Pig manure organic fertilizer production line is a series of production equipment for making organic fertilizer through fermentation and processing of high-tech equipment. Pig manure organic fertilizer production line adopts advanced production technology, providing 1-100 tons/hour of organic fertilizer production line, pig manure organic fertilizer production line covers a small area, saves money, saves manpower, the effect is very good, is the wise choice of organic fertilizer processing project investment, small organic fertilizer equipment price of about 100,000 yuan, according to the degree of automation of equipment selection price is not the same.
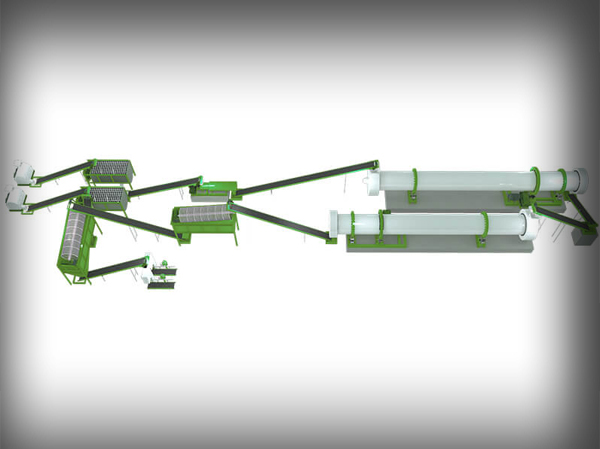
Automatic pig manure fertilizer production line
processing capacity:1-100T/h
Application scope:poultry animal excrement processing into fertilizer
Pig manure bio-organic fertilizer is a kind of biological organic manure that is mixed with pig manure.after fermentation, compost, pre-treatment, and finally make into biomass fertilizer. Pig manure is an excellent fertilizer for crops. Pig manure is fine in texture and contains more organic matter and nitrogen, phosphorus and potassium nutrients.Through the scientific treatment of the granulation after the fermenting and tossing of fertilizer, the pig manure can be made into high quality organic fertilizer, which can achieve zero pollution, zero emission and no smell, and turn the dung into wealth.

Working principle of pig manure organic feed production line
① Raw material fermentation – ② Raw material computer belt scale automatic batching – ③ Crushing and mixing – ④ Disc granulation, drum granulation – ⑤ Drying machine drying organic fertilizer particles – ⑥ Cooling machine cooling organic fertilizer particles – ⑦ Screening machine screening qualified organic fertilizer particles – ⑧ Coating machine coating particles, smoother – ⑨ Packaging scale automatic filling of organic fertilizer particles – ⑩ Sealing
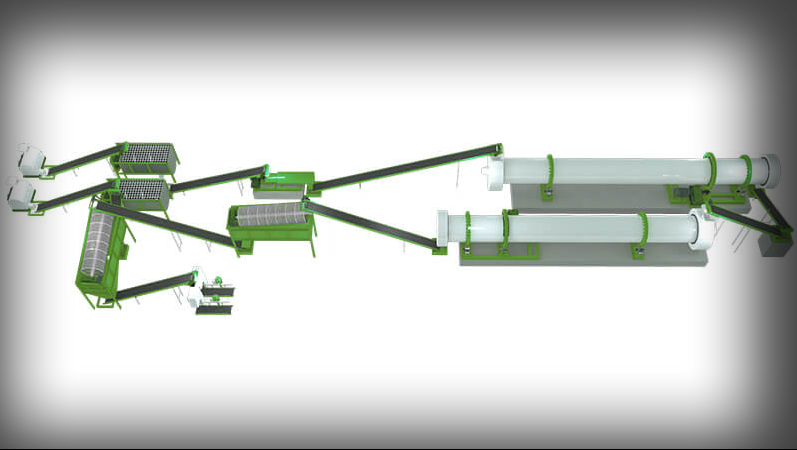
Processing flow of pig manure organic feed production line
- Raw material fermentation: Various animal manure such as chicken manure, pig manure, cow manure, biogas residue, or raw materials that can be fermented or have fertilizer effects after treatment are prepared in a certain proportion (based on market demand and soil testing results in different regions).
- Raw material mixing: Mix the prepared raw materials evenly to increase the overall uniform fertilizer content of the fertilizer particles.
- Raw material granulation: Send the mixed raw materials into a granulator for granulation (a rotary drum granulator or an extrusion granulator can be used).
- Particle drying: Send the granules made by the granulator into the dryer to dry the moisture contained in the granules, increase their strength, and facilitate storage.
- Particle cooling: The temperature of the dried fertilizer particles is too high, making them prone to clumping. After cooling, they are easy to store in bags and transport.
- Particle grading: Classify the cooled particles, grind and re pelletize the unqualified particles, and sieve out the qualified products.
- Finished product coating: Coat qualified products with coating to increase the brightness and roundness of particles.
- Finished product packaging: Pack the particles that have been coated with film, that is, the finished product, into bags and store them in a well ventilated area.
Supporting equipment of pig manure fertilizer production line
Organic fertilizer conversion granulator
Drum granulator is a molding machine that can produce materials into specific shapes. The rotary drum granulator is one of the key equipment in the compound fertilizer industry, suitable for large-scale production of cold and hot granulation as well as high, medium, and low concentration compound fertilizers. The main working method is wet granulation of granules, which uses a certain amount of water or steam to fully react the basic fertilizer after being humidified in the cylinder. Under certain liquid phase conditions, the rotating motion of the cylinder generates squeezing force between the material particles to aggregate into balls.
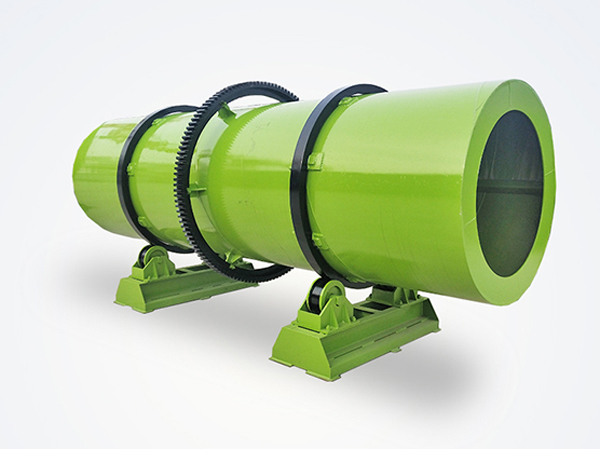
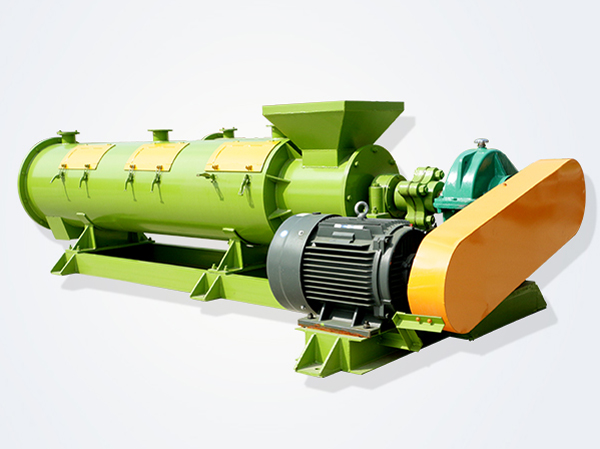
New type of organic fertilizer granulator
The wet stirring gear granulator utilizes the high-speed rotating mechanical stirring force and the resulting aerodynamic force to continuously mix, granulate, spheroidize, and compact fine powder materials inside the machine, thereby achieving the purpose of granulation. This granulation method results in higher ball formation rate and more aesthetically pleasing particles, while also saving energy
Organic fertilizer disc granulator
The granulation disc of the disc granulator (also known as the ball disc) adopts an integral circular arc structure to achieve a granulation rate of over 93%. The granulation disc is equipped with three discharge ports for intermittent production operations, greatly reducing labor intensity and improving labor efficiency. The reducer and motor are driven by flexible belts, which ensures smooth starting, reduces impact force, and improves equipment service life. The bottom of the granulation disc is reinforced with multiple radiating steel plates, which are sturdy and durable. The thickened, weighted, and sturdy base design does not require anchor bolts for stable operation, making it an ideal equipment for organic fertilizer and compound fertilizer granulation.
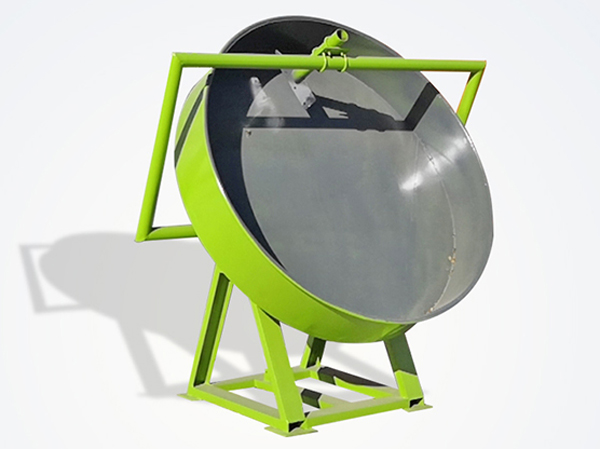
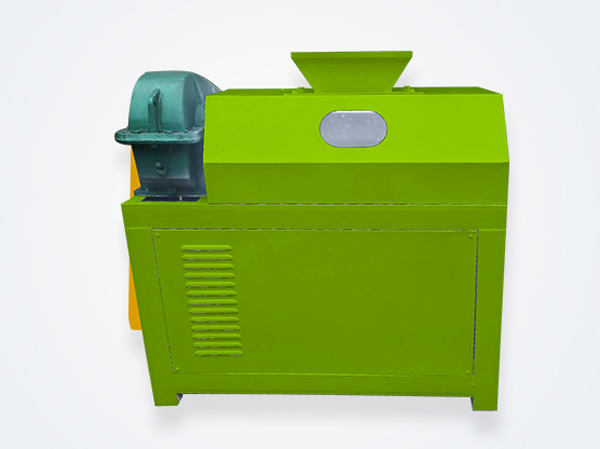
Roll squeezing granulator
The roller extrusion granulator is a key equipment for compound fertilizer granulation. It has advanced technology, reasonable design, compact structure, novelty and practicality, low energy consumption, and can be matched with corresponding equipment to form a small production line. It can form a continuous and mechanized production with a certain capacity.
Adopting eugenic formula, no need for drying, produced at room temperature, the product is rolled and formed in one go, ensuring that the product quality meets the technical requirements of compound fertilizers. It is a new generation product for producing high, medium, and low concentration special compound fertilizers for various crops and energy-saving and consumption reducing products in the compound fertilizer industry.
The shape and size of the ball and socket on the roller skin of this series of granulators can be customized according to user needs, with a wide range of choices. The ball pressing shapes include pillow shaped, semi-circular, stick shaped, pill shaped, walnut shaped, flat ball shaped, and square bar shaped.
Stirring gear conversion granulator
Our company has newly developed an organic fertilizer rotary drum and toothed dual-purpose granulator. The rotary drum granulator is a molding machine that can manufacture materials into specific shapes. The wet stirring gear granulator utilizes the high-speed rotating mechanical stirring force and the resulting aerodynamic force to continuously mix fine powder materials into granules, spheroidize, and compact them inside the machine, thereby achieving the purpose of granulation. Conversion granulation to pellet wet granulation involves a certain amount of water or steam to allow the basic fertilizer to undergo sufficient chemical reaction after being humidified in the cylinder. Under certain liquid phase conditions, the rotating motion of the cylinder generates squeezing force between the material particles, causing them to aggregate into balls. The combination of these two granulation methods results in higher ball formation rate and more aesthetically pleasing particles, while also saving energy and being highly efficient and energy-saving.
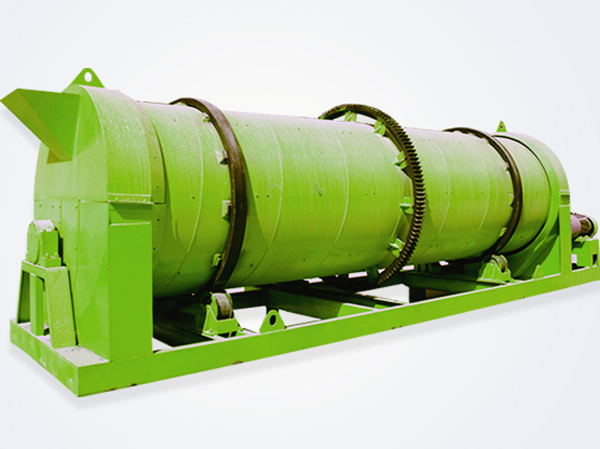
Pig manure fertilizer production line configuration — raw material fermentation and crushing part
NAME | Specifications | Quantity | Remark |
---|---|---|---|
Trough tipping machine | ZCFD-3000 | 1 | Includes a shift car (tank changing car), shift motor, electrical control cabinet, remote control handle, and cable drum for customer selection (The track needs to be purchased by the customer) According to customer requirements, our company has flipping equipment with a width of 2-20 meters and a flipping depth of 0.8-3 meters. |
Forklift feeder | ZCW-2030 | 1 | Includes uniform discharge device, anti smashing net device, mixing anti blocking device, and vibration anti blocking device. The capacity of the silo is about 5m3, greatly reducing the workload of the forklift operator, and the forklift driver can also operate the stacker. The function of this device is to uniformly transport raw materials to the crusher. |
Drum screen | ZGS-1240 | 1 | The screen mesh is made of stainless steel material to prevent corrosion. According to customer requirements, a striking anti sticking net device can be added. |
Vertical composite mill | ZLFF-600 | 1 | The crusher adopts a chain blade composite structure, which can crush materials with a moisture content of less than 40% to a granulation state. The chain is made of high manganese alloy, and the blades are made of spring steel material, which has the advantage of durability and wear resistance. The rotor is dynamically balanced and can operate stably without the need for a foundation. |
Three warehouse dynamic batching | ZZP-1515 | 4 | The size of this silo is customized according to the customer’s ratio. The part in contact with the material can be made of 304 stainless steel material. The computer quantitative weighing system adopts imported sensors and instruments, with high measurement accuracy, ingredient accuracy of ≤± 0.5%, packaging accuracy of ≤± 0.2%, and reliable operation. |
Pig manure feed production line configuration — granulation part
NAME | Specifications | Quantity | Remark |
---|---|---|---|
Single-shaft mixer | ZSJ-0830 | 1 | The mixing blade adopts a double spiral structure, which ensures uniform mixing and high efficiency. The mixing blades are made of high-strength and wear-resistant materials, which have a longer service life. The minimum gap between the rotor and the shell can be adjusted to near zero, effectively reducing the amount of material residue. Mixing capacity: 5-8t/h Body thickness: 6mm Dimensions: 3800 * 1320 * 770mm Reducer model: JZQ350-31.5 Mixing speed: 34r/min |
Stir tooth granulator | ZZGZ-600 | 1 | The interior of the barrel is lined with rubber sheets, which automatically remove scars. Anti corrosion insulation. The support wheel frame and transmission gear ring roller belt of the granulator are all made of cast steel material. Barrel thickness: 14mm, barrel inner diameter: 1800mm, barrel length: 6000mm. Material Q345. Adopting a one-time forming spiral tube. Production capacity: 7-9t/h Rotation speed: 11.5r/min |
Rotary dryer | ZHG-1010 | 1 | The dryer cylinder is a 14mm thick integrated spiral tube, which has the advantages of high concentricity, strong rigidity, and smooth operation. The thickness of the lifting plate is 8mm. The gear ring, rolling belt roller, and bracket are all cast steel parts. The induced draft fan is self-made by the company and has undergone static and dynamic balance calibration, resulting in stable and high-intensity operation. Adopting a co current drying method, the material and heat source airflow enter the drying equipment from the same side, resulting in a low outlet temperature and high thermal efficiency of the dryer. Choose reasonable operating parameters to balance the “coal, material, and air”, thereby greatly improving the thermal efficiency of the dryer and reducing drying energy consumption by more than 30-50%. |
Rotary cooling machine | ZLQ-0880 | 1 | The cooling machine cylinder is a 14mm thick integrated spiral tube, which has the advantages of high concentricity, strong rigidity, and smooth operation. The thickness of the lifting plate is 6mm. The gear ring, rolling belt roller, and bracket are all cast steel parts. The induced draft fan is self-made by the company and has undergone static and dynamic balance calibration, resulting in stable and high-intensity operation. Choose reasonable operating parameters to balance the “material and air”, thereby greatly improving the cooling efficiency of the cooling machine and reducing cooling energy consumption by more than 20-50%. |
Drum screen | ZGS-1240 | 1 | The screen mesh is made of stainless steel material to prevent corrosion. According to customer requirements, a striking anti sticking net device can be added. The function of this screening machine is to screen the crushed raw materials, the finished products enter the granulation process, and the waste products are returned for re crushing. The finished product is also a powdered organic fertilizer |
Pig fertilizer feed production line configuration — supporting equipment
NAME | Specifications | Quantity | Remark |
---|---|---|---|
There is a bucket pellet packaging machine | ZKB | 1 | The parts in contact with the material are made of 304 stainless steel material. Specially designed feeding and bucket metering are carried out simultaneously with bagging and unloading. Save one-third of homework time, fast packaging speed, and high packaging accuracy. Imported sensors and pneumatic actuators are used, which are reliable in operation and easy to maintain. Measurement accuracy is plus or minus two thousandths. Wide quantitative range, high accuracy, combined with a conveyor sewing machine that can be raised and lowered on the table, making it versatile and efficient. |
Finished product warehouse | ZLC-1200 | 1 | The finished organic fertilizer warehouse is widely used in various fertilizer production lines to undertake the transfer equipment that is quickly transported to the belt conveyor and transported by the belt conveyor to the next deep processing link. This finished product warehouse, equipment material quality, durable. |
Chain return mill | ZLTF-500 | 1 | The outer wall of the crusher is made of 8mm thick manganese steel plate. The crusher chain adopts a high-strength alloy chain. The crushed material is uniform, not easy to stick to the wall, and easy to clean. The inner wall can be made of rubber or stainless steel (depending on customer needs) to achieve a smooth surface and easy cleaning. Quick opening maintenance doors are installed on both sides of the body, and the body and transmission device are mounted on a steel base. A shock absorber is installed at the bottom of the base and connected to the foundation. |
Cyclone dust collector | ZXC-900 | 2 | The cyclone dust collector has a simple structure, is easy to manufacture, install, and maintain, and has low equipment investment and operating costs. The cyclone dust collector is composed of an intake pipe, an exhaust pipe, a cylindrical body, a conical body, and an ash hopper. Each component of the cyclone dust collector has a certain size ratio, and the diameter of the dust collector, inlet size, and exhaust pipe diameter are all accurately calculated by engineers. Ensure the best dust removal effect is achieved. |
Induced draft fan | ZYF-6C | 15 | The induced draft fan is self-made by the company and has undergone static and dynamic balance calibration, resulting in stable and high-intensity operation. The induced draft fan and connecting pipeline are matched with the dryer. The impeller consists of 10 aft inclined blade types, a curved front plate, and a flat rear plate. Made of copper plate or cast aluminum alloy, and calibrated for dynamic and static balance, it has good air performance, high efficiency, and smooth operation. The air inlet is made as a whole and installed on the side of the fan. The cross-section parallel to the axial direction is curved, which allows gas to enter the impeller smoothly with minimal loss. |
Characteristics of pig manure fertilizer production line
(1) The organic fertilizer produced by the organic fertilizer granulator is nutritionally strong, if it is put evenly, there is no need to add other fertilizers for at least 100 days, and this effect can not be replaced by any other fertilizer.
(2) There is an organism and enzyme in organic fertilizer granulation, which can increase the biological property and enzyme activity of the land, increase the nutrient content of the land and improve the acidity and alkalinity of the soil.
(3) Organic fertilizer pelletizing machine can add disease and pest prevention drugs during production to reduce disease and pest and rodent damage.
(4) The organic fertilizer produced by the organic fertilizer granulator has comprehensive nutrition, and in addition to the three major elements of nitrogen, phosphorus and potassium, there are rich calcium, magnesium and silicon, etc., which change the composition of the soil and is conducive to growth.