The design scale of this project for the fully automatic pre mixed powder production line is to produce 300000 tons of pre mixed sugar annually. It is mainly a finished powder made by mixing 90% sugar, starch, and other additives through the ingredient system. Its main properties are auxiliary food additives, food/baking/cake/solid beverage/coffee/milk tea/bread/dessert/pastry pre mixed powder.
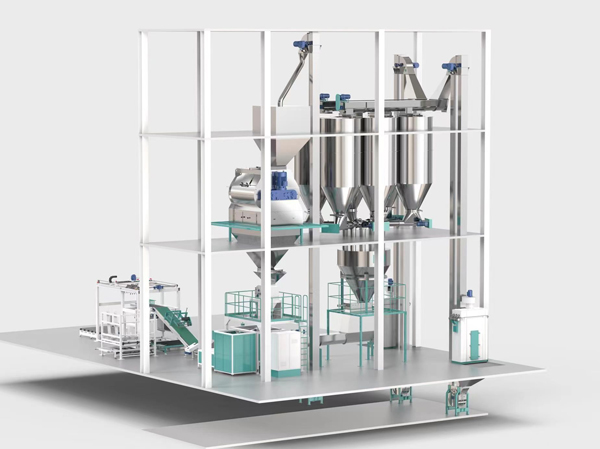
Automatic pre mixed powder production line
Processing capacity: 50-2000 tons/d
Application scope: Particle and powder materials
Product Introduction: grain, flour, starch,Sugar cane, white sugar, glucose powder mixed in proportion
According to the requirements, two or more materials are mixed with other additives in a certain proportion through the ingredient system to form a finished powder. Its main properties are auxiliary food additives, pre mixed powders for food/baking/cake/solid beverages/coffee/milk tea/bread/desserts/pastries.
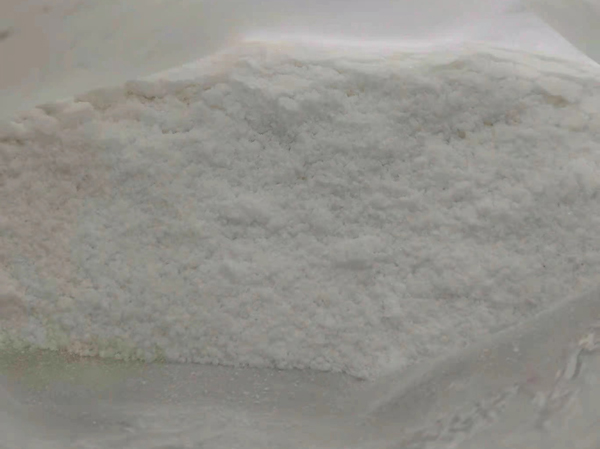
The pre mixed powder production line in the bonded zone, designed, manufactured, and constructed by the company, mainly uses a computer batching system to accurately mix the main raw materials and auxiliary materials, evenly mix them to make finished pre mixed powder, and use it as a food auxiliary material additive.
The entire production line is built inside the existing standard factory building, divided into a raw material feeding purification workshop, a pre mixed powder mixing and processing workshop, and a finished product packaging and storage workshop. The main processing equipment is installed in the form of a steel frame platform. The batching and mixing processing workshop covers an area of 11x7m, with a height of about 14m. The raw material feeding and purification workshop covers an area of 100 square meters, and the fully automatic packaging and palletizing line covers an area of 12x5m.
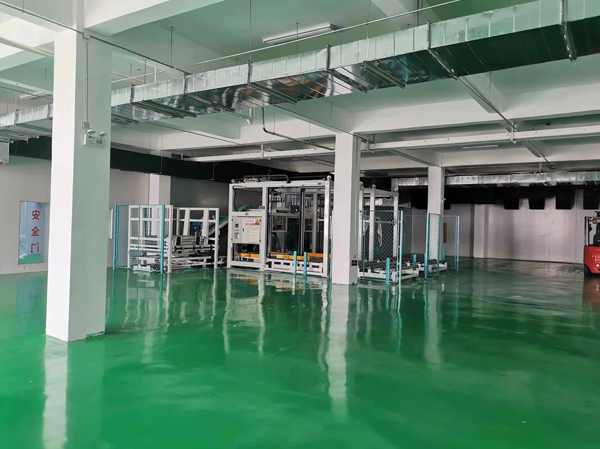
The main raw materials, such as white sugar and auxiliary materials, are fed into the stainless steel seamless tube through a closed air feeding valve after being fed into the purification workshop feeding platform. They are then transported into the batching bin through negative pressure dilute pneumatic conveying. The automatic weighing and batching process is used, controlled by a computer, with precise batching and high degree of automation, saving labor; After the ingredients are completed, in order to reduce the height of the rack, negative pressure dilute pneumatic conveying is used again to temporarily store in the mixing bin, and then mixed in the mixer. The evenly mixed finished products are directly dropped and enter the packaging process. The fully automatic packaging line is used to automatically bag, weigh, sew and seal the mouth. Finally, the high-level palletizer automatically stacks the products, and the forklift sends them to the finished product stacking area.
The entire production process is concise and clear, with a high degree of automation, which reduces the labor cost of the enterprise and improves economic efficiency; The material is conveyed using negative pressure pneumatic conveying, which has no residue or cross contamination, and is convenient for pipeline cleaning, improving the hygiene and safety of production.
1、 Raw material receiving section
Store the required raw materials for production in the purification feeding workshop in advance. During production, each raw material is fed into the feeding hopper according to the formula requirements and sent into the stainless steel seamless pipeline through a closed air feeder. The material is then pumped to the designated batching bin by a Roots blower.
2、 Ingredient section
After the materials enter the batching bin, the batching system automatically discharges them in sequence according to the formula, controlled by the batching program, and enters the batching scale for measurement. The entire process is controlled by a computer. The dynamic batching accuracy error of the batching system is ≤ 3 ‰, and the static accuracy error is ≤ 1 ‰, with high precision and efficiency.
3、 Mixing section
In order to reduce the height of the entire production line, materials are conveyed to the mixing bin through negative pressure pneumatic conveying after batching is completed, and then enter the stainless steel single axis blade mixer for mixing. The mixing time of the mixer is about 120-300 seconds (the specific time is adjusted according to different formulas), and the mixing uniformity is ≥ 95%.
4、 Finished product packaging section
The mixed materials enter the packaging system, which is a fully automatic packaging line with automatic bagging, weighing, sewing, and sealing. Finally, an automatic high-level palletizing system is used, and the products are transported to the finished product stacking area by forklift.
5、 Auxiliary section
Workshop dust removal: After raw material feeding and batching are completed, they enter the mixer and are all transported by negative pressure pneumatic conveying system, without dust overflow; The packaging area is also equipped with a suction hood for dust removal.
The equipment area is fully enclosed and separated, and personnel must undergo air shower and purification before entering the equipment processing area; After feeding, the raw materials should be cleaned up in a timely manner, and the conveying system should be kept idle for more than 2 minutes to ensure that various raw materials do not cross contaminate during the conveying process.