In a powder mixing system, the equipment, process steps and interacting parameters must all work together as an integral solution in order to ensure the optimal functionality, quality and efficiency of your total system. we carefully select, configure and integrate all the components and processes when designing a powder mixing system.
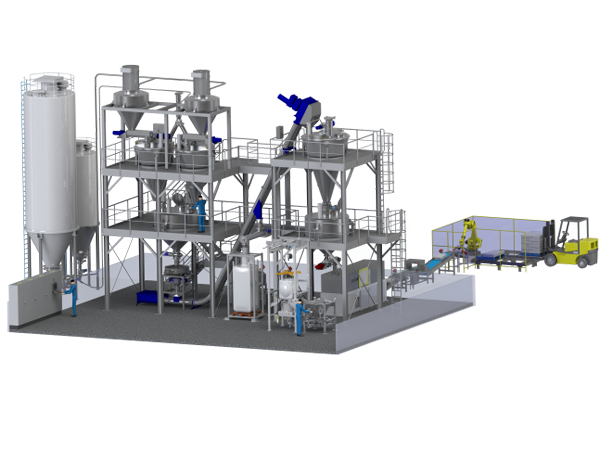
Bulk Solids Powders Mixing Production Line Systems
Weprovides a one-stop solution for the mixing, packaging machine system.
The system including the machine below
- Screw feeder with dust cover
- Ribbon blender
- Screw feeder
- Powder filling machine
Whether your requirements are for a single machine or turnkey process, we have rich experience to your project.
The picture is a typical small and medium-sized powder mixing and packaging production line.
The system is used for powder mixing. High standard mixing requirement.
Before mixing, there is a powder feeding table with vibrate sieve. Sieve the powder before mixing. The products convey by vacuum feeder, go into the paddle mixer.
Under the mixer, there is a hopper. After mixing, the products will be temporary storage on this hopper. Then delivery to the next step.
For the mixer, especially for food industry mixer, sanitation is very important.
Inside the blender, areas that present cleaning problems corners and discharge arrangements. Surfaces of the trough interiors and the agitator should be polished to help eliminate material sticking, buildup, and product contamination.
This mixer not only full weld and well polished, and mixing paddle could be full out to clean. Very convenient.
Processing technology of powder mixing systems
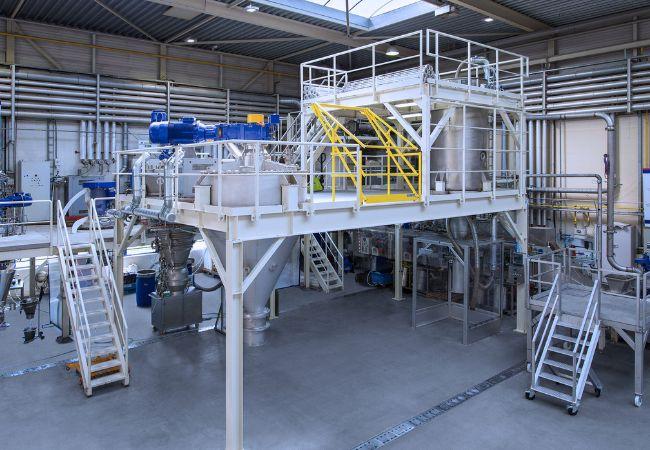
Offers flexible and effective solutions for the conveying and handling of powders, granules and bulk solids. Our design-to-application approach ensures the most beneficial and effective handling solutions are used, ranging from mechanical and aero-mechanical to pneumatic conveying. All our systems are custom-built with a focus on safety, reliability, efficiency and hygiene.
Dosing & Weighing
Accurate dosing and reliable weight-controlled filling systems are key to the quality of your process and final product. We design dosing, weighing and filling systems to suit every need: from liquids to powders, very low to very high feed rates, and batch or continuous feed.
Mixing & Blending
Our mixer range includes low, medium and high-shear mixers for both batch and continuous operation. We strike a balance between your specific application, product characteristics and upstream and downstream processes to select the right mixing technology for you.
Size reduction & Classification
classification and size-reduction technology is fast and efficient for numerous applications. We help you to identify the best solution based on your product specifications, chosen application and pre- and post-processing set-up.
Packaging & Storage
From bulk silos to hoppers and IBC containers, we offer a variety of packaging and bulk storage solutions for both raw materials and finished products, including the accurate and safe dustless filling of powders. Our dosing and weighing systems are suitable for pack-off into drums, bags and IBC systems.
Controls & Process Automation
Powder mixing systems include optimally integrated hardware and software controls to ensure consistently high product quality under varying circumstances. We can provide ergonomic and visual HMI-PLC panels including lot traceability, operator identification, remote service, alerts and customized data reports to give you full insight into your production processes.
Benefits of Powder Mixing Systems
Improved Product Quality
The uniform mixing ensures that each batch of powder is consistent in composition and quality, enhancing the overall product performance.
Increased Production Efficiency
The efficient mixing process reduces cycle times and minimizes waste, leading to higher throughput and lower production costs.
Enhanced Safety and Compliance
The hygienic design and automated controls help meet stringent food safety regulations and industry standards.
Cost-Effective Solution
Durable construction and low maintenance requirements make paddle mixers a cost-effective investment for long-term use.