The fully-automatic high-end industrial packaging pulp molding production line is composed of a pulping system, host equipment, vacuum system, high pressure water system and an air compressor system, and is used to produce high-grade lining or outer packaging. The production line uses sugarcane pulp, bamboo pulp, wood pulp, reed pulp, straw pulp and other pulp boards as raw materials, and is blended into a slurry with a certain concentration through hydra pulping and a refining processes. Wet blank products are formed through vacuum with the pulp evenly attached on the metal mold, and then subjected to drying, hot pressing, trimming, stacking and other processes.
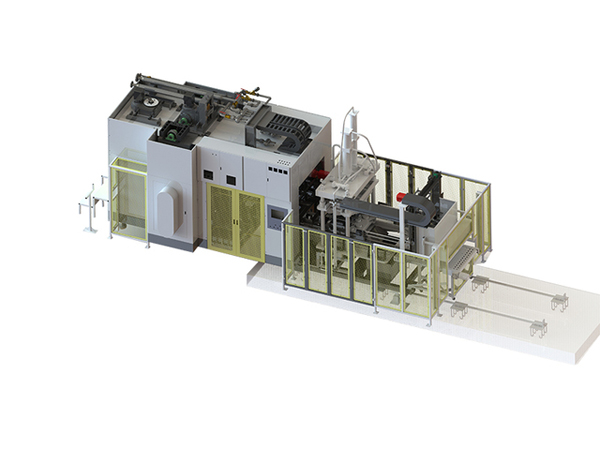
Fully-automatic High-end Industrial Packaging Pulp Molding Production Line
The fully-automatic high-end industrial packaging pulp molding production line is composed of a pulping system, host equipment, vacuum system, high pressure water system and an air compressor system, and is used to produce high-grade lining or outer packaging. The production line uses sugarcane pulp, bamboo pulp, wood pulp, reed pulp, straw pulp and other pulp boards as raw materials, and is blended into a slurry with a certain concentration through hydra pulping and a refining processes. Wet blank products are formed through vacuum with the pulp evenly attached on the metal mold, and then subjected to drying, hot pressing, trimming, stacking and other processes.
Automatic pulp molding equipment, pulp molding environmental protection tableware equipment, pulp molding cup lid production equipment, fine industrial packaging production equipment.
Automatic molding fiber (pulp) production line is an advanced new technology in the field of fiber (pulp) molding machinery. It has the following notable features:
Automatic pulp molding and cutting machine
Automatic pulp molding equipment, “forming, shaping, cutting, punching” in the same machine automatically completed, no need for secondary processing.
One machine with multiple functions
The same pulp molding equipment is suitable for the production of “environmental tableware”, “inverted hot drink cup lid”, “boutique small Angle industrial packaging”, “boutique egg box egg tray fruit and vegetable tray” and so on
Set automatic forming, shaping, cutting in one, the design is simple and compact, compact structure, small footprint
The production workshop of the same area, the production capacity is the production capacity of 2 to 3 workshops of the same machine. Greatly reduce the cost of civil construction, plant rent, management costs
Adopt full enclosed security protection
European and American design standards, complete fully closed safety protection door, open the door automatically shut down, CE certified automatic pulp molding production line.
High capacity, high automation, low energy consumption, low labor costs
Years of experience in pulp molding equipment and mold design and manufacturing, automatic pulp molding equipment is competitive in stability, vacuum and air pressure consumption, mold production cost, energy consumption and other aspects. The direct production cost of the product is greatly reduced, which is about 30% lower than that of conventional equipment.
The specific parameters are as follows:
Model | TSMP-9570 |
Equipment composition | Forming, hot pressing, trimming, stacking |
Platen Size | 1100mm*750mm |
Capacity Each Machine | 100,000pcs/day (basing on 80 cup lids) or 300-500kg(High-end Industrial Packaging, Capacity differs according to specific style) |
Outline Dimension(mm) | L 13000 * W 3230 * H 3850mm |
Forming Type | Single-sided flipping suction molding |
The forming minimum shut height is 130mm(mm) | 120 |
Hot-press standard mold closing height(mm) | 240~290 |
Forming Pressure | 5T |
Hot pressing pressure | 30T |
Trimming Pressure | 60T |
Product Height(mm) | ≤130 |
Workable Product angle (degree) | ≥7 |
Heating method electricity | Electricity |
Control method | Control method PLC + touch screen |
Remarks | The above parameters are for reference. Due to the continuous development of technology, relevant data will be continuously updated |

Models | Output Capacity | Floor | Staff | Electricity | Water |
FP2000 | 2000Kg/day | 24*18Meters, height ≥6 meters | 3persons/shift | 210-230KW/Hour | 0.05-0.1Tons/Hour |
FP3000 | 3000Kg/day | 24*18Meters, height ≥6 meters | 6persons/shift | 300-320KW/Hour | 0.1-0.2Tons/Hour |
FP4000 | 4000Kg/day | 24*36Meters, height ≥6 meters | 7persons/shift | 410-430KW/Hour | 0.2-0.3Tons/Hour |
FP6000 | 6000Kg/day | 24*48Meters, height ≥6 meters | 9persons/shift | 580-600KW/Hour | 0.3-0.4Tons/Hour |
FP8000 | 8000Kg/day | 24*72Meters, height ≥6 meters | 11persons/shift | 1070-1090KW/Hour | 0.5-0.6Tons/Hour |
FP10000 | 10000Kg/day | 24*72Meters, height ≥6 meters | 14persons/shift | 1280-1300KW/Hour | 0.6-0.7Tons/Hour |
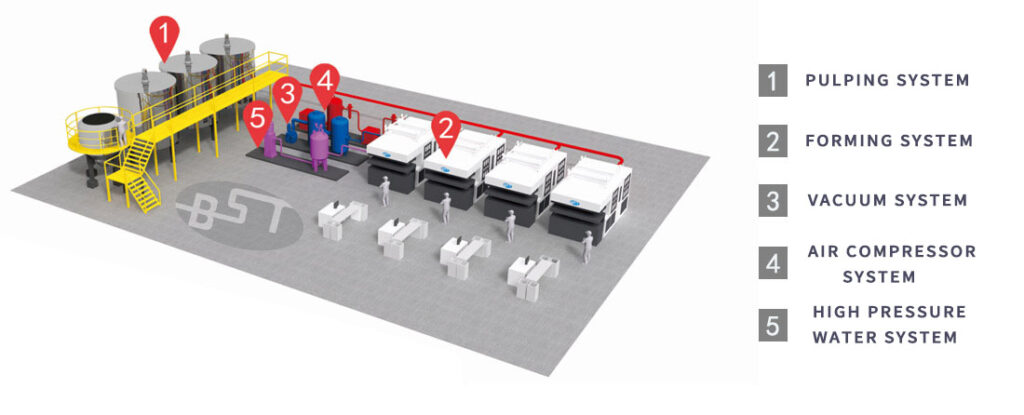
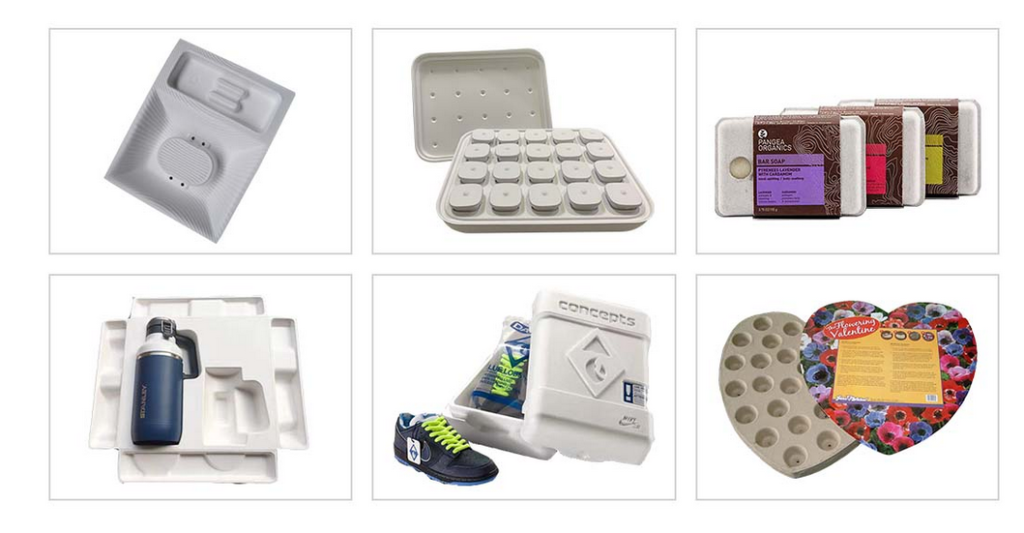