Fully automatic fruit jam production line, jam production equipment mainly includes cleaning equipment, lifting equipment, picking equipment, crushing equipment, pre cooking equipment, boiling equipment, glass bottle filling machine, bottle washing machine, capping machine, capping machine, pasteurization equipment, blow drying machine, labeling machine, inkjet printer, packing equipment, etc. Fruit cleaning equipment can use a high-pressure spray bubble cleaning machine. Track running through type cleaning, with bubbles and waves below and high-pressure spray cleaning above, double cleaning, clean thoroughly without damaging the product, high output, track conveying, saving labor and reducing labor.
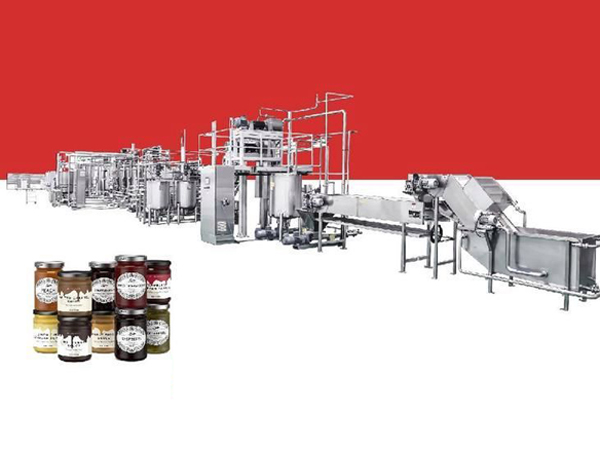
Fully automatic fruit jam production line
Customized sales technology advantages of jam production line equipment:
The jam production line mainly processes fresh fruits through cleaning, lifting, sorting, crushing, pulping, concentration and sterilization, and then aseptic filling to produce finished fruit jam in barrels. The entire production line is designed specifically for fruit sauce according to international quality standards.
- Crushing system: The whole fruit pipeline is broken, and the crushing process does not come into contact with air, ensuring the color of the fruit sauce.
- Energy saving and recycling of evaporator: The condensed water generated by the first effect is used for secondary evaporation and recycling in the second effect.
- Safety of sterilization machine: The sterilization agent is designed reasonably, and the Bix36-38 system pressure does not exceed 7Mpa.
Processing technology of jam production line equipment:
Fresh fruit → lifting → washing → fruit washing and sorting → crushing → preheating → sorting/pulping/refining → storage → concentration → storage → TIT disinfection → aseptic filling → finished product → pump → mixing system → F filtration → degassing → homogenizer → UHT sterilizer

Jam production line: including raw fruit lifting system, cleaning system, sorting system, crushing system, preheating and enzyme inactivation system, pulping system, vacuum concentration system, sterilization system, and sterile large bag filling system.
Jam processing:
- Including the lifting system, cleaning system, sorting system, crushing system, preheating and enzyme inactivation system, pulping system, vacuum concentration system, sterilization system, and sterile large bag filling system for the original fruit.
- The production capacity includes daily processing of 150 tons, 300 tons, 400 tons, 500 tons, 600 tons, 800 tons, 1000 tons, 1200 tons, 1500 tons, and 2500 tons of fresh tomatoes.
- Product concentration: 28-30%, 30-32%, 36-38%
- Under 300 tons, manual control or automatic control can be used.
A complete jam production line mainly includes the following parts:
——Suction system: used to extract raw materials from sterile large barrels or ton boxes;
——Sugar blending system: The tank is equipped with a digital analog static pressure level gauge to reduce manual intervention and workload, ensuring product quality;
——Vacuum sandwich pot boiling system: fully automatic PLC control, fully functional system, equipped with vacuum device, steam valve group, etc., specially designed condensation recovery device, can recover volatile aromatic substances to ensure product quality;
——Filling system: using a specially designed plunger filling form for filling high viscosity materials, fully automatic PLC control;
——Labeling or labeling system: fully automatic PLC control;
——Post pasteurization cooling system and post transport packaging: fully automatic PLC control;
——RO water system: fully automatic PLC control, used for preparing beverage water;
——CIP cleaning system. Independent Siemens control system, fully automatic PLC control.
Characteristics of jam production line:
The main structure is made of high-quality 304 or 316L stainless steel;
Integrate Italian technology and comply with European standards;
We can provide semi-automatic and fully automatic production lines for customers to choose from based on their actual needs;
The quality of terminal products is excellent, the quality of finished products is excellent, and the color is delicious;
High production efficiency, flexible production, and the ability to customize production lines according to customers’ actual needs;
Adopting fully automatic PLC control to reduce production labor intensity and improve production efficiency;
An independent Siemens control system that monitors various processing sections and systems.
The independent control system adheres to the design philosophy of:
- High degree of automation, maximizing the reduction of the number of operators;
- All electrical components are from top international brands, ensuring the stability and reliability of equipment operation;
During the production process, human-machine interface operation is adopted. The device operation and status are completed and displayed on the touch screen;
- The equipment adopts linkage control to automatically and intelligently respond to possible emergencies.