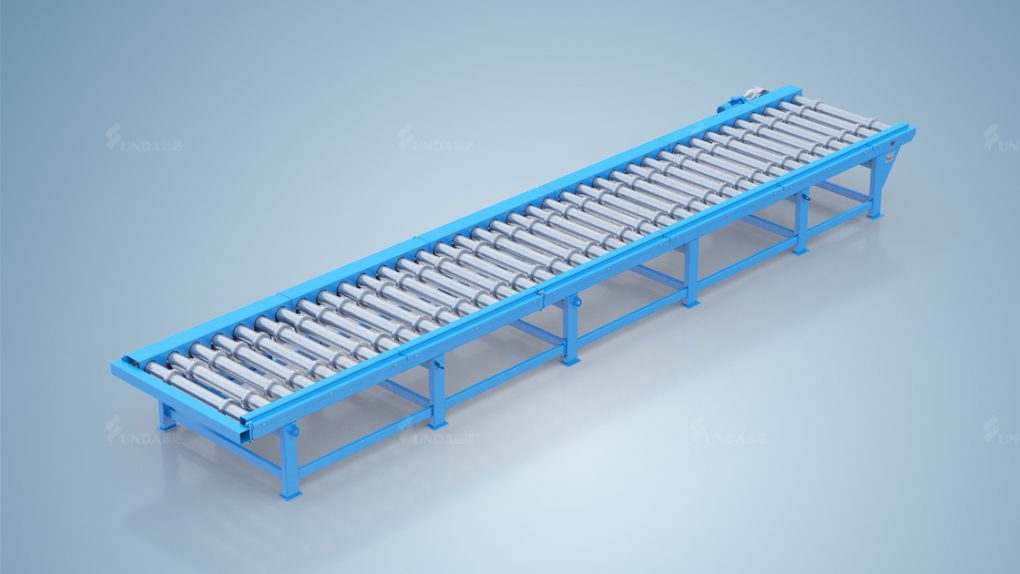
Roll Conveyor
Advantages
Stable transportation, firm structure, lower power consumption
Support rings set up for rollers to leave space between bale and roller surface so as to easily remove the bale wires
Structure and Principle:
The machine is composed of main drive carrier roller device, driven carrier roller device and machine frame, etc.
Main drive carrier roller device
The device consists of motor, reducer, drive carrier rollers, chain wheel, mounted bearing and support ring, etc. The driving force is directly transmitted to the main shaft from motor through reducer, and then to the parallel driven carrier rollers through the chain wheel. The mounted bearing supports and fastens drive rollers on machine frame.
Pulper and auxiliary equipment
Drum Pulper
Drum pulper is a pulping equipment for the recycled fibers,provides maximum retention of fiber physical characteristics, minimum breakdown of contaminants, clean impurities and high quality of accept.
The drum pulper consists of two groups: the rotating part and the driving system. the rotating part is composed of the mixing section, the pulping section and the screening section. the driving system is composed of the support rolls , the transmission device and the lubrication unit.
Working principle
The waste paper enters the mixing section and pulping section of the drum pulper and gets fully disintegrated by gentle rubbing in the pulping section, and then goes forward to the screening section, where it is diluted by the spraying shower, and the accept stock goes into the bottom vat, waste plastics are washed away and discharged from the reject discharge outlet.
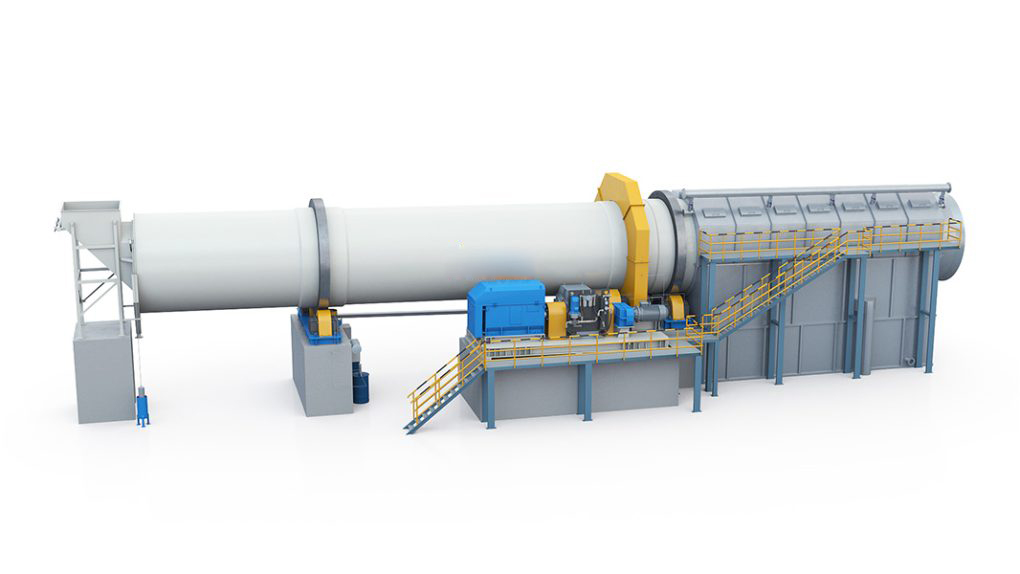
D-type Pulper
D-Type pulper is mainly used for the pulping of various Waste Paper, Broke paper and Board in continuous or batch modes according to the needs. The continuous pulping system removes impurities in time and requires very little shut down time only for cleaning, The pulping efficiency is high.
