Steam boiler refers to the production of steam boiler equipment, which belongs to special equipment, its design, production, factory, installation must accept the supervision of the state technical supervision department, the user needs to obtain the boiler use certificate to operate the boiler. Different from atmospheric boilers, steam boilers must be delivered with boiler procedures, boiler procedures include boiler body drawing, installation drawing, instrument valve drawing, pipeline drawing and inspection certificate.
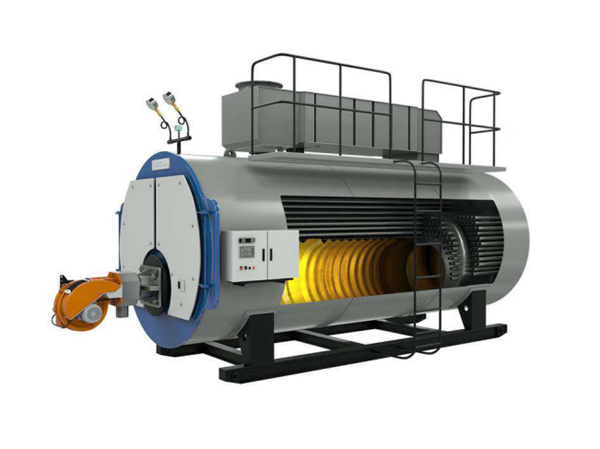
Commercial coal oil fired steam boiler manufacturer
Coal-fired fuel oil steam boiler, all products of the furnace type are packaged factory, to ensure that the boiler can be quickly installed in the user site, in addition to the need for water supply, gas supply and electrical connection accessories, do not have any other building structure and special installation process, before the boiler factory have carried out a series of testing and commissioning work, to ensure the boiler factory quality. The boiler is mainly composed of boiler body, connecting flue, burner, steam water system, instrument, energy saver, condenser and so on. Clean combustion, pollution-free emission, convenient operation, sufficient output.
Features of coal-fired oil-fired steam boiler:
1, the design and manufacture of the boiler in strict accordance with the “steam boiler safety supervision regulations” and “general technical conditions for Industrial boilers”, “boiler shell boiler body manufacturing technical conditions” requirements strictly implemented.
2, the furnace body is equipped with pressure gauge, safety valve, water level gauge and other instrument valves, the pressure gauge shows the pressure of the boiler, the user knows well; When the boiler reaches a certain pressure, the safety valve automatically opens, deflates and depresses, and ensures the safe and reliable operation of the boiler
3, vertical coal-fired fuel oil steam boiler, mainly by the shell head, furnace gall, furnace gall top, lower seal ring, cupola and cross water pipe composition, combustion chamber arranged in the furnace gall, fuel burning on the fixed grate, natural ventilation, flue gas in the furnace gall horizontal scour water pipe, through the cupola, chimney into the atmosphere.
- The horizontal coal-fired oil-fired steam boiler adopts a three-return water-fire tube structure with a single cylinder arranged longitudinally, and the water cooling wall tubes are densely covered on both sides of the furnace. The design structure is reasonable and compact; The heating area is large, the flue gas process is long, the heat transfer effect is good, the smoke exhaust temperature is low, so the thermal efficiency is high, the operating cost is low, and the use is more economical.
5, vertical coal-fired fuel oil steam boiler, the heating area of the pipe is all straight pipe, and there is enough cleaning hand hole device, easy to manual mechanical cleaning dirt and internal inspection. The upper part of the horizontal coal-fired oil-fired steam boiler is equipped with a manhole large enough for personnel to enter the furnace body from the manhole, which greatly facilitates the inspection and maintenance of the boiler.
6, coal-fired fuel steam boilers are randomly equipped with high-quality instrument valves and other safety accessories, complete sets of equipment safe and durable, user satisfaction. The user can choose the boiler softening water device – water treatment, adding water treatment, furnace gall scale is less, boiler safety and energy saving.
7, LSG type (vertical) series coal-fired fuel oil steam boiler using water-cooled pipe structure, scientific and reasonable design, heating up fast, large steam space, good steam quality.
8, DZG type (horizontal) series coal-fired fuel oil steam boiler adopts two return water and fire tube mixed structure, the boiler arranged a bunch of fire tube, the left and right sides of the furnace are equipped with water wall tube, heating surface is sufficient, high thermal efficiency. Hand coal, natural ventilation. The combustion is stable and sufficient, and the fire, heating and pressure increase are fast. Equipped with a number of protection devices such as water level gauge, safety valve, pressure gauge, etc., the operation status is clear at a glance, fundamentally eliminating the user’s worries, safe and reliable use.
9, DZH type (horizontal) series coal-fired fuel oil steam boiler adopts three return water and fire tube mixed structure, boiler body selection of threaded smoke pipe, strengthen heat transfer, energy saving and consumption reduction. With hand firing grate, easy to operate and convenient. The overall structure of the boiler is compact, beautiful appearance, convenient transportation and installation.
10, energy saving coal fuel steam boiler/coal steam boiler using fast factory, easy to install; The boiler structure is compact and reasonable, convenient for lifting and transportation. Widely used in hospitals, schools, textile factories, clothing factories, clothing supermarkets, clothing factories, dry cleaners, restaurants, hotels, restaurants, food factory, beverage factory, soybean products factory, meat products factory, canning factory, winery, pharmaceutical factory, packaging factory, building materials factory, coating factory, beauty salon, bath center, sauna, steam room and other places.
Item/Type | Coal Fired Steam Boiler | |||||||||
Rated capacity t/h | 1 | 2 | 4 | 6 | 8 | 10 | 12 | 15 | 20 | |
Rated steam pressure MPa | 0.7/1.25 | 0.7/1.25/1.6 | 1.25/1.6 | 1.25/1.6 | 1.25/1.6 | 1.25/1.6 | 1.25/1.6 | 1.25/1.6 | 1.25/1.6 | |
Rated steam temperature ℃ | 170/194 | 170/194/204 | 194/204 | 194/204 | 194/204 | 194/204 | 194/204 | 194/204 | 194/204 | |
Feed water temperature ℃ | 20 | |||||||||
Boiler thermal efficiency % | 78.1 | 80.2 | 82.3 | 82.5 | 82.5 | 82.9 | 82.9 | 83.1 | 83.1 | |
Body heating area m2 | 22.99 | 48.7 | 96.34 | 148.15 | 174.4 | 226.2 | 276 | 374.5 | 669 | |
Fuel & consumption | Fuel type | Class II Soft Coal, Biomass, Wood Chips, Wood Pellets, Rice Husk, Palm Kernel Shell, etc. | ||||||||
Coal kg/h | 118.76 | 231.30 | 450.79 | 674.54 | 899.39 | 1118.81 | 1342.57 | 1674.18 | 2232.23 | |
Biomass kg/h | 171.63 | 334.27 | 651.48 | 974.85 | 1299.81 | 1616.92 | 1940.30 | 2419.54 | 3226.05 | |
Size of boiler largest parts mm | Length | 4600 | 5800 | 6700 | 7000 | 7300 | 7600 | 7600 | 8500 | 9500 |
Width | 1900 | 2600 | 2700 | 3000 | 3000 | 3200 | 3200 | 3400 | 3800 | |
Height | 2900 | 3500 | 3500 | 3500 | 3500 | 3500 | 3500 | 3500 | 7100 | |
Weight of boiler largest parts ton | 18 | 22 | 30.1 | 40 | 21/14 | 23/17 | 23/19 | 21/24 | 25/24 |
Item/Type | Oil Gas steam boiler | ||||||||||||
Rated capacity t/h | 0.5 | 1 | 1.5 | 2 | 3 | 4 | 5 | 6 | 8 | 10 | 15 | 20 | |
Rated steam pressure MPa | 0.7/1.0/1.25/1.6 | ||||||||||||
Rated steam temperature ℃ | 170/184/194/204 | ||||||||||||
Boiler thermal efficiency % | 91.2 | 91.8 | 91.7 | 92.4 | 92.55 | 92.6 | 92.5 | 92.9 | 93.1 | 93.4 | 93.5 | 93.7 | |
Body heating area m2 | Boiler body | 13.05 | 21.15 | 33.14 | 45.1 | 67.87 | 80.37 | 110.5 | 140.13 | 194.27 | 142.3 | 218.5 | 275.3 |
Economizer | 10.4 | 18.6 | 20.4 | 26.1 | 30.4 | 43.41 | 46.5 | 57.1 | 74.4 | 112.6 | 155 | 225.5 | |
Boiler water volume m3 | 1.19 | 2.49 | 3.96 | 5.6 | 6.25 | 7.54 | 8.9 | 8.5 | 13.9 | 19.5 | 24.5 | 31.5 | |
Flue diameter mm | φ250 | φ350 | φ380 | φ420 | φ450 | φ520 | 750×410 | 800×410 | 940×520 | 850×500 | 1200×600 | 1500×600 | |
Water inlet diameter DN | 25 | 40 | 40 | 40 | 40 | 50 | 50 | 50 | 50 | 50 | 65 | 80 | |
Main steam valve diameter DN | 50 | 65/25 | 65/40 | 80/40 | 100/40 | 100/40 | 125/40 | 125/40 | 150/40 | 150/40 | 200/50 | 200/65 | |
Safety valve diameter DN | 40 | 50 | 2×40 | 2×40 | 2×40 | 50+40 | 2×50 | 2×65 | 2×65 | 2×80 | 2×100 | 2×100 | |
Blowdown diameter DN | 40 | 40 | 40 | 40 | 40 | 40 | 40 | 40 | 40 | 2×50 | 2×50 | 2×50 | |
Fuel consumption | Diesel kg/h | 30.03 | 59.70 | 89.65 | 118.63 | 177.65 | 236.74 | 296.25 | 353.97 | 470.95 | 586.79 | 879.25 | 1169.83 |
Natural gas Nm³/h | 36.72 | 73.01 | 109.63 | 145.07 | 217.25 | 289.51 | 362.28 | 432.40 | 573.44 | 717.57 | 1075.21 | 1430.55 | |
Largest transportation size | Length mm | 2550 | 3100 | 3750 | 3660 | 4600 | 4900 | 5250 | 5850 | 6500 | 6240 | 8500 | 9200 |
Width mm | 1450 | 2200 | 1950 | 2700 | 2200 | 2300 | 2350 | 2400 | 2600 | 2850 | 3500 | 3950 | |
Height mm | 1740 | 2200 | 2250 | 2630 | 2500 | 2650 | 2680 | 2700 | 2850 | 3100 | 4000 | 4350 | |
Largest transportation weight kg | 2300 | 3600 | 4400 | 5300 | 8000 | 8700 | 11200 | 12500 | 17800 | 22000 | 32500 | 40500 |
The coal-fired oil-fired steam boiler is mainly composed of pulverized coal preparation system, burner, heating surface, air preheater and other main parts.
Preparation system editing
There are two kinds of pulverized coal preparation systems commonly used. ① Direct blowing pulverizing system: the pulverized coal is directly sent into the furnace for combustion, and medium speed and high speed coal mills are suitable for grinding soft bituminous coal and lignite. The disadvantage is that the output of the mill and the fineness of the coal powder are related to the boiler load, so the operating number of the mill needs to be adjusted with the change of the boiler load, and the grinding parts are easy to wear. Direct blowing pulverizing system of medium speed coal mill is divided into positive pressure type and negative pressure type. Modern large capacity boilers mostly use positive pressure system. ② Intermediate storage pulverization system: characterized by the output of the mill and the fineness of the coal powder have nothing to do with the boiler load, it is suitable for the steel ball mill that can grind various kinds of hardness coal. The disadvantage is that the equipment is more complex direct blowing, the power consumption of the mill is larger, and the power consumption is not much different between no-load and full load, so it should be often run under full load.
Burner editing
Pulverized coal burner is the equipment that sends pulverized coal into the furnace for combustion, which can be divided into the following two kinds according to its structure. ① Swirl burner: The primary air carrying pulverized coal and the secondary air without pulverized coal are connected with the burner by different pipes. Pulverized coal and air can be fully mixed and form a reflux zone. Each boiler can be configured with 4 ~ 48 burners. ② Direct flow burner: the nozzle is narrow, and the first and second wind do not rotate in the burner. Pulverized coal can be completely burned in it.
Heating surface editing
The heating surface is divided into evaporative heating surface and superheated heating surface. Modern large and medium-sized boilers all form the furnace with a water cooling wall, so that the water cooling wall (that is, the heating surface) absorbs the radiant heat in the furnace and evaporates water into saturated steam. In order to increase the radiant heating surface without increasing the furnace volume, double-sided exposed water cooling walls can be used in large boilers. The superheating surface can be divided into the screen superheater heating surface arranged in the upper part of the furnace and the convection superheater heating surface arranged in the convection flue. The former absorbs radiant heat in the furnace; The latter absorbs convective heat.
Operation of coal-fired steam boilers
Fire boost edit
- Boiler ignition heating up After the inspection and preparation before the boiler ignition is completed, the ignition can be started. Ignition operation due to boiler combustion equipment is not
Same but different. The general requirements are: the furnace temperature rises slowly, and try to make the temperature of each part of the boiler rise evenly.
Before ignition, first open the wind and flue baffle of the boiler for natural ventilation or start the induced draft fan (the fan inlet baffle should be closed before starting, and then gradually open after the fan starts), and force ventilation for more than 5 minutes to remove the combustible gas accumulated in the flue, and prepare enough firewood and ignition materials. The ignition procedure of common combustion equipment :(1) The ignition of the hand-fired grate will first spread the wood and the kindling on the front of the grate and then ignite the kindling to ignite the wood, and after the burning is strong, throw a small amount of coal on the fire with the manual or coal thrower. When the coal is burning vigorously, the red fire will gradually move around until the coal is covered with all the grate, and gradually increase the amount of coal and increase the amount of air to make the burning prosperous. (2) The ignition of the mechanical grate “first lay a thin layer of coal on the grate between the coal gate and the back arch, and lay wood and primer on the coal, and then start the induced draft fan to keep the negative pressure of the furnace in the range of 10~ 30Pa. After igniting the kindling and firewood, wait for the firewood to burn steadily, turn the grate at the slowest speed to advance 0.5~1m, and then stop the grate rotation, wait for the coal burning strong, then start the grate and gradually accelerate the rotation speed, increase the amount of coal, start the blower, and open the baffle of each air chamber step by step with the movement of coal. Adjust the supply air volume. If necessary, the fire can be stirred from the fire door on both sides of the boiler, and the large pieces of wood that have not been burned can be moved to the front until the burning is normal (when the burning is normal, the coal should be on fire about 300mm away from the coal gate. 2. Ignition heating time In order to prevent local overheating of the boiler, resulting in uneven expansion and damage to the furnace structure, the length of the boiler ignition heating time should be determined according to the boiler structure. Under normal circumstances, for boilers with good water circulation, small capacity and evaporation capacity below 2t/h, the time from the cold furnace ignition to the pressure boost should not be less than 1.5h, and for boilers with poor water circulation, large water capacity and evaporation capacity of 4~10t/h, the ignition heating time is 3~5h.
3.
The setting pressure of the safety valve of the economizer, reheater and DC boiler start-up separator is 1.1 times of the working pressure at the installation site. The opening and closing pressure difference of the safety valve should generally be 4% to 7% of the setting pressure, and the maximum should not exceed 10%. When the setting pressure is less than 0.3OMPa, the maximum opening and closing pressure difference is 0.03Mh. The specific requirements are as follows: Note :1. There must be a safety valve on the boiler, which is set according to the lower setting pressure in the table. For boilers with superheaters, the safety room for setting at a lower setting pressure must be the safety valve on the superheater to ensure that the safety valve on the superheater is opened first. 2. The working pressure in the table, for the impulse type safety valve refers to the working pressure at the impulse discharge point, for other types of safety valve refers to the working pressure at the installation point of the safety valve 1) The calibration of the safety valve should be adjusted by the legal department or professional personnel, generally under the operating state of the boiler. Adjust the safety valve should be prepared in advance tools, check the safety valve and exhaust pipe should be intact, normal adjustment, the operator should wear protective equipment to prevent burns and falls, but also have a special person to monitor the water level. The fire potential of the furnace must be stable, the steam pressure should rise slowly, and the special person should read the steam pressure gauge to the operator
Value. Boilers with more than two safety valves should be calibrated one by one. If the safety valve does not work, it can be carried on the hand test, and is strictly prohibited for hammering. After the adjustment, an automatic exhaust test should be carried out again. If the opening pressure and return pressure meet the requirements, the check can be finished and the safety valve is sealed or locked. 2) Calibration method of safety valve When adjusting the spring type safety valve, the lifting handle and top cover should be removed, and the adjusting screw should be slowly turned with a wrench. When the specified pressure can be automatically discharged, the fixing screw can be tightened. When adjusting the lever type safety valve, first loosen the fixing screw of the heavy pallet, slowly move the heavy, and when the heavy pallet is moved to the specified pressure, it can automatically exhaust the steam and tighten the fixed screw.
3) In the adjustment of the safety valve, an opening test should be carried out to check whether the opening pressure of the safety valve is correct and whether the exhaust steam capacity is enough. After the safety valve is verified, it should be sealed or locked. It is strictly forbidden to press or jam with heavy objects.
4) After the safety valve is verified, the setting pressure, opening and closing pressure, sealing and other inspection conditions are recorded and archived. - Ignition booster precautions
(1) During the ignition heating, it is necessary to closely monitor the change of water level to prevent boiler water shortage accidents such as leakage due to improper opening of the valve or excessive water. (2) The boiler equipped with the economizer should open the bypass flue or open the recirculation valve through the water tank. If the economizer is equipped with the above protection device, the economizer can be cooled by draining water from the boiler side and pouring water into the boiler through the economizer. In addition, the outlet water temperature of the economizer must be controlled below the saturation temperature of 40 ° C. (3) The boiler equipped with superheater must fully open the superheater outlet trap to prevent the superheater from overheating and burning. (4) During the pressure boost process, pay attention to control the combustion, make it gradually strengthen, and pay attention to maintain stability. (5) After the valve on the steam pipeline is opened, in order to prevent the heat expansion after jamming, it should be fully opened and then closed half a circle. (6) The expansion indication of each part should be observed and recorded at any time according to the requirements of the operating rules during the process of temperature rise and pressure boost.
Boiler maintenance
Boiler maintenance can be divided into two kinds of dry maintenance and wet maintenance, dry maintenance is to drain the water in the furnace, put the desiccant such as lime or silica gel in the cylinder, and then seal, but the more troublesome is to open regularly to see whether the lime is dry, the silicone has no discolcolor. Wet maintenance is to fill the inside of the boiler with water, add maintenance agents in the water, and then seal the boiler, as long as the concentration of maintenance agents is enough, it can ensure that the inside of the boiler is not scaled, not corroded. The detection method is relatively simple, and the PH value of the furnace water can be measured. At the same time, the cost of wet maintenance may be lower than dry maintenance.