Boiler is a kind of energy conversion equipment, the energy input to the boiler is the chemical energy in the fuel, electric energy, boiler output has a certain heat of steam, high temperature water or organic heat carrier.
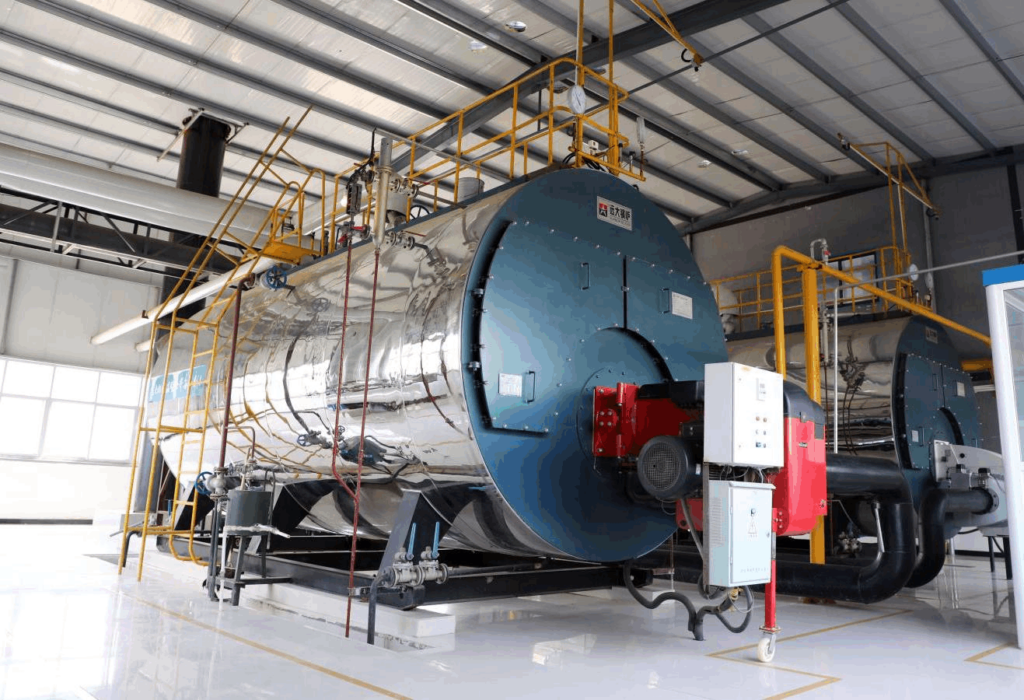
Boiler manufacturer
Fuels for industrial boilers are divided into three categories:
Solid fuel – bituminous coal, anthracite, lignite, peat, oil shale, wood chips, bagasse, rice bran, etc.;
Liquid fuel – heavy oil, clean oil, residual oil, diesel oil, etc.;
Gas fuels – natural gas, artificial gas, liquefied petroleum gas, etc
There are many types of boilers, and there are many classification methods, which can be roughly classified as follows:
(1) Classification by use: industrial boilers, power station boilers. Industrial boilers are mainly used for industrial production and heating, and power station boilers mainly use steam to drive steam turbines to generate electricity.
(2) According to the evaporation classification: there are small boilers, medium-sized boilers, large boilers. Boilers with an evaporation capacity of less than 20 tons/hour are called small boilers, boilers with an evaporation capacity of 20-75 tons/hour are called medium-sized boilers, and boilers with an evaporation capacity of more than 75 tons/hour are called large boilers.
(3) According to pressure classification: low pressure boiler, medium pressure boiler, high pressure boiler. The boiler with working pressure of not more than 2.5 mpa is a low-pressure boiler, the boiler with working pressure of 3.0-5.0 mpa is a medium pressure boiler, and the boiler with working pressure of 8-11 mpa is a high-pressure boiler.
(4) According to the medium classification: there are steam boilers, hot water boilers, steam and water dual-purpose boilers. The boiler outlet medium is saturated steam or superheated steam boiler into a steam boiler, the outlet medium is high temperature water (≥120 ° C) or low temperature water (below 120 ° C) boiler is called hot water boiler, steam and water dual-purpose boiler is both produced steam and can be used for hot water boiler.
(5) According to the combustion chamber layout classification: internal combustion boiler, external combustion boiler.
(6) According to the use of fuel classification: coal-fired boilers, oil-fired boilers, gas boilers.
⑺ According to the position of the cylinder classification: there are vertical boilers, horizontal boilers.
(8) Classification by boiler body type: shell boiler (fire tube boiler), water tube boiler.
(9) Classification by installation mode: there are whole boiler, (rapid loading boiler), bulk boiler.
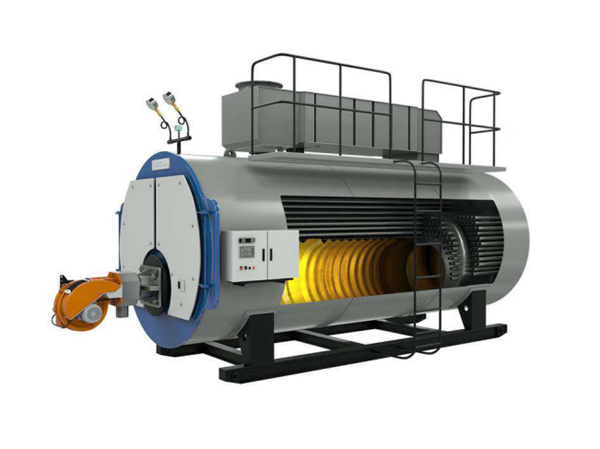
Boiler composition
1, “furnace” : is composed of combustion equipment, furnace wall, furnace arch and steel frame and other parts, so that the fuel combustion produces hot smoke part. Through the furnace and each section of flue gas to the boiler heating surface heat, and finally from the tail of the boiler into the chimney discharge.
2, “pot” : that is, the boiler body part, it includes boiler drum (drum), water wall tube, convection tube bundle, down pipe, header (header), superheater, economizer and other pressure parts, thus composed of the closed pressure part of the pot water and steam.
3, accessory instrument: In order to ensure the normal and safe operation of the boiler, the boiler needs to be equipped with some accessory instruments, such as safety valve, pressure gauge, water level meter (including two-color water level meter, high and low water level alarm, low status water level meter), low water level interlocking protection device, temperature meter, overtemperature alarm, flow meter, blowdown device, explosion-proof door, commonly used valves and automatic regulation device.
4, auxiliary equipment: auxiliary equipment is installed in the boiler this part of the necessary equipment, it is the supply of fuel system, ventilation system, water supply system, slag removal dust removal system and other devices and equipment, such as ball mill, coal equipment, water pump, water treatment device, blower, induced draft fan, slag removal machine, dust collector and soot blowing device.
The role of each part of the boiler body:
1, pot cylinder: the role of the cylinder is to collect, store, purify steam and supply water. All the hot water boiler cylinder is loaded with hot water, and the steam boiler boiler cylinder is loaded with hot water, the lower part of the boiler cylinder is hot water, the upper part is steam space, the surface of the water is called the water surface, and the position of the soda water boundary is called the water level.
- Water cooling wall: The cold wall is the radiant heating surface arranged around the furnace. It is the main heating surface of the boiler.
3, convection tube bundle: flow tube bundle is the convection heating surface of the boiler. The heat absorption of the high temperature flue gas is related to the flow rate of the flue gas, the arrangement of the pipe and the way of the flue gas washing.
4, the descending pipe: the role is to transport the water in the cylinder to the lower collection box, so that the heating surface pipe has enough circulating water to ensure reliable operation.
5, the header: called the header, it is mainly collected and distributed pot water, to ensure that the heating surface pipe reliable water supply or collection of the pipe water or soda mixture, the header generally should not be subject to radiation heat, so as to avoid the internal water bubble cooling is not good, overheating burned out.
6, superheater: the heater is the auxiliary heating surface of the steam boiler, its role is in the case of constant pressure, from the pot cylinder to lead saturated steam, and then heated, so that the water in the saturated steam evaporation and steam temperature rise, improve the quality of steam, become superheated steam.
7, economizer: Coal is arranged in the tail of the boiler flue, the use of smoke exhaust temperature waste heat to improve the feed water temperature of the heat exchanger, the role is to improve the feed water temperature, reduce smoke exhaust heat loss, improve the boiler thermal efficiency.
In general, for every 1℃ increase in the temperature of the economizer outlet, the boiler exhaust smoke temperature is reduced by 2-3℃ on average, and the feed water temperature is not increased by 6-7. Coal saving 1%, generally equipped with a economizer boiler can save coal 5-10%.
When the heating boiler is running, the combustible substance in the fuel is mixed with the air delivered to the furnace by the ventilation system at the appropriate temperature, and the heat is released, which is transferred to the pot water through the heating surface, the water temperature continues to rise, resulting in vaporization, and then the saturated steam enters the main steam valve through the steam separator for output and use. If the steam quality is higher.
The saturated steam can be put into the superheater and then heated to become the superheated steam output. For the hot water boiler, the pot water temperature is always below the boiling point temperature, and the user’s heating network is connected for circulation.
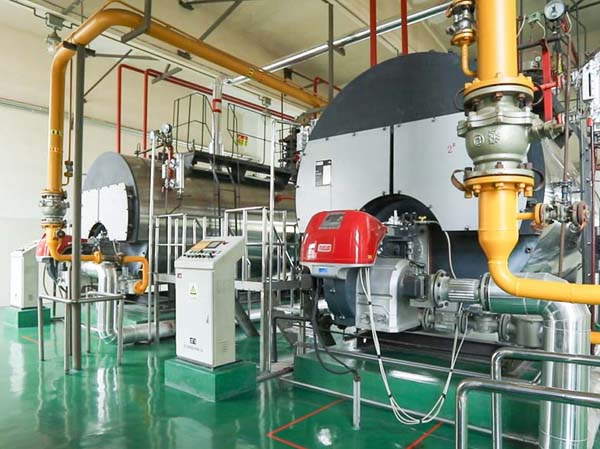
Boiler water circulation:
The boiler body is a closed circuit composed of boiler drum, down pipe, water wall pipe, header, convective tube bundle and other pressurized parts.
The water or soda mixture in the boiler is constantly flowing in this loop, following a certain route, and the flowing route constitutes a cyclic loop, called a circulation loop. The flow of water in the boiler in the circulation loop is called the boiler water cycle, and the number of cycles is different due to the different structure of the boiler.
The water circulation of the boiler is divided into two categories: natural circulation and forced circulation. General steam boiler water cycle is a natural cycle, hot water boiler water cycle is mostly forced circulation.
The natural cycle is to use the small weight and light weight of the soft water mixture in the rising pipe, the large weight of the water in the falling pipe, the heavier the weight, the pressure difference caused by the loss of balance between the two sections of the water column, resulting in the water flow and circulation of the boiler, the greater the weight difference between the two, the greater the pressure difference, the greater the driving force for the water cycle, the better the circulation. Forced circulation is the circulation of boiler water forced by the pushing action of the pump.
Boiler safety accessories:
In order to ensure the normal operation of the boiler, the boiler is equipped with pressure gauge, safety valve, water level gauge and high and low water level alarm, steam valve and blowdown valve and other accessories. Among them, the pressure gauge, safety valve and water level gauge are the basic accessories to ensure the safe operation of the boiler, known as the three main accessories of the boiler, and also the eyes and ears of the operator to carry out normal operation.
1, pressure gauge: The force meter is one of the essential safety accessories of the boiler, to measure and express the working pressure of the boiler steam water system. Boiler commonly used pressure gauge for the spring type pressure gauge, simple structure, accurate and reliable, installation and use is also very convenient.
Each boiler must be equipped with a pressure gauge directly connected with the steam space of the cylinder, and it is generally appropriate to set two parallel, easy to check each other. The pressure gauge must be checked at least once every six months after installation, and the verification date must be indicated.
In addition to the pressure gauge installed on the cylinder, the pressure gauge should also be installed in front of the economizer outlet and the regulating valve of the water supply pipe.
2, the safety valve, the whole valve is a safety accessory that can automatically control the working pressure of the boiler within the predetermined allowable range. When the boiler pressure exceeds the allowable working pressure, the safety valve will automatically open, and can quickly release enough steam to reduce the boiler pressure, while issuing an audible alarm to warn the furnace personnel in order to take the necessary measures to reduce the boiler pressure.
Commonly used safety valves are lever type safety valves and spring type safety valves.
3, the water level meter, the level meter is a reflection of the level of the measuring instrument, used to indicate the level of the water level in the boiler, can assist the furnace personnel to monitor the dynamics of the boiler water level, in order to control the boiler water level within the normal range.
In addition to the pressure gauge installed on the cylinder, the pressure gauge should also be installed in front of the economizer outlet and the regulating valve of the water supply pipe.
4, high and low water level alarm is a device that can automatically send an alarm signal when the boiler water level reaches the highest or lowest allowable limit. The floating body is used to automatically issue an alarm signal with the rise and fall of the boiler water level, so as to remind the operator to pay attention to the change of the water level, and take effective measures in time to prevent the occurrence of water shortage and full water accidents.
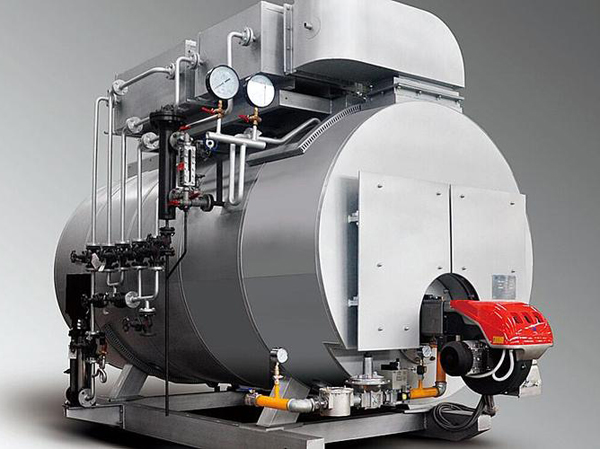
Common protection methods for furnace shutdown:
- Hydrazine anticorrosion, ammonia solution anticorrosion, alkali solution anticorrosion; Trisodium phosphate and sodium nitrite, desiccant anticorrosion, nitrogen filling, ammonia filling anticorrosion.
- Maintain feed water pressure and steam pressure; Hot furnace water, waste heat drying.
Drying oven: Purpose: dry the water of the furnace wall and the furnace arch, so as to avoid cracks in the furnace wall caused by sudden heating.
How:
(1) Heating is carried out according to the heating curve
(2) Daily temperature rise does not exceed (50℃) (20℃)
(3) Oven time: light furnace wall 4-6 days; Heavy furnace wall 10-14 days.
(4) Oven temperature: (final smoke temperature) light furnace wall does not exceed 160℃;
Heavy furnace wall does not exceed 220℃.
The purpose of water treatment is to change the boiler water (hard water) into soft water, so that the internal heating surface of the boiler is kept clean, no scaling (less scaling), improve the efficiency of the boiler and ensure the quality of steam, prevent the corrosion of the metal wall of the boiler, and ensure the safety and economy of the boiler and continuous operation.