The continuous pulping system consists of D type pulper, Trash Well, Detrasher, Drum Screen , Ragger, Rope Cutter, Trash Well and Grapple, etc., the whole pulping process is controlled by the DCS automatic control system.
The waste paper is conveyed into the D type pulper which is the main aequipment of the low consistency continuous pulping system through chain conveyor. Special vat body design shortens the recirculation routes of the stock, and fastens the contact in between the rotor and stock, shortens the pulping time, and lowers the energy consumption;
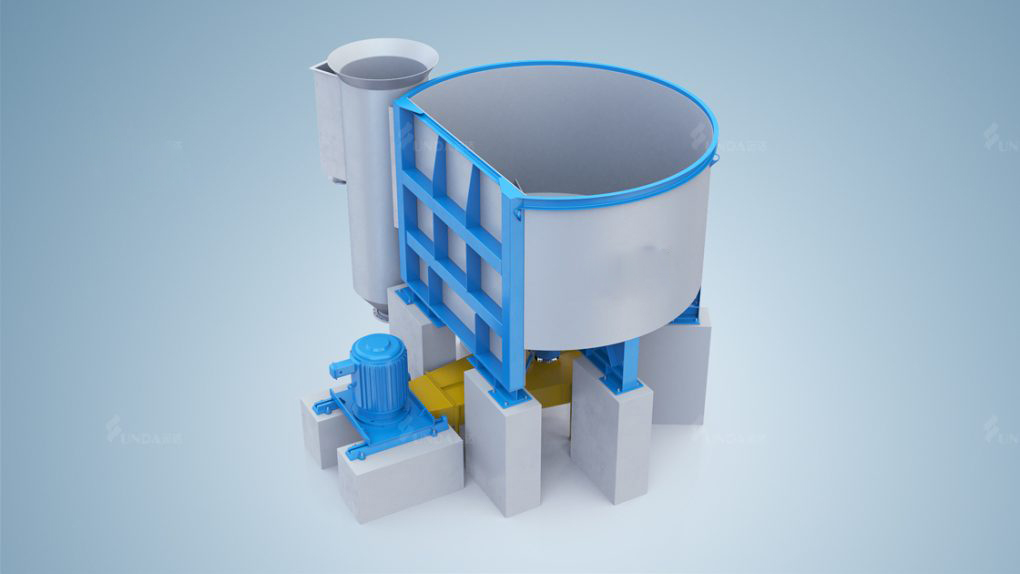
High Consistency Pulper
high consistency hydraulic pulper is mainly used for the deinking process of waste paper and the separation of aluminum and plastic for Tetra Pack and other liquid packaging. It adopts a tower-shaped spiral rotor and the pulping consistency can reach 12%~18%.
Advantages
Tower-shape spiral rotor has a strong defibering ability meanwhile not broken the impurities.
Suitable for high consistency stock of 12-18%,energy saving and chemicals saving.
Compact construction,easy operation and maintenance.
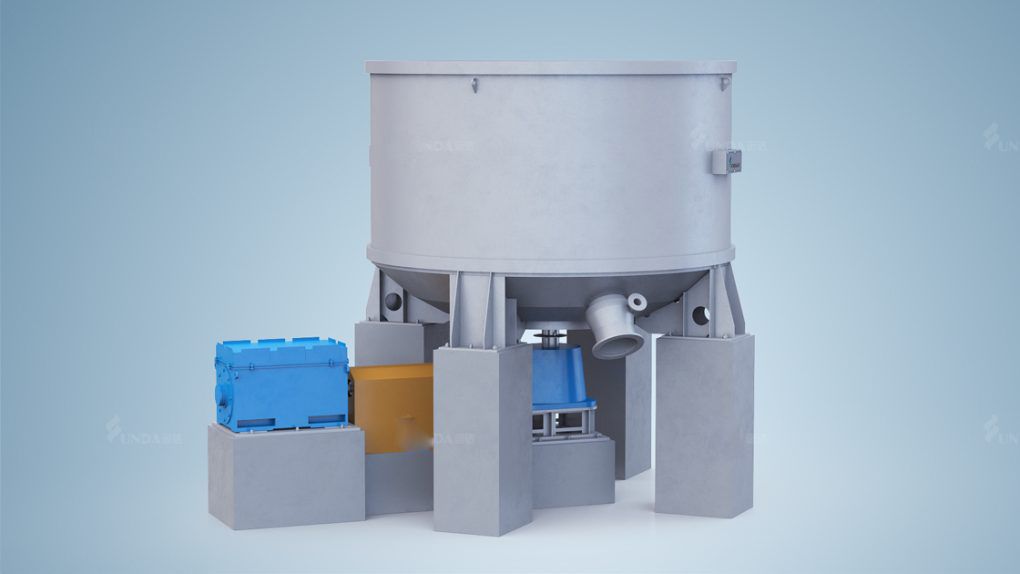
Mid Consistency Pulper
Pulpuer is mainly to pulp kinds of pulp boards, broke and waste paper. It features strong pulping capability, broad scope of application, simple structure and friendly operation and maintenance, etc., thus is comparatively ideal OCC pulping equipment in modern time.
Structure
Hydrapulper is composed of vat body, rotor and transmission device,etc.
The vat body is welded by stainless steel, the top of vat has a conical opening to avoid stock from splashing.
The lower steel flange connects with transmission part. there are guiding plates installed at the bottom of vat to form recirculation when stock backflow, reject channel and reject outlet are cocated in the bottom.
Below the vat is transmission device, which is main shaft, bearing, bearing base, belt pulley and so on.
Below the rotor is screen plate, it can select holes of different sizes according to customer needs.
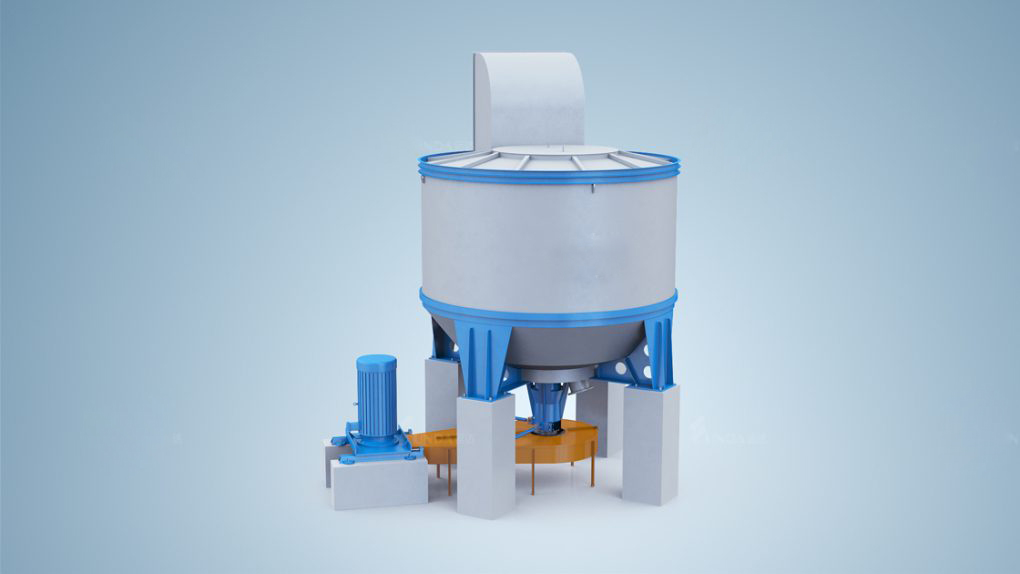
Broke Pulper
Broke Pulper is mainly used for pulping kinds of broke and waste paper,pulper rotor is installed horizontally and heavy rejects sink to the bottom.
of the tank; reduce the loss of the slag, prevent the screen hole from being blocked.
Advantages
New energy saving rotor to improve the hydraulic circulation and pulping efficiency
Clearance between screen plate and rotor can be conveniently adjusted as required
Belt drive or reducer drive are optional according to work space on site
Single set or two sets parallel are both permitted
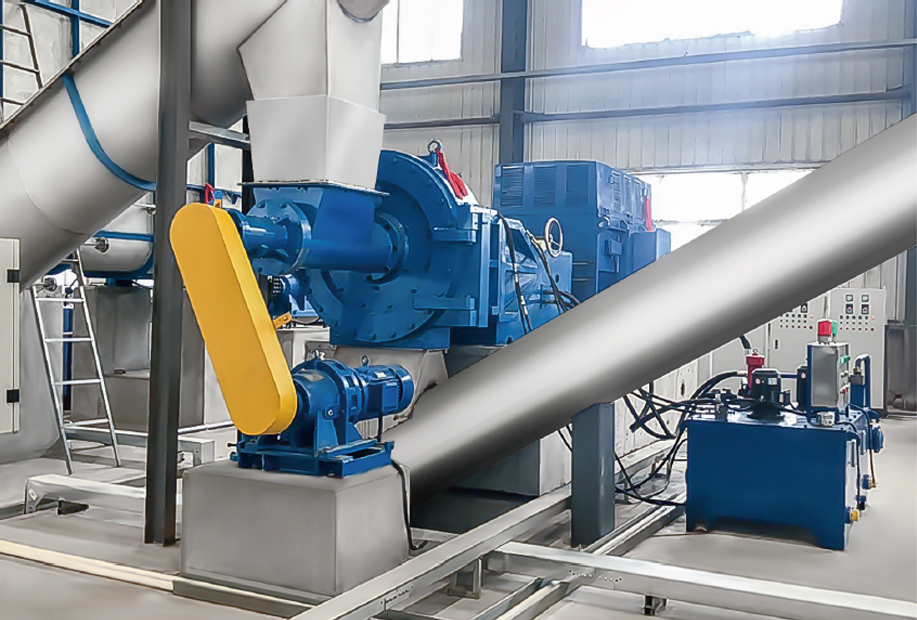
Refining and Deflaking and Thickening
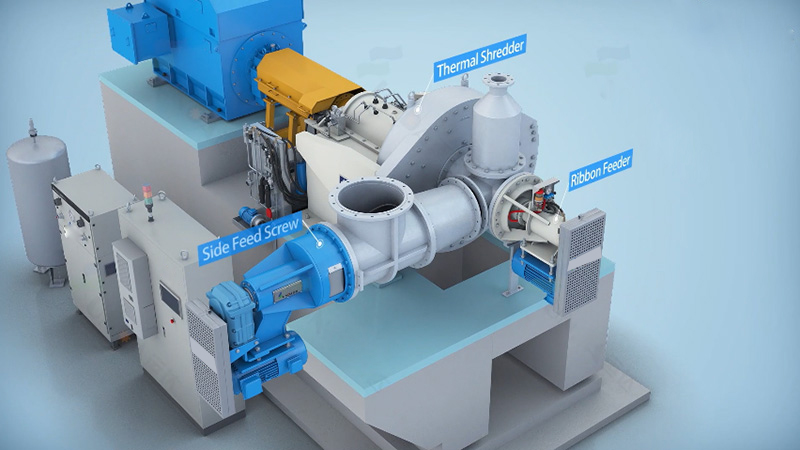
High Consistency Refiner
High Consistency Refiner(Thermal Shredder), Innovation design of the thermal shredder have a number of patents,which has superior performance, safety and reliability and wide range of raw materials. The main structure is composed of three parts: Thermal Shredder, Ribbon Feeder and Side feed Screw.
Raw materials such as wood chips, bamboo chips are going into the Host Pulping Zone through the high-speed rotating ribbon feeder, and after pulping chips enter the fiber coarse refining zone and fiber hair-like shreds zone. And it shredded into uniform hair-like shreds under the action of the rotary and stationary discs, where the chemicals are added at the same time. Compared to the chips, the hair-like shreds has a larger specific surface and higher chemical reaction efficiency, which reduce chemical consumption and pollution.
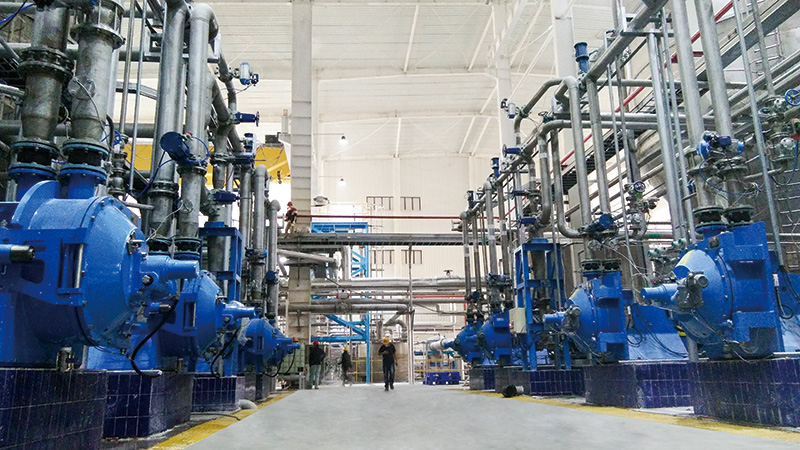
Double Disc Refiner
Double Disc Refiner is is a relatively ideal continuous pulping system at present. As required by pulping process, paper factories may choose a single set or several sets for parallel operation or series operation
Advantages
Specially designed rotary disc is self aligned automatically under the function of stock.
According to refining requirement, clearance is adjustable through electromechanical device.
Special tool for easy and fast change of refiner disc.
High strength welded structure to ensure stable and reliable operation.
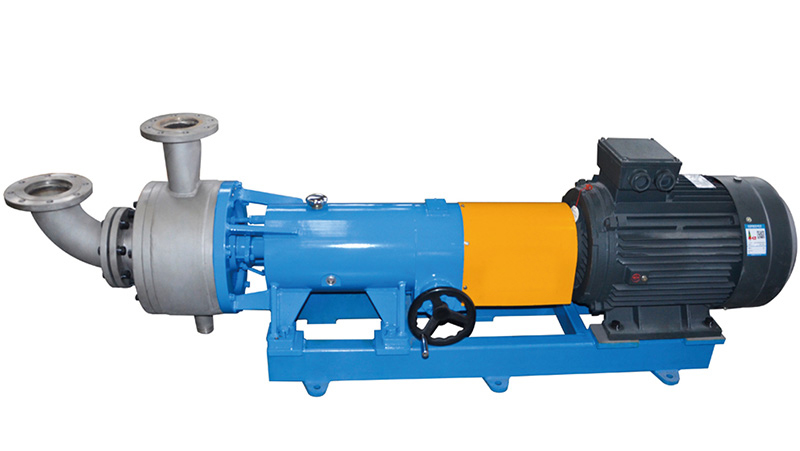
Fiber Deflaker
This machine is used for deflaking, applied for deflaking and evening kinds of stock (wood, straw, waste paper, etc.).. Single set or multi sets in series are allowed. As required by process, it also can be used in series with double disc refiner
Advantages
Compact structure
Lighter weight and smaller floor area
Higher efficiency and save more power
Stronger technological adaptability, easy operation and maintenance
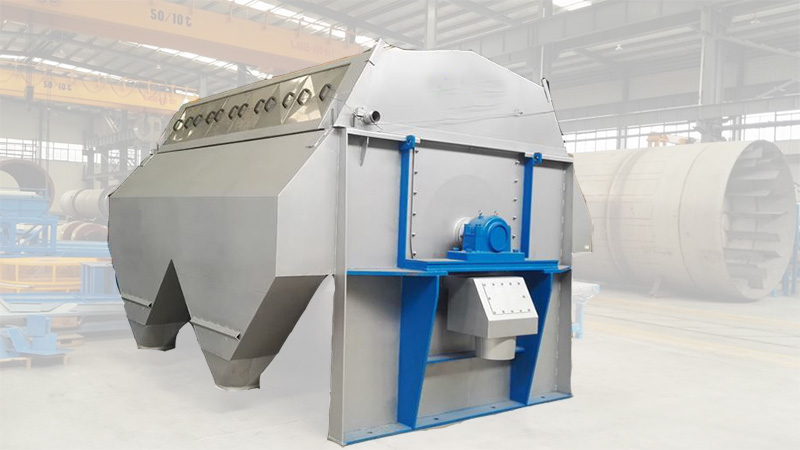
Disc Thickener
disc thickener belongs to continuous rotary thickening equipment, mainly used for dewatering and concentration of CTMP or Semi Chemical Pulp , waste paper pulp
Advantages
Mainly used for washing and thickening low consistency pulp;
Combined disk screen basket, greatly increase the filtering size, smaller floor area, larger capacity;
Stainless steel screen cloth, longer service life;
Rational washing structure, not easily blocked and strong dewatering capabilit
Screening and purifying equipment
Combi-Screen
Combination of defibering, screening and dehydration, cleaning production, higher fiber yield.
Advantages
No packing seal or mechanical seal required in the upper drive device reduces maintenance cost.
Combined screening separate heavy rejects and light rejects effectively, which will improve efficiency.
Light rejects above the liquid level is spun off by centrifugal force, higher dry degree and less fiber loss.
Combination of defibering, screening and dehydration, cleaning production, higher fiber yield.
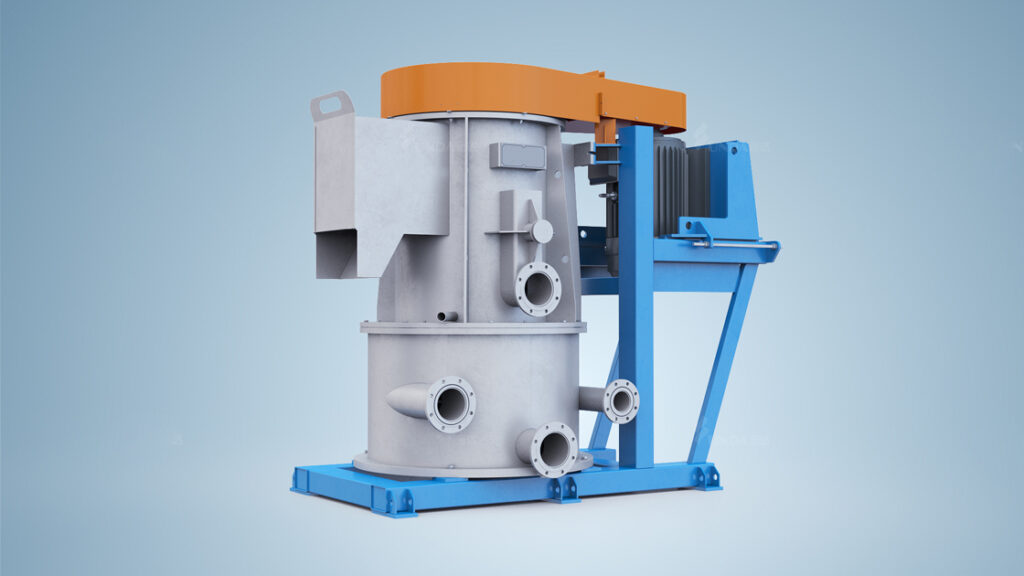
Head Box Screen
Head Box Screen (foil set outside the screen basket) featuring high screening quality, bigger capacity and lower pulp pulse, especially as a screening equipment used before the web of paper machine.
Advantages
Smaller motor power, lower energy consumption but bigger capacity.
Centripetal structure, low pulsation, good evenness on web.
Diffusing outlet design, smooth accept flow, companion flange without spacer, inner surface polishing treatment, seamless connection of pipeline, no fiber hanging.
Modular design for main motor and drive, stable and reliable structure, easy and fast installation and maintenance.
Equipped with auto oiling device and mechanical sealing water monitoring and alarming device, detection sensor port reserved to transfer bearing temperature rise and vibration, high automatic level.
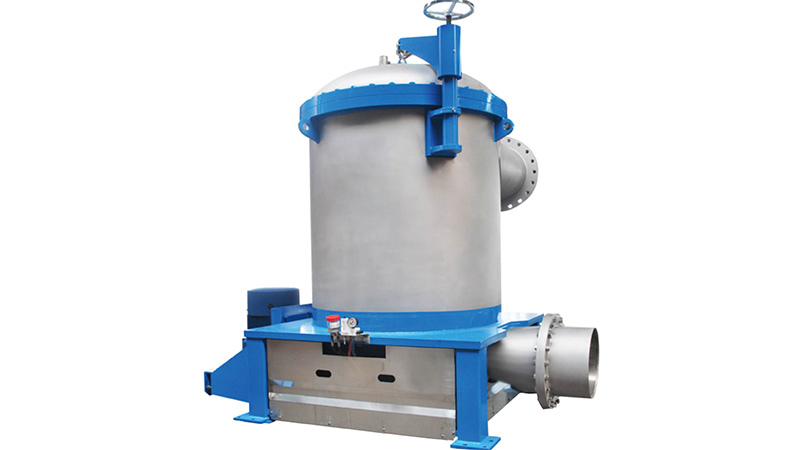
MC Screen
mid consistency screen applied to coarse screening or fine screening of CTMP、chemical pulp and waste paper pulp,strong adaptability, lower power and water consumption, high production efficiency
Advantages
Multi-foil design, no winding, gentle pulse, good screening effect, high pulse frequency and bigger capacity.
Mid consistency screen (Max. 4%), less water consumption in production, less energy cost, smaller screen basket size and lower investment and maintenance cost for same capacity.
Lower densification in screening section and higher screening efficiency, longer service life of screen basket.
Equipped with automatic oiling device and mechanical sealing water flow detection device, DCS interface reserved (detection of temperature rise and vibration of bearing), high degree of automation.
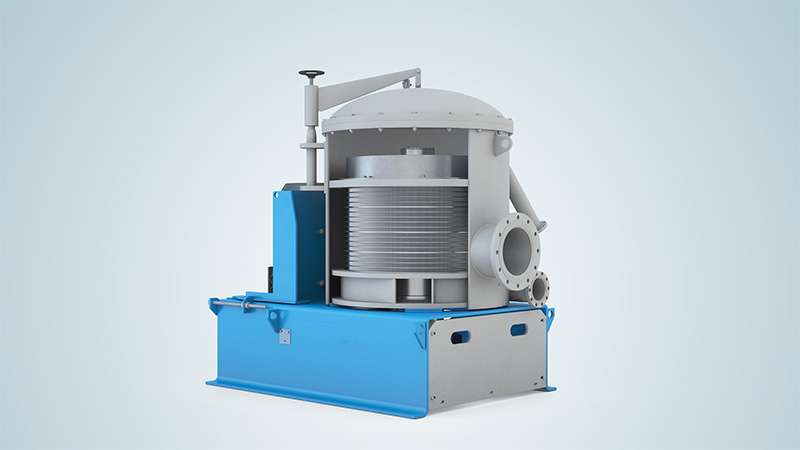
Super Screen
Super Screen is designed from three-dimensional simulation and fluid analysis technology, which finally provides high stickies removal efficiency, big throughput, high reliability and energy saving.
Advantages
Designed on basis of hydrodynamics theory, lower motor power, more energy saving.
Optimized rotor and screen basket design makes fiber sufficiently fluidized thus higher screening efficiency.
Module design, stable and reliable structure, saving labor and time for installation and maintenance.
Equipped with automatic oiling device and mechanical sealing water flow detection device, DCS interface reserved (detection of temperature rise and vibration of bearing), high degree of automation.
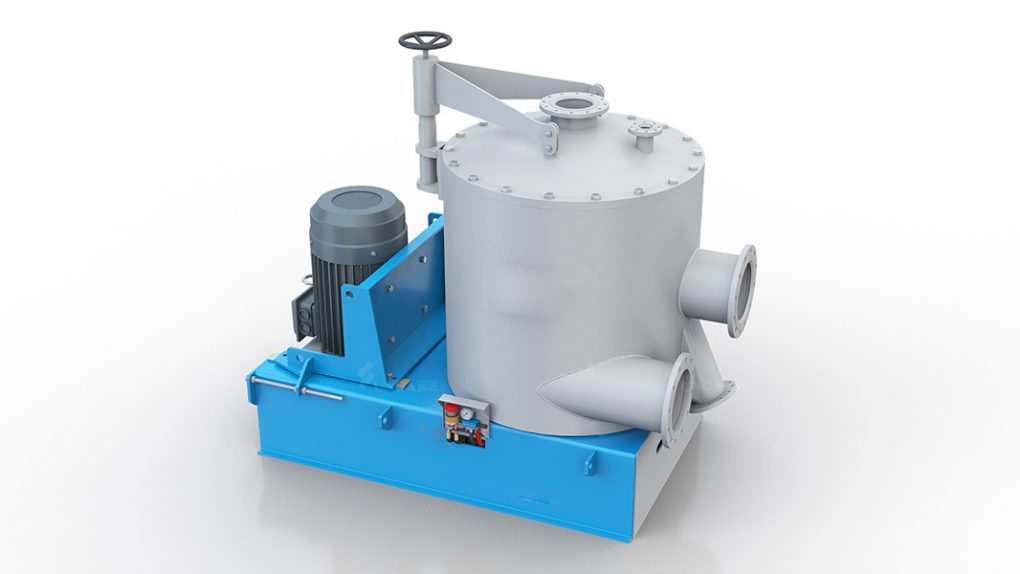
Float Purger
Float Purger is newly developed equipment to make waste paper pulp of high quality. Its functions are separating light and heavy impurities in waste paper pulp, secondary deflaking fiber, featuring high efficiency and energy saving. This machine is especially capable of removing the light impurities contained in the waste paper, collecting and removing the heavy impurities to clean the pulp.
Float Purger
ZQF Float Purger is newly developed equipment to make waste paper pulp of high quality. Its functions are separating light and heavy impurities in waste paper pulp, secondary deflaking fiber, featuring high efficiency and energy saving. This machine is especially capable of removing the light impurities contained in the waste paper, collecting and removing the heavy impurities to clean the pulp.
ZQF Float Purger is newly developed equipment to make waste paper pulp of high quality. Its functions are separating light and heavy impurities in waste paper pulp, secondary deflaking fiber, featuring high efficiency and energy saving. This machine is especially capable of removing the light impurities contained in the waste paper, collecting and removing the heavy impurities to clean the pulp.
Structure of Equipment
The float purger is mainly composed of shell, inlet and outlet pipe, screen plate, impeller and so on.
The shell of the float purger is a metal cone made from rolling and welding steel plate.
The inlet is located in the tangent direction on the side wall and at the upper part provided with light impurity outlet. The screen plate is installed at bottom part of the shell. Accepted pulp passes through the screen plate and then discharged through outlet pipe.
Rotating impeller is close to the screen plate, the clearance between the impeller and the screen plate is 1-3mm. The impeller is fixed to the spindle, which is supported by a rolling bearing and driven by motor through pulley.
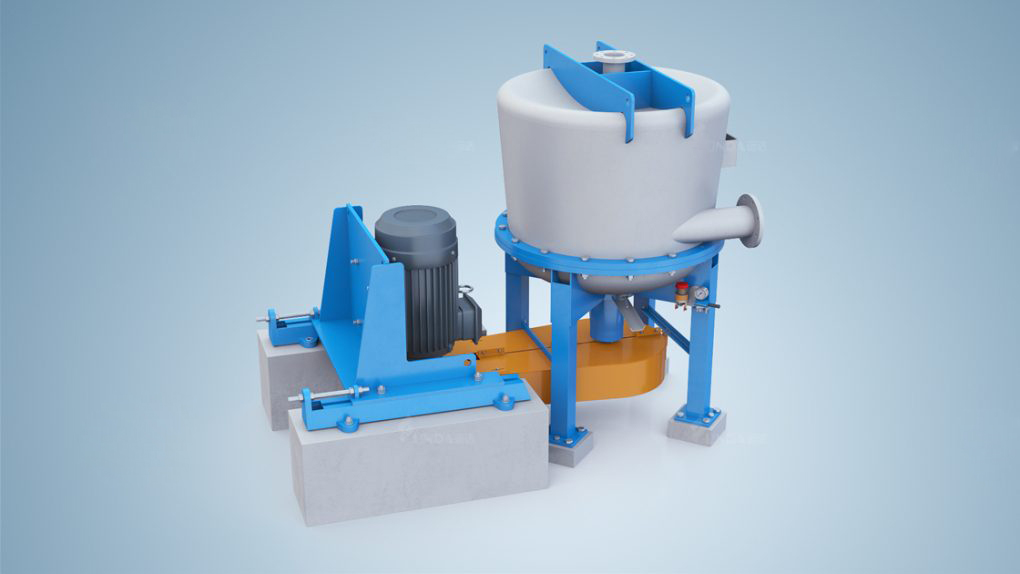
Vibrating Screen
vibrating screen Mainly used for the screen of light impurities ,It have self-cleaning function, high screen efficiency, save energy, low noise, easy maintain.
Advantages
Applicable for all kinds of reject handing at the last stage of screening and seperating.
Adopting double-row self-aligning roller bearing, reliable and stable operation.
Perfect screening ability with self-washing, high screening efficiency, easy operation and maintenance
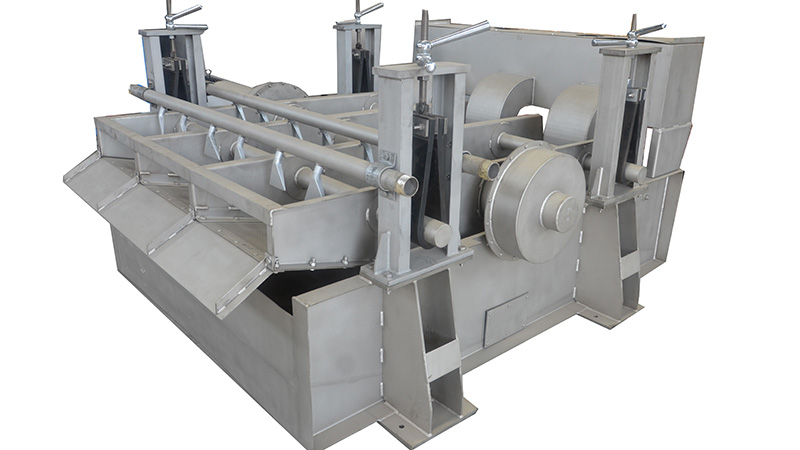
Reject Sorter
reject sorter is generally used to deal with impurities from coarse screen, with features of no vibration, less wear and complete closure.
Advantages
The coarse contaminants after handling by this machine have less fiber and almost no water. Thus, help reduce handling cost in the following procedure.
Low friction force due to special rotor design, almost no disintegration of contaminants, realize the high efficient separation of contaminants and pulp.
Upper cover can be opened for simpler and easier maintenance.
Equipped with washing pipe to reduce basket plugging and fiber loss.
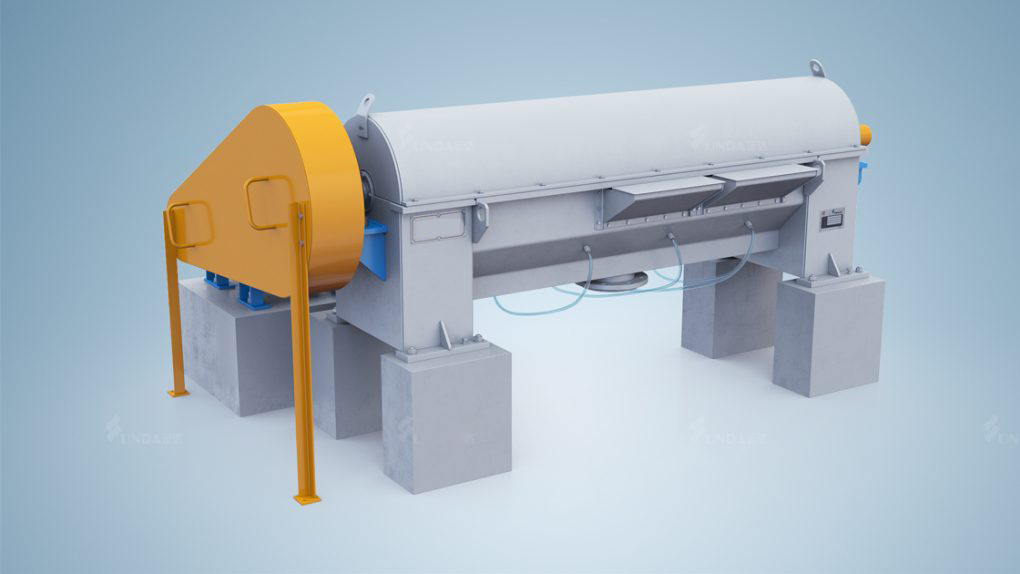
Fiber Sorter
fiber sorter used to separate heavy and light impurities in wastepaper stock and further defiber with higher efficiency but lower energy cost.
Advantages
Conical shell is in favor of separating and removing light and heavy impurities and defibering at the same time.
Separate light and heavy impurities effectively, defibering sufficiently, energy-saving.
Able to adopt automatic rejecting as required, reliable operation.
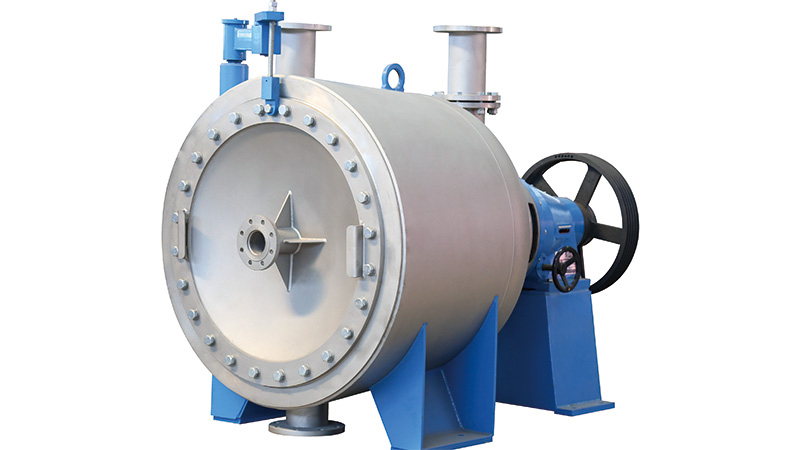
Reverse Cleaner
Reverse Cleaner is utilized for coarse screen or fine screen in tail pulp handling section of pulping line, washing tail pulp, recycling pulp fiber and rejecting waste plastics and furfural material.
Advantages
Screening by slotted cylindrical screen, higher efficiency
Combined belt drive, stable operation, lower noise
Fan-shaped spraying system, better light rejects screening
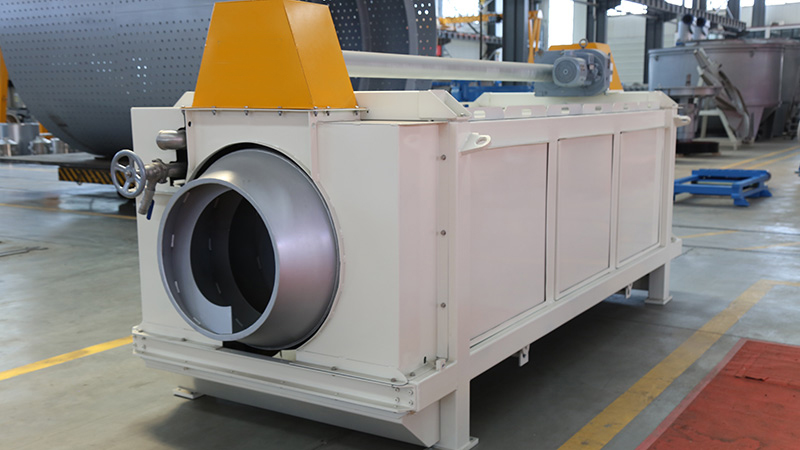