The pellet organic fertilizer production line is a process in which organic fertilizer raw materials (animal manure, household waste, dead branches and leaves, biogas residue, waste bacterial strains, etc.) are fermented and then enter a semi wet material crusher for crushing. Then, nitrogen, phosphorus, potassium and other elements (pure nitrogen, phosphorus pentoxide, potassium chloride, ammonium chloride, etc.) are added to meet the required mineral element standards. The mixture is then stirred by a mixer and enters a new type of organic fertilizer granulation mechanism for granulation. After coming out, it is dried and screened by a screening machine. Qualified products are packaged, and unqualified products are returned to the granulator for granulation.
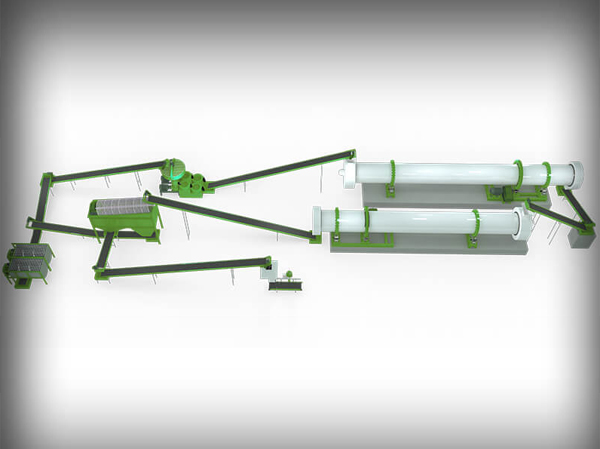
Automatic pellet organic fertilizer production line
processing capacity:1-100T/h
Application scope:animal manure, domestic waste, dead leaves, biogas residue, waste bacteria, etc into fertilizer
Sources of organic fertilizer raw materials and types of organic fertilizers
1、 Source of raw materials: local materials, leftovers from agricultural and sideline products, livestock and poultry manure, paper mill sludge, water treatment plant sludge, peat, bone meal, cake, bagasse, weathered coal, peat soil, lignite, leftovers from distilleries, pharmaceutical factories and monosodium glutamate factories can be fermented into organic fertilizers.
2、 Types of organic fertilizers: 1. Straw organic fertilizer 2. Livestock manure organic fertilizer 3. Humic acid organic fertilizer 4. Household waste and sludge organic fertilizer 5. Slag organic fertilizer 6. Organic inorganic compound fertilizer, etc.
Organic fertilizer production line: It uses fresh chicken, pig, cow manure, organic matter, urban garbage, sludge, straw, rice husk and other raw materials without any chemical components. However, chickens and pigs have poor digestion ability and can only consume 25% of the nutrients, while the other 75% of the nutrients in the feed are excreted with feces, resulting in dry products containing nitrogen, phosphorus, potassium, organic matter, amino acids, proteins and other components.

Our company can design the process flow according to different raw materials. This organic fertilizer production line can increase or decrease equipment according to the needs of different customers. It can be simple or complex, semi automated, fully automated, or assembly line production. It can customize organic fertilizer production equipment with an annual output of 100000-800000 tons according to user requirements.
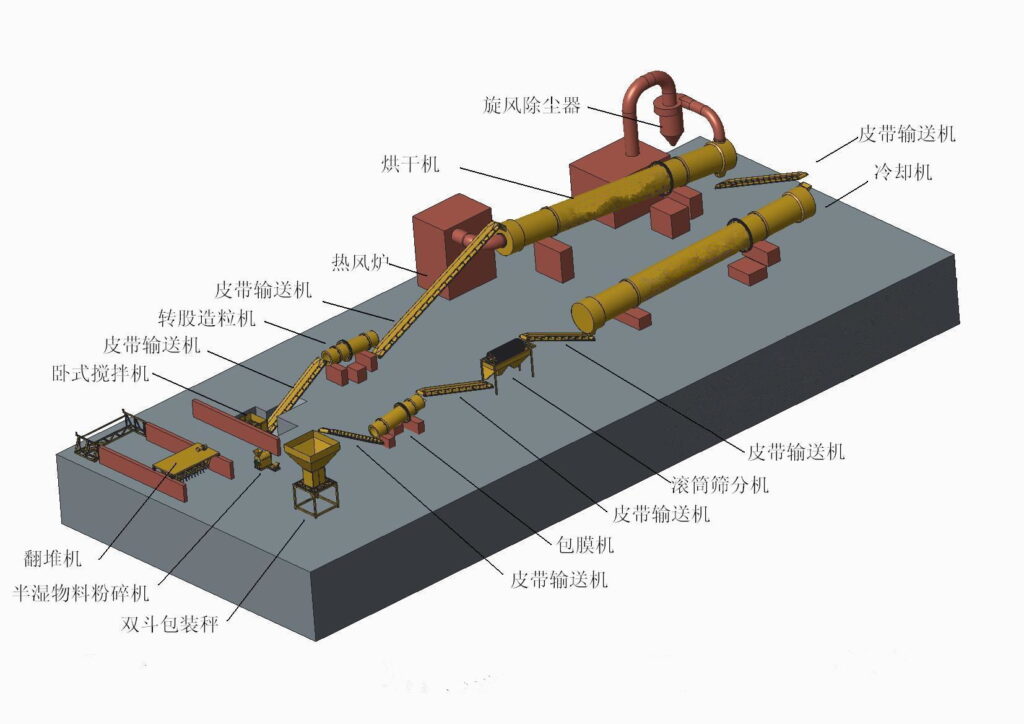
Processing technology of pellet organic fertilizer production line
Process flow of pellet organic fertilizer production line: Fermentation turning machine – batching machine – crusher – mixer – granulator – dryer – cooler – screening machine – round throwing machine – coating machine – packaging machine – palletizer
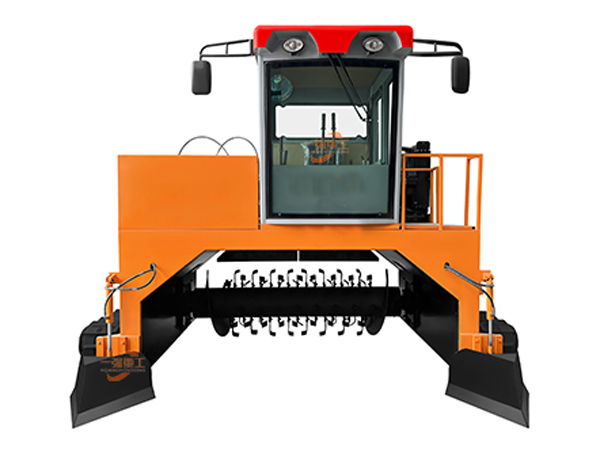
Add raw materials – strip pile fermentation
Dispose of livestock and poultry manure and auxiliary materials (straw, rice straw, sawdust, mushroom residue, etc.); According to the ratio, stack the strips as needed. The length of the strip stack is not limited, with a width of 4 meters (not fixed) and a height of 1 meter (not fixed). When stacking strips, it is necessary to evenly stack the materials layer by layer;
Raw material processing – granulation processing
After fermentation according to the above steps, it becomes powder organic fertilizer after screening and deep processing; Powder organic fertilizer can also be used as the main raw material and mixed with inorganic raw materials such as nitrogen, phosphorus, and potassium through an automatic batching system as an organic-inorganic compound fertilizer (optional). Powder organic fertilizer is used as a granulation raw material and mixed with a dual axis mixer to adjust the moisture content before entering the granulator for deep processing and granulation. Disc granulator, new organic fertilizer stirring tooth granulator, conversion granulator, etc., enter the next process after the particles are formed;
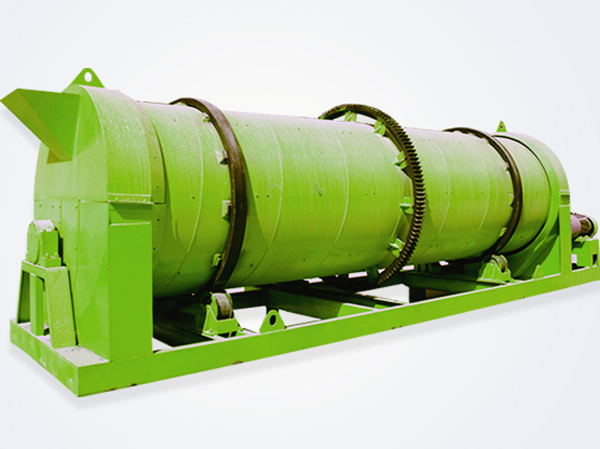
Drying/Cooling – Packaging
The newly made granules have a relatively high moisture content and need to be dried to below 20% of the organic fertilizer standard. The dried granules of organic fertilizer are then cooled and screened out by a cooling machine before being packaged directly.
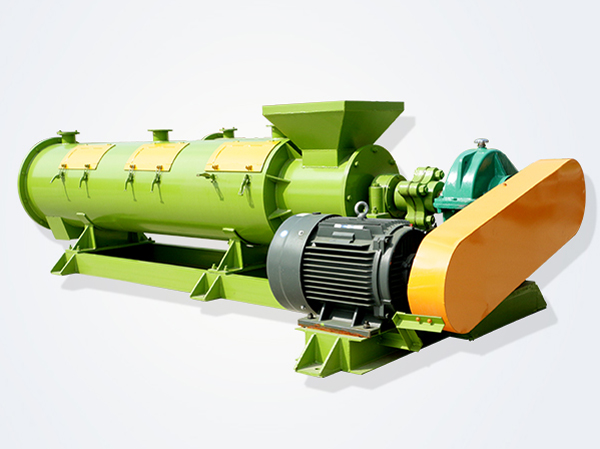
Project conditions: Take the annual output of 10,000 tons as an example (2~3 tons per hour) equipment configuration
Main raw materials: animal manure from cattle, sheep, pigs, chickens, etc., unknown auxiliary materials (auxiliary materials include waste such as peat, sawdust, straw, soybean cake, and keratin powder);
Production capacity: 2 to 3 tons/hour per hour.
Factory personnel: produce approximately 1800 square meters; Fermentation workshop covers an area of approximately 1400 square meters; Approximately 6-10 people.
Equipment | Model | Power (kw) | Quantity | Equipment use |
---|---|---|---|---|
Hydraulic tipping machine | ZPY-4 | 11*2,2.2,1.5,4 | 1 | Fermentation of organic fertilizer |
Forklift into the bin | TC-2*3 | 6 | 1 | Production feeding equipment, suitable for 30 forklifts |
Vertical mill | LP-60 | 15 | 1 | The raw material of organic fertilizer is broken to meet the requirements of granulation |
Drum screen | GT – 1.2 * 4 | 5.5 | 1 | Fine screening of powdered raw materials after grinding |
Automatic batching system | ZD-N | 1.1 | 1 | Automatic computer proportioning system. (N indicates quantity of raw materials) (optional) |
Double shaft mixer | TC-40 | 15 | 1 | Stir raw materials and adjust granulation water |
Stir tooth granulator | JC-60 | 37 | 1 | The raw material of powdered organic fertilizer is made into granules |
Tumble dryer | HG – 1.2 | 7.5 | 1 | The finished particles are dried so that the moisture meets the storage requirements. |
Roller cooler | LQ – 1.0 | 5.5 | 1 | Cool the dried finished product particles to the appropriate temperature to prevent the finished product packaging from returning to moisture. |
Drum screen | GT – 1.2 * 4 | 5.5 | 1 | Finished particle sieving |
Packaging machine | Type 50 | 2.2 | 1 | Packaged finished products, ranging from 20kg to 50kg/ bag |
Belt conveyor | B500 | 2.2~5kw | The devices are connected, and the power is equipped according to the length |