Ruminants are animals that can store food in their stomachs for ruminant digestion, such as cows, sheep, camels, etc. Feed for ruminants needs to meet their special digestive system and nutritional needs, so the ruminant feed production line also needs to be optimized accordingly to improve feed quality and efficiency.
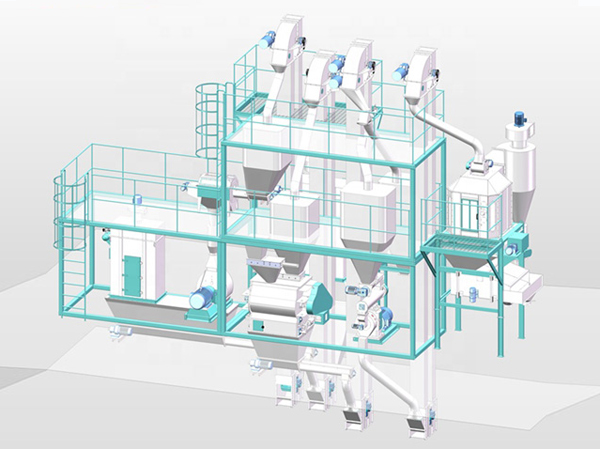
Automatic ruminant feed pellet production line
processing capacity:1-100T/h
Application scope:Ruminant and livestock poultry concentrated feed processing machine
According to the unique digestive physiological characteristics and feed nutrition requirements of ruminants, there are great differences between cattle and sheep feed and pig and poultry feed in feed formula and feed production line preparation process. For example, ruminants can fermented food in the rumen, and more crude fiber has little impact on it, so the production of ruminant feed will add more crude fiber raw materials. If you use a single stomach animal feed line, it is easy to break the machine.
Digestion in ruminants takes place in two stages: first, the raw material is chewed and swallowed into the stomach, and after a period of time, the semi-digested food is chewed again.
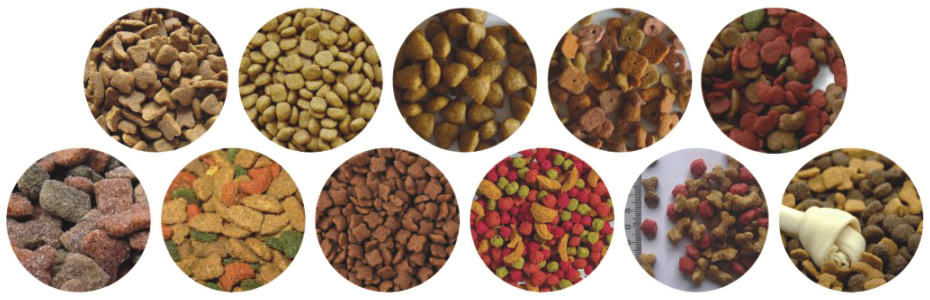
Advantages of ruminant feed production line:
The large feed processing unit designed and produced by us is of great significance for reducing cost, saving resources and improving the efficiency of animal husbandry.
The large feed processing unit is designed with humanization, small footprint, low noise, simple and safer operation, and can be customized according to customer needs.
The ruminant feed production line has high output, good performance and low energy consumption, making it an ideal equipment for ruminant feed.
Types of ruminant feed pellet production lines
Ruminant feed pellet production line is a typical feed pellet processing system, mainly for the processing of animal feed such as cattle, sheep, camels, deer, etc. ZHI Machinery, as a pioneer and leader in ruminant feed equipment and feed mill engineering, is committed to tailoring professional forage processing, ruminant concentrate supplements, total diet processing and other system solutions for the majority of ruminant feed factories, constantly innovating independently, upgrading processes and equipment, and continuously providing new development momentum for the ruminant industry!
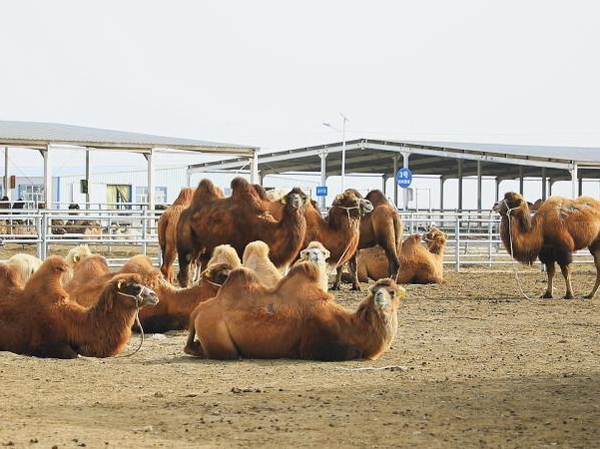
Camels feed production line
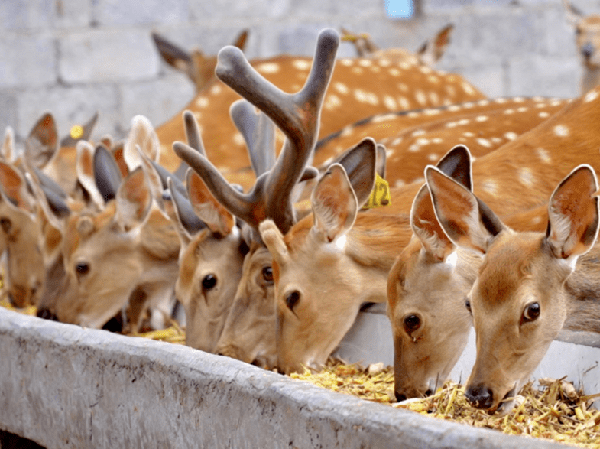
Deer feed pellet production line
Production Process Of Ruminant Feed Pellet Production Line
In modern agricultural production, the production and management of feed play a crucial role in improving breeding efficiency and product quality. Especially in the production process of ruminant animal feed, how to achieve full process control and optimize management is the key to improving production efficiency and ensuring animal health. Realize full process control and optimize management on the ruminant feed production line.
Firstly, from the procurement of raw materials, strict quality control is required. Due to the fact that the main component of ruminant animal feed is silage, its quality directly affects the subsequent production process and the quality of the final product. Therefore, advanced quality inspection equipment is used to conduct detailed testing on each batch of raw materials to ensure that the quality of the raw materials meets the standards. At the same time, establish long-term cooperative relationships with reputable suppliers to ensure stable supply and reliable quality of raw materials.
Secondly, in the production process, automation and information technology are adopted to achieve full process control of the production process. By installing sensors and monitoring equipment throughout the production line, various data during the production process can be monitored in real time, and problems can be discovered and solved in a timely manner. In addition, by using an intelligent production management system, production parameters can be automatically adjusted, production processes can be optimized, and production efficiency can be improved based on factors such as the characteristics of raw materials, market supply and demand, and production plans.
Then, in order to ensure the safety and stability of the product, strict quality inspection was conducted before the product left the factory. We use modern quality inspection equipment and technology to conduct comprehensive testing on each batch of products, including testing for nutritional content, microbial indicators, heavy metals, and other items. Only products that have passed inspection can enter the market.
Production Process Of Ruminant Feed Pellet Production Line
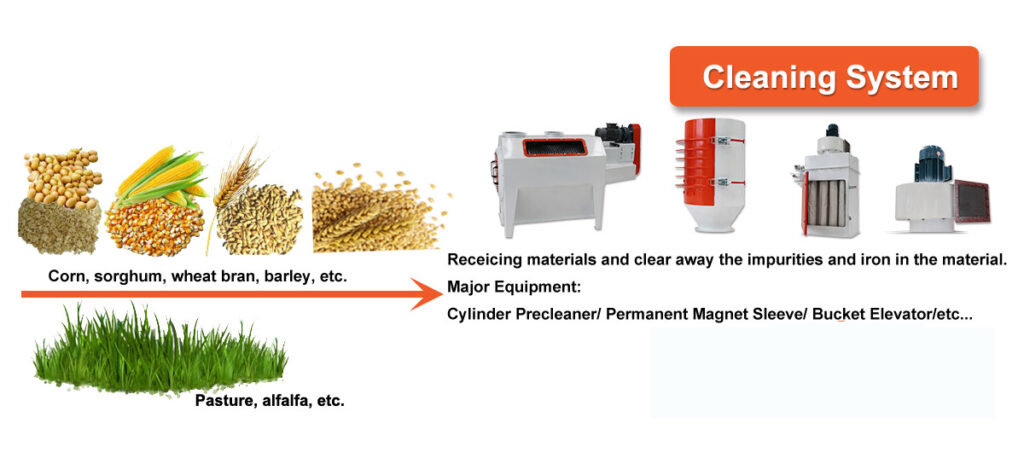
Raw material cleaning
Raw material cleaning is the first process in feed production, aimed at removing impurities such as stones, metals, plastics, etc. from the raw materials to ensure the safety and quality of the feed. Raw material cleaning can be carried out using methods such as screening, magnetic separation, and air selection, and appropriate equipment and parameters can be selected based on the different characteristics of the raw materials. After cleaning the raw materials, they should be transported to the storage warehouse according to the plan to avoid cross contamination.
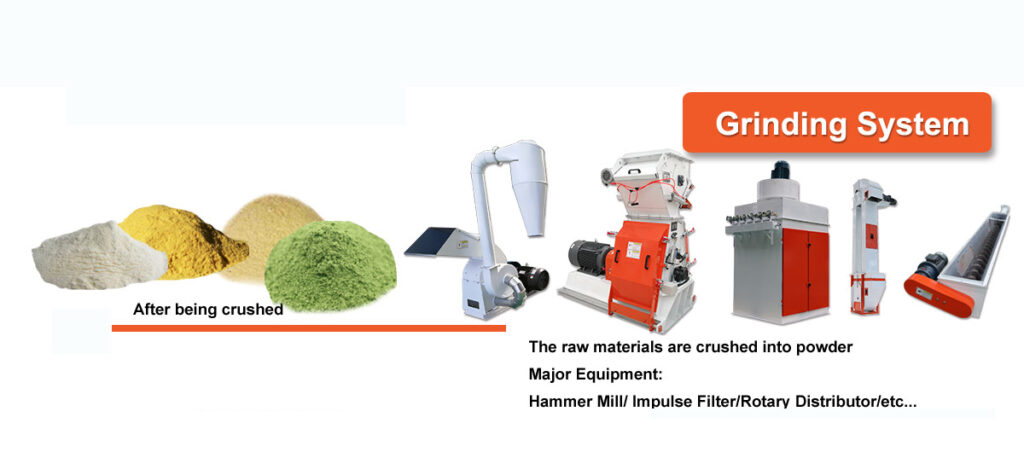
crushing system
The crushing system is the starting point of the ruminant feed production line. It crushes raw materials such as grains, beans, cellulose, etc. to a degree suitable for subsequent processing. This process usually requires the use of high-speed rotating grinders or hammer mills to ensure that the raw materials can be uniformly crushed.
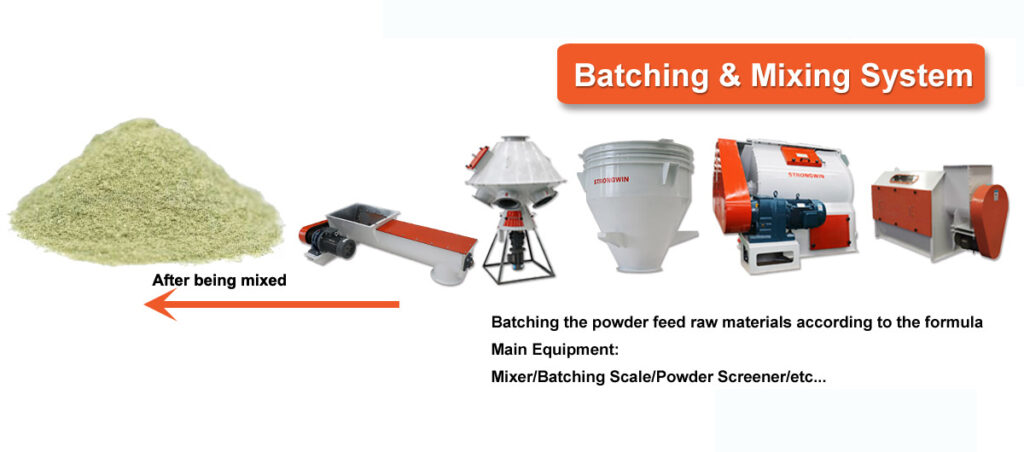
Mixing system
The mixing system mixes the crushed raw materials. This process usually requires the use of a vertical or horizontal mixer to ensure that the raw materials can be evenly distributed during the mixing process. At the same time, the hybrid system can also add appropriate amounts of other additives such as minerals, vitamins, etc. as needed to meet the nutritional needs of ruminants.
Formula mixing is the process of mixing various raw materials together in a certain proportion according to the different growth stages and nutritional needs of ruminants. Formula mixing requires consideration of factors such as the nutritional composition, physical properties, and cost of raw materials to achieve the best formula effect. Formula mixing can use different forms of mixers such as horizontal, vertical, conical, etc., and the mixing uniformity can be controlled according to parameters such as mixing time, speed, and sequence.
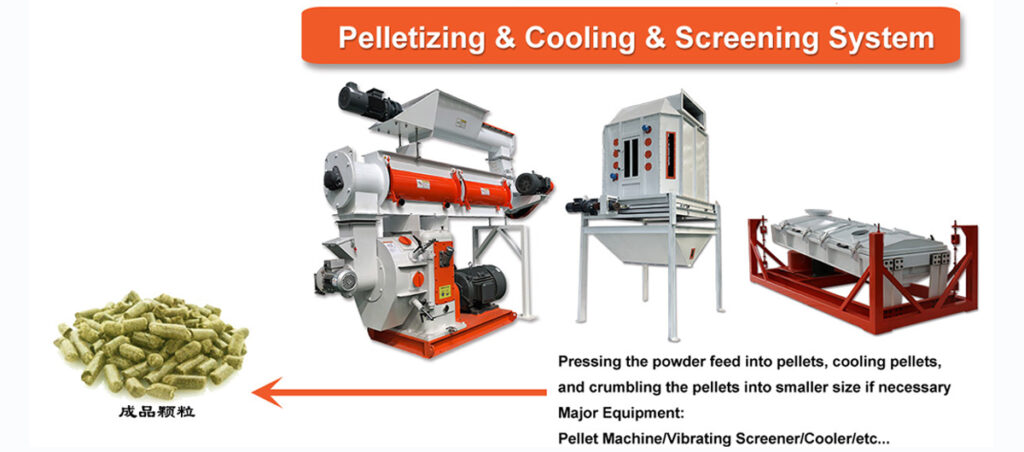
Pelletizing & Cooling & screening & dust recovery system
The material is entering in the ruminant feed pellet mill passing through the pellet making machine conditioner. Here other ingredients like steam, molasses and grease could be added, before the material goes into the pellet pressure chamber to be transformed into pellets by the ring die. On the outside of the holes some knives cut the ruminant feed pellets at the desired length.
After pelleting, the product is very hot, therefore it’s necessary to cool the product at approximately +5°C in respect to the room temperature, in order to give it the right hardness and the best consistence to store and handle it.
In the screening section the product is cleaned from the dust, which is brought back into the production cycle.
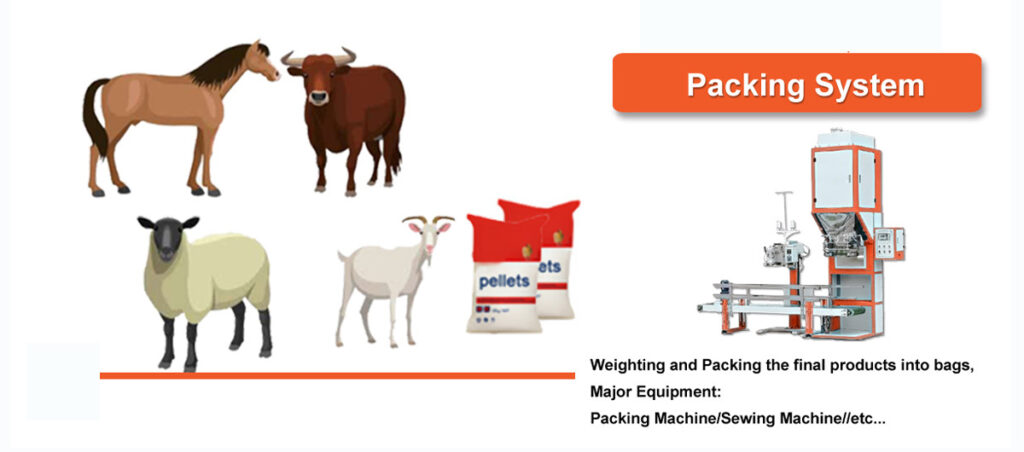
Packing system
Finally, the packaging system packages the dried feed. This process usually requires the use of automatic or semi-automatic packaging machines to ensure that the weight and particle size of each bag of feed meet the standards. At the same time, the packaging system can also add necessary labels and instructions as needed to help consumers understand the information about the feed.
How to build a new ruminant feed pellet production line?
If you want to start a new ruminant feed pellet line for your ruminant feed mill or ruminant farm, you should pay attention to the following main processes:
Determine the scale of ruminant feed mill.
Determine the ruminant feed manufacturing process and recommend ruminant feed machine.
Control mode selection (the degree of automation of the ruminant food processing plant).
Complete feed mill plant structure selection.
Planning the general drawing of ruminant feed mill plant site.
Due to the influence of various objective factors such as ruminant feed raw materials, processes, formulas, project area, local regulations, etc., various technological ruminant feed production process and ruminant feed equipment configurations have appeared in the actual ruminant feed plant design.
Therefore, if you want to build a high-efficiency, high-quality, high-return ruminant animal feed pellet production line, please do not hesitate to contact Richi Machinery and communicate directly with our engineer team, you will definitely get a satisfactory answer. The following is the ruminant feed mill machine configuration display of ruminant feed production business plan we have done in several customer project :
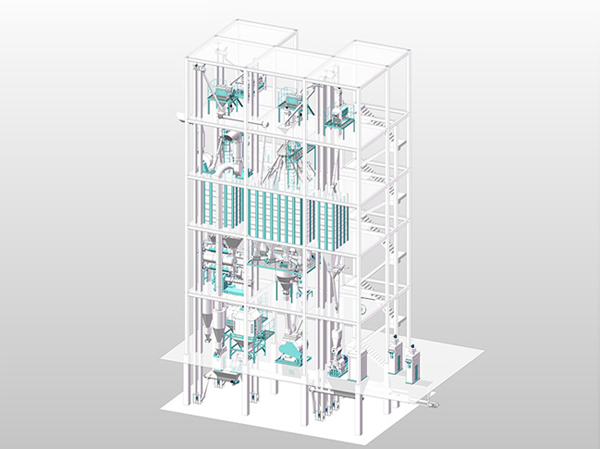
Production line of 20 tons of ruminant feed
Grass receiving and crushing section | Coarse rabbit feed often requires the addition of coarse fiber materials such as alfalfa and straw,. |
Grass coarse crusher | MFSP68 × 108, 55kw, side feeding, yield 3-5 T/H; Secondary crusher: MFSP568-II, 37kw, output 4-6T/H |
Raw material receiving and cleaning section | In this section, the cleaning of granular material feeding and powder material feeding are separated independently, with separate dust removal and good dust removal effect. |
Cleaning equipment | Particle sieve SCY80, designed to produce 20-30T/H; The powder sieve SQLZ60 × 50 × 100 is designed to produce 10-15 T/H. |
Crushing section | Due to the requirement of coarse crushing fineness for ruminant feed, this section uses two low-power crushers, each equipped with two crushing bins, which can simultaneously crush different raw materials and improve production efficiency. Before entering the warehouse, impurities are removed by a magnetic separation device to ensure the safe operation of the crusher. |
Crushing equipment (2 sets) | Crushing equipment (2 sets) |
Mixing section of ingredients | This section adopts 16 ingredient warehouses (including 2 circular warehouses for grass powder), with two ingredient scales for simultaneous ingredient mixing. The batching is controlled by our company’s independently developed batching program, achieving precise fast and slow feeding, fast batching speed, and high accuracy. Due to the presence of a certain amount of grass powder raw materials in the formula, grass powder has a small specific gravity, a large volume, and is prone to arching. Therefore, disc feeders are used for the discharge of the two grass powder silos, and large-sized equipment is also used for the discharge machine. The batching scale hopper is enlarged, and the feeding sequence controlled by the batching program is optimized. |
The weighing equipment selected for this section | ingredient scale PCS20 (customized enlarged)/PCS05, ingredient accuracy: dynamic ≤ 3 ‰, static ≤ 1 ‰. Mixing equipment: SHSJ4 mixer (30KW, 2000kg/batch), designed to produce 24-30T/H. Mixing uniformity CV ≤ 5%. |
Granulation section | This section uses two single-layer tempering granulators, each equipped with two granulation bins for easy switching of varieties. After granulation, they enter the cooler and elevator in order, and then enter the rotary classification screen for screening. The finished products enter the packaging warehouse, while the rest return to granulation or bagging; Simultaneously design bulk truck packaging and transportation. |
Granulation equipment (2 units) | SZLH508160KW, designed to produce 8-12 T/H per unit. Cooling equipment (2 units): SKLN6, designed to produce 10-15 T/H per unit. |
Packing equipment | Belt scale (can handle both powder and granular materials), packing range 20-50kg/bag, 6-8 bags/minute. |
Auxiliary section | dust removal system to improve the working environment for workers; Oil and fat addition system, commonly added at the mixer to improve feed palatability. |
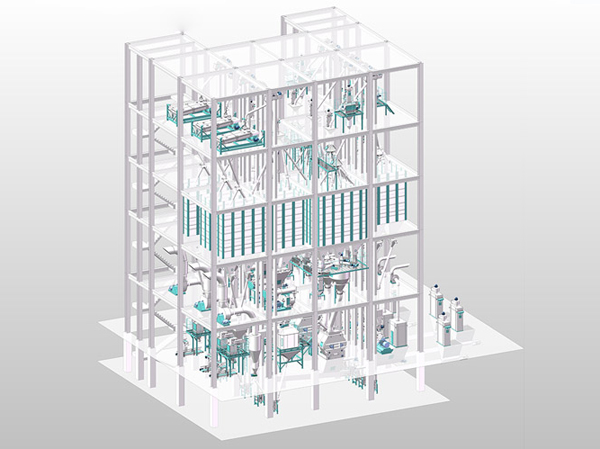
Production line of 60 tons of cattle and sheep feed
Raw material receiving and cleaning section | In this section, the cleaning of granular material feeding and powder material feeding are separated independently, with separate dust removal and good dust removal effect. |
Cleaning equipment | Particle sieve SCY100, designed to produce 30-50T/H; The powder sieve SQLZ90 × 80 × 110 is designed to produce 30-50T/H. |
Crushing section | Due to the requirement of coarse crushing fineness for ruminant feed, this section uses three low-power crushers, each equipped with two crushing bins, which can simultaneously crush different raw materials and improve production efficiency. Before entering the warehouse, impurities are removed by a magnetic separation device to ensure the safe operation of the crusher. |
Crushing equipment (3 units) | Crushing machine SFSP668 × 1000160KW, designed to produce 18-20T/H per unit. |
Ingredient mixing section | This section adopts 21 ingredient warehouses and two sets of ingredient systems for simultaneous ingredient mixing. Each ingredient system is equipped with two ingredient scales for simultaneous ingredient mixing, which is controlled by our company’s independently developed ingredient program to achieve precise fast and slow feeding, fast ingredient speed, and high accuracy. |
Weighing equipment | ingredient scale PCS20/PCS10, ingredient accuracy: dynamic ≤ 3 ‰, static ≤ 1 ‰. |
Mixing equipment (2 units) | SHSJ4 mixer (30KW, 2000kg/batch), designed to produce 25-30T/H per unit. Mixing uniformity CV ≤ 5%. |
Granulation section | This section uses three single-layer tempering granulators, each equipped with two granulation bins for easy switching of varieties. After granulation, they enter the cooler and elevator in order, and then enter the rotary classification screen for screening. The finished products enter the packaging warehouse, while the rest return to granulation or bagging. |
Granulation equipment (3 units) | SZLH678220KW, designed to produce 20-22T/H per unit. |
Cooling equipment (3 units) | SKLN10, 1.5+1.5+2.2KW, 10m ³ capacity, designed to produce 20-25T/H per unit. |
Packaging section | There are a total of 6 finished product warehouses in this section, of which 4 warehouses are dedicated to storing finished granular materials, and 2 warehouses can store both powder and granular materials. The powder finished product warehouse is designed with a unique anti grading device. The granular or powder materials are ultimately automatically weighed and packaged by a packaging scale. |
Packing equipment | Double bucket belt scale (can handle both powder and granular materials), with a packing range of 20-50kg/bag and 10-12 bags/minute. |
Auxiliary section | dust removal system to improve the working environment for workers; Oil and fat addition system, commonly added at the mixer to improve feed palatability. |
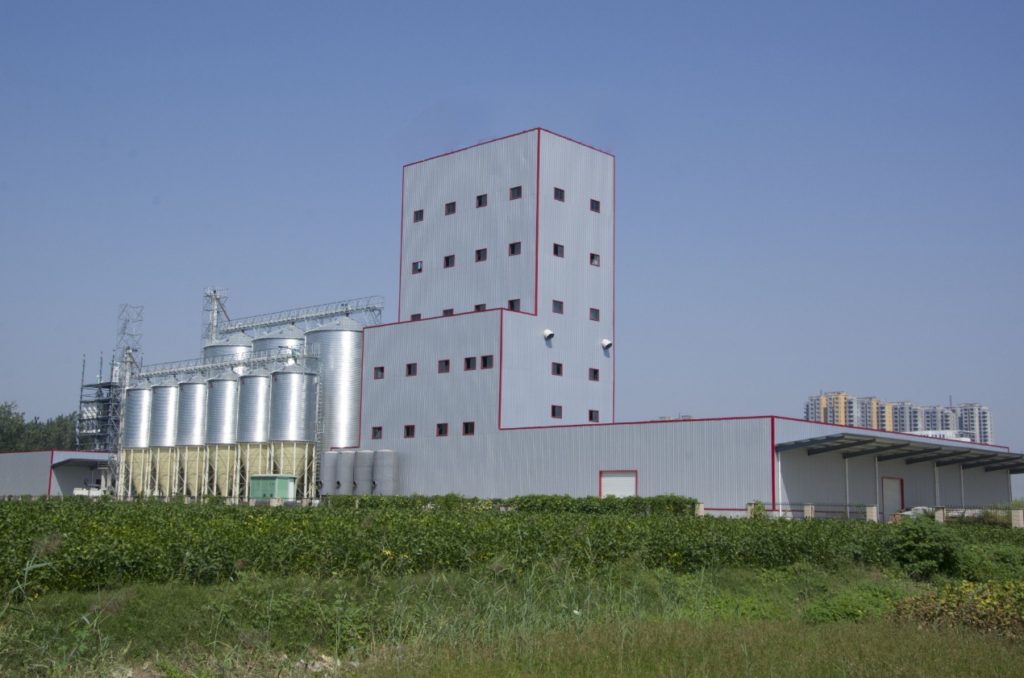
According to the needs of different customers, this solution can optimize the configuration:
1.This scheme adopts a single point dust removal mode, which means that each rotary distributor (powder) and granular cleaning screen is equipped with a pulse dust collector, which has good dust removal effect. Single point dust removal is a humanized design for our company, providing a better working environment, but the cost increases. Customers can consider whether to adopt this configuration according to their actual needs;
2.The configuration of grass crushing depends on whether there is grass added according to the actual situation of the customer, so as to choose whether to configure it.
3.The number of silos can also be adjusted based on factors such as customer formula and raw material characteristics to achieve the highest utilization rate and effectively control production costs;
4.The packaging dust removal design can improve the working environment for workers, and customers can configure it according to their needs.