Industrial molding pulp packaging production line, mainly used to produce a variety of general industrial packaging shock-proof products, such as home appliance packaging, electronic product packaging, instrument packaging, tool packaging, accessories packaging. Flexible configuration, professional diversified customization! Well-known electronic brand paper mold industrial packaging complete production system provider.
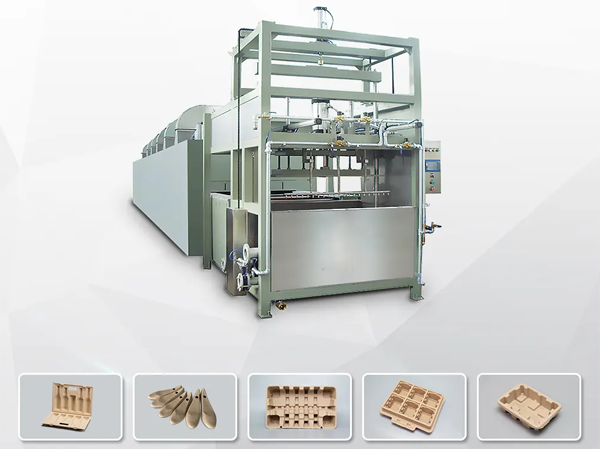
Pulp molding industrial packaging production line
Flexible configuration, professional and diversified customization! Renowned electronic brand paper mold industrial packaging complete production system provider. Mainly used for producing various ordinary industrial packaging shock resistant products, such as home appliance packaging, electronic product packaging, instrument packaging, tool packaging, accessory packaging, etc.
● Possess all types of paper mold packaging machine technology, which can more comprehensively focus on customer value;
● Various template sizes can be customized according to needs;
The cost of supporting molds is relatively low;
● Simple and flexible operation and maintenance;
Natural drying or optional drying channel or single-layer drying line.
Raw Material
The traditional raw material for pulp molding products is waste paper, including discarded newspapers, cardboard boxes, scraps from paper mills or printing factories, etc. The production process characteristics of pulp molded products determine their flexible and versatile structure, which can undergo significant elastic-plastic deformation, thereby playing a buffering role. Production is simple and fast, and can be recycled and reused in the future.
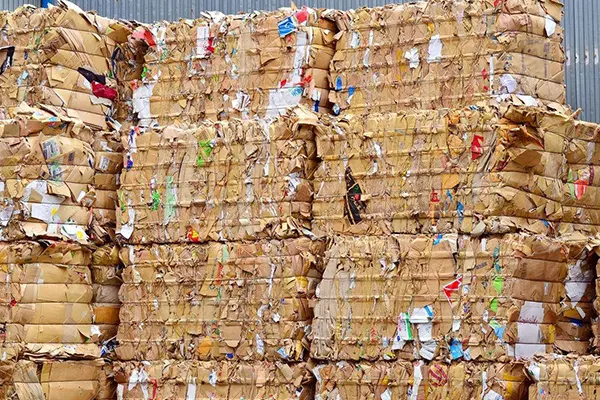
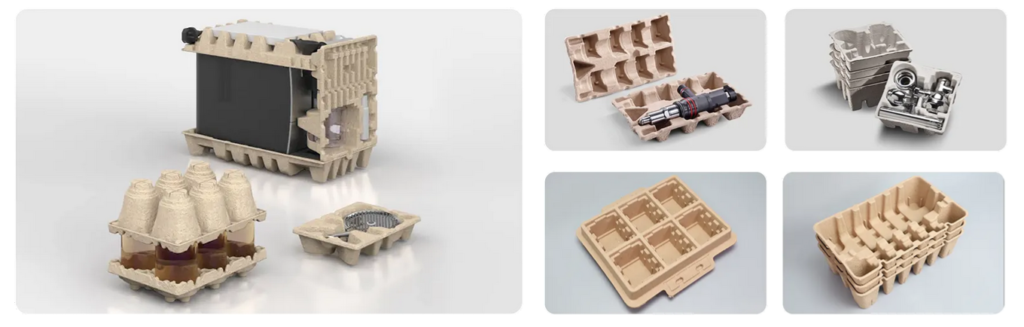
Final products
The Molded Pulp Industrial Packaging Machine produces a Mainly applied for producing all kinds of ordinary industrial packaging shock-proof products, like Household appliances packaging, electronic packaging, instruments and meters packaging, tools packaging, accessories packaging and so on.
Technical Parameters of Pulp molding industrial packaging production line
Model number | Reciprocating industrial molding pulp packaging line |
---|---|
Equipment composition | Forming upper template x1; Molded template x1; If the larger upper die of the template is automatically removed; Or match with the drying line to feed automatically |
Form size | Templates of different sizes can be customized on demand |
Forming method | Reciprocating forming |
Matching drying line | Natural drying or optional drying line or single layer drying line |
Drying energy | Heat conduction oil, natural gas or steam heating |
Control mode | PLC plus touch screen |
Design capacity | Depends on the product |
Raw material | ≤150mm |
Production Process of Automation pulp molding industrial packaging production line

Main machine of Molded Pulp Industrial Packaging Machine
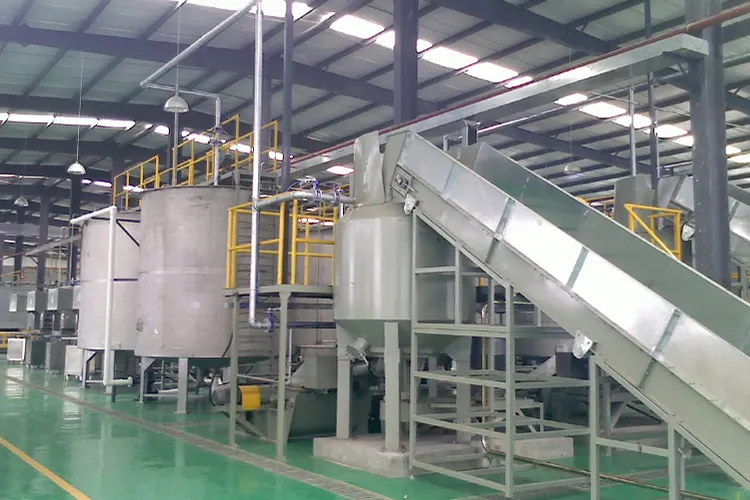
Pulping system:
The pulping system refers to the process of converting waste paper into usable molded pulp. This involves soaking, breaking, stirring, and pulping various raw materials such as newspapers, magazines, and other paper products. The goal is to produce a consistent slurry of pulp that can be used in the molding process.
- Pulper: Mixes waste paper with water and agitates to form a pulp;
- Refiner: Further processes the slurry to improve fiber quality;
- Agitators and Mixers: Keep the slurry in constant motion to ensure uniformity;
- Screening and Cleaning Systems: Remove impurities and oversized particles;
- Consistency Control: Adjusts the water-to-paper ratio for optimal slurry consistency;
- Storage Tanks: Hold the prepared pulp, ensuring a continuous supply to the molding machines.
Forming system:
The forming system utilizes the main pulp molding equipment, assisted by a positive and negative pressure system. This ensures that the pulp is evenly distributed on the mold. The forming system is crucial for shaping the pulp into egg trays with uniform thickness and strength. Once the pulp is molded, the trays are transferred to the drying system via the transfer mold.
- Molding Equipment: Shapes the pulp into egg trays;
- Positive and Negative Pressure System: Ensures even distribution of pulp on the mold;
- Transfer Mold: Moves the formed trays to the drying system;
- Transfer Mold: Moves the formed trays to the drying system.
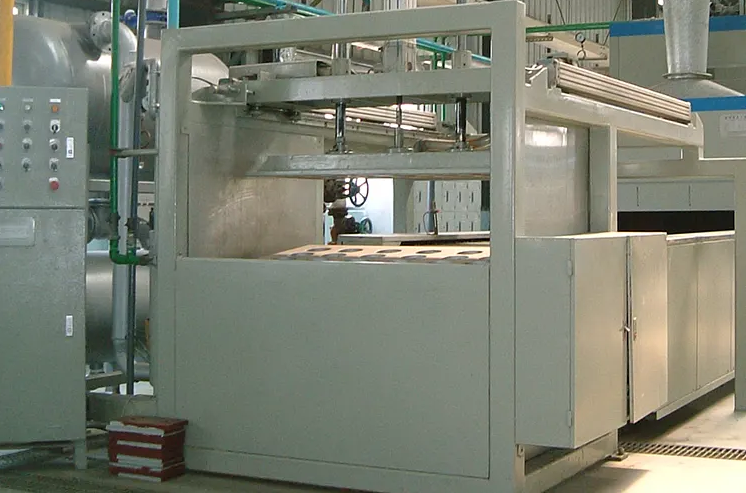
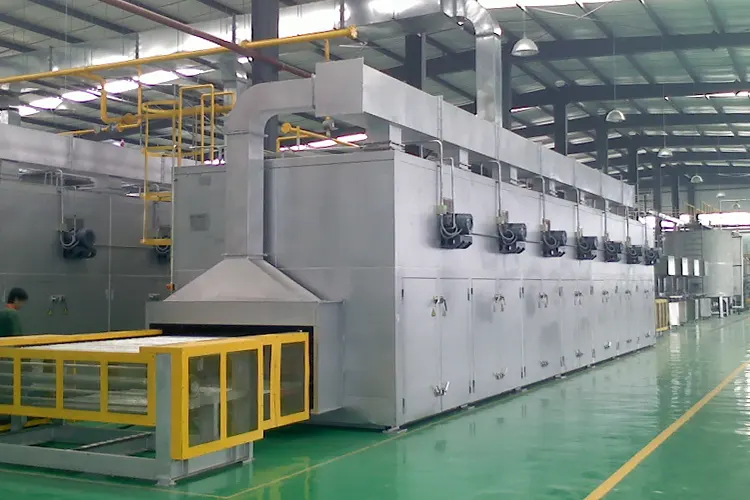
Drying system
The drying system can be heated by various methods, including burning coal, wood, natural gas, or electricity. The purpose is to dry the molded egg trays to ensure they are sturdy and ready for use. There are two main types of drying tunnels used for this purpose: civil construction drying tunnels and steel structure drying tunnels.
- Heating Source: Can use Thermal Oil, Natural Gas or Steam Heating;
- Drying Tunnel: Metal structure drying tunnel.
Unique Features of Molded Pulp Industrial Packaging Machine
Precision and Control
- Reciprocating Motion: The unique reciprocating motion of the machine ensures precise control over the molding process. This back-and-forth motion allows for consistent thickness and uniformity in the egg trays, leading to higher quality products.
Energy Efficiency
- Energy-Efficient Design: The machine is designed to minimize power consumption without compromising on productivity. This energy-efficient design reduces operational costs and contributes to environmental sustainability.
Ease of Maintenance
- User-Friendly Maintenance: The machine’s design facilitates easy maintenance and reduces downtime. Components are accessible and designed for quick servicing, ensuring that the machine remains operational for longer periods and production is not frequently interrupted.
Versatile Raw Material Use
- Wide Range of Raw Materials: The machine can process various types of waste paper, including newspapers, magazines, and other paper products. This versatility allows manufacturers to utilize readily available materials, reducing raw material costs and promoting recycling.
Advanced Forming System
- Positive and Negative Pressure System: The forming system uses a combination of positive and negative pressure to ensure even distribution of pulp on the mold. This advanced technology results in egg trays with consistent density and structural integrity.
Efficient Drying System
- Multiple Heating Options: The drying system offers flexibility with multiple heating options, including coal, wood, natural gas, and electricity. This allows manufacturers to choose the most cost-effective and available fuel source, optimizing operational efficiency.
- Choice of Drying Tunnels: The machine can be equipped with either a civil construction drying tunnel or a steel structure drying tunnel. This adaptability allows the machine to be tailored to different production environments and scales.
High Production Capacity
- High Throughput: Despite its energy efficiency, the machine maintains a high production capacity, making it suitable for large-scale operations. This ensures that manufacturers can meet high demand without compromising on quality or efficiency.
Eco-Friendly Operation
- Sustainable Production: By utilizing waste paper as the primary raw material and featuring energy-efficient operation, the machine supports eco-friendly production practices. This aligns with global sustainability goals and reduces the environmental impact of manufacturing processes.
Customizable and Modular
- Modular Design: The machine’s modular design allows for customization and scalability. Manufacturers can add or upgrade components based on specific production needs, ensuring the machine remains versatile and adaptable to changing market demands.
Detailed Equipment Description
- This equipment is used for recyclable pulp molded industrial packaging paper products.
- The product will automatically fall onto the product stacking platform.
- This machine has two workstations and can produce two different types of products simultaneously. By changing molds, machines can manufacture a variety of different types of products.
- The slurry bucket is made of SUS304 stainless steel, which has good corrosion resistance.
- PLC and touch screen control.
- Drive: Pneumatic drives the lower mold and drives the upper mold forward and backward.
- Main pneumatic component brands: SMC/ARK. Main electrical accessory brand: Siemens.