The coal and oil burning hot thermal boiler is a vertical three-way water and fire tube mixed heating furnace, and a long series of spiral smoke tubes are arranged under the heating furnace barrel. The upper and lower sides of the furnace body are provided with smooth tubular water cooling walls. Selection of light air block grate, equipped with blower, booster fan to develop ventilation. After the oil falls in the grate, after the furnace is sufficiently lit, the flame enters the end of the element according to the smoke inlet of the furnace wall, enters the front cigarette box from both sides of the combustion chamber, the past cigarette box returns to the tube bundle in the pot, and enters the dust removal equipment according to the rear cigarette box. The ventilating fan is then vented into the air according to the flue.
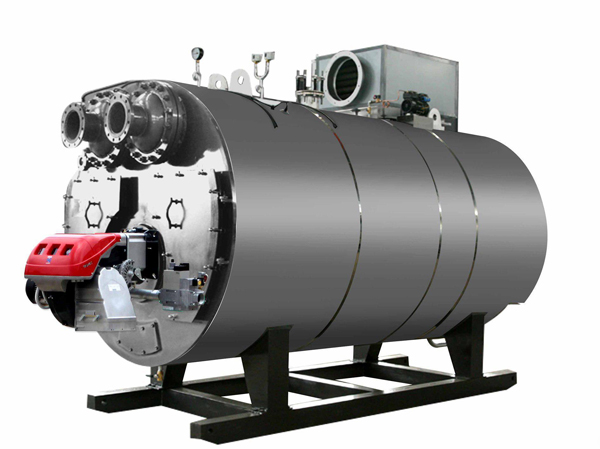
Coal diesel oil fired thermal boiler
Technical parameters
Model: DRS30~2400
Rated working pressure: 10MPa
Rated thermal power: 30~24million kcal/hour
Applicable fuel: light oil, natural gas, urban gas augmentation, heavy oil,
light oil/natural gas dual-purpose, light oil/urban medium gas dual-purpose
boiler is high-tech, energy-saving and environmentally friendly independently developed by our company that integrates electromechanical, combustion and heat exchange. The boiler adopts a modular design. The body is composed of tight spiral coils and is combined with enhanced heat transfer modules to form a three-pass flue gas structural solution. Mosquito-coil-shaped coils are installed at the front and rear of the furnace, and transition coils are installed at the gaps in the inner coils. The entire furnace is completely covered by oil pipes. The application of enhanced heat transfer modules gives the boiler a sufficient heating area, combined with an efficient fully oil-cooled fireplace, to ensure that the boiler’s thermal efficiency and environmentally friendly emissions meet regulatory requirements.
Item | Thermal Oil boiler for Chemical Industry Coal Fuel | ||||||||||||||||
Rated thermal power | kw | 1900 | 2300 | 2900 | 3500 | 4100 | 4700 | 5900 | 7000 | 8200 | 9400 | 12000 | 14000 | 16500 | 17500 | 19000 | 23500 |
×104(Kcal/h) | 160 | 200 | 250 | 300 | 350 | 400 | 500 | 600 | 700 | 800 | 1000 | 1200 | 1400 | 1500 | 1500 | 2000 | |
Boiler thermal efficiency % | 82 | 83 | 83 | 83 | 83 | 83 | 84 | 84 | 84 | 84 | 84 | 85 | 85 | 85 | 85 | 85 | |
Design pressure Mpa | 1.1 | 1.1 | 1.1 | 1.1 | 1.1 | 1.1 | 1.1 | 1.1 | 1.1 | 1.1 | 1.1 | 1.1 | 1.1 | 1.1 | 1.1 | 1.1 | |
Max. working temperature ℃ | 320 | 320 | 320 | 320 | 320 | 320 | 320 | 320 | 320 | 320 | 320 | 320 | 320 | 320 | 320 | 320 | |
Medium circulation flow m3/h | 160 | 160 | 200 | 200 | 200 | 260 | 300 | 340 | 400 | 520 | 500 | 620 | 800 | 1000 | 1000 | 1000 | |
Medium volume m3 | 1.7 | 2.6 | 3 | 3.2 | 3.5 | 4.1 | 4.6 | 6.2 | 8.9 | 12.6 | 13.6 | 14.8 | 16.5 | 18.2 | 19.7 | 22.3 | |
Main pipe diameter DN | 150 | 150 | 200 | 200 | 200 | 200 | 250 | 250 | 250 | 300 | 300 | 350 | 350 | 400 | 400 | 400 | |
Installation capacity kw | 75 | 77 | 100 | 100 | 120 | 140 | 175 | 215 | 215 | 270 | 315 | 380 | 460 | 540 | 600 | 620 | |
Fuel type | Bituminous Coal, Soft Coal, Anthracite, Lignite, Poor Coal, etc. | ||||||||||||||||
Fuel consumption | Coal kg/h | 307.01 | 367.17 | 462.95 | 558.73 | 654.51 | 750.30 | 930.65 | 1104.16 | 1293.44 | 1482.73 | 1892.84 | 2182.34 | 2572.04 | 2727.92 | 2961.74 | 3663.21 |
Biomass kg/h | 443.69 | 530.63 | 669.06 | 807.49 | 945.91 | 1084.34 | 1344.98 | 1595.74 | 1869.30 | 2142.86 | 2735.56 | 3153.94 | 3717.15 | 3942.43 | 4280.35 | 5294.12 | |
Boiler weight | ton | 25 | 32 | 33 | 39 | 41 | 67 | 70 | 80 | 98 | 108 | 115 | 130 | 140 | 170 | 197 | 225 |
Item/Type | Thermal Oil Boiler For Paper Industry | |||||||||||||||||||
Rated thermal power | kw | 350 | 600 | 900 | 1200 | 1500 | 1800 | 2300 | 2900 | 3500 | 4700 | 5900 | 7000 | 8200 | 9400 | 10500 | 12000 | 14000 | 15000 | 16000 |
×104(Kcal/h) | 30 | 50 | 75 | 100 | 130 | 150 | 250 | 250 | 300 | 400 | 500 | 600 | 700 | 800 | 900 | 1000 | 1200 | 1300 | 1400 | |
Boiler thermal efficiency % | 92 | 92 | 92 | 92 | 92 | 93 | 93 | 93 | 93 | 93 | 93 | 93 | 93 | 93 | 94 | 94 | 94 | 94 | 94 | |
Design pressure MPa | 1.1 | 1.1 | 1.1 | 1.1 | 1.1 | 1.1 | 1.1 | 1.1 | 1.1 | 1.1 | 1.1 | 1.1 | 1.1 | 1.1 | 1.1 | 1.1 | 1.1 | 1.1 | 1.1 | |
Max. working temperature ℃ | 320 | 320 | 320 | 320 | 320 | 320 | 320 | 320 | 320 | 320 | 320 | 320 | 320 | 320 | 320 | 320 | 320 | 320 | 320 | |
Medium circulation flow m3/h | 40 | 58 | 100 | 100 | 100 | 160 | 160 | 200 | 200 | 260 | 300 | 340 | 400 | 520 | 600 | 600 | 680 | 800 | 800 | |
Medium volume m3 | 0.4 | 0.6 | 0.6 | 0.8 | 1.2 | 2.1 | 2.6 | 3.5 | 7.8 | 8.4 | 8.8 | 10.5 | 11.2 | 11.5 | 13 | 15 | 18 | 21 | 23 | |
Main pipe diameter DN | 100 | 100 | 125 | 125 | 125 | 150 | 150 | 200 | 200 | 200 | 250 | 250 | 250 | 300 | 300 | 300 | 350 | 350 | 350 | |
Installation capacity kw | 14.5 | 18 | 31 | 37.5 | 49.5 | 57.5 | 61.5 | 75 | 75 | 98.5 | 121.5 | 148.5 | 155 | 195 | 235 | 235 | 295 | 341 | 341 | |
Fuel type | Diesel, Fuel Oil, Heavy Oil, Natural Gas, LPG, City Gas, Coke Oven Gas, Methane Gas, Biogas, Furnace Oil, etc. | |||||||||||||||||||
Fuel consumption | Diesel kg/h | 29.79 | 51.06 | 76.59 | 102.12 | 127.65 | 151.54 | 193.63 | 244.15 | 294.66 | 395.68 | 496.71 | 589.32 | 690.34 | 791.37 | 874.57 | 999.51 | 1166.09 | 1249.39 | 1332.68 |
Natural gas Nm³/h | 36.42 | 62.44 | 93.66 | 124.88 | 156.11 | 185.31 | 236.79 | 298.56 | 360.33 | 483.87 | 607.41 | 720.66 | 844.20 | 967.74 | 1069.49 | 1222.27 | 1425.98 | 1527.84 | 1629.70 | |
Boiler size m (Diameter×H) | 1.2×2.4 | 1.7×3 | 1.82×3.5 | 1.92×4 | 1.95×4.3 | 2.4×4.3 | 2.52×5.3 | 2.8×6.3 | 2.92×6 | 3.23×6.7 | 3.26×7.45 | 3.26×7.9 | 3.62×9 | 3.6×9.48 | 3.65×10.4 | 3.65×10.6 | 3.98×11.5 | 4×12.2 | 4.06×12.5 | |
Circulating oil pump | Model WRY | 80-50-180 | 100-65-190 | 100-65-230 | 100-65-240 | 100-65-257 | 125-80-250 | 125-80-250 | 125-100-250 | 125-100-250 | 125-100-257 | 125-100-260 | 150-125-270 | 125-100-250 | 125-100-257 | 125-100-260 | 125-100-260 | 150-125-270A | 150-125-280A | 150-125-280 |
Flow m³/h | 40 | 60 | 100 | 100 | 100 | 160 | 160 | 200 | 200 | 260 | 300 | 340 | 200×2 | 260×2 | 300×2 | 300×2 | 340×2 | 400×2 | 400×2 | |
Head m | 40 | 38 | 55 | 70 | 80 | 60 | 60 | 60 | 60 | 70 | 70 | 76 | 60 | 70 | 70 | 70 | 76 | 78 | 78 | |
Power kw | 7.5 | 11 | 22 | 30 | 37 | 45 | 45 | 55 | 55 | 75 | 90 |
Characteristics Characteristics:
one. DZH series quick installation heating furnace: composed of upper and lower parts. The upper end is composed of a furnace body, a furnace wall and a heat insulation layer. The lower part is composed of a talking grate and a door. The left and right composition structure saves the space occupied by the boiler room and reduces the installation profit and capital distribution.
- Arched tube plate and spiral smoke pipe are selected to produce boiler tube, so that the boiler tube is changed from the quasi-steel structure to the elastic structure, which eliminates the supporting plate in the tube plate area and reduces the shear force. In order to deal with the problem of cracks in the tube plate, the smoke pipe is changed from twice to once.
Three. The boiler has the advantages of stable operation, convenient adjustment, abundant output, fast temperature and pressure rise and simple operation.
- A wide range of applications: the furnace uses an efficient and power-saving arch, the overall pouring of high-temperature concrete, the improvement of the ignition standard of coal, the selection of a separate constant pressure valve, to maintain an effective cyclone spread, so that the furnace produces a gas energy field that is beneficial to ignition. Thus expanding the adaptability of coal.
- The selection of new furnace bricks and thermal insulation materials, the heat conduction damage of the furnace body is small, the thermal conductivity and heat value are improved. Because of the dry torsion of the smoke in the flue, the soot is not easy to accumulate in the pipeline, and has the effect of self-washing.
- Complete operation function, equipped with axial fan, booster fan, circulating pump, dust removal equipment, etc., reliable characteristics, stable safety, to ensure that the heating furnace will operate safely.