Burners for biomass gas steam boilers are provided by world-renowned manufacturers. They are automatically ignited and terminated according to the indication of the control panel. The individual plc controller has several emergency protection, emergency stability features and low retention. The current steam boiler automatic sensor, all Chinese liquid crystal display, industrial touch screen and customer is convenient to set, the boiler can be started according to customer needs, such as starting, adjusting the load, automatic tap water and so on. The boiler has perfect function, complete maintenance, simple operation, relatively stable, and self-diagnosis function. If there is an abnormal situation in the operation of the boiler, the incineration will be automatically cut off, and the sound and light alarm will be transmitted.
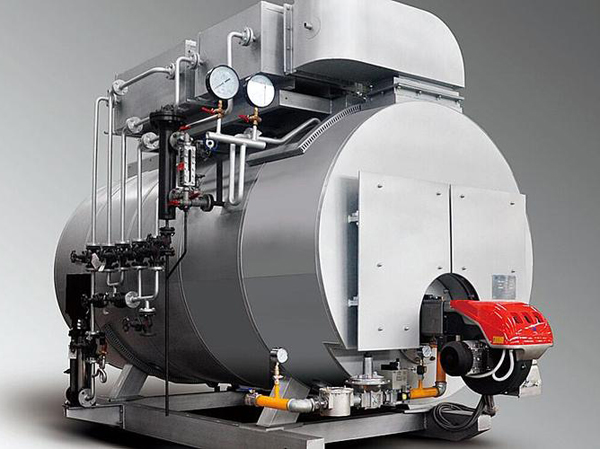
Commercial biomass gas fired steam boiler manufacturer
The boiler has a large storage tank space, a large amount of steam storage, and strong efficiency to accommodate the load. In order to meet the customer’s demand for high quality steam, an effective built-in gas-water separator is provided. The manhole, head hole and hand hole are set up in the furnace body, which is conducive to cleaning the interior of the furnace and making the overhaul and maintenance extremely convenient.
Boiler safety with multi-level interlock guarantee: Pressure controller protection (automatic termination and alarm of high set pressure), low water level protection (water level in the boiler significantly reduces the water level, automatically disconnects the electrical source and alarm), valves are protected (boiler pressure exceeds the working pressure), automatic gas discharge and pressure relief) to ensure that the boiler is safe under any working conditions, and it is safe to go out. The organic combination of mechatronics, beautiful novel, compact structure, small footprint, convenient transportation, convenient installation. Selection of new thermal insulation materials and high-quality white steel plate packaging, light net weight, good insulation characteristics, unique, not easy to rust.
The following matters should be noted in the application of steam boiler pressure gauges:
one. If the rated steam pressure is lower than 2.45MPa, the precision of the barometer should not be less than 2.5; The rated steam water pressure should be equivalent to 2.45MPa, and the water pressure should not be lower than 1.5. The diameter of the dial of the barometer should not be less than 100mm to ensure that the operator can clearly see the surface water pressure mark.
- Draw a red line on the dial of the steam boiler barometer to express the larger allowable pressure.
- The steam boiler barometer should be installed in an area conducive to observation and purging, and should avoid high temperature, freezing and vibration.
The steam boiler barometer should be checked at least once every five months, and should be sealed after correction. - Steam boiler pressure gauge connection pipe does not need to have water vapor leakage, otherwise the marked value of water pressure will be reduced.
Six. The accuracy level of the steam boiler barometer should be suitable for the pressure of the components under test, generally 1.5 or 3 times the pressure, and the most suitable pressure is twice.
Steam boiler does not have a barometer, the barometer is damaged or installed does not meet the requirements, if there is no one of the following conditions, steam boiler barometer should be disabled:
one. Surface tempered crushed or dial hazy.
2, no seal, seal damage or beyond the inspection period; - In the absence of water pressure, the gauge needle of the limited position can not be repaired to the limit foot position, and the number of infinite order gauge needle of the offset zero position exceeds the allowable range of water pressure layer. Destitute or needy;
4, leakage of steam in the table or dial flutter; - Other disadvantages that jeopardize the accuracy of the pressure gauge.
Item\model | Oil Gas Fired Steam Boiler | ||||||||
Rated steam capacity t/h | 0.1 | 0.2 | 0.3 | 0.5 | 0.8 | 1.0 | 1.5 | 2.0 | |
Rated working pressure MPa | 0.4/0.7 | 0.4/0.7 | 0.4/0.7 | 0.4/0.7/1.0 | 0.7/1.0 | 0.7/1.0 | 1.0 | 1.0/1.25 | |
Saturated steam temperature ℃ | 152/170 | 152/170 | 152/170 | 152/170 | 170/184 | 170/184 | 184 | 184/194 | |
Design efficiency % | ≧92 | ||||||||
Heated area m² | 2.85/3.53 | 5.2/5.67 | 8.8 | 11.34 | 18.4 | 23.1 | 26.05 | 29.38 | |
Boiler water capacity m3 | 0.45 | 0.454 | 0.931 | 1.086 | 1.37 | 2.76 | 2.27 | 2.27 | |
Flue diameter mm | Φ170 | Ф160 | Ф250 | Ф250 | Ф320 | Ф350 | Ф350 | Ф400 | |
Feed water diameter | DN25 | DN25 | DN25 | DN25 | DN40 | DN40 | DN40 | DN40 | |
Main steam tube diameter | DN25 | DN40 | DN40 | DN50 | DN65 | DN65 | DN65 | DN80 | |
Safety valve diameter | DN40 | DN40 | DN40 | DN40 | 2xDN40 | 2xDN40 | 2xDN40 | 2xDN40 | |
Blowdown tube diameter | DN40 | DN40 | DN40 | DN40 | DN40 | DN40 | DN40 | DN40 | |
Fuel consumption | Diesel kg/h | 5.4 | 10.8 | 16.3 | 27.1 | 43.4 | 54.2 | 81.3 | 108.4 |
Natural gas Nm³/h | 6.5 | 13.0 | 19.5 | 32.4 | 51.9 | 64.9 | 97.3 | 129.7 | |
LPG Nm³/h | 2.4 | 4.8 | 7.2 | 11.9 | 19.1 | 23.8 | 35.8 | 47.7 | |
Boiler size | L mm | 1000 | 1000 | 1200 | 1300 | 1550 | 1750 | 1800 | 2100 |
W mm | 950 | 1000 | 1150 | 1200 | 1520 | 1700 | 1800 | 1950 | |
H mm | 1900 | 1960 | 2200 | 2600 | 2650 | 3050 | 3100 | 3200 | |
Transportation weight (kg) | 450/730 | 650/735 | 990/1100 | 1500/1800 | 2400 | 2600/2850 | 4100 | 5400/5600 |
Item\Type | Cost Saving Biomass Fired Steam Boiler | ||||||
Rated capacity t/h | 0.5 | 1 | 2 | 3 | 4 | 6 | |
Rated steam pressure MPa | 0.7/1.0 | 0.7/1.0/1.25 | 1.0/1.25 | 1.0/1.25 | 1.25 | 1.25 | |
Rated steam temperature ℃ | 170/184 | 170/184/194 | 170/184/194 | 184/194 | 194 | 194 | |
Feed water temperature ℃ | 20 | 20 | 20 | 20 | 20 | 20 | |
Heated surface area m² | radiation / convection | 1.42/12.1 | 4.55/20.12 | 7.3/41.4 | 10.06/74.1 | 12.1/76.8 | 16/129.6 |
Suitable fuel type | Coal / Biomass / Wood / Charcoal / Jute / Fabric, ect. | ||||||
Boiler heat efficiency % | 79.2 | 80.2 | 81.1 | 81.2 | 81.6 | 81.7 | |
Fuel consumption kg/h | 84.62 | 167.14 | 330.56 | 342.67 | 454.65 | 681.15 | |
Effective area of grate m2 | 1.0 | 1.5 | 2.72 | 3.0 | 3.98 | 5.89 | |
Transportation size of boiler mm | length | 3270 | 4270 | 4900 | 5840 | 6735 | 6700 |
width | 1664 | 1920 | 2560 | 2660 | 2660 | 3000 | |
height | 2725 | 2870 | 3470 | 3520 | 3520 | 3600 | |
Weight of largest parts of boiler transportation (ton) | 7 | 11/11.6 | 16 | 25 | 27 | 28 | |
Notes: 1.This form is only for reference, if any changed, please refer to factory’s technical documents. 2.The calorific value of fuel in this form is based on the calorific value as follows: biomass-18800 KJ/kg. |