Organic fertilizer production line: fresh chicken, pig, cow manure, organic matter, municipal waste, sludge straw, rice husk and other raw materials, does not contain any chemical composition, and chickens, pigs poor digestion, can only consume 25% of the nutrients, and the other 75% nutrients in the feed with the excrement, so that the dry product contains nitrogen, phosphorus, potassium, organic matter, amino acids, protein and other ingredients.
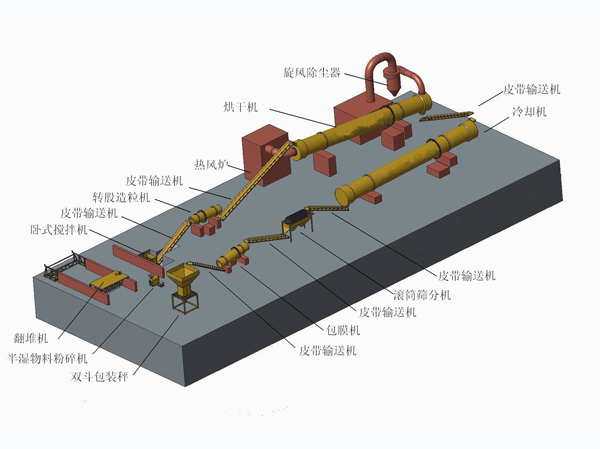
Automatic organic fertilizer production line
processing capacity:1-100T/h
Organic fertilizer raw material sources and organic fertilizer types
1, raw material source: local materials, agricultural by-product waste, livestock and poultry manure, paper mill sludge, water treatment plant sludge, peat, bone meal, bagasse, weathered coal, peat soil, lignite, distillery, pharmaceutical factory, MSG factory waste can be fermented into organic fertilizer.
2, organic fertilizer types: 1, straw organic fertilizer 2, livestock and poultry manure organic fertilizer 3, humic acid organic fertilizer 4, domestic waste, sludge organic fertilizer 5, slag organic fertilizer 6, organic-inorganic compound fertilizer and so on.

Process flow of organic fertilizer production line: Fermentation turning machine – batching machine – crusher – mixer – granulator – dryer – cooler – screening machine – round throwing machine – coating machine – packaging machine – palletizer
Our company can design the process flow according to different raw materials. This organic fertilizer production line can increase or decrease equipment according to the needs of different customers. It can be simple or complex, semi automated, fully automated, or assembly line production. It can customize organic fertilizer production equipment with an annual output of 100000-800000 tons according to user requirements.
Processing technology of organic fertilizer processing line

Ingredient crushing and mixing system
The function of this system is to crush, ratio, and mix various raw materials such as composted materials, nitrogen, phosphorus, potassium inorganic fertilizers, and other additives in a certain proportion. Based on years of experience, the recommended equipment configuration is as follows: using a vertical crusher to crush cow manure compost is not easy to stick to the wall and block, and a multi-layer turbulent chain hammer structure improves crushing performance; Adopting a continuous automatic batching system suitable for dynamic metering and batching control of organic fertilizer raw materials; The mixed operation is equipped with a dual axis continuous mixer, which has good sealing performance and makes it difficult for wet materials to adhere to the root of the mixing shaft.
Granulation molding system
The function of this system is to make particles from the material that has been thoroughly mixed with crushed ingredients. Flat die granulator is suitable for granulation, which has the advantages of wide adaptability to raw materials, especially suitable for organic materials, with broad requirements for raw material density and moisture content, and does not require drying of raw materials; The diameter of the pressure roller is large, and the template can be used on both sides. The material is evenly distributed in the compression chamber, ensuring stable granulation and high particle forming rate. The finished particles have a uniform appearance and are not easily broken; The entire granulation process does not add water, saving the cost of subsequent particle drying; The fineness requirement for raw material crushing is not high. Granulated raw materials (after composting) generally do not require fine crushing, and small stones can be directly crushed without easily blocking the pressure plate mold holes.
Screening and return system
The granular materials output from the granulation molding system have certain differences in particle size and need to be screened and classified. The selected rotary screening machine requires low vibration, low noise, easy screen replacement, and is equipped with a screen surface cleaning device. It is recommended to equip an automatic material return system to screen the unqualified large and small particles, which are then transported out by a belt elevator, re crushed, and sent to the granulator for further granulation. This will help improve the continuous operation capacity of the organic fertilizer production line.
Particle drying system
The function of this system is to further remove moisture from the screened particles to meet the standard requirements for organic fertilizer moisture content. Particle drying generally uses a three cylinder dryer to improve particle shaping while drying. The function of the particle cooling system is to achieve cooling of the dried particle material, which helps to store and preserve the quality of the particles. The hot particulate material output from the dryer enters the counterflow cooler from above, and the dry air enters from the lower part of the cooler under the action of the cooling fan, and undergoes sufficient cold and heat exchange with the wet and hot particles from the upper part to the lower part. After cooling, the difference between the particle temperature and the ambient temperature is less than 5 ℃. A swing type flip plate unloading mechanism with pneumatic system control, adjustable unloading speed, uniform and smooth unloading. Compared with drum coolers for cooling organic fertilizers, the advantages of countercurrent coolers are: less land occupation, lower price, and better cooling effect.
Finished product packaging system
The cooled granular material is transported into the finished product warehouse through a bucket elevator. Granular materials are quantitatively weighed and packaged using an automatic packaging scale. The automatic packaging scale adopts microcomputer control and can achieve multi range measurement. It has high weighing accuracy, automatic clamping, sewing, automatic peeling weight and detection functions. Its advantages are incomparable to manual packaging.
Supporting equipment of organic fertilizer production line
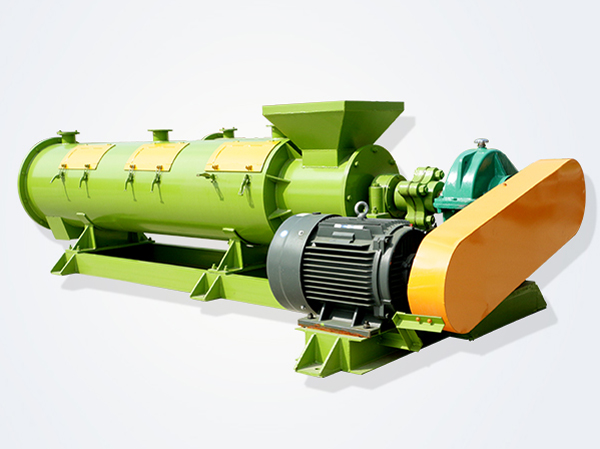
New type of organic fertilizer granulator
The wet stirring gear granulator utilizes the high-speed rotating mechanical stirring force and the resulting aerodynamic force to continuously mix, granulate, spheroidize, and compact fine powder materials inside the machine, thereby achieving the purpose of granulation. This granulation method results in higher ball formation rate and more aesthetically pleasing particles, while also saving energy
Organic fertilizer conversion granulator
Drum granulator is a molding machine that can produce materials into specific shapes. The rotary drum granulator is one of the key equipment in the compound fertilizer industry, suitable for large-scale production of cold and hot granulation as well as high, medium, and low concentration compound fertilizers. The main working method is wet granulation of granules, which uses a certain amount of water or steam to fully react the basic fertilizer after being humidified in the cylinder. Under certain liquid phase conditions, the rotating motion of the cylinder generates squeezing force between the material particles to aggregate into balls.
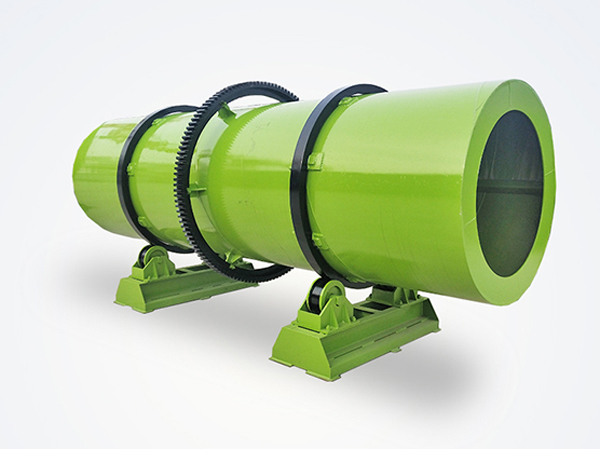
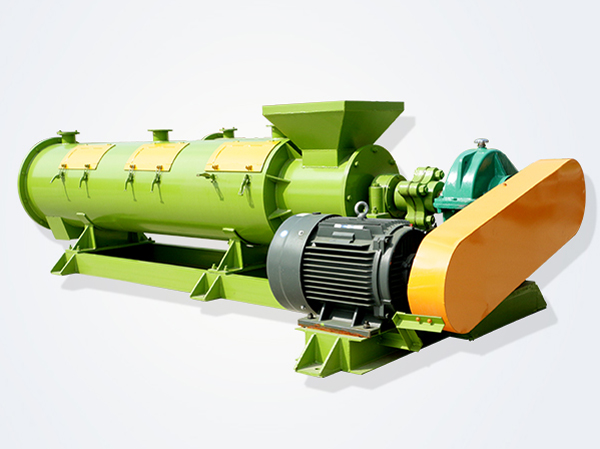
New type of organic fertilizer granulator
The wet stirring gear granulator utilizes the high-speed rotating mechanical stirring force and the resulting aerodynamic force to continuously mix, granulate, spheroidize, and compact fine powder materials inside the machine, thereby achieving the purpose of granulation. This granulation method results in higher ball formation rate and more aesthetically pleasing particles, while also saving energy
Organic fertilizer disc granulator
The granulation disc of the disc granulator (also known as the ball disc) adopts an integral circular arc structure to achieve a granulation rate of over 93%. The granulation disc is equipped with three discharge ports for intermittent production operations, greatly reducing labor intensity and improving labor efficiency. The reducer and motor are driven by flexible belts, which ensures smooth starting, reduces impact force, and improves equipment service life. The bottom of the granulation disc is reinforced with multiple radiating steel plates, which are sturdy and durable. The thickened, weighted, and sturdy base design does not require anchor bolts for stable operation, making it an ideal equipment for organic fertilizer and compound fertilizer granulation.
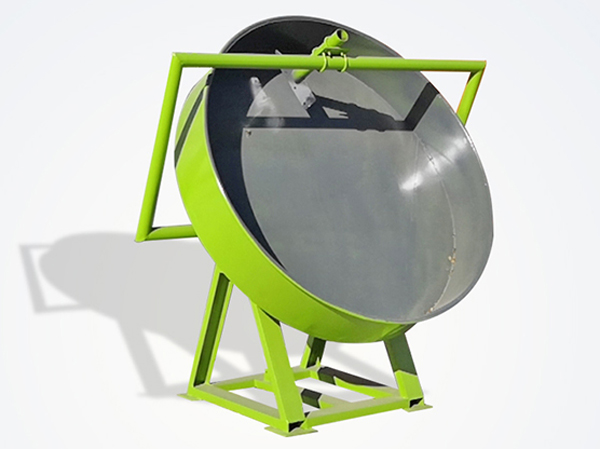
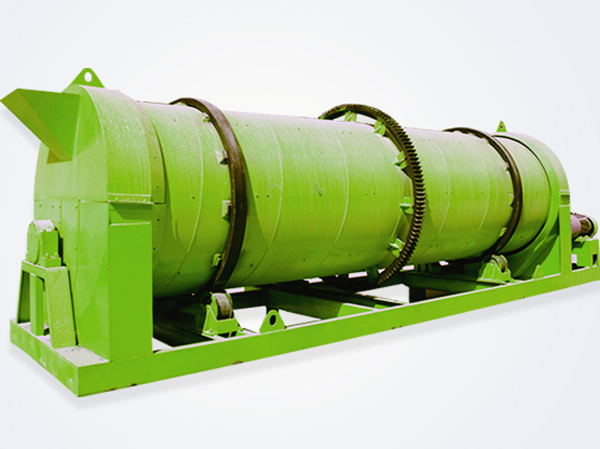
Stirring gear conversion granulator
Our company has newly developed an organic fertilizer rotary drum and toothed dual-purpose granulator. The rotary drum granulator is a molding machine that can manufacture materials into specific shapes. The wet stirring gear granulator utilizes the high-speed rotating mechanical stirring force and the resulting aerodynamic force to continuously mix fine powder materials into granules, spheroidize, and compact them inside the machine, thereby achieving the purpose of granulation. Conversion granulation to pellet wet granulation involves a certain amount of water or steam to allow the basic fertilizer to undergo sufficient chemical reaction after being humidified in the cylinder. Under certain liquid phase conditions, the rotating motion of the cylinder generates squeezing force between the material particles, causing them to aggregate into balls. The combination of these two granulation methods results in higher ball formation rate and more aesthetically pleasing particles, while also saving energy and being highly efficient and energy-saving.
Roll squeezing granulator
The roller extrusion granulator is a key equipment for compound fertilizer granulation. It has advanced technology, reasonable design, compact structure, novelty and practicality, low energy consumption, and can be matched with corresponding equipment to form a small production line. It can form a continuous and mechanized production with a certain capacity.
Adopting eugenic formula, no need for drying, produced at room temperature, the product is rolled and formed in one go, ensuring that the product quality meets the technical requirements of compound fertilizers. It is a new generation product for producing high, medium, and low concentration special compound fertilizers for various crops and energy-saving and consumption reducing products in the compound fertilizer industry.
The shape and size of the ball and socket on the roller skin of this series of granulators can be customized according to user needs, with a wide range of choices. The ball pressing shapes include pillow shaped, semi-circular, stick shaped, pill shaped, walnut shaped, flat ball shaped, and square bar shaped.
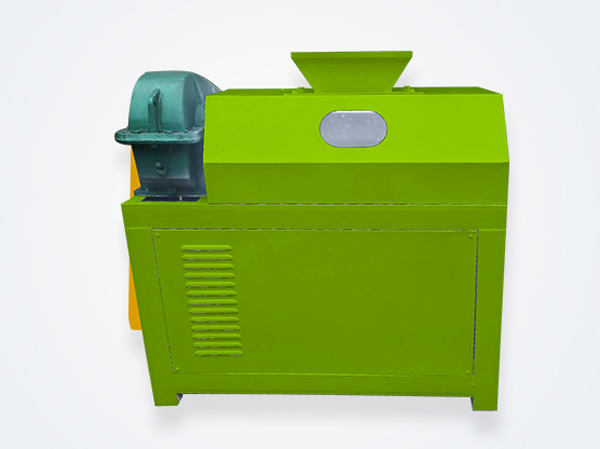
Case of an annual output of 10,000 tons of organic fertilizer prodution plant
Annual production line of 10,000 tons of organic fertilizer
Organic fertilizer production line flow
1.The recycled livestock and poultry waste is directly transferred to the fermentation area. After a fermentation, secondary aging stacking, eliminate the odor of livestock and poultry manure. At this stage, fermentation strains can be added to decompose the coarse fibers in them, so that the particle size requirements after grinding meet the particle size requirements of granulation production.
2.The fermentation materials that have completed the secondary aging stacking process are crushed and entered into the mixing mixing system. Before mixing and mixing, N, P, K and some other trace elements are added to the mixing mixing system according to the formula to start mixing.
3.The mixed material is transported into the granulation system, the particles enter the cooling system after the dryer, the material will be screened at room temperature, the particles that meet the requirements enter the coating machine and start packaging, and the particles that do not meet the requirements are crushed by the crusher and returned to the granulation system to continue granulation.
4.Automatic packaging of finished products.
Detailed configuration of organic fertilizer production line
name | Power (KW) | Quantity |
---|---|---|
Trough tipping machine | Turning power: 18.5kw 2. Walking power: 1.5kw (frequency conversion) 3. Shift power: 0.75kw | 1 |
Forklift feeder | 5.5 | 1 |
Drum screen | 3*2 | 2 |
Vertical composite mill | 30 | 1 |
Double shaft mixer | 11 | 1 |
New organic fertilizer granulator | 75 | 1 |
Rotary dryer | 11 | 1 |
Rotary cooling machine | 11 | 1 |
There is a bucket pellet packaging machine | 1.5 | 1.5 |
Finished product warehouse | ||
Chain return mill | 15 | 15 |
Hot blast stove | 2 | |
Cyclone dust collector | 2 | |
6C induced draft fan | 15 | 1 |
Dust chamber | 2 | |
8C induced draft fan | 22 | 1 |
Belt conveyor | 45 | 100 |
Integrated control electric control cabinet | ||
Dryer cooling machine pipe |