Automatic egg tray machine is an excellent project for the investors. Because of high automation, great working efficiency and easy operation, high yield of the equipment, it is popular among customers all over the world. With the full-automatic egg tray machine, there isn’t more labor force, the machine can process waste paper into pulp molding products directly. We have different kinds of models on automatic egg tray machine, the output ranges from 1000pcs/h to 7000ocs/h, we can design the most suitable egg tray line according to customers’ real situation, welcome to contact us about the details information.
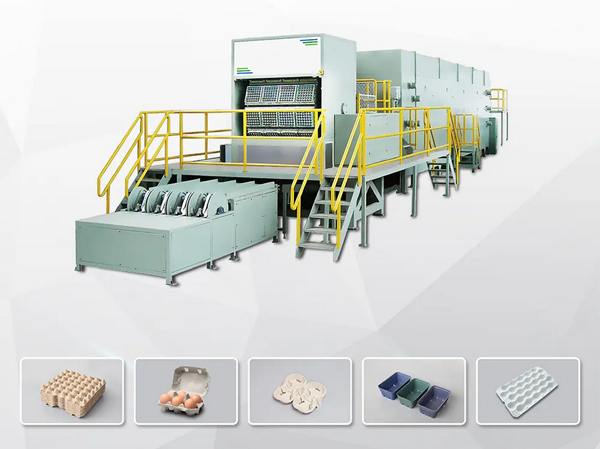
Automatic pulp egg tray production line
Rotary Egg Tray Making Machine is an efficient and scalable solution for manufacturing egg trays. It offers high production capacity, consistent quality, and automation, making it suitable for medium to large-scale production facilities. By converting waste paper into useful products, it also supports environmental sustainability. Rotary Egg Tray Pulp Molding Machine is ideal for manufacturing a range of standard products, including egg trays, fruit trays, drinking cup trays, bottle trays, and more, with exceptional precision and efficiency.
Egg tray raw materials: Waste paper boxes, waste books, waste newspapers, book scraps, recycled egg trays, and other waste paper materials.
Final products: 20 egg tray, 30 egg trays (including chicken egg, duck egg, goose egg, quail egg, etc.), 6 egg box, 10 egg boxes, 12 egg carton, 15 egg cartons, 18 egg box carton, fruit tray (apple tray, avocado tray, melon tray, mushroom tray), berry trays, coffee cup carriers, coffee cup holders, seeding tray, etc.


Specification of Full Automatic Egg Tray Production Line
Production line models | Output (p/h) | Pulping machine | Egg tray machine | Drying type | |||
---|---|---|---|---|---|---|---|
Natural drying | Civil engineering | Single layer metal | Multilayer metal | ||||
ZMDT3×1-1000 | 1000 | ZDS1(1m³) | DTF3×1(3 moulds) | √ | √ | √ | √ |
ZMDT4×1-1500 | 1500 | ZDS1(1m³) | DTF4×1(4 moulds) | √ | √ | √ | √ |
ZMDT3×4-2000 | 2000 | ZDS1(1m³) | DT3×4(12 moulds) | √ | √ | √ | √ |
ZMDT4×4-2500 | 2500 | ZDS2(2m³) | DT4×4(16 moulds) | √ | √ | √ | √ |
ZMDT3×8-3000 | 3000 | ZDS2(2m³) | DT3×8(24 moulds) | √ | √ | √ | |
ZMDT4×8-4000 | 4000 | ZDS4(4m³) | DT4×8(32 moulds) | √ | √ | √ | |
ZMDT5×8-5000 | 5000 | ZDS4(4m³) | DT5×8(40 moulds) | √ | √ | √ | |
ZMDT5×12-6000 | 6000 | ZDS8(8m³) | DT5×12(60 moulds) | √ | √ | √ | |
ZMDT8×8-10000 | 10000 | ZDS8(8m³) | DT8×8(64 moulds) | √ | √ | √ |
Consumption table of egg tray production line
Models | Drying type | Material(kg/h) | Power(kw/h) | Fuel(kg/h) | ||||
---|---|---|---|---|---|---|---|---|
Paper | Water | Coal | Gas(m³/h) | Diesel | LPG | |||
ZMDT3×1-1000 | Natural drying | 85 | 255 | 23.1 | ||||
ZMDT3×1-1000T | Civil engineering | 36.1 | 50 | 22-32 | 18-28 | 18-28 | ||
ZMDT3×1-1000J1 | Single layer metal | 36.1 | 22-32 | 18-28 | 18-28 | |||
ZMDT3×1-1000J6 | Multilayer metal | 36.1 | 22-32 | 18-28 | 18-28 | |||
ZMDT4×1-1500 | Natural drying | 102 | 306 | 24.5 | ||||
ZMDT4×1-1500T | Civil engineering | 42.7 | 60 | 26-36 | 22-32 | 22-32 | ||
ZMDT4×1-1500J1 | Single layer metal | 42.7 | 26-36 | 22-32 | 22-32 | |||
ZMDT4×1-1500J6 | Multilayer metal | 42.7 | 26-36 | 22-32 | 22-32 | |||
ZMDT3×4-2000 | Natural drying | 170 | 510 | 36.8 | ||||
ZMDT3×4-2000T | Civil engineering | 52.1 | 83 | 37-47 | 30-40 | 30-40 | ||
ZMDT3×4-2000J1 | Single layer metal | 52.1 | 37-47 | 30-40 | 30-40 | |||
ZMDT3×4-2000J6 | Multilayer metal | 52.1 | 37-47 | 30-40 | 30-40 | |||
ZMDT4×4-2500 | Natural drying | 212 | 636 | 34.1 | ||||
ZMDT4×4-2500T | Civil engineering | 57.4 | 104 | 46-56 | 38-48 | 38-48 | ||
ZMDT4×4-2500J1 | Single layer metal | 57.4 | 46-56 | 38-48 | 38-48 | |||
ZMDT4×4-2500J6 | Multilayer metal | 57.4 | 46-56 | 38-48 | 38-48 | |||
ZMDT3×8-3000T | Civil engineering | 255 | 765 | 88.9 | 125 | 56-66 | 46-56 | 46-56 |
ZMDT3×8-3000J1 | Single layer metal | 88.9 | 56-66 | 46-56 | 46-56 | |||
ZMDT3×8-3000J6 | Multilayer metal | 88.9 | 56-66 | 46-56 | 46-56 | |||
ZMDT4×8-4000T | Civil engineering | 340 | 1020 | 88.9 | 160 | 67-77 | 55-65 | 55-65 |
ZMDT4×8-4000J1 | Single layer metal | 100.8 | 67-77 | 55-65 | 55-65 | |||
ZMDT4×8-4000J6 | Multilayer metal | 100.8 | 67-77 | 55-65 | 55-65 | |||
ZMDT5×8-5000T | Civil engineering | 424 | 1272 | 112.7 | 185 | 82-92 | 67-77 | 67-77 |
ZMDT5×8-5000J1 | Single layer metal | 123.9 | 82-92 | 67-77 | 67-77 | |||
ZMDT5×8-5000J6 | Multilayer metal | 123.9 | 82-92 | 67-77 | 67-77 | |||
ZMDT5×12-6000T | Civil engineering | 510 | 1530 | 123.9 | 208 | 92-103 | 77-87 | 77-87 |
ZMDT5×12-6000J1 | Single layer metal | 123.9 | 92-103 | 77-87 | 77-87 | |||
ZMDT5×12-6000J6 | Multilayer metal | 123.9 | 92-103 | 77-87 | 77-87 |
Working Process of Rotary Egg Tray Machine

Introduction to the production line of egg tray machine
(1) Process overview
- After the raw material — waste paper (or raw pulp cardboard) is broken into pulp fibers by hydraulic pulper, in order to have special functions (such as waterproof, moisture-proof, antistatic, etc.), a small amount of functional additives is added to the pulp storage tank, and water is added to the pulp storage tank, the slurry is adjusted to the required concentration, and the slurry is formed into wet billet on a special mold through vacuum adsorption. The formed wet blank is finished after drying and hot pressing.
2, production process: raw materials (waste paper) → hydraulic pulp crushing → pulp water storage pool → pulp mixing system → pulp suction molding → dehydration and drying → hot press molding → packaging → finished products.
3, raw materials: The raw materials for the production of pulp molding products are mainly waste newspapers, carton paper and paper mills, carton factories, printing plants corner waste paper. The raw materials used are abundant in resources, low in price, and the waste is recycled.
There is no waste water and exhaust gas discharge in the production process, and the water used in the production process is recycled, which will not cause pollution to the environment and can save water costs.
4, the same equipment, by replacing the mold, you can use a variety of waste paper to produce a variety of paper tray products, such as egg trays, egg boxes, mobile phone trays, bottle trays, fruit trays, nursery trays, shoe braces, electronic products, and so on. One machine multi-purpose, can meet different market needs.
(2) Pulping process
The raw material (waste paper or pulp) is broken into fibers by hydraulic action and suspended in water, and then the necessary additives and water are added according to the process requirements to form a slurry that meets the molding requirements.
(3) Molding process
The upper and lower die of the reciprocating molding machine do vertical reciprocating movement, the lower die suctions form wet egg supporting products and then move up, and merge with the upper die. In the merging process, the wet egg supporting products are transferred to the upper die, and the upper die sends out the wet egg supporting products and puts them on the drying line. The depth of products produced with this device can exceed 5cm.
(4) Drying process
Pulp products after crushing, molding, generally contain high water, need to be dried to remove the water in the product.
The drying production line uses fuel (gas), electricity or steam (thermal oil) as the heat source, heating the air, drying the molded pulp products in the hot air (180~220 ° C), using the fan to extract the water evaporated from the products to achieve rapid drying effect.
The direct-fired fuel (gas) drying production line designed and manufactured by the company breaks the design habit of foreign zone combustion for the first time, adopts the central heating mode, and its drying temperature is stable, reasonable, high thermal efficiency, and high degree of integration automation; It is superior to other similar equipment in terms of energy consumption and output, and has obtained national zhuanli technology. The electric control system of drying line adopts centralized control mode, and the start, stop, speed regulation and inspection of the production line can be realized in front of the cabinet. At the same time, real-time voltage and current are displayed on the instrument panel of the electric control cabinet, and the temperature of each working area can be displayed in a rolling cycle
Drying line, single-layer drying line and multi-layer drying line; If single-layer drying line is used, the length of the workshop should not be less than 30 meters; If the multi-layer drying line is used, the floor area is small, the length of the workshop can be less than 20 meters, the height of the workshop is ≥4.5 meters, and the volume is small, which can effectively save the energy inside the drying line.
Customers can choose according to their own plant size and energy situation.
(5) Shaping technology
After forming, drying, and basically shaping, the finished product can be directly stored in the warehouse after manual finishing or packaging;
The production process of egg cartons and industrial packaging products needs more than one shaping process after drying, and the product is reshaped with a hot press shaping machine, so that the appearance of the product is neat and beautiful, to achieve better toughness and better shock-proof performance.
The shaping process generally uses electricity (or thermal oil) to heat the heating plate, so that the metal mold has a higher temperature (180~250 ° C), and the use of pneumatic or hydraulic pressure to press pulp products to achieve the shaping effect.
After shaping, some products also need to be labeled on the surface or printed patterns, text, etc.
Customers can choose according to their specific circumstances.