High quality fresh noodles and dry noodles production line adopts advanced technology, high degree of automation, easy maintenance and operation, low energy consumption, small footprint, to ensure that all the processes from powder to fresh noodles and dry noodles finished at one time. The fresh noodle production line is targeted at the market demand of the company. The production equipment adopts vacuum technology, static curing technology and composite calendering technology, automatic roll instead of manual roll molding, which greatly reduces the production cost and increases the production capacity.
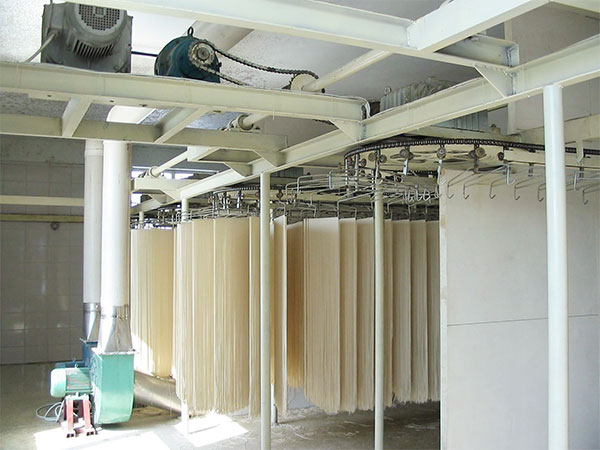
High quality fresh noodles and dry noodles production line Performance characteristics:
1, fresh noodles production line and noodle production line can save labor and production time;
2, the machine material in line with food hygiene standards, all food contact parts are made of 304 stainless steel;
3, with PLC frequency control, the production line data can be transmitted to the computer, easy to control and record;
4, intelligent alarm system, operation and maintenance safety.
Stick Noodle Production Line
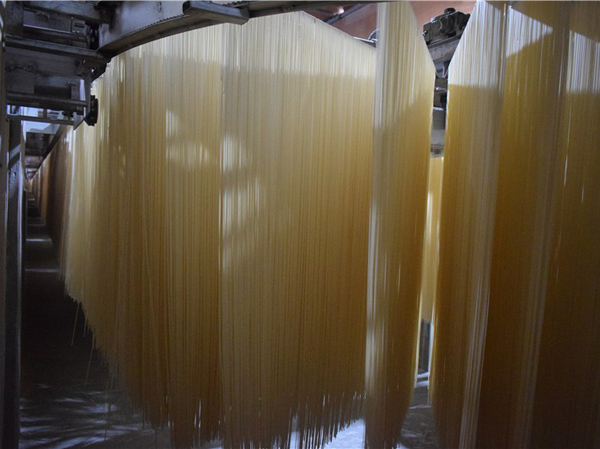
The automated continuous dried stick noodle making machine include alkali water mixer, measuring water supply, flour mixing,aging, compound rolling machine, continuous rolling machine, slitting, shelf transportation, cutting the bottom of noodle neatly, drying and putting- down, cutting and packing.
Dried stick noodle making machine usually cut into 12cm to 30 cm . Drying time is about 4 hours .Material is wheat flour . But we can add little vegetable powder or sauce, egg powder to make change into other color . There are two types drying way, one is several lines go ahead straightly together . The other type is only one line go ahead circularly.
The capacity is from 300kg per hour to 2000kg per hour. Roller width is 300 to 1000 mm. The size can customized by customer.
Production flow of Stick Noodle Production Line
The automated continuous dried stick noodle making machine include alkali water mixer, measuring water supply, flour mixing,aging, compound rolling machine, continuous rolling machine, slitting, shelf transportation, cutting the bottom of noodle neatly, drying and putting- down, cutting and packing.
Chow mein & fresh noodle making machine
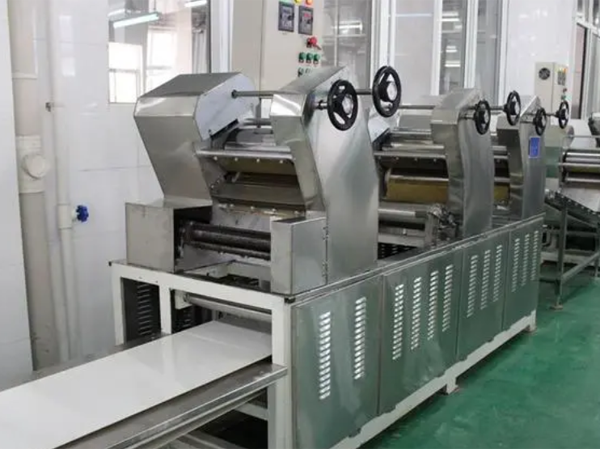
Chow mein & fresh noodle making machine,It is applied to the automatic production of fresh wet surface and semi-dry surface with multiple layers of dough and floss. It realizes the full automatic production process from vacuum dough mixing, dough curing, floss compounding, continuous calendering, roll curing, and cutting molding. It can also be customized according to special requirements.
The process and equipment of fresh noodles seem simple, in fact, the equipment requirements of each link are extremely strict and picky, such as the general use of vacuum flour mixer and noodles; Require multiple sets of multiple curing devices and so on. In addition, it is also necessary to build cold storage, transport with refrigerated trucks and so on.
Semi-dry noodles production line is on the basis of fresh noodles to increase the high temperature drying and softening modeling process, the moisture content of the finished product is generally between (20-25)%, but also must do anti-corrosion treatment.
Production Flow of Fresh Noodle Production Line
Fresh noodles production line process flow is: the water supply for powder — – and – cure – tablet, cutting, cooling, conveying, packing, warehousing, etc.
The main equipment of fresh noodle production line is: water supply system – powder supply system (or artificial pouring powder) – flour mixer – curing machine – flour press machine – cooling conveyor – packaging machine and so on.
Main Equipment Of Noodle Production Line
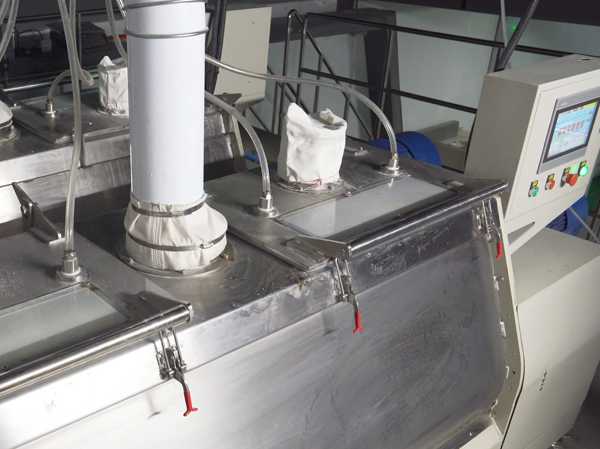
Flour feeding & dough mixing
After feeding the flour by positive pressure air, the water and flour are rapidly and continuously mixed.
Under negative pressure, the flour and water are fully mixed and more uniform, which greatly improves the water content of the dough and makes the gluten network better formed.
Flour ,water combined and mixed full. There are two types, small one match single shaft flour mixer, big model match double shaft flour mixer .Mixing tank ,shaft ,mixing gear made of stainless steel 304 . And door open type include air discharge and manual way.There is also double speed design, match motor and gear box.
50kg to 75kg usually use single shaft type, 100kg,150kg,200kg,250kg,300kg,350kg,400kg use double shaft type.
And we usually put flour mixer on the first floor ,and put other machines(like rolling machine, steamer,fryer) on the ground floor.
Dough Belt Folding & Rolling
Fold the dough belt at 90°, the direction of the gluten network is changed during rolling.
From the single longitudinal rolling to simulates manual horizontal rolling, which makes the dough belt more flexible and improves the quality of the finished product (more chewiness).
Material: feeder, mixing shaft,wave former, made of stainless steel 304.Frame,driving fitting,noodle slitter carbon steel.
scrapper ,noodle combs brass material. noodle press roller use solid alloy steel. guard board for roller is nylon, handwheel with meters. Roller width model is the whole noodle production model. For example if roller width is 300mm, then we will say this noodle production line is model 300 .
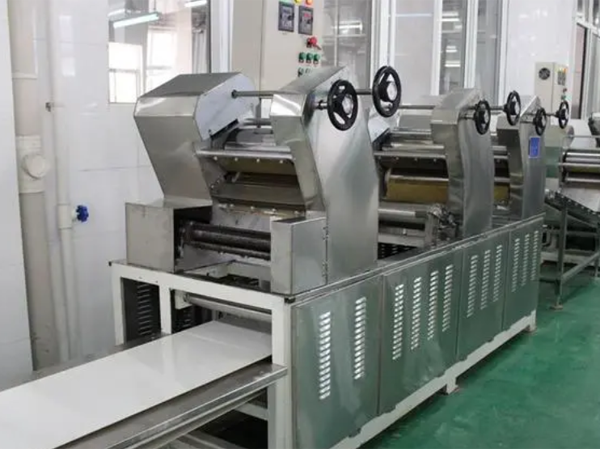
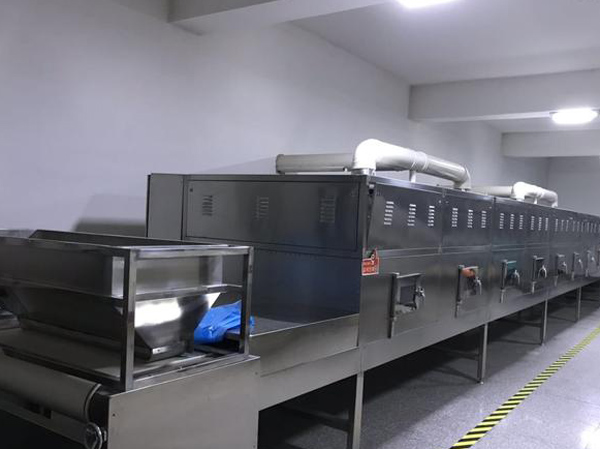
Constant Temperature & Humidity Ripening
Make the thick dough belt which just pressed out from the rolling machine go out in the constant temperature & humidity box.
The gluten network organization inside the dough belt reaches a stable state, which is more ductile, flexible and delicate.
Dried stick noodle cutting machine
There are two forms cutting machines currently, the new straight blade cutting machine and the old rolling blade cutting machine. The cutting length is 150-300mm, and new straight blade cutting machine is equipped with PLC and touch screen control,cut noodles more neat. Old type cuttting machine is more economical.
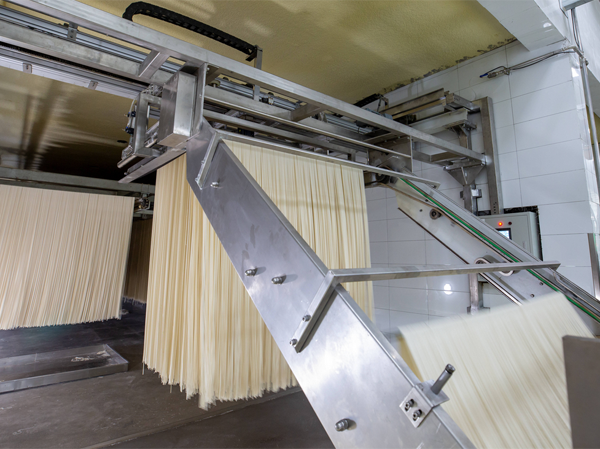
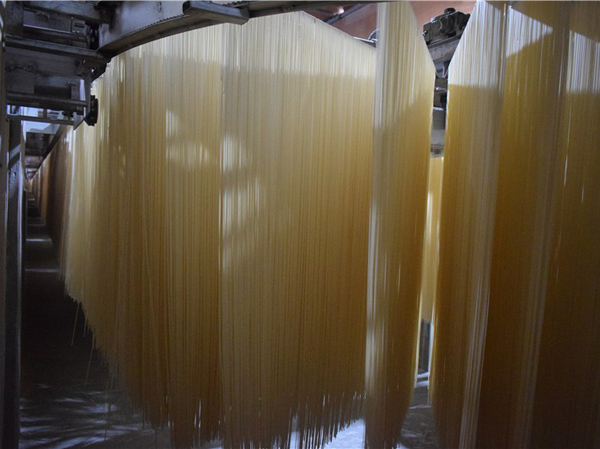
Drying room equipment
Transmission system: total length of drying room designed accord buyer’s workshop. Usually with 4 temperature zones .Drying time: about 4 hours, main conveyor chain is 1 inch large roller carbon steel special chain.Track carbon steel galvanized profile,.carbon steel driven parts.
Heating system: heating medium steam, temperature and humidity automatic electrical control, total 4 groups of inner diameter dn32 finned tubes.temperature and humidity sensors (domestic) 4pcs.
Air circulation system: fan , pressed special fan blades (carbon steel sprayed plastic), carbon steel galvanized fan frame.
Humidity removal system: humidity discharge fan (carbon steel), the ground humidity discharge channel is constructed by the buyer, including 304 stainless steel humidity discharge riser, including humidity discharge pipe after humidity discharge fan.
Stick noodle packing machine
Adopting photoelectric sensing and PLC centralized control technology, the size of the longitudinal sealing film can be adjusted at any time, and the LCD screen displays, which can set and prompt the operating status, parameter adjustment, and fault prompt. The entire packaging process is automated without manual contact with food, ensuring food, health, and hygiene. Easy to operate.
Fully automatic measuring and weighing, automatic lifting, automatic cutting, automatic material handling, and automatic packaging, realizing a fully automated packaging production line, saving labor, easy management, fast speed, exquisite packaging, and no waste or pressure on the surface.
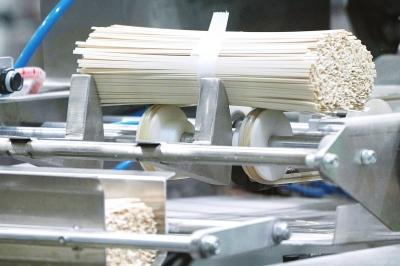
- Provide free plant basic facilities planning and fresh noodles production line planning layout;
- Welcome to visit the factory to inspect the equipment, and put forward your valuable comments on our products;
- Equipped with our professional installation and after-sales service team, our technicians will come to your factory for equipment positioning and installation after the equipment is shipped, and teach related staff daily equipment operation and maintenance during the installation process.
- In the production process, if any parts on the equipment need to be replaced, you can contact us directly, we can arrange it for you immediately, saving you the time to find parts suppliers.