The definition of a fully automatic bottled water production line is very broad, commonly divided into three types based on capacity: 350ml, 550ml, and 600ml. The production capacity of bottled purified water production line can be achieved from 2000 bottles per hour to 24000 bottles per hour. The investment budget for the bottled purified water production line project ranges from 30000 to 1 million yuan. The common production lines for bottled purified water also have 3 gallon and 5 gallon options, which are 11.3L and 18.9L large bucket water packaging.
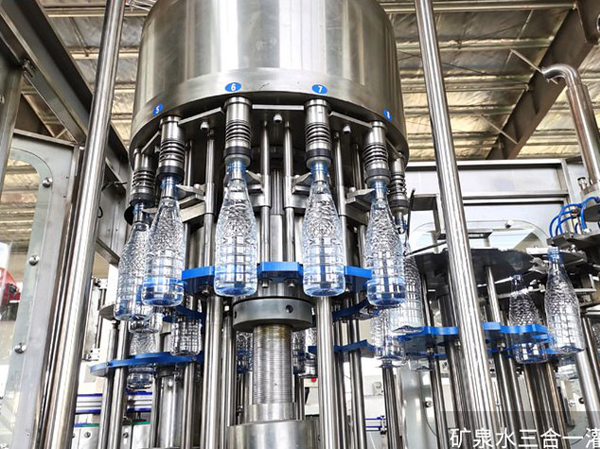
Fully automatic bottled water production line
Basic parameter configuration of bottled water production line equipment:
- Round or square polyester bottles.
- Bottle specifications: The bottle body is between 50 and 90 millimeters, the bottle height is between 150 and 320 millimeters, and the bottle diameter is between 20 and 35 millimeters.
- Bottle cap type: plastic threaded cap.
- Bottle cap specifications: outer diameter of Φ 25- Φ 35 millimeters, cap height H=15-25 millimeters.
Bottled water production process: water treatment → sterilization → filling → lamp inspection → labeling → drying → coding → film packaging → packaging of finished products
This production line is used for the production of plastic bottled purified water, mineral water and other beverages. It can customize a production line of 2000-36000 bottles per hour according to customer requirements and production volume. The entire production line includes water storage tanks, water treatment, sterilization equipment, blow molding machines, bottle sorting machines, air delivery, filling machines, lamp inspection, labeling machines, blow drying machines, inkjet printers, film wrapping machines, conveying, and conveying lubrication systems. The degree of automation can be configured according to customer requirements. The entire equipment design is advanced, and the electrical part adopts internationally or domestically renowned brands. We provide process flow and workshop layout design, and provide technical guidance throughout the process
Optional configuration:
Water treatment unit: purified water/mineral water/mountain spring water/functional water, etc
Bottle body label: set label/labeling
Spray code: laser spray code/ink spray code
Packaging: cardboard box/PE film
The bottled water production line includes water treatment, bottle production, filling, labeling, packaging, transportation, inspection, control and cleaning and disinfection equipment, and the specific configuration depends on the production scale and requirements.
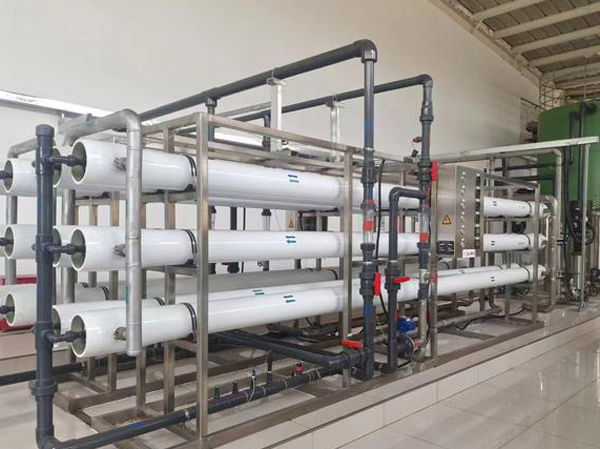
Water treatment equipment
Pre treatment system: including sand filtration, activated carbon filtration, and microfiltration, used to remove impurities from water.
Reverse osmosis system: used to remove dissolved solids and bacteria.
UV sterilizer: uses ultraviolet light to kill microorganisms in water.
Ozone generator: further disinfect water sources with ozone.
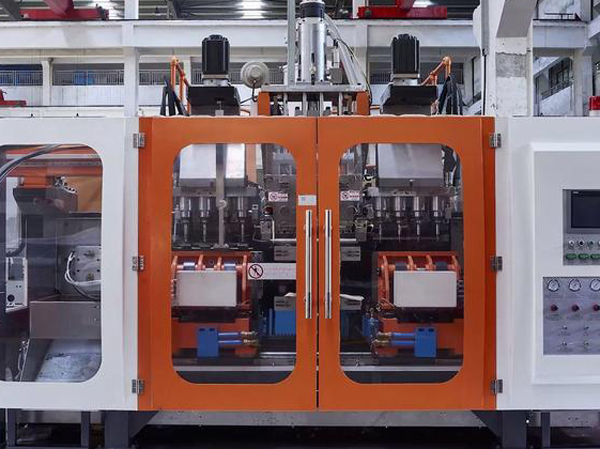
Bottle production equipment
Injection molding machine: a preform used for manufacturing bottles.
Blowing machine: Blows prefabricated blanks into finished bottles.
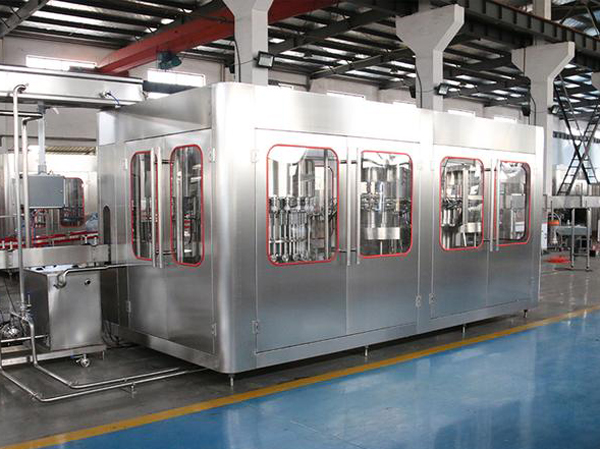
Filling equipment
Filling machine: Fill processed water into bottles, usually with gravity filling and pressure filling types.
Capping machine: used to seal the lid of a filled bottle.
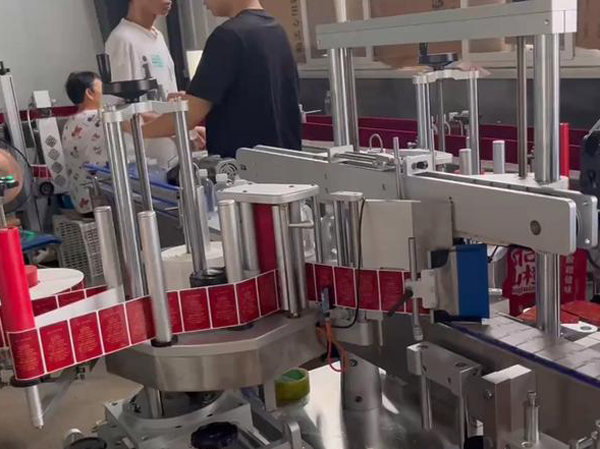
Labeling equipment
Labeling machine: Attach labels to bottles, which can be self-adhesive labels or heat shrink labels.
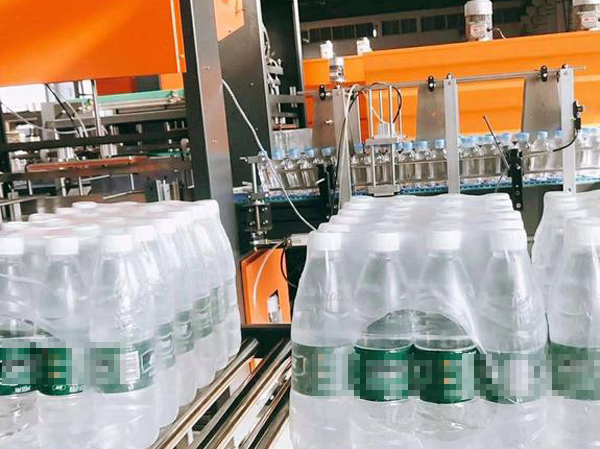
Packaging equipment
Shrink packaging machine: multiple bottles are put together for heat shrink packaging.
Carton packer: Put bottled water into the carton for outer packing.
Conveyor system:
Conveyor belt: connects various devices to ensure smooth flow of water bottles on the production line.
Inspection equipment:
Online detection instrument: used to check the quality of bottles and water, including bottle shape, liquid level, sealing, etc.
Control system:
PLC control system: used to monitor and control the operation of the entire production line, ensuring the coordination of various equipment.
Cleaning and disinfection equipment:
Bottle cleaning machine: cleans and disinfects used bottles.
The specific configuration of each production line may vary depending on the production scale and requirements, but the above equipment is a basic component of most bottled water production lines.
Main equipment of bottled purified water production line:
- Rack
The structural steel body has a 304 stainless steel layer on the exterior, a 304 stainless steel frame, and adjustable stainless steel feet.
- Bottle conveying system
The bottle conveying system adopts 304 stainless steel star wheels, and except for the bottle discharge star wheel, all other star wheels use bottleneck conveying The bottle is directly transported to the bottle feeding star wheel by wind power, ensuring the reliability of bottle operation and making bottle shape replacement more convenient and efficient The bottle dispensing wheel adopts a non bottleneck structure, which can avoid the need to adjust the height of the equipment chain surface after the three in one machine due to bottle height adjustment.
- Rotating bottle washing part
The bottle cleaning pliers adopt a stainless steel snap in structure, which does not touch the thread of the bottle mouth, ensuring stable and reliable bottle gripping, and high bottle cleaning efficiency.
- Rotary filling part
The parts in contact with the product are all made of 304 stainless steel, and the inner and outer surfaces of the filling cylinder are polished with mirror finish. The filling system adopts a filling cylinder and bottle lifting method to maintain the cleanliness and hygiene of the filling system. The filling method is gravity filling, which has a fast filling speed and can control the filling liquid level.
- Rotating sealing machine part
The capping head adopts magnetic capping, which has overload protection function and stable and reliable capping torque. The capping machine adopts the technology of Arol company in France, and there is no biting, high, crooked or curled edge phenomenon when capping. The screw cap sliding shaft adopts a rolling bearing structure, which ensures good alignment of the sliding shaft guide and high sealing qualification rate, reaching 99.7%.
- Lid organizer section
Horizontal pneumatic lid structure, 304 stainless steel lid compartment, 304 stainless steel lower lid groove, lid compartment and lower lid groove with electronic uncovered detection system, automatic control of lid feeding machine and machine operation speed. It can achieve no bottle, no lid delivery, and automatic shutdown without lid.
- Power system
Equipped with variable frequency speed regulation, all moving components are gear driven for smooth operation, and all bottle wheel gears are oil nylon gears.
- Electrical control system
Sealed electric control box, made of 304 stainless steel material, with variable frequency and stepless speed regulation. The whole machine is controlled by PLC industrial computer and displayed on a visible screen. The whole machine has the function of capped bottles but not capped bottles.
- Waterproof structure:
The host platform adopts a fully stainless steel platform with a water inlet for drainage. In order to prevent water from splashing onto the door and flowing to the bottom of the equipment during operation, a double-layer door waterproof structure is specially designed. The external door adopts a stainless steel integrated structure, and is equipped with an observation window and door handle, with neat and uniform upper and lower surfaces, presenting a beautiful and elegant appearance. The internal door adopts a plug-in design, which is waterproof to enter the equipment’s internal platform and electrical control box